1. ABS 플라스틱이란 무엇인가요?
광택 아크릴로니트릴 부타디엔 스티렌 (ABS)은 충격에 견딜 수 있는 강도, 인성 및 충격으로부터의 자유로움을 결합한 특정 유형의 열가소성 폴리머입니다. 자동차부터 전자제품, 장난감, 가정용품에 이르기까지 기존 산업 전반에 걸쳐 광범위하게 사용되고 있습니다. ABS는 아크릴로니트릴, 부타디엔, 스티렌을 결합하는 중합이라는 공정을 통해 만들어지며, 각 재료에 고유한 특성을 부여합니다:

- 아크릴로니트릴은 내화학성과 열 안정성에 기여합니다.
- 부타디엔은 내충격성과 인성을 향상시킵니다.
- 스티렌은 견고함과 광택을 제공합니다.
ABS는 사출 성형 제조 공정에서 널리 사용되어 왔습니다. 이 공정은 높은 내충격성과 인성 등 ABS의 우수한 기계적 특성을 최대한 활용합니다. ABS 사출 성형은 강도와 내구성이 필요한 제품을 만드는 데 이상적이며 자동차 대시보드, 전자 하우징 및 가전 제품 부품에 일반적으로 사용됩니다.
2. ABS 플라스틱의 종류
다양한 용도에 맞는 다양한 유형 또는 등급의 ABS 플라스틱이 있습니다. 주요 유형은 다음과 같습니다:
- ABS 표준: 가장 많이 사용되는 등급으로 강도, 유연성 및 가공성이 절충된 제품입니다. 사출 성형에 유리한 특성을 가지고 있습니다.
- 고충격 ABS(HI-ABS): 이 등급은 향상된 인성과 내충격성으로 설계되어 자동차 부품이나 보호 케이스와 같은 용도에 적합합니다.
- 난연성 ABS: 이 유형의 ABS에 첨가된 첨가제는 플라스틱의 가연성을 감소시켜 난연성이 필요한 전기 부품 및 가정용품에 사용하기에 이상적입니다.
- ABS/폴리카보네이트(PC) 혼합: 이 소재는 두 가지를 혼합한 소재입니다. 일반적으로 전자 하우징에 사용됩니다.
- ABS Plus: 표면 품질이 우수하고 매끄럽고 정밀한 최종 제품을 생산하기 위한 이상적인 가공 특성을 갖춘 새로운 ABS 변형입니다.
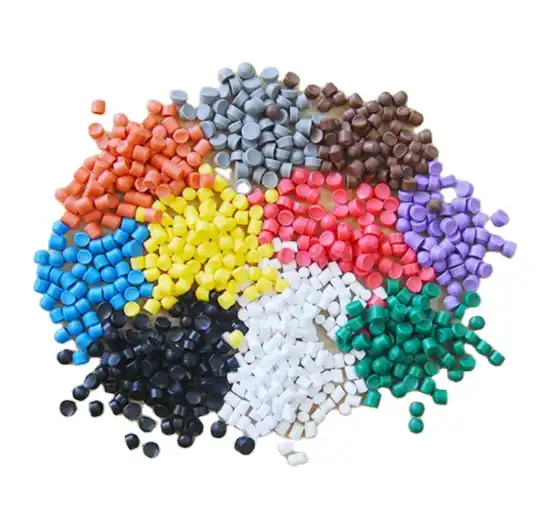
여러 종류의 ABS 플라스틱은 다양한 이점을 제공하며, 일반적으로 강도, 내구성, 환경 조건에 대한 내성 등의 요소를 고려하여 각 용도에 적합한 특정 등급이 있습니다.
ABS 소재의 6가지 특성
내충격성: ABS는 내구성과 내충격성이 뛰어나 자동차 부품, 전자제품 등 물리적 스트레스를 받는 제품에 사용됩니다.
강성 및 인성: 강성과 인성의 균형이 잘 잡혀 있으며 까다로운 애플리케이션에 사용됩니다.
열 안정성: 최대 100°C/212°F까지 큰 충격 없이 열을 수용하므로 자동차 및 전자제품의 내열성에 적합합니다.
미적 매력: 매끄럽고 광택이 나는 표면은 쉽게 칠하거나 질감을 낼 수 있어 장난감이나 전자제품과 같은 소비재에 이상적입니다.
손쉬운 가공: ABS는 특히 사출 성형에서 성형 및 성형이 쉬운 소재로, 낭비가 거의 없이 복잡한 디자인을 구현할 수 있습니다.
내화학성: 많은 화학 물질은 영향을 받지 않지만 아세톤과 같은 용제는 영향을 미칠 수 있습니다.
3. ABS의 성능
ABS의 성능
ABS 플라스틱은 기계적 특성이 뛰어나 다양한 용도에 적합합니다. 성능을 위한 주요 기능은 다음과 같습니다:

물리적 속성
ABS는 제조 공정으로 인해 경도, 강성, 인성 등 기계적 특성이 매우 우수합니다. 따라서 다목적 엔지니어링 플라스틱으로 자주 활용됩니다. ABS 수지는 흰색 또는 밝은 크림색이며 불투명하고 무독성이며 대략 1.05의 밀도를 가지고 있습니다. 용융 유속은 0.2%에서 0.7%입니다. 연소하면 노란색 불꽃을 내며 검은 연기가 발생하고 물방울이 떨어지거나 부드러워지지 않습니다.
내열성
ABS는 내열성이 있지만 1.86MPa의 열 변형 온도가 약 85°C로 중간 정도입니다. 열처리를 통해 이 온도를 10°C 정도 높일 수 있으며, ABS의 사용 범위는 40°C~85°C이며 100°C를 초과하는 것은 권장하지 않습니다. ABS의 열전도율은 0.16~0.29W/(m-K)이며 선팽창계수는 (6.2~9.5) × 10-⁵K-¹입니다. 그 결과 열가소성 플라스틱 중 가장 낮은 팽창 계수를 가지고 있어 정밀한 치수의 부품을 제작하는 데 적합합니다.
기계적 특성
충격 강도가 높은 견고한 열가소성 플라스틱입니다. 고무 성분의 에너지 흡수 특성 덕분에 은색 선이 형성되는 것을 방지할 수 있습니다. 아크릴로니트릴 부타디엔 스티렌은 충격 강도가 높고 -40°C 이하에서도 견딜 수 있는 저온 인성이 우수합니다. 또한 7.2MPa의 하중에서도 해당 파이프가 2년 동안 크기를 유지하며 뛰어난 크리프 저항성을 보여줍니다.
내화학성
ABS는 물, 무기염, 알칼리, 묽은 산에 내성이 있습니다. 그러나 농업용 황산 및 질산과 같은 산화성 산에는 민감합니다. 스트레스 균열은 지방족 탄화수소, 알코올, 광물성 및 식물성 오일에 장시간 노출될 때 발생합니다. ABS는 아세트산에틸, 아세톤, 염화메틸렌에 용해되거나 에멀젼을 형성할 수 있습니다.
내후성
ABS의 구조에는 이중 결합이 포함되어 있어 햇빛, 열, 산소에 더 잘 견딥니다. 궁극적으로 이는 산화와 성능 저하로 이어집니다. 예를 들어 ABS는 6개월 동안 실외에 노출되면 충격 강도가 45% 감소합니다. 자외선, 열, 산소로 인해 깨지기 쉽습니다. 일반적으로 카본 블랙이나 페놀계 항산화제와 같은 첨가제를 사용하여 내후성을 향상시킵니다.
4. ABS 사출 성형 가이드
ABS 사출 성형은 아크릴로니트릴 부타디엔 스티렌으로 구성된 부품을 제조하는 데 가장 많이 사용되는 공정 중 하나입니다. 다음은 ABS 사출 성형에 사용되는 단계입니다:

1단계 – 자료 준비
ABS 펠릿이 사출기에 로드됩니다. 펠릿은 용융 상태로 가열되어 금형에 주입할 준비가 됩니다.
2단계 – 금형에 사출
녹은 ABS를 고압으로 몰드 캐비티에 주입합니다. 사출 공정은 재료가 금형에 완전하고 균일하게 침투할 수 있도록 세심하게 조절됩니다.
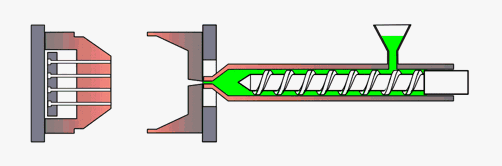
3단계 – 냉각 및 응고
사출이 완료되면 금형이 냉각되어 ABS가 원하는 형태로 굳어집니다. 냉각 시간은 부품 두께와 금형 설계에 따라 다릅니다.
4단계 – 금형 열기 및 부품 제거하기
부품이 냉각되고 굳으면 금형이 열리고 부품이 배출됩니다. 그런 다음 다음 공정 단계로 진행하기 전에 결함 및 품질을 검사합니다.
5단계 – 후처리(필요한 경우)
용도에 따라 성형된 ABS 부품은 트리밍, 도장 또는 표면 마감 처리가 필요할 수 있습니다.
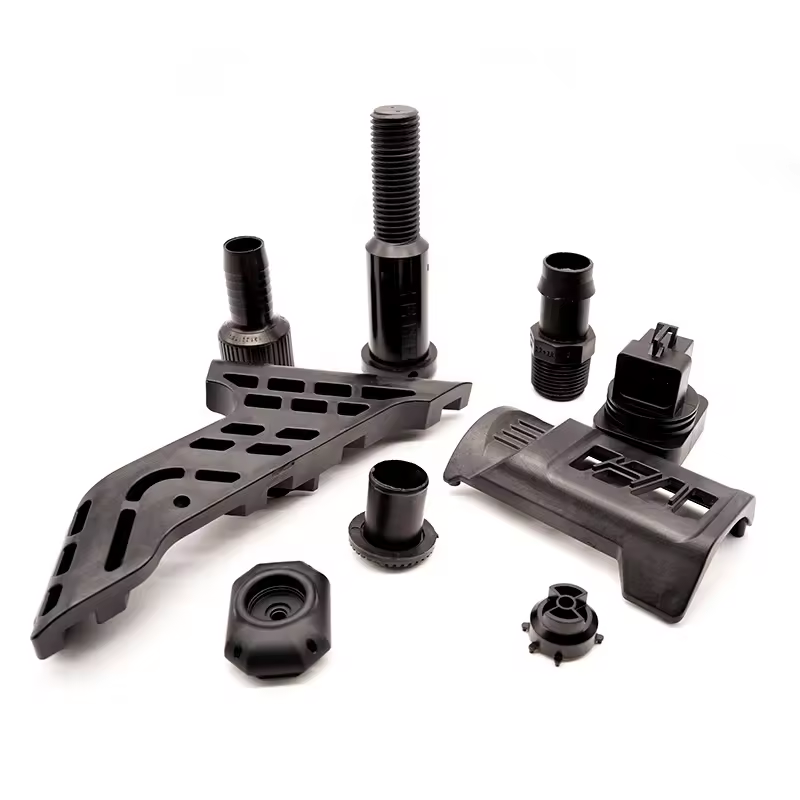
성공적인 ABS 사출 성형을 위한 3가지 팁:
- 온도 제어: 배럴, 금형 및 재료 온도를 제어하여 뒤틀림, 표면 마감 불량 등의 결함을 방지해야 합니다.
- 주입 속도: 짧은 샷이나 불완전한 충전과 같은 문제를 방지하기 위해 주입 속도를 신중하게 조정해야 합니다.
- 배출: 부품이 금형에서 사출될 때 부품이 형태를 유지할 수 있을 만큼 충분히 응고되어야 하므로 사출 시 변형되지 않도록 충분한 냉각 시간이 필요합니다.
ABS 사출 금형 온도 가이드
부품의 수축률이 증가하고 성형 주기가 길어집니다. 이 문제를 해결하기 위해 가열 금형 방식이 사용됩니다. 60-70°C의 금형 온도는 높은 표면 품질, 복잡한 모양 및 성능 요구 사항이 있는 부품에 이상적입니다.
ABS 사출 성형 압력
사출 압력은 벽 두께, 장비 유형 및 레진 등급에 따라 다릅니다. 얇은 벽, 긴 공정, 작은 게이트, 내열성 또는 난연성 제품에는 압력이 높을수록 좋습니다. 이렇게 하면 캐비티를 채우는 데 도움이 되지만 과도한 압력은 릴리스 문제나 손상을 유발할 수 있습니다. 내부 스트레스를 최소화하려면 60-70MPa로 유지 압력을 제어하세요.
ABS 사출 성형 속도
사출 속도는 ABS 용융 유동성에 영향을 미칩니다. 속도가 느리면 주름이나 용접 불량과 같은 표면 결함이 발생할 수 있습니다. 속도가 빠르면 적절한 금형 충진 시간이 부족하여 표면 마감이 불량해집니다. 일반 생산의 경우 중간에서 저속을 사용합니다. 고속은 까다로운 금형 충진에만 필요합니다.
ABS 플라스틱 성형 후처리
ABS 부품에 내부 응력이 있을 수 있습니다. 사용 빈도가 낮은 부품은 열처리가 필요합니다. 고성능 부품을 70~80°C에서 24시간 동안 가열한 후 실온으로 식힙니다. 내부 응력을 테스트하려면 부품을 빙초산에 담급니다. 2분 후에도 균열이 나타나지 않으면 스트레스가 낮은 상태입니다. 5-15초 이내에 균열이 생기면 내부 스트레스가 높다는 뜻입니다.
ABS 사출 성형의 6가지 주요 이점
내충격성 및 내구성 – ABS는 매우 강하고 견고하여 마모를 견뎌야 하는 제품에 적합한 옵션입니다. 자동차 부품이나 전자 하우징과 같이 기계적으로 스트레스를 받는 부품에 이상적이며 열악한 조건에서도 손상되지 않도록 보장합니다.
낮은 재료비 – ABS를 광범위하게 사용하면 부품 비용을 낮추고 전체 생산 비용을 절감할 수 있습니다. 사출 성형을 통한 손쉬운 가공으로 품질 저하 없이 대량 생산이 가능하며, 대량 생산 시 비용 효율성이 전혀 다른 차원에 이릅니다.
성형 또는 설계 유연성 향상 – 유동성이 우수하여 뒤틀림이나 불완전한 충전과 같은 결함이 발생할 가능성이 적은 ABS는 사출 성형 시 가공이 용이합니다. 또한 복잡한 모양과 복잡한 디자인을 쉽게 제작할 수 있어 제조업체가 세밀한 기능적 구성을 정확하게 만들 수 있습니다.
뛰어난 미적 마감 – ABS 부품의 윗면이 유리로 되어 있어 깔끔한 외관을 원하는 많은 제품에서 선호합니다. 도색, 텍스처링 또는 마감 처리가 간단하고 추가 단계가 필요하지 않아 최고 품질의 시각적 결과를 얻을 수 있으므로 소비자를 대면하는 제품에 적합합니다.
뛰어난 온도 저항성 – ABS는 중간 온도 환경에서 우수한 성능을 발휘하므로 부품이 고온에 노출될 수 있는 자동차 또는 전기 애플리케이션에서 작동할 수 있는 경험과 작업 경력을 쌓을 수 있습니다. 구조나 성능 저하 없이 열을 견뎌냅니다.
광범위한 응용 분야 – ABS는 자동차 부품부터 가전제품, 의료기기에 이르기까지 다양한 산업에서 일반적으로 사용되는 열가소성 폴리머입니다. 첨가제(예: 난연제)로 성능을 향상시킬 수 있어 성능과 관련하여 유연성을 제공합니다. 공급망도 훨씬 더 유연해질 것입니다.
5. ABS 플라스틱 사출 성형 문제 및 해결 방법
ABS는 널리 사용되는 사출 성형 재료이지만 사출 성형 공정에는 몇 가지 문제가 있습니다. 다음은 몇 가지 일반적인 문제와 이를 방지하는 방법입니다:

이슈 | 원인 | 솔루션 |
뒤틀림 | 고르지 않은 냉각 또는 금형 설계 문제 | 냉각 채널 및 성형 파라미터 조정 |
쇼트 샷 | 부적절한 사출 압력 또는 부적절한 금형 온도 | 사출 압력 증가 및 금형 온도 최적화 |
흐름 표시 | 높은 사출 속도 또는 부적절한 금형 온도 | 사출 속도 감소 및 금형 온도 미세 조정 |
싱크 마크 | 벽이 두껍고 냉각이 부적절한 부품 | 벽 두께 및 냉각 시간 최적화 |
에어 트랩 | 금형 캐비티의 환기 불량 | 금형 환기 및 배기 시스템 개선 |
표면 결함 | 재료의 오염 또는 습기 | 적절한 재료 건조 및 금형 청결 유지 |
성형 초기에 이러한 문제를 해결하면 제품 품질을 개선하고 불량률을 줄일 수 있습니다.
결론
견고하고 저렴한 ABS 플라스틱은 수천 가지 응용 분야에서 신뢰할 수 있는 소재입니다. 제조업체는 유형, 성능 및 사출 성형 공정을 파악함으로써 생산을 최적화하고 제품 품질을 개선하며 비용을 절감하는 등의 효과를 얻을 수 있습니다. 또한 ABS 사출 성형은 최적의 금형 설계, 재료 준비 및 가공 파라미터를 수행한다면 고강도 및 내충격성이 요구되는 부품에 특히 유용합니다.
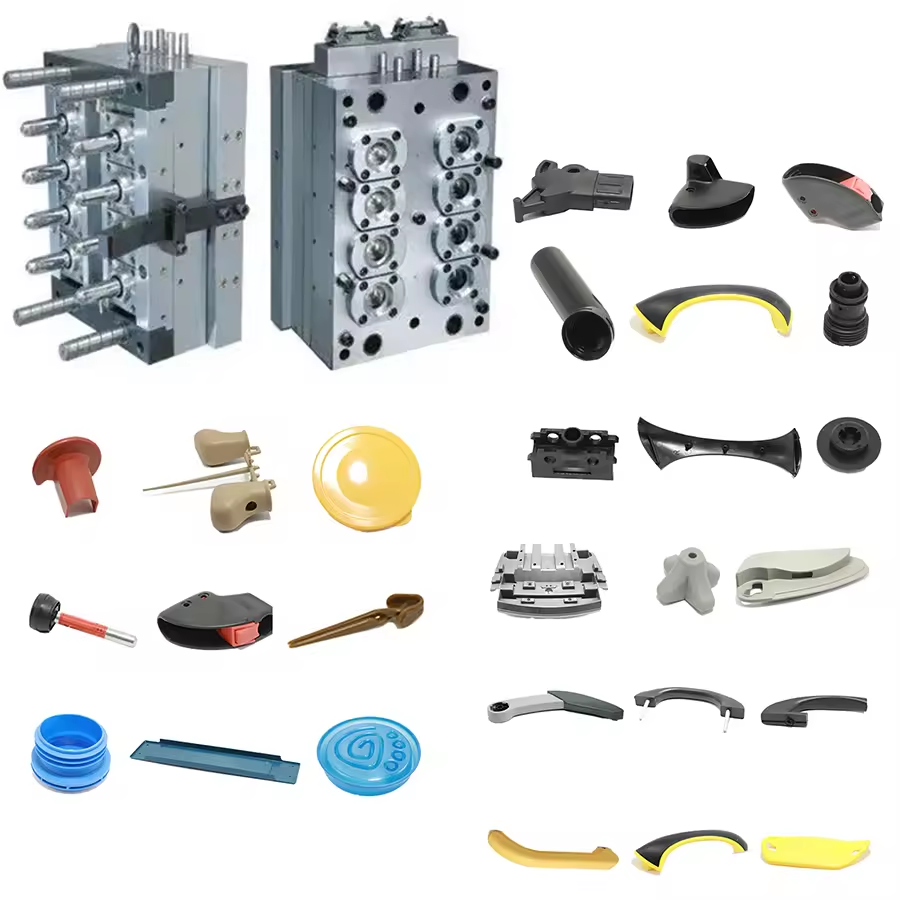
BFY Mold 정보
BFY Mold는 사출 성형 및 금형 제조에 중점을 두고 대량 생산, 주문형 생산, CNC 가공 및 미러 스파크 마감 서비스를 제공합니다. 잘 갖추어진 사내 공장과 숙련된 전담 인력을 통해 프로젝트에 고품질의 저렴한 솔루션을 보장할 수 있습니다.
새로운 ABS 사출 성형 프로젝트를 시작하려면 지금 BFY Mold에 문의하십시오!
ABS 사출 성형에 관한 10가지 FAQ
1. ABS가 사출 성형에 선호되는 재료인 이유는 무엇인가요?
ABS(아크릴로니트릴 부타디엔 스티렌)는 높은 내충격성, 뛰어난 가공성 및 비용 효율성을 제공합니다. 균형 잡힌 특성(예: 인장 강도: 40~50MPa, 최대 80°C의 내열성)으로 자동차 트림, 가전제품 및 산업용 하우징에 이상적입니다.
2. ABS 사출 성형 공급업체는 어떤 인증을 받아야 하나요?
ISO 9001(품질 관리), IATF 16949(자동차), 난연성 등급(예: ABS+PC)에 대한 UL 인증을 확인합니다. 의료용 애플리케이션의 경우 ISO 13485를 준수하는지 확인하세요.
3. ABS 부품의 뒤틀림이나 싱크 자국을 방지하려면 어떻게 해야 하나요?
- 최적화된 냉각: 금형 온도를 60~80°C로 유지합니다.
- 균일한 벽 두께: 1.2~3.5mm 사이의 벽을 디자인합니다.
- 재료 건조: ABS 펠릿을 80~90°C에서 2~4시간 예열하여 습기를 줄입니다.
4. ABS 사출 성형으로 어떤 표면 마감을 구현할 수 있나요?
- SPI 표준: 광택(SPI-A1), 질감(SPI-C1) 또는 무광택(SPI-D3).
- 후처리: 브랜딩을 위한 페인팅, 전기 도금 또는 레이저 에칭.
5. ABS 사출 금형의 일반적인 툴링 비용은 얼마입니까?
- 알루미늄 금형: 3,000–3,000–15,000 (prototyping/low-volume).
- 강철 주형: 15,000-15,000-80,000개 이상(대량 생산).
비용은 부품의 복잡성, 캐비티 수, 표면 마감에 따라 달라집니다.
6. 재활용 ABS를 사출 성형에 사용할 수 있나요?
예, 하지만 확실히 하세요:
- 소비 후 ABS는 식품 접촉 애플리케이션에 대한 FDA 21 CFR을 충족합니다.
- 기계적 특성을 유지하기 위해 재활용 콘텐츠 ≤30%.
- 공급업체는 자재 추적성 및 테스트 보고서를 제공합니다.
7. ABS는 PP나 PC와 같은 다른 플라스틱과 어떻게 다른가요?
속성 | ABS | PP | PC |
충격 강도 | 높음 | 보통 | 매우 높음 |
내열성 | 80°C | 100°C | 130°C |
비용 | $2–4/kg | $1–3/kg | $4–8/kg |
ABS는 비용과 성능의 균형을 맞추는 반면, PC는 고열 애플리케이션에서 탁월한 성능을 발휘합니다. |
8. 어떤 산업에서 일반적으로 ABS 사출 성형을 사용합니까?
- 자동차: 대시보드 구성 요소, 인테리어 트림.
- 전자 제품: 키보드 키, 프린터 하우징.
- 가전제품: 진공 청소기 부품, 냉장고 라이너.
9. 공급업체는 ABS 부품의 색상 일관성을 어떻게 보장하나요?
- 마스터배치 믹싱: 균일한 색상을 위한 정밀한 안료 주입.
- 인라인 분광광도계: 실시간 컬러 모니터링.
- 배치 테스트: 팬톤 또는 RAL 표준과 비교합니다.
10. ABS 공급업체는 어떤 성형 후 지원을 제공하나요?
- 조립 서비스: 초음파 용접 또는 스냅핏 통합.
- 품질 보증: CMM 보고서, 낙하 테스트, 인화성 검사.
- 재고 관리: 창고 보관 비용 절감을 위한 JIT(적시 배송) 배송.