주사 성형 금형 EDM은 정밀 캐비티 금형 제조에 널리 사용됩니다.
소위 “미러 EDM”은 일반적으로 표면 거칠기 값이 Ra 0.2μm 미만이며 표면에 미러 반사 효과를 갖는 EDM을 의미합니다. 일부 정밀 가공에 사용되는 미러 EDM은 수동 연마 공정을 대체할 수 있으며 부품의 품질을 향상시켜 실용적인 의미를 갖습니다.
1. 처리 유형
전기 방전 가공의 거울 효과는 전기 방전 가공 과정에서 생성되는 탄소 검은색 층과 직접적으로 관련이 있습니다. 가공 부위가 빠르게 균일한 탄소 검은색 층을 형성할 수 있다면, 이는 거울 효과를 쉽게 구현할 수 있음을 의미합니다.
2. 금형 강철
경화강 EDM에서는 거울 효과를 빠르게 달성할 수 있지만, 어떤 경우에도 다른 경화강에서는 달성할 수 없습니다. 또한, 금형강의 경도가 더 높기 때문에 EDM 거울 효과가 더 우수합니다.
3. 미러 EDM의 전극에 대한 몇 가지 요구 사항
거울 EDM에 일반적으로 사용되는 전극 재료는 구리와 크롬 구리로, 후자는 전극 손실이 덜 발생합니다. 구리 재료를 선택할 때는 균일한 조직과 최소한의 불순물을 확보하는 것이 중요합니다. 품질이 낮은 구리는 거울 가공 시 심각한 전극 손실과 표면 주름 현상 등 이상 현상을 유발할 수 있습니다. 구리 합금 전극은 낮은 수준의 전극 손실을 달성할 수 있지만, 만족스러운 거울 효과를 내지 못합니다.
미러 EDM에 대한 참고 사항
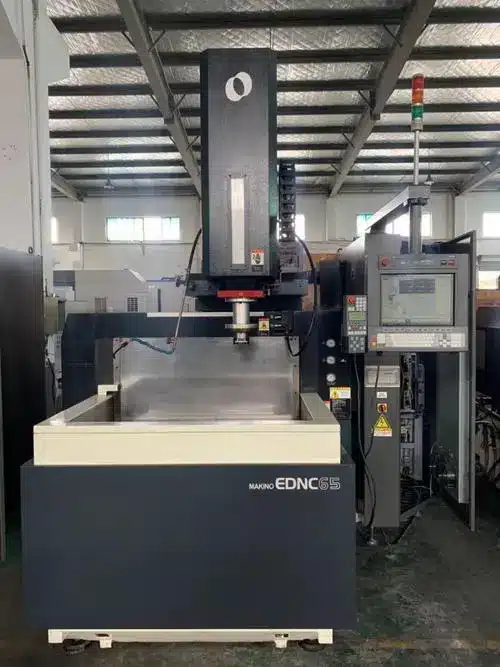
a. 거울 EDM의 가공 여유량을 조절합니다.
EDM 공정은 거친 가공부터 마무리 가공까지의 과정입니다. 먼저, 거친 가공 전극을 사용하여 특정 가공 품질(치수 정확도, 형상 정확도, 위치 정확도, 표면 거칠기)을 보장하는 조건 하에서 대량의 금속을 부식시켜 가공 시간을 단축하고 가공 효율을 향상시킵니다. 그 다음 정밀 가공 전극으로 교체하고 더 작은 방전 에너지를 사용하여 정밀 가공을 완료합니다. 거친 가공이든 정밀 가공이든 여러 가지 방전 조건이 사용되며, 전류는 크에서 작으로 변화하며, 깊이 피드를 통해 가벼운 바닥을 수리하고, 가벼운 측면의 이동 수리를 통해 진행됩니다.
b. 거울 가공 시 배출 매개변수의 합리적 사용 및 가공 제어
음극 처리를 사용하는 처리에서 일부 비 주 전기 매개 변수의 선택도 매우 중요하며 기존 처리의 선택은 더 오래 설정하는 방전 시간, 리프팅 도구 높이가 짧고 리프팅 도구 속도가 너무 빠를 수 없으며이 설정의 목적은 거울 처리에서 자체적으로 많은 전기 부식 제품을 생성하지 않기 때문에 안정적인 소 에너지 전기 부식 공정을 유지하는 것입니다. 너무 자주 나이프 리프팅 동작이 지속적이고 안정적인 방전을 방해합니다.
경면 가공의 전기 부식 능력은 매우 약하며, 가공 시간이 오래 걸립니다. 경면 가공의 치수 변화가 매우 작기 때문에, 실제로는 연마 역할만 수행되며, 요구되는 표면 거칠기까지 가공이 완료되면 충분합니다. 따라서 CNC EDM 기계 공구의 타이밍 가공 기능을 사용할 수 있으며, 경험에 따라 가공 시간을 결정할 수 있습니다.
c. 분말 혼합 기술을 활용한 대면적 가공을 통해 거울 가공 효과를 달성합니다.
혼합 분말 EDM은 EDM의 표면 거칠기를 개선하는 기술입니다.
소위 혼합 분말 EDM은 가공 표면에 거울 같은 효과를 얻기 위해 작업 유체에 실리콘 분말, 알루미늄 분말, 크롬 분말 및 관련 첨가제를 추가하는 것을 의미합니다. 혼합 분말 가공 기술을 사용하면 동일한 전기 파라미터 조건 하에서 혼합 분말 가공 기술을 사용하지 않을 때보다 더 빠른 가공 속도(마무리 시간을 20~30% 단축)와 더 우수한 표면 거칠기를 얻을 수 있습니다. EDM의 넓은 면적에 대해显著한 개선 효과를 나타냅니다.