플라스틱 금형 설계 및 제조 담당자는 고객이 제공 한 위의 기준과 요구 사항에 따라 금형 설계를 신중하게 수행해야하며, 금형 설계시 위의 내용을 하나씩 구체화하여 도면 및 기술 문서 형태로 표현합니다. 플라스틱 금형 설계 및 제조의 일반적인 절차를 자세히 알아 보겠습니다.
1. 플라스틱 금형 설계 최적화를 위한 청사진 분석
플라스틱 금형의 금형 설계 및 제조 전에 먼저 제품 도면 또는 실제 세부 분석 및 소화, 그 내용에는 다음이 포함됩니다:

a. 제품 지오메트리
b. 제품 치수, 공차 및 설계 표준;
c. 제품 기술 요구 사항(기술 조건);
d. 제품에 사용된 플라스틱의 이름과 종류;
e. 제품 표면 요구 사항.
2. 금형 호환성을 위한 사출기 선택
사출기의 사양 결정은 주로 플라스틱 제품의 크기와 생산 배치에 따라 다르며, 사출기 선택시 설계자는 주로 가소 화율, 사출량, 클램핑 력, 설치 금형 생산 면적 (사출기로드 간격), 체적 비율, 압출 형태 및 압출 길이를 고려합니다. 고객이 사용 된 사출 모델 번호 또는 사양을 제공하면 설계자는 해당 매개 변수를 비교하고 요구 사항을 충족하기에는 너무 무서운 경우 고객과 교체에 대해 논의해야합니다.
3. 금형 제조의 캐비티 레이아웃 전략
캐비티 수는 주로 제품의 투영 면적, 기하학적 모양(측면 코어 포함 여부), 제품의 정확도에 따라 결정됩니다. 그리고 경제성이 결정합니다. 캐비티 수는 주로 다음 요소에 따라 결정됩니다:
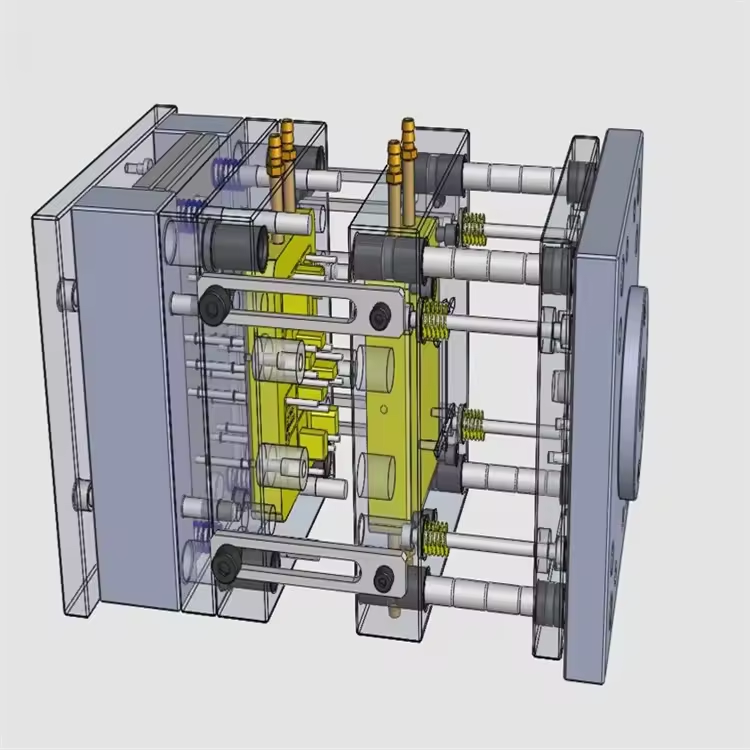
a. 제품 무게 및 사출기 사출량
b. 제품 투사 영역 및 사출기 잠금력
c. 금형의 전체 크기 및 사출기 마운팅 브래킷 금형의 유효 면적(사출기 로드 사이의 거리)
d. 제품 정확도
e. 제품 색상
f. 제품에 사이드 코어가 있는지 여부 및 처리 방법
g. 제품 생산 배치(월별 배치 또는 연간 배치).
h. 경제적 이익; (모델당 생산량)
이러한 요소 중 일부는 상호 제한되어 있으며 설계 계획을 결정할 때 주요 조건을 충족하도록 조정할 필요가 있습니다. 캐비티 수가 결정된 후 캐비티가 배치, 즉 캐비티의 위치가 배치됩니다. 캐비티 배열에는 금형 크기, 주입 시스템의 설계, 주입 시스템의 균형, 코어 슬라이더 메커니즘의 설계, 플러그인 및 코어의 설계, 열 전달 시스템의 설계가 포함됩니다. 이러한 문제에는 비교적 완벽한 설계를 달성하기 위해 특정 설계 프로세스에서 조정해야 하는 분할 표면 및 게이트 위치 선택도 포함됩니다.
4. 정밀 금형 기능을 위한 파팅 표면 설계
일부 외국 제품 도면에도 분리면이 명시되어 있지만 금형 설계자가 많은 금형 설계를 결정해야 합니다. 일반적으로 평면의 분리 표면은 다루기 쉽기 때문에 3차원 부품의 분리 표면을 만질 때 특별한 주의가 필요할 수 있습니다. 분리 표면의 선택은 다음 원칙을 따라야 합니다:
a. 제품의 외관에 영향을 미치지 않는 제품, 특히 외관에 대한 명확한 요구 사항이 있는 제품의 경우 타이핑이 외관에 미치는 영향에 주의를 기울여야 합니다.
b. 제품 정확성 보장 지원
c. 금형 가공에 도움
d. 주입 시스템, 배기 시스템 및 냉각 시스템의 설계에 도움이됩니다.
e. 제품 성형, 절단 제품 유지 보수 및 금형을 열 때 움직이는 금형 측에 제품을 남겨 두는 데 도움이됩니다;
f. 간편한 금속 플러그인 설치
5. 측면 코어 풀링 메커니즘: 설계 및 구현
측면 분리 메커니즘을 설계할 때는 안전성과 신뢰성을 확보하고 이젝터 메커니즘과의 간섭을 피해야 합니다. 그렇지 않으면 환류 메커니즘을 금형에 설정합니다.
6. 효율적인 플라스틱 흐름을 위한 게이트 시스템 설계
게이팅 시스템의 설계에는 메인 채널의 선택, 다이버터 채널의 단면 모양 및 크기 결정, 게이트 위치 선택, 게이트의 형태 및 게이트의 단면 크기 결정이 포함됩니다. 포인트 게이트를 사용하는 경우 다이버터가 떨어지지 않도록하기 위해 게이트 해제 장치는 먼저 주입 시스템을 설계 할 때 게이트 위치 선택에주의를 기울여야합니다. 게이트 위치의 선택은 제품의 성형 품질 및 원활한 사출 공정과 직접적인 관련이 있습니다. 다음 원칙에 따라 게이트 위치를 선택하십시오.
a. 게이트 위치는 사용 중 금형 가공 및 게이트 청소를 용이하게 하기 위해 가능한 한 파팅 표면에서 선택해야 합니다;
b. 게이트 위치와 캐비티의 각 부분 사이의 거리는 가능한 한 일정하게 유지하여 흐름이 짧아지도록 합니다.
c. 플라스틱이 캐비티로 흘러 들어갈 때 게이트 위치는 플라스틱 주입을 용이하게 하기 위해 캐비티의 더 넓고 두꺼운 부분을 기준으로 해야 합니다.
d. 플라스틱이 캐비티로 흘러 들어갈 때 캐비티 벽, 코어 및 플러그인과 직접 충돌하지 않도록 하세요. 이렇게 하면 플라스틱이 캐비티의 여러 부분으로 빠르게 흘러 들어가 코어와 플러그인의 변형을 방지할 수 있습니다.
e. 제품에 용접 자국이 생기지 않도록 제품의 중요하지 않은 부분에 용접 자국이 생기지 않도록 합니다;
f. 게이트 위치 및 플라스틱 유입 방향, 플라스틱이 캐비티로 유입될 때 캐비티의 평행 방향을 따라 고르게 흘러야 캐비티의 가스 배출에 도움이 됩니다;
g. 게이트는 씰을 쉽게 제거할 수 있는 부분에 설치해야 하며 제품 외관에 영향을 주지 않도록 주의하세요.
위는 플라스틱 금형 설계 및 제조의 일반적인 절차에 대한 자세한 작업입니다. 자세한 정보가 필요하면 언제든지 BFY Mold에 문의 할 수 있습니다!