소개
경쟁이 치열한 소비자 가전 업계에서 제품 수명이 단축되고 마진이 줄어들면서 제조업체는 고품질 플라스틱 부품을 더 낮은 비용으로 공급해야 하는 거의 절체절명의 과제에 직면해 있습니다. 웨어러블 건강 기술을 선도하는 한 혁신 기업에서는 기존의 맞춤형 사출 성형 공정이 자원을 낭비하고 출시가 지연되며 정밀도 기준을 충족하지 못했기 때문에 이 과제가 매우 중요했습니다.
BFY Mold와의 파트너십을 통해 고객은 총 생산 비용을 40% 절감하는 동시에 출시 기간을 단축하고 제품 신뢰성을 개선하는 진정한 돌파구를 마련할 수 있었습니다. 이 사례 연구에서는 이러한 혁신을 가능하게 한 기술 전략, 재료 혁신 및 공급망 최적화에 대해 살펴보고, 점점 더 비용에 민감한 환경에서 성공하고자 하는 전자 제품 브랜드에 실행 가능한 인텔리전스를 제공합니다.
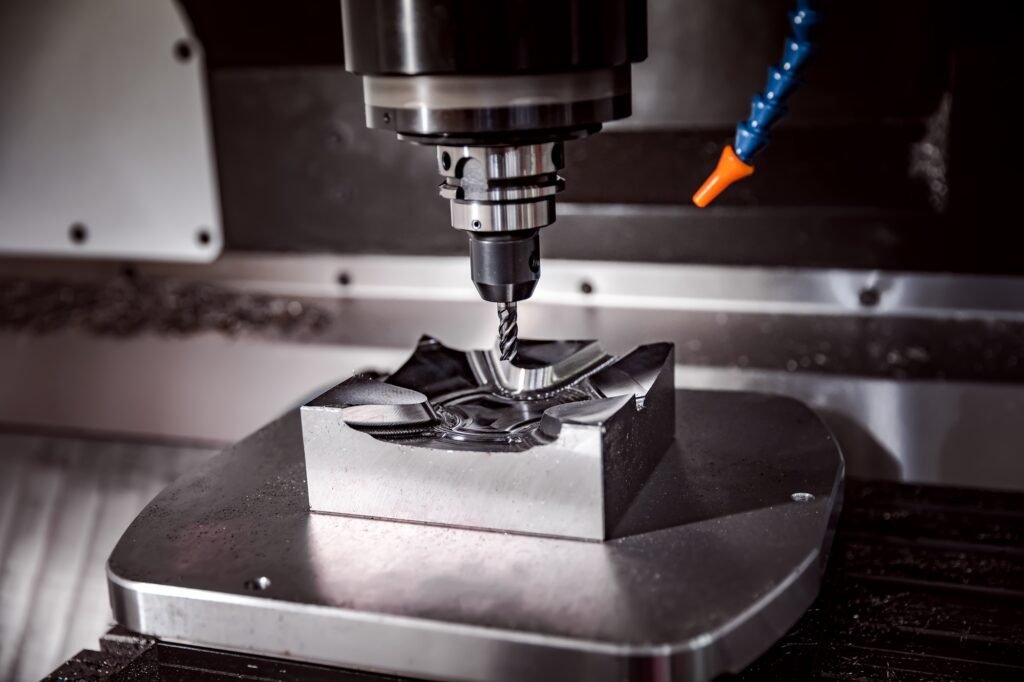
도전 과제: 비용, 속도, 정확성 간의 균형
연간 5백만 대 이상의 스마트워치와 활동 추적기를 개발하는 한 고객사의 경우, 데이터 정확성을 보장하는 도구를 확보하는 데 어려움을 겪었습니다. 이 고객의 어려움은 업계 전반의 고충을 반영하는 것이었습니다:
- 재료 낭비: 기존 설계에서는 금형 제작 시 15%의 잉여 재료가 발생했습니다(대부분 ABS/PC 혼합물 유지).
- 프로토타입 제작 시간 지연: 디자인 변경 시마다 금형 조정에 2~3주가 소요되어 제품 출시가 중단됩니다.
- 해외 공급업체의 한계: 해외 공급업체는 인건비가 저렴하지만 ±0.05mm의 허용 오차 요구 사항을 지원하지 못해 품질이 일관되지 않았습니다.
“우리는 최첨단 엔지니어링과 가전제품의 긴급성을 모두 이해하는 파트너가 필요했습니다.”라고 고객의 제조 책임자는 말합니다. “모든 비용을 절감하고 하루하루를 단축하는 것이 중요했습니다.”
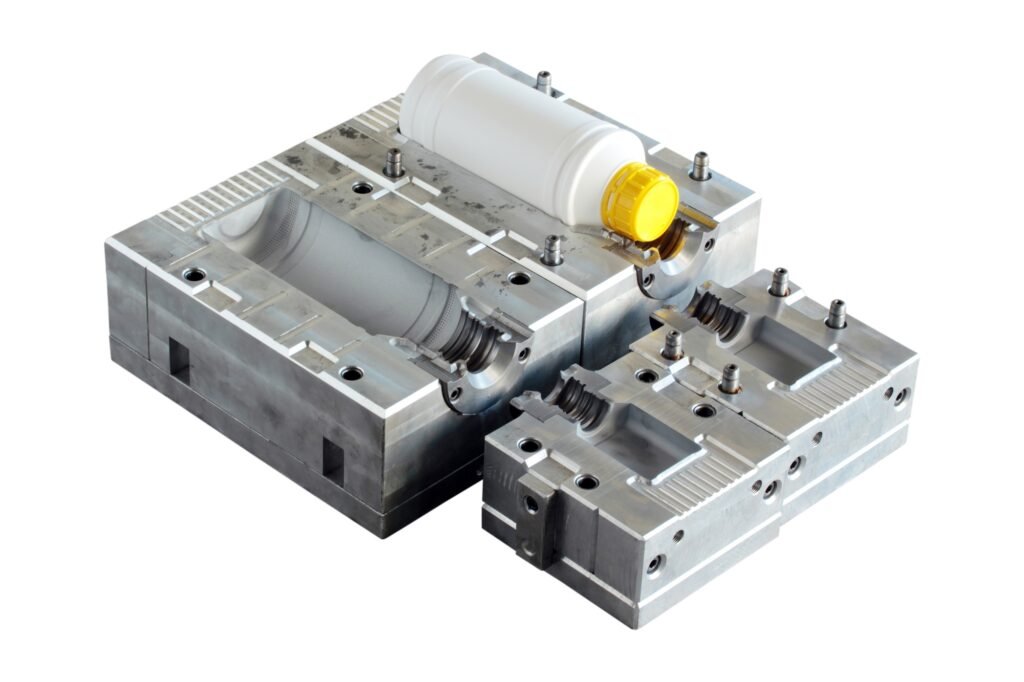
솔루션: BFY Mold의 세 가지 전략
1. 현지 맞춤형 금형 설계 최적화
문제: 오래된 시행착오로 인한 금형 조정으로 시간과 재료가 낭비되었습니다.
혁신:
- 금형 흐름 시뮬레이션: BFY Mold의 엔지니어들은 고급 시뮬레이션 소프트웨어를 활용하여 폴리머 흐름, 냉각 패턴 및 응력 분포를 분석했습니다.
- 최적의 게이트 위치를 파악하여 자재 사용량을 12% 줄였습니다.
- 싱크 마크와 뒤틀림 위험을 예측하여 테스트 반복 횟수를 5회에서 2회로 줄였습니다.
- 단일 캐비티 효율성: 다중 캐비티 금형을 선호하는 업계 표준과 달리 시뮬레이션 결과, 고객의 중저용량 요구 사항에 더 적합한 사이클 시간(18% 더 빠름)을 제공하는 단일 캐비티 설계가 더 적합한 것으로 나타났습니다.
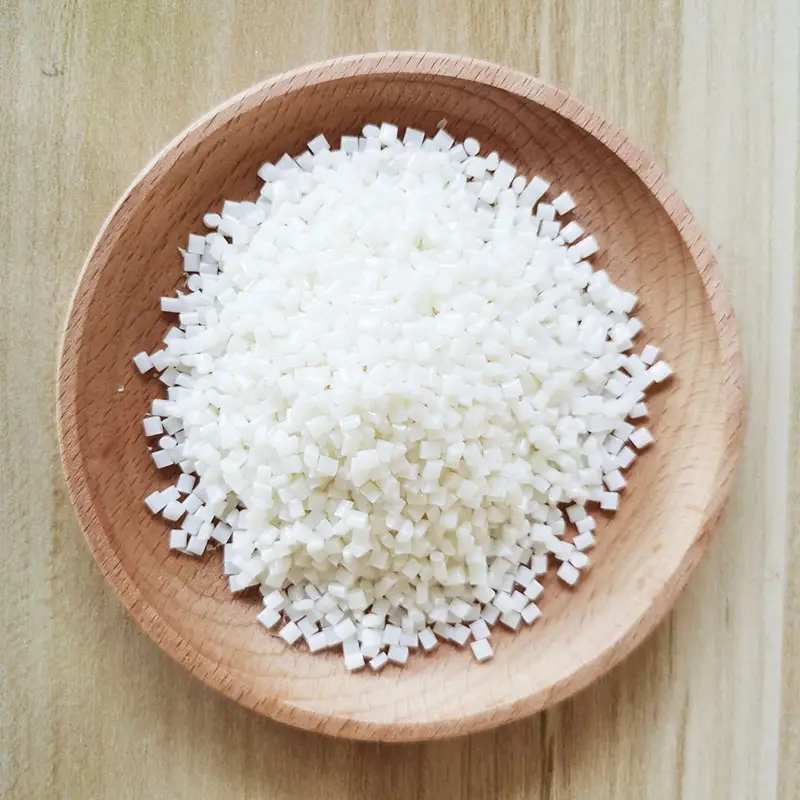
결과:
- 12% 재료 절감: 단위당 ABS/PC 소비량 감소.
- 50% 더 빨라진 프로토타이핑: 48시간 시뮬레이션 주기가 몇 주에 걸친 실제 시험을 대체했습니다.
2. 하이브리드 금형 제조: 비용 대비 완벽한 내구성
문제: 풀 스틸 몰드는 내구성은 뛰어나지만 엄청나게 비쌌습니다(세트당 28,000달러).
혁신:
- 알루미늄-강 복합 금형:
알루미늄 프레임: 제조용 금형 비용 35% 절감(세트당 $18,200).
스틸 코어 인서트: 대용량 전자 제품에 필수적인 500,000회 이상의 정밀도를 유지합니다.
- 컨포멀 냉각 채널:
3D 프린팅 채널은 금형의 윤곽을 따라 제작되어 냉각 효율을 25% 향상시켰습니다.
냉각 시간이 15초에서 11초로 단축되어 열 변형을 최소화했습니다.
비교 데이터:
Metric | 전통 금형 | BFY 몰드 하이브리드 몰드 |
초기 비용 | $28,000 | $18,200 |
사이클 타임 단축 | – | 18% |
도구 수명 | 100만 주기 | 500만 주기(업그레이드 가능) |
3. 현지화된 공급망 및 자재 소싱
문제: 해외 생산으로 인해 물류 지연과 숨겨진 비용이 발생했습니다.
혁신:
- 국내 소재 대체:
- 수입산 Sabic ST-800 ABS를 22% 저렴하면서도 UL94 V-0 인증을 받은 현지에서 수정한 대체품으로 교체했습니다.
- 재료 과학자들과 협력하여 웨어러블 디바이스의 난연성을 강화했습니다.
- 통합 프로덕션 허브:
- 중국 심천에 전용 시설을 설립하여 금형 제작, 맞춤형 사출 성형 및 QC를 함께 배치했습니다.
- 리드 타임을 8주에서 4주로 단축하세요.
비즈니스 파트너 공급망 책임자는 “BFY Mold의 수직 통합은 판도를 바꿨습니다.“ 라고 언급했습니다. “물류 오버헤드의 60%를 없애고 실시간으로 생산을 감독할 수 있게 되었습니다.”

가시적인 성과: 비용 절감 그 이상의 효과
- 총 비용 40% 절감:
- 재료: 12%
- 툴링: 35%
- 물류: 60%
- 시장 출시 시간 단축:
- 프로토타입 제작 주기가 50% 단축되어 제품 출시를 6주 앞당길 수 있었습니다.
- 2024년 연말연시 매출을 달성하여 매출을 230만 달러 증가시켰습니다.
- 향상된 품질 관리:
- 치수 정확도: ±0.03mm(초기 목표 초과).
- 불량률이 12%에서 2%로 감소하여 후반 작업 재작업이 최소화되었습니다.
- 전략적 파트너십:
- 플라스틱 투데이에 소개되어 포춘 500대 전자 기업 3곳으로부터 문의를 받았습니다.
- TWS 이어버드 케이스 및 IoT 센서를 포함하도록 맞춤형 사출 성형과의 협업을 확대했습니다.
왜 BFY 몰드인가? 전자 브랜드를 위한 기술적 우위

- 독점적인 몰드 플로우 데이터베이스: 소비자 가전 프로젝트에 1,000개 이상의 과거 시뮬레이션을 활용합니다.
- 이중 인증: ISO 9001 생산 인증으로 업계 전반의 규정 준수를 보장합니다.
- 유연한 생산 모델: 반복적인 기술 제품에 이상적인 소량 배치(1,000개 이상)를 지원합니다.
결론 결론: 전자 제조업체를 위한 청사진
이 여정은 소비자 가전 분야에서 혁신은 제품 기능뿐만 아니라 제조 자체를 재창조하는 것이라는 중요한 교훈을 강조합니다. AI 기반 설계, 하이브리드 툴링, 현지화된 민첩성을 결합하여 BFY Mold는 품질이나 속도의 저하 없이 40%의 비용 절감을 실현했습니다.
최종 CTA:
“맞춤형 사출 성형 공정을 혁신할 준비가 되셨나요?
무료 프로젝트 감사를 받으려면 BFY Mold의 엔지니어링 팀에 이메일로 문의하세요. 비용 혁신을 설계해 드리겠습니다.”