PC 플라스틱 사출 성형은 재료 열화, 표면 결함, 구조적 불일치 등의 일반적인 문제를 극복하기 위해 정밀도가 요구됩니다. 최종 제품의 취성, 물 주입구 근처의 가스 자국, 고르지 않은 흐름 패턴 등 각 문제는 부품의 성능과 미관에 직접적인 영향을 미칩니다. 이 가이드에서는 용융 공정 최적화를 통한 재료 무결성 보존, 목표 설계 조정을 통한 가스 트랩 제거, 취성 및 헤이즈 형성 해결, 분사 최소화를 위한 크로스 러너 시스템 개선 등 네 가지 핵심 솔루션을 자세히 살펴봅니다. 이러한 전략을 마스터하여 수율을 높이고 고품질의 PC 부품을 일관되게 납품하세요.
1. PC 플라스틱 열화 방지
용융 접착제가 끝나면 후면 케이블이 들어 올려지고 나사가 뒤로 이동하며 공기가 노즐로 펌핑되어 고온의 PC 재료와 혼합됩니다. PC 소재는 수분을 흡수하기 쉽기 때문에 공기 중 소량의 수분으로 인해 사출 부품에 은색 광선이 생성 될 수 있습니다.
비슷한 상황에서는 투명한 PVC 접착제를 부을 수 없습니다. 투명한 PVC는 접착제를 태우기 매우 쉽기 때문에 공기와 만나면 즉시 화학 반응을 일으켜 사출 성형 부품에 노란색 반점이 생기고 접착제를 태우는 검은 반점도 많이 생깁니다.
따라서 PC 소재 또는 투명 PVC 소재를 사출 성형 할 때는 녹인 후 케이블을 뒤집지 마십시오. 공정으로 인해 배압을 높여야 하고 노즐이 접착제를 뱉어낼 때 조금만 부으면 뱉어낸 접착제를 제거할 수 있습니다. 더 이상 노즐에 공기가 들어가지 않습니다.
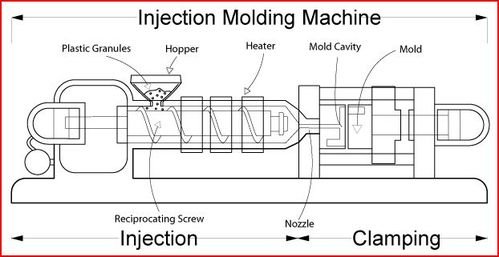
2. PC 플라스틱 가스 마크 제거
GPPS, K 소재, 투명 ABS, PC 소재 등 많은 투명 소재 중에서 PC 부품은 물 위치에서 가스 라인을 생성하기 매우 쉽고 제거하기가 매우 어렵습니다.
PC 재료의 유동성 때문에 이러한 재료에서는 상대적으로 열악하며 사출 성형시 고속 사출 접착제를 사용해야하며 그렇지 않으면 고르지 않거나 병 자국이 생기기 쉽습니다. 급속 사출의 결과는 입구 위치에서 캐비티 표면에 급속 사출 후 용융 접착제의 반동으로 인한 약간의 갇힌 가스입니다. 그리고 사출 부품이 두꺼울수록 갇힌 공기 면적이 커집니다. 높은 재료 온도로 인해 갇힌 가스 위치의 용융 접착제 표면이 산화되고 여기에 가스 막이 형성되어 용융 접착제를 금형 표면에서 분리하여 사출 부품의 표면이 서브 크로마틱 가스 패턴을 형성하여 사출 부품의 투명성에 영향을 미칩니다.
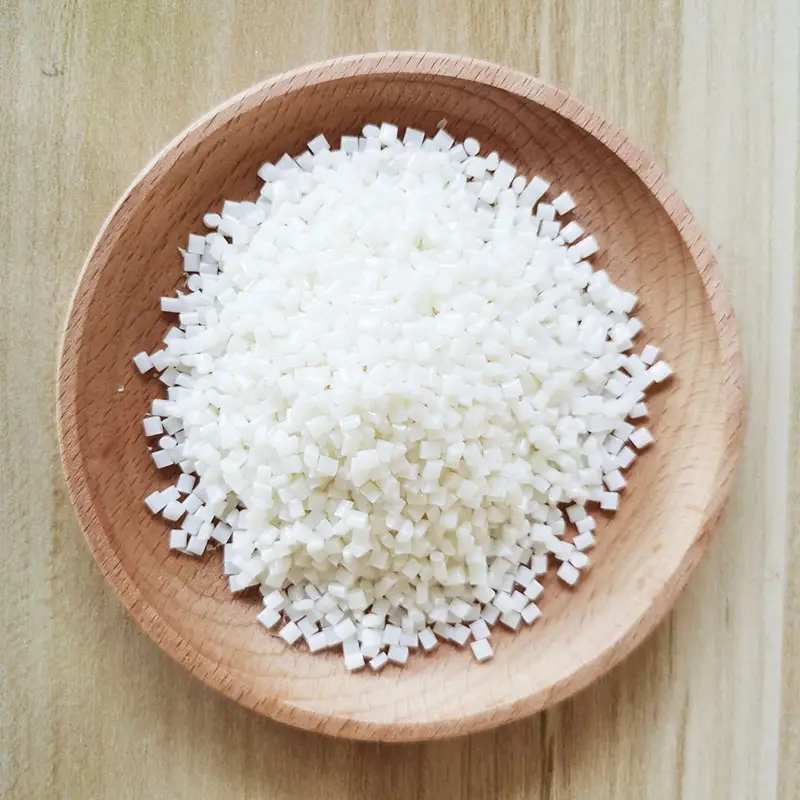
다른 투명 재료의 유동성이 훨씬 좋습니다. 따라서 금형을 채우는 것이 더 쉽고 병을 생산하기가 쉽지 않습니다. 따라서 토출 속도가 상대적으로 낮을 수 있고 입구 위치에 갇힌 가스가 존재하더라도 매우 미미하므로 서브 크로마틱 가스 라인을 형성하기가 쉽지 않습니다. 가스 라인이 생성되더라도 접착제보다 제거하기가 더 쉽습니다. 사출 속도와 압력을 조금만 낮추면 해결할 수 있으며 찌그러짐이나 재료 누락 문제가 없습니다. 속도를 줄이기위한 PC 재료는 진동이 재료 부족이 아니라 할 수 없습니다.
따라서 PC 소재의 물 흡입구 호흡 패턴 문제는 일반적으로 사용되는 투명 소재에서 제거하기가 매우 어렵고 사출 성형 문제라고 할 수 있으며이를 해결하기 위해 몇 가지 조치와 조정 기술이 필요하다고 할 수 있습니다.

3. PC 플라스틱 취성 솔루션
몇 년 전만 해도 PC 사출 성형 부품이 부서지는 문제를 거의 보지 못했습니다. 그 이유는 당시 사용된 PC 소재 브랜드가 상대적으로 적었기 때문인데, 보통 일본 PC7025A와 1250Y 두 가지 브랜드만 사용했습니다. 요즘에는 PC 소재를 생산하는 제조업체가 점점 더 많아지면서 자연스럽게 브랜드와 등급도 다양해졌습니다.
그러면 문제가 발생합니다. 다양한 등급의 PC 사출 성형 기술 공정이 동일하지 않고 가장 엄격한 공정 요구 사항이 다르기 때문에 PC7025A 및 1250Y의 동일한 사출 성형 공정을 사용하여 다른 등급의 PC 재료를 생산하면 문제가 발생할 수밖에 없으며 PC 사출 성형 부품이 충격의 취성을 견디지 못하는 경우가 종종 있습니다.
면밀한 연구 결과, 다양한 등급의 PC 소재의 내열성과 물리적 특성이 다르기 때문에 용융 온도와 건조 온도 및 건조 시간까지 사출 부품의 내충격성에 큰 영향을 미친다는 사실을 발견했습니다.
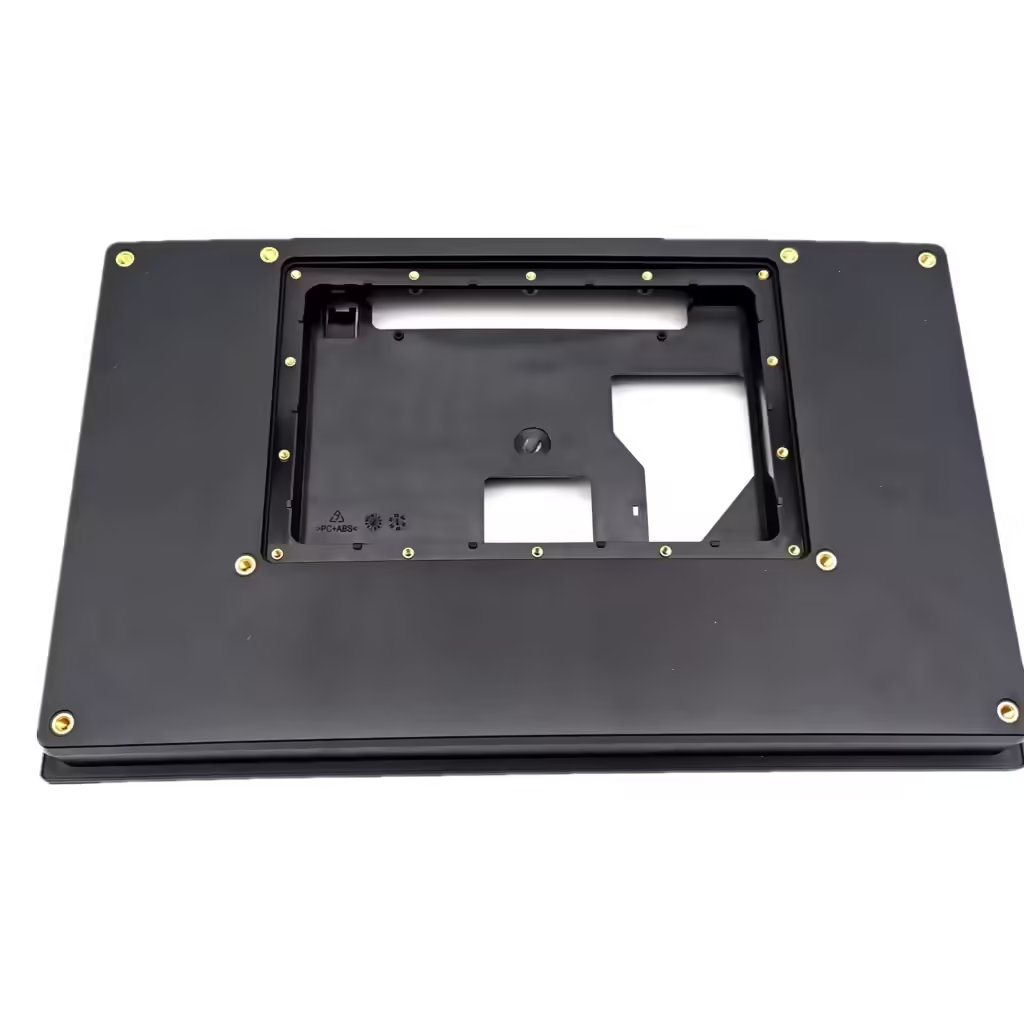
일반적으로 PC7025A 및 1250Y 소재를 생산할 때 용융 온도는 일반적으로 290~310도로 조정됩니다. 일부 등급의 PC 소재를 생산한 후 이 온도를 사출 성형에 사용하면 사출 성형 부품이 매우 부서지기 쉽습니다. 따라서 이러한 종류의 PC 소재의 경우 사출 온도는 290도를 초과하지 않는 것이 좋으며 일부는 취성 문제를 해결하기 위해 더 낮을 수 있습니다. 따라서 용융물의 유동성이 금형을 채우기에 충분한 한, 사출 부품이 부서지기 쉽고 강도 불안정을 유발하는 것을 방지하기 위해 더 낮은 온도를 사용하여 생산하는 것이 좋습니다.
두 번째는 건조 온도의 영향입니다. PC7025A와 1250Y는 일반적으로 4시간 이상 110~120도까지 구울 수 있습니다. 그러나 일부 브랜드의 PC 소재는 100도를 초과할 수 없습니다. 그렇지 않으면 사출 부품이 매우 부서지기 쉽고 흰색 안개가 발생하여 외관과 투명도에 영향을 미칩니다.
사람들의 관심을 끌기 쉽지 않고 잘못되기 쉬운 것은 건조 시간입니다. 일반적으로 PC7025A 및 1250Y 재료를 사출 성형 할 때 50kg 건조 호퍼를 채 웁니다. 수증기가없는 한 6 ~ 7 시간 동안 천천히 생산해도 문제가되지 않습니다.
그러나 일부 PC 재료를 건조 호퍼에서 4 시간 이상 구우면 사출 성형 부품에 명백한 흰색 안개가 생길뿐만 아니라 매우 부서지기 쉬워지고 시간이 길수록 더 부서지기 쉽고 흰색 안개가 많아지면 맥주가 흐려집니다. 이때 재료 한 통으로 6 시간 동안 생산하기에 충분하다면 재료의 절반 만 추가 할 수 있습니다. 사출 부품에 물과 가스 생산이있는 경우 조금 더 자주 조금 더 자주 사용하면 문제가 다시 발생하지 않습니다.
때때로 건조 호퍼에 원료 몇 개가 오랫동안 갇혀서 구워져야하는 흰색 안개가 몇 번 발생하고 때때로 재료가 통에서 흘러 나와 금형에 쏘아집니다.
이것이 생산에서 PC 사출 부품의 취성과 백무의 중요한 이유입니다. 따라서 다양한 등급의 PC 사출 부품을 생산하려면 다양한 등급의 원료의 사출 성형 공정의 특성과 요구 사항에주의를 기울여야합니다. 물론 다양한 브랜드 자체의 성능이 다르기 때문에 강도와 내 충격성이 다르고 일부 브랜드의 내 충격성이 정말 열악합니다.
따라서 향후 생산에서 PC 사출 부품에 갑자기 부서지기 쉬운 문제가 나타나고 투명성이 부족한 경우 용융 온도와 건조 온도 및 시간을 우선적으로 고려할 수 있으므로 사람들이 많은 우회로를 취할 수 있습니다.
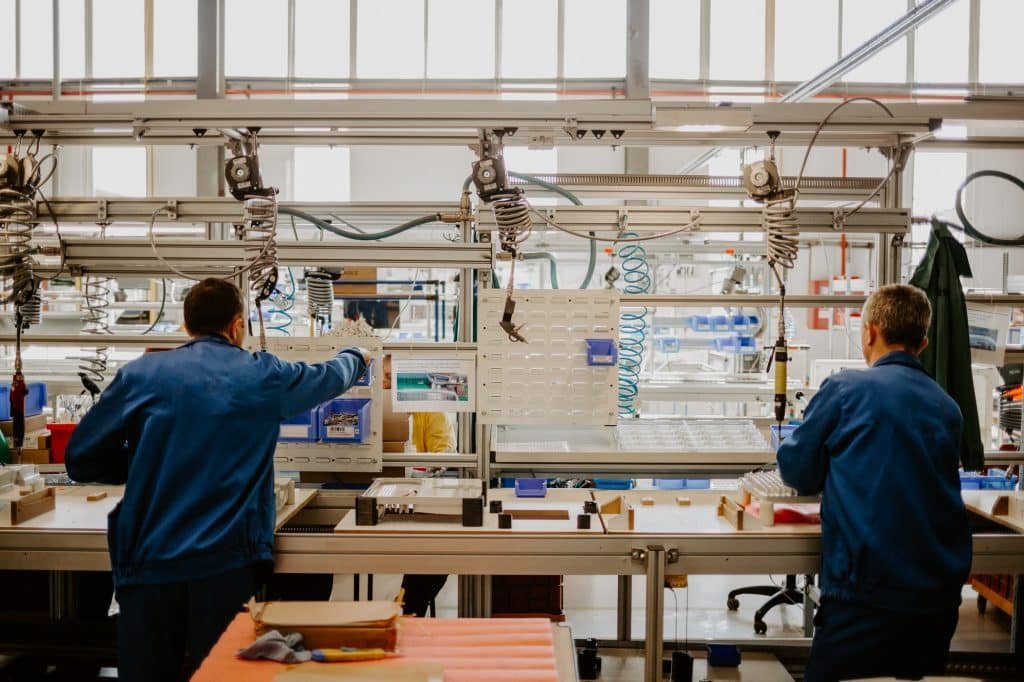
4. PC 플라스틱 분사 방지
때로는 흐름 경로가 너무 길기 때문에 냉각 앞의 용융물이 너무 많아 사출 부품에 제트와 진동이 발생하는 경우가 있는데, 이 점에서 PC 소재가 특히 두드러지고 투명 PVC가 그 뒤를 잇습니다.
이것이 때때로 용융 온도가 매우 높게 상승한 이유입니다. 사출 부품이 여전히 슛이나 찌그러짐을 제거하지 못하는 이유입니다.
이때 크로스 러너의 두 끝을 각각 몇 센티미터씩 연장하면 앞에서 냉각 된 저온 용융물이 연장 된 크로스 러너로 유입되어 캐비티로 유입되지 않고 결함이 잘 개선 될 수 있습니다. 이 방법은 다른 플라스틱에도 개선 효과가있을 것으로 생각되며 PC 및 PVC 재료의 개선이 더 분명해질 것입니다.
따라서 기계를 어떻게 조정해도 제트 또는 지진 자국을 해결할 수없는 경우이 방법을 시도 할 수 있습니다.