소개:
사출 성형에 적합한 소재를 선택하는 것은 제품의 성능, 가격, 내구성에 큰 영향을 미칠 수 있습니다. 가장 논쟁의 여지가 있는 소재로는 자동차, 전자제품, 소비재 등의 산업에서 강도와 적응성이 뛰어난 두 가지 열가소성 플라스틱인 ABS 소재와 폴리카보네이트(PC)가 있습니다. 그렇다면 프로젝트의 요구 사항에 맞는 소재를 어떻게 선택해야 할까요? 이 글에서는 강도, 내열성, 비용 효율성, 최적의 사용 분야와 같은 재료 특성을 분석하여 ABS와 PC의 주요 차이점을 살펴보고, 더 나은 제조 결과를 위한 정보에 입각한 결정을 내릴 수 있는 지식을 제공합니다.
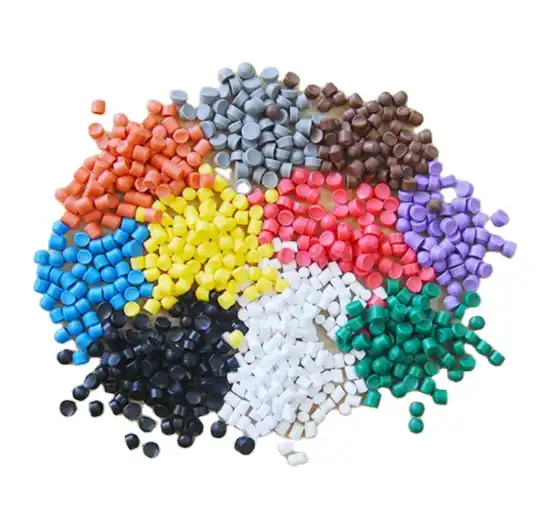
사출 성형의 부상:
사출 성형은 19세기 후반에 처음 시작된 이래 눈부시게 발전해 왔습니다. 처음에는 단순한 소규모 품목을 위한 것이었던 사출 성형은 복잡하고 정밀한 부품을 제작하는 정교한 기술이 되었습니다. 플라스틱을 녹여 금형에 주입한 다음 냉각하여 원하는 모양을 만드는 방식으로 작동합니다. 이 방법은 대량 생산에 가장 적합하며 복잡한 디자인과 복잡한 부품을 만들 수 있습니다.
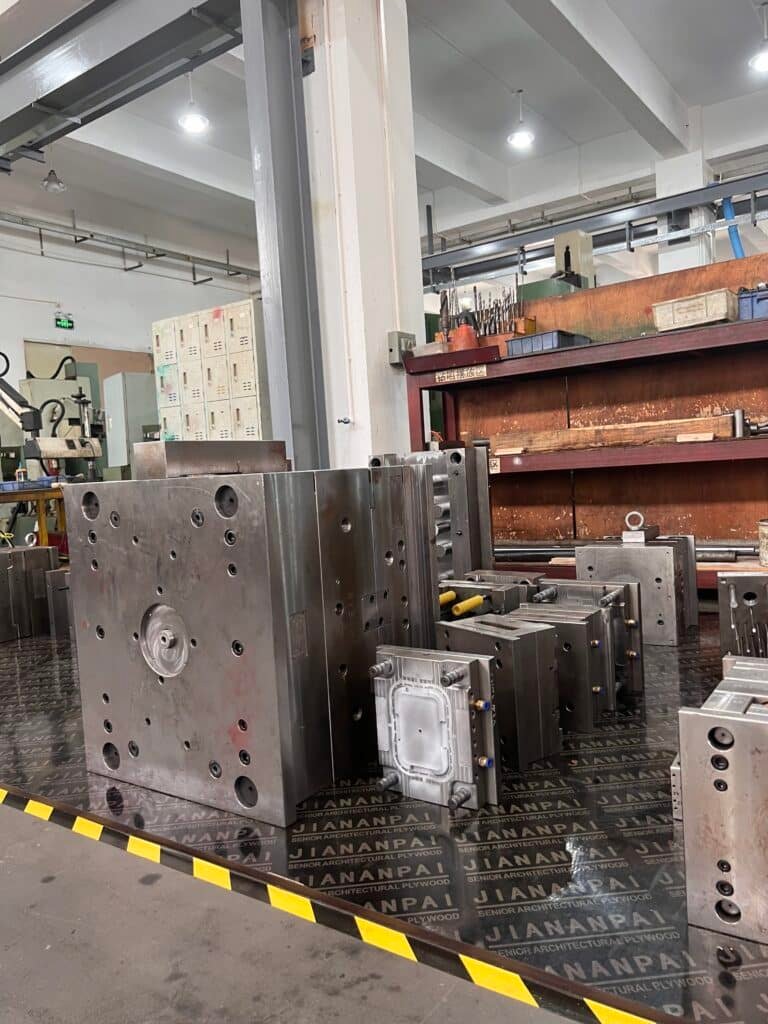
사출 금형
PC 및 ABS 소재: 듀얼 파워하우스:
폴리카보네이트(PC)와 아크릴로니트릴 부타디엔 스티렌(ABS)은 플라스틱 산업에서 뛰어난 소재이며, 각각 다양한 용도에 필수적인 고유한 특성을 자랑합니다.
뛰어난 투명도, 높은 내충격성 및 내열성으로 높이 평가받는 폴리카보네이트는 투명성과 내구성이 요구되는 용도로 자주 선택됩니다. 고온을 견디고 치수 안정성을 유지하는 능력이 가장 중요한 광학 부품, 전자 하우징 및 자동차 부품에 이르기까지 다양한 용도로 활용됩니다.
반면 아크릴로니트릴 부타디엔 스티렌(ABS)은 견고함, 뛰어난 내충격성 및 가공성으로 유명합니다. ABS는 강도와 유연성의 균형이 잘 잡혀 있어 소비재부터 자동차 내장재에 이르기까지 다양한 분야에 이상적입니다. 쉽게 성형하고 후가공할 수 있다는 점도 제조 분야에서 매력을 더합니다.
사출 성형 공정:
사출 성형 공정은 정밀도와 제어의 복잡한 춤과도 같습니다. 사출 성형은 PC 또는 ABS와 같은 플라스틱 원료를 작은 알갱이로 과립화하는 것으로 시작됩니다. 그런 다음 이 펠릿을 가열된 배럴에 공급하여 점성이 있는 용융 상태로 녹입니다. 재료가 최적의 농도에 도달하면 고압으로 금형 캐비티에 주입하여 금형의 구석구석이 채워지도록 합니다. 일반적으로 강철 또는 알루미늄으로 만들어진 금형은 최종 제품의 모양과 특징을 정의합니다.

금형 설계
용융된 재료가 금형 내에서 냉각되면서 응고되어 원하는 형태를 갖추게 됩니다. 원하는 특성을 얻고 뒤틀림이나 수축과 같은 결함을 방지하려면 온도, 압력 및 냉각 속도를 신중하게 제어하는 것이 필수적입니다. 냉각 과정이 완료되면 금형이 열리고 새로 형성된 제품이 드러납니다. 이 과정이 수초 내에 반복되므로 사출 성형은 매우 효율적이고 확장 가능한 제조 공정입니다.
산업 전반의 애플리케이션:
사출 성형과 PC 및 ABS 소재의 결합은 다양한 산업 분야에서 무수히 많은 응용 분야를 찾아볼 수 있습니다. 자동차에서는 대시보드와 차체 부품을 튼튼하고(ABS 사용) 투명하게(PC 사용) 만드는 데 이 소재가 사용됩니다. 전자 제품에서는 PC의 내열성과 ABS의 단열성 덕분에 케이스와 커넥터에 사용됩니다.
또한 PC와 ABS는 장난감, 가전제품, 생활용품을 만드는 데도 사용되어 소비재 분야에서 그 다재다능함을 보여줍니다. 의료 분야에서도 멸균되고 내구성이 뛰어난 부품을 생산할 때 이러한 소재의 이점을 활용하고 있습니다. 광범위한 응용 분야는 PC 및 ABS 소재를 사용한 사출 성형이 현대 제조의 요구 사항을 어떻게 적응하고 안정적으로 충족할 수 있는지 보여줍니다.
결론:
PC와 ABS 소재를 이용한 사출 성형에 대해 자세히 알아보면 현대 제조업에 큰 영향을 끼친 것이 분명합니다. 이들 소재의 고유한 특성과 정밀한 사출 성형 기술이 결합되어 자동차 부품부터 전자 제품 등에 이르기까지 무한한 가능성을 제공합니다.