광학 렌즈, 의료 기기 하우징 또는 소비자 포장과 같은 투명 제품을 사출 성형하려면 재료 순도, 공정 정밀도 및 표면 마감 무결성에 세심한 주의를 기울여야 합니다. 기포, 흐름 자국, 헤이즈와 같은 사소한 결함도 제품을 사용할 수 없게 만들 수 있으므로 재료 준비부터 금형 설계에 이르는 모든 단계가 중요합니다.
이 가이드는 고급 건조 프로토콜, 금형 온도 제어, 광학 등급 연마 기법 등 7가지 협상 불가 요소를 세분화하여 선명한 결과물을 보장합니다. PMMA 또는 폴리카보네이트 부품을 생산할 때 이러한 전략은 재작업을 최소화하고 투명성과 내구성에 대한 업계 표준에 부합합니다.
투명한 제품 선명도를 위한 표면 마감 표준
투명 플라스틱은 빛 투과율이 높기 때문에 엄격한 표면 품질 기준이 필요합니다. 자국, 기공, 변색, 광택 저하와 같은 결함은 용납할 수 없습니다. 재료, 장비, 금형, 제품 디자인 등 사출 성형 공정의 모든 측면이 엄격한 요건을 충족해야 합니다.

투명한 제품 성형: 헤이즈 및 거품 제거
투명 플라스틱은 일반적으로 녹는점이 높고 유동성이 낮습니다. 제품 품질을 보장하려면 배럴 온도, 사출 압력, 사출 속도와 같은 공정 파라미터를 미세 조정해야 합니다. 이를 통해 플라스틱이 내부 응력, 변형 또는 균열을 일으키지 않고 금형을 채울 수 있습니다.
투명한 폴리머 무결성을 위한 재료 건조
재료 순도 보장
플라스틱의 불순물은 투명도에 영향을 줄 수 있습니다. 보관, 운송 및 공급 중에는 재료를 밀봉하여 청결을 유지해야 합니다. 원재료에 수분이 있으면 가열 시 품질이 저하될 수 있으므로 철저한 건조가 필수적입니다. 건조 호퍼를 사용하고 투입되는 공기가 여과되고 제습되었는지 확인하세요.
투명한 제품 순도를 위한 장비 세척
청소 배럴, 나사 및 액세서리
사용 전과 종료 후 나사 세척제로 나사 및 액세서리를 세척하여 오염을 방지하세요. 세척제를 사용할 수 없는 경우 PE 또는 PS 수지를 사용할 수 있습니다. 일시 정지 중에는 건조기와 배럴의 온도를 낮추어 원재료의 열화를 방지합니다.
고광택 투명 제품을 위한 금형 설계
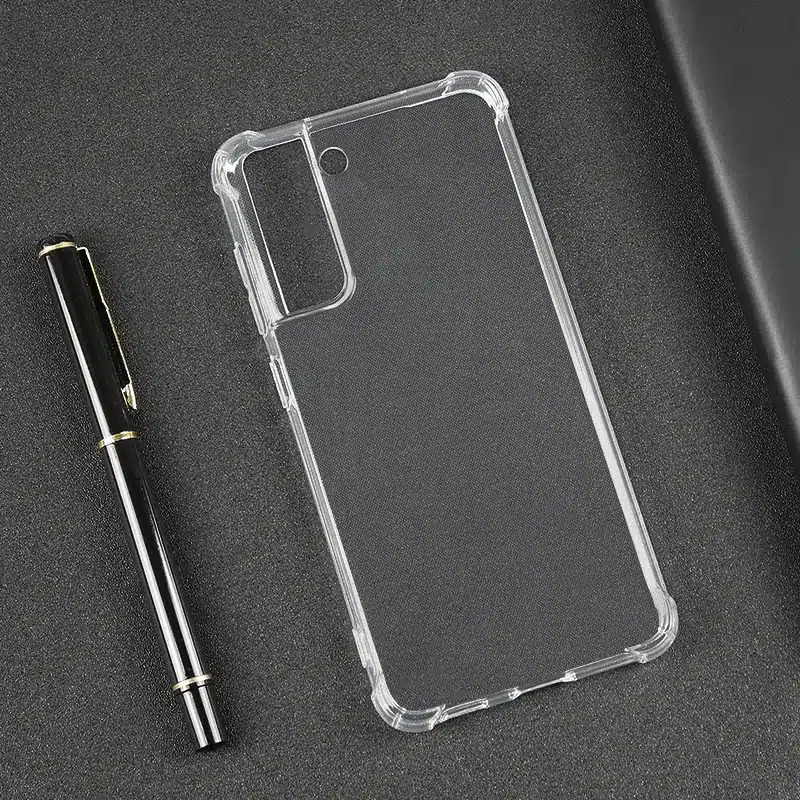
품질을 위한 디자인
표면 결함을 방지합니다:
1. 벽 두께가 균일하고 탈형 경사가 충분한지 확인합니다.
2. 모서리가 날카롭지 않도록 모서리를 서서히 전환합니다.
3. 필요한 경우 넓고 짧은 러너와 냉각 우물이 있는 적절한 위치의 게이트를 사용하세요.
4. 거칠기가 낮고 통풍이 잘되는 매끄러운 금형 표면을 유지합니다.
금형 표면 및 벽 두께
금형 표면은 거칠기가 낮고 매끄러워야 합니다(가급적 0.8 미만). 용융물에서 공기와 가스를 배출할 수 있도록 환기가 충분히 이루어지도록 합니다. PET를 제외하고 벽의 두께가 지나치게 얇지 않도록 최소 1mm를 유지합니다.
수정처럼 맑은 투명 제품을 위한 사출 파라미터
최적의 주입 매개변수
내부 스트레스와 표면 결함을 최소화합니다:
1. 특수 나사와 온도 조절 노즐을 사용합니다.
2. 수지의 분해 한계 내에서 더 높은 사출 온도를 사용합니다.
3. 용융된 재료의 점도를 극복할 수 있도록 높은 사출 압력을 가하되 변형을 일으킬 정도로 높지 않도록 합니다.
4. 가급적 느린-빠른-느린 다단계 주입을 사용하여 낮은 주입 속도를 선택합니다.
5. 압력 유지 시간과 성형 주기를 짧게 유지하여 함몰과 기포가 생기지 않도록 합니다.
6. 재료의 열화를 방지하기 위해 낮은 나사 속도와 배압을 사용합니다.
7. 최적의 냉각 및 제품 품질을 위해 금형 온도를 정밀하게 제어합니다.
투명 제품 성형 후 결함 방지
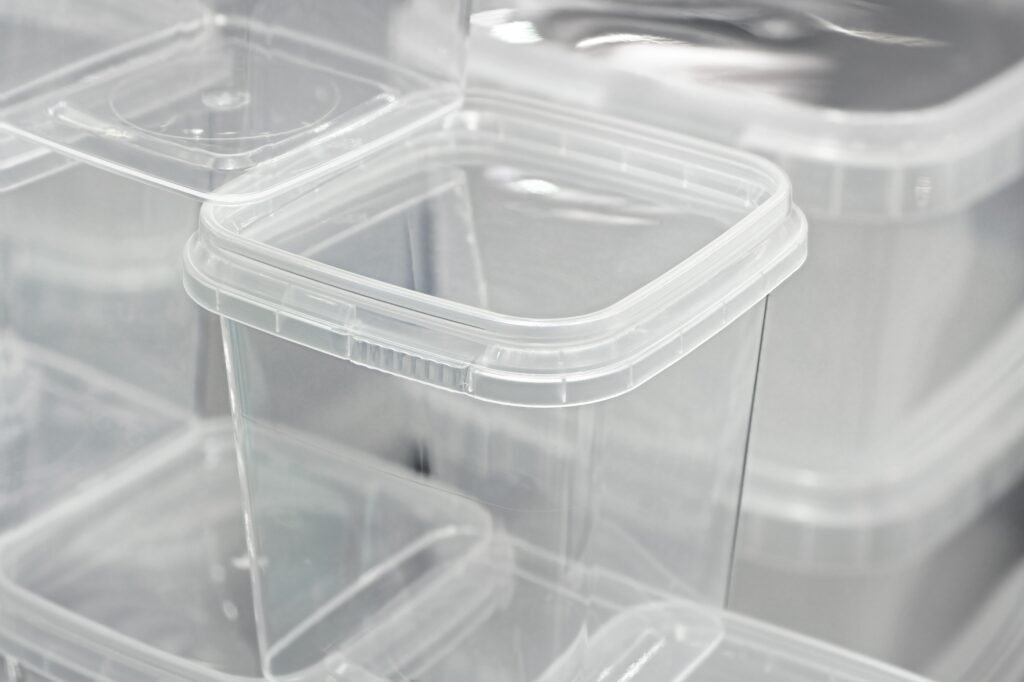
이형제 및 재활용 재료 사용
표면 품질 저하를 방지하기 위해 이형제 사용을 최소화합니다. 재활용 소재를 사용할 때는 20%를 초과하지 않도록 합니다.
제품 사후 처리
PET와 같은 특정 소재는 내부 응력을 제거하기 위해 후처리가 필요합니다. PMMA는 70~80℃에서 4시간 동안 건조하고, PC는 110~135℃에서 가열해야 하며, 제품에 따라 시간은 달라집니다. PET는 우수한 기계적 특성을 얻기 위해 양방향 드로잉을 거쳐야 합니다.