Kalıpları nasıl hızlı ve başarılı bir şekilde deneyebilirsiniz?
Birçok plastik parça ürünü, kalıp açıldıktan sonra yeni kalıplardan numune alınmasını ve test edilmesini gerektirir. Kalıp testi sırasında, gecikmeleri ve komplikasyonları önlemek için hızlı sonuçlar ve sorunsuz bir süreç hedefliyoruz. Kalıp testi süresi boyunca kalıp testi nasıl tamamlanır? İşte bilmemiz gereken iki nokta:
1. Kalıp tasarımcıları ve imalat teknisyenleri bazen hata yaparlar. Kalıpları denerken dikkatli olmazsak, küçük hatalar büyük hasarlara neden olabilir.
2. Kalıp denemesinin sonucu, gelecekteki üretimin düzgünlüğünü sağlamaktır.
Kalıp denemesi sırasında uygun adımların izlenmemesi ve doğru kayıtların tutulmaması seri üretimin sorunsuz akışını tehlikeye atabilir. Kalıbın sorunsuz bir şekilde kullanılması halinde kar geri kazanımının hızla artacağını daha fazla vurguluyoruz. Aksi takdirde, maliyet kaybı kalıbın kendi maliyetinden daha büyük olacaktır.

9 Küf Denemesi Öncesi Önlemler
1. Kalıpla ilgili bilgileri anlamak
Kalıp tasarım çizimlerini edinin, bunları iyice analiz edin ve kalıp teknisyenlerini deneme sürecine dahil edin.
2. Önce tezgah üzerindeki mekanik koordinasyonunu kontrol edin:
Çizikler, eksik veya gevşek parçalar olup olmadığını kontrol edin ve kayar plakaya doğru düzgün hareket ettiğinden emin olun. Su kanallarında ve hava borusu bağlantılarında sızıntı olup olmadığını inceleyin ve kalıp açıklığındaki herhangi bir kısıtlamayı doğrudan kalıp üzerinde işaretleyin. Bu kontrollerin kalıbı asmadan önce yapılması zaman kazandırabilir ve daha sonra gereksiz sökme işlemlerini önleyebilir.
3. Tüm kalıp parçalarının doğru çalıştığı onaylandıktan sonra, test için uygun bir enjeksiyon makinesi seçin. Seçim yaparken dikkat edin.
(a) Enjeksiyon kapasitesi
(b) Kılavuz çubuk genişliği
(c) Büyük ayrılış
(d) Aksesuarlar
Yukarıdakilerin eksiksiz olup olmadığı vb. Her şeyin sorunsuz olduğu onaylandıktan sonra, bir sonraki adım kalıbı asmaktır. Asarken, kalıbın düşmesine neden olabilecek gevşeme veya kırılmayı önlemek için tüm sıkıştırma şablonlarını kilitlemeden ve kalıbı açmadan önce asma kancalarının çıkarılmadığından emin olun.
Kalıbı kurduktan sonra, düzgün çalıştıklarını doğrulamak için sürgü plakası, ejektör pimi, diş çıkarma yapısı ve limit anahtarı dahil olmak üzere her bir parçanın mekanik hareketlerini titizlikle inceleyin. Ve enjeksiyon memesi ile besleme portunun hizalı olup olmadığına dikkat edin. Bir sonraki adım kalıp kapama eylemine dikkat etmektir. Bu sırada kalıp kapama basıncı düşürülmelidir. Manuel ve düşük hızlı kalıp kapatma sırasında, herhangi bir düzensiz hareket veya anormal ses olup olmadığını dikkatlice gözlemleyin ve dinleyin.
4. Kalıp sıcaklığını arttırın:
Kalıbı gerekli üretim sıcaklığına yükseltmek için hammadde performansına ve kalıp boyutuna göre uygun bir kalıp sıcaklık kontrolörü seçin. Kalıp sıcaklığını artırdıktan sonra, çeliğin termal genleşmesi nedeniyle sıkışmayı önlemek için her bir parçanın hareketini tekrar kontrol edin. Gerilme ve titreşimi önlemek için kaymaya çok dikkat edin.
5. Fabrika deneysel bir plan takip etmiyorsa, kalıp denemeleri sırasında her seferinde yalnızca bir koşulun ayarlanması tavsiye edilir. Bu, bireysel değişikliklerin bitmiş ürün üzerindeki etkisini ayırt etmeye yardımcı olur.
6. Hammaddelere bağlı olarak, onları uygun şekilde kavurun.
7. Deneme kalıpları ve gelecekteki seri üretim için mümkün olduğunca aynı hammaddeleri kullanın.
8. Kalıbı tamamen düşük kaliteli malzemelerle test etmeyin. Bir renk gereksinimi varsa, birlikte bir renk testi düzenleyebilirsiniz.
9. İç gerilim gibi sorunlar genellikle ikincil işlemeyi etkiler. İkincil işleme, kalıp denemesinden sonra ve bitmiş ürün stabil hale geldikten sonra gerçekleştirilmelidir. Kalıbı yavaşça kapattıktan sonra, kalıp kapama basıncını ayarlayın ve doğru olup olmadığını kontrol etmek için birkaç kez çalıştırın. Eşit olmayan kalıplama basıncı, bitmiş üründe çapak ve kalıp deformasyonunu önleyecektir.
Yukarıda belirtilen adımları tamamladıktan sonra, kalıp kapama hızını ve basıncını düşürün ve emniyet tokasını ve çıkarma strokunu yapılandırın. Daha sonra, normal kalıp kapama hızını ve basıncını ayarlayın. Daha büyük stroklu bir limit anahtarı mevcutsa, kalıp açma strokunu biraz kısaltın ve daha büyük stroktan önce yüksek hızlı kalıp açma eylemini devre dışı bırakın. Bu önlem, kalıp yükleme sırasında yüksek hızlı hareket stroku düşük hızlı olandan daha uzun olduğu için gereklidir. Ek olarak, plastik makinesindeki mekanik ejektör çubuğunu, ejektör plakasının veya soyma plakasının kuvvet nedeniyle deforme olmasını önlemek için tam hızlı kalıp açma eyleminden sonra çalışacak şekilde ayarlayın.
İlk kalıp enjeksiyonunu yapmadan önce aşağıdaki maddeleri kontrol edin:
(a) Besleme strokunun çok uzun veya yetersiz olup olmadığı.
(b) Basıncın çok yüksek veya çok düşük olup olmadığı.
(c) Kalıp doldurma hızının çok hızlı veya çok yavaş olup olmadığı.
(d) İşlem döngüsünün çok uzun veya çok kısa olup olmadığı.
Bitmiş ürünün kısa atışlardan, kırılmadan, deformasyondan, çapaklardan ve hatta kalıbın hasar görmesinden kaçınmak için.
İşleme döngüsü çok kısaysa, ejektör pimi bitmiş ürüne nüfuz edecek veya halka soyulacak ve bitmiş ürün zarar görecektir. Bu tür bir durumda bitmiş ürünü çıkarmanız iki ila üç saatinizi alabilir.
İşleme döngüsü çok uzunsa, kauçuk malzemenin büzülmesi nedeniyle kalıp çekirdeğinin zayıf kısımları kırılabilir.
Elbette, küf davası sırasında ortaya çıkabilecek tüm sorunları önceden tahmin edemezsiniz, ancak önceden zamanında ve tam olarak düşünülmüş önlemler almak ciddi ve pahalı kayıplardan kaçınmanıza yardımcı olabilir.

Küf Davasının 10 Ana Adımı
Seri üretim sırasında gereksiz zaman ve sorunlardan kaçınmak için, işleme koşullarını etkili bir şekilde ayarlamak ve kontrol etmek için sabır gereklidir. Bu, optimum sıcaklık ve basınç ayarlarının bulunmasını ve günlük işlemler için standart kalıp deneme prosedürlerinin oluşturulmasını içerir.
1. Varildeki plastik malzemenin doğru olup olmadığını ve yönetmeliklere göre pişirilip pişirilmediğini kontrol edin (deneme kalıplama ve üretimde farklı hammaddeler kullanılırsa, farklı sonuçlar elde edilmesi muhtemeldir).
2. Sıkışmaya neden olabilecek kötü kauçuk veya döküntülerin kalıba enjekte edilmesini önlemek için malzeme tüpünün iyice temizlendiğinden emin olun. Hem malzeme tüpü hem de kalıp sıcaklıklarının işlenen hammaddeler için uygun olduğunu doğrulayın.
3. Tatmin edici bir görünüme sahip bitmiş bir ürün üretmek için basıncı ve enjeksiyon hacmini ayarlayın. Ancak çapaklara izin verilmemelidir. Özellikle bazı kalıp boşluğu ürünleri tamamen katılaşmadığında, kalıp dolduğu için çeşitli kontrol koşullarını ayarlamadan önce bunu düşünmelisiniz. Hızdaki küçük bir değişiklik kalıp dolumunda önemli değişikliklere neden olabilir.
4. Sabırlı olun ve makine ve kalıp koşulları dengelenene kadar bekleyin. Orta büyüklükteki makinelerin bile 30 dakikadan fazla beklemesi gerekebilir. Bu süreyi bitmiş ürünle ilgili olası sorunları gözden geçirmek için kullanın.
5. Vida ilerleme süresi geçit plastiğinin katılaşma süresinden daha kısa olamaz, aksi takdirde bitmiş ürünün ağırlığı azalacak ve bitmiş ürünün performansı tehlikeye girecektir. Ve kalıp ısıtıldığında, bitmiş ürünü sıkıştırmak için vida ilerleme süresinin de uzatılması gerekir.
6. Toplam işlem döngüsünü azaltmak için makul ayarlamalar yapın.
7. Yeni ayarlanan koşulları kararlı hale gelene kadar en az 30 dakika boyunca çalıştırın ve ardından sürekli olarak en az bir düzine tam kalıp numunesi üretin. Kapların üzerine tarih ve miktarı işaretleyin ve gerçek çalışmalarının kararlılığını test etmek için kalıp boşluklarına göre yerleştirin. ve makul kontrol toleransları elde edin. (Özellikle çok gözlü kalıplar için değerlidir).
8. Sürekli numuneleri ölçün ve önemli boyutlarını kaydedin (numuneler ölçülmeden önce oda sıcaklığına kadar soğutulmalıdır).
9. Her bir kalıp numunesinin ölçülen boyutlarını karşılaştırırken lütfen unutmayın:
(a) Boyutların sabit olup olmadığı.
(b) Zayıf sıcaklık kontrolü veya yağ basıncı kontrolü gibi makine işleme koşullarının hala değişmekte olduğunu gösteren, artma veya azalma eğiliminde olan belirli boyutlar var mı?
(c) Boyutlardaki değişikliğin tolerans aralığı içinde olup olmadığı.
10. Bitmiş ürünün boyutları çok fazla değişmiyorsa ve işleme koşulları normalse, her bir kalıp boşluğundaki bitmiş ürünün kalitesinin kabul edilebilir olup olmadığını ve boyutların izin verilen tolerans dahilinde olup olmadığını gözlemlemek gerekir. Kalıp boyutunun doğru olup olmadığını kontrol etmek için ortalama değerden sürekli olarak daha büyük veya daha küçük olan kalıp boşluğu numaralarını kaydedin.
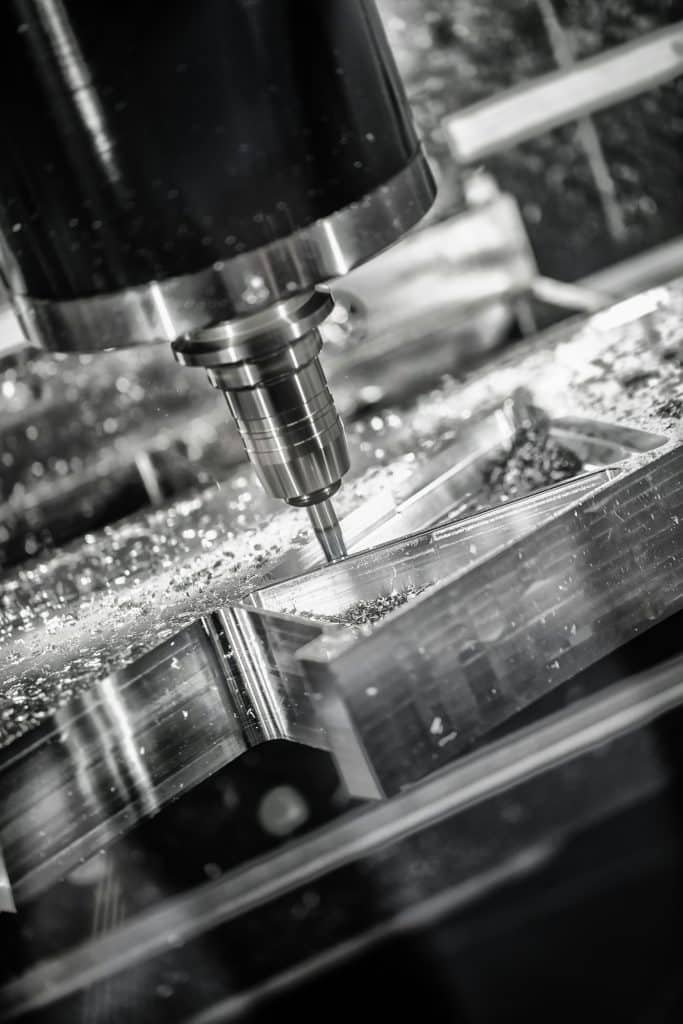
Verileri Kaydetme ve Analiz Etme
Kalıpların ve üretim koşullarının değiştirilmesi ihtiyaçlarını karşılamak ve gelecekteki seri üretim için bir referans olarak verileri kaydedin ve analiz edin.
1. Eriyik sıcaklığını ve hidrolik yağ sıcaklığını stabilize etmek için işleme operasyon süresini uzatın.
2. Makine koşullarını tüm bitmiş ürünlerin boyutunun çok büyük veya çok küçük olmasına göre ayarlayın. Büzülme oranı çok büyükse ve bitmiş üründe yetersiz enjeksiyon malzemesi var gibi görünüyorsa, referans için kapı boyutunu da artırabilirsiniz.
3. Her bir kalıp boşluğunun boyutu çok büyük veya çok küçükse, düzeltin. Kalıp boşluğunun ve kapısının boyutu hala doğruysa, kalıp doldurma hızı, kalıp sıcaklığı ve her bir parçanın basıncı gibi makine koşullarını değiştirmeyi denemeli ve bazı kalıpları kontrol etmelisiniz. Boşluk dolumunun yavaş olup olmadığı.
4. Bitmiş kalıp boşluğu ürünlerinin uyumuna veya kalıp çekirdeğinin yer değiştirmesine göre, bireysel düzeltmeler yapın. Tekdüzeliği iyileştirmek için kalıp doldurma oranını ve kalıp sıcaklığını ayarlamayı da deneyebilirsiniz.
5. İşleme koşullarında değişikliklere neden olacak yağ pompası, yağ valfi, sıcaklık kontrolörü vb. arızalar gibi enjeksiyon makinesinin arızalarını kontrol edin ve düzeltin. En mükemmel kalıp bile bakımı kötü yapılmış bir makinede iyi performans gösteremez.
Kaydedilen tüm değerleri gözden geçirdikten sonra, düzeltilmiş numunelerin iyileşip iyileşmediğini görmek için bir dizi numuneyi düzeltme ve karşılaştırma için saklayın.
Son Önemli Hususlar
İşleme döngüsü sırasındaki çeşitli basınçlar, eriyik ve kalıp sıcaklığı, malzeme tüpü sıcaklığı, enjeksiyon eylem süresi, vida besleme süresi vb. dahil olmak üzere kalıp deneme süreci sırasında numune incelemesinin tüm kayıtlarını uygun şekilde saklayın. Kısacası, gelecekte yardımcı olacak tüm kayıtlar tutulmalıdır. Aynı işleme koşullarını başarılı bir şekilde oluşturmak için kullanılabilecek veriler, kalite standartlarını karşılayan ürünler elde etmek için kullanılabilir.
Şu anda, fabrikalarda kalıp testi sırasında kalıp sıcaklığı genellikle göz ardı edilmektedir ve kısa süreli kalıp testi ve gelecekteki seri üretim sırasında kalıp sıcaklığını kontrol etmek zordur. Yanlış kalıp sıcaklığı numunenin boyutunu, parlaklığını, büzülmesini, akış çizgilerini ve malzeme eksikliğini etkileyebilir. Kalıp sıcaklık kontrolörü kullanılmazsa, ileride seri üretimde zorluklar ortaya çıkabilir.

BFY Kalıp, ürün kavramını ürün şekillendirme ile bütünleştirir ve esas olarak plastik kalıp ürün geliştirme, kalıp tasarımı ve üretimi, ürün enjeksiyon kalıplama, ürün yüzey işleme ve diğer hizmetleri üstlenir. Kalıp tasarımı ve kalıp imalatında 20 yılı aşkın üretim tecrübesi ile enjeksiyon kalıplama işleme endüstrisi sizin için rekabetçi kalıplar oluşturabilir. Ücretsiz çizim optimizasyonu için bugün bize ulaşın.