Aşırı kalıplamada, sert bileşenlerin dikkatli bir şekilde konumlandırılması, ölçeklenebilirliğin sağlanması ve parça bozulmasını önlemek için taslak deliklerin dahil edilmesi gerekir.
Piyasada giderek daha popüler hale gelen iki vuruşlu kalıplama, boyamaya gerek kalmadan ürün estetiğini geliştirir, ancak maliyetlidir ve ileri düzeyde beceri gerektirir.
İster iki vuruşlu kalıplama ister aşırı kalıplama olsun, her ikisinde de iki tür plastik kompozit enjeksiyonu kullanılır: önce sert parçalar, sonra yumuşak parçalar. Benzer olsalar da farklı süreçlerdir. Aşağıda, BFY kalıp mühendisleri farklılıkları tanımlamaktadır.
İki Atışlı Kalıplama ve Üst Kalıplama Arasındaki Farklar
A. İki Atışlı Kalıplama
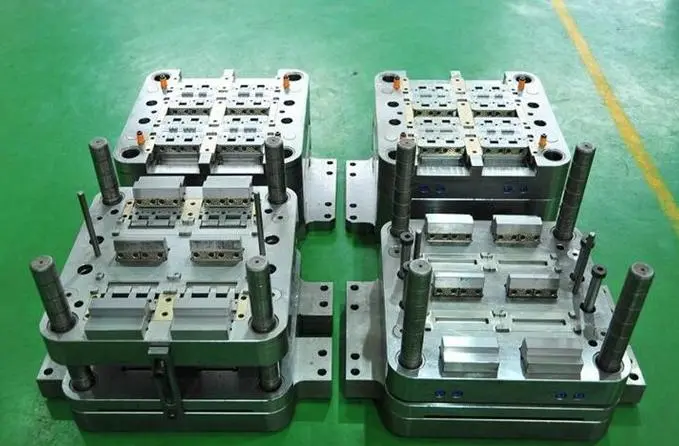
İki plastik malzeme, tek kalıplı bir ürün çıktısı ile iki adımda aynı makineye enjekte edilir. Genellikle çift malzemeli enjeksiyon olarak adlandırılır, tipik olarak bir kalıp seti ile tamamlanır ve özel bir iki vuruşlu enjeksiyon makinesi gerektirir.
İki vuruşlu kalıplar, iki reçine türünü ve rengini tek bir üründe birleştirerek montaj ve işlem sonrası süreçleri azaltır. Bu yaklaşım yapıştırma ve baskı maliyetlerinden tasarruf sağlar, görsel çekiciliği artırır ve ürün kalitesini ve değerini yükseltir. Ayrıca, kaymayı önleyici özellikler ve gelişmiş ergonomik his gibi işlevsellik sağlar.
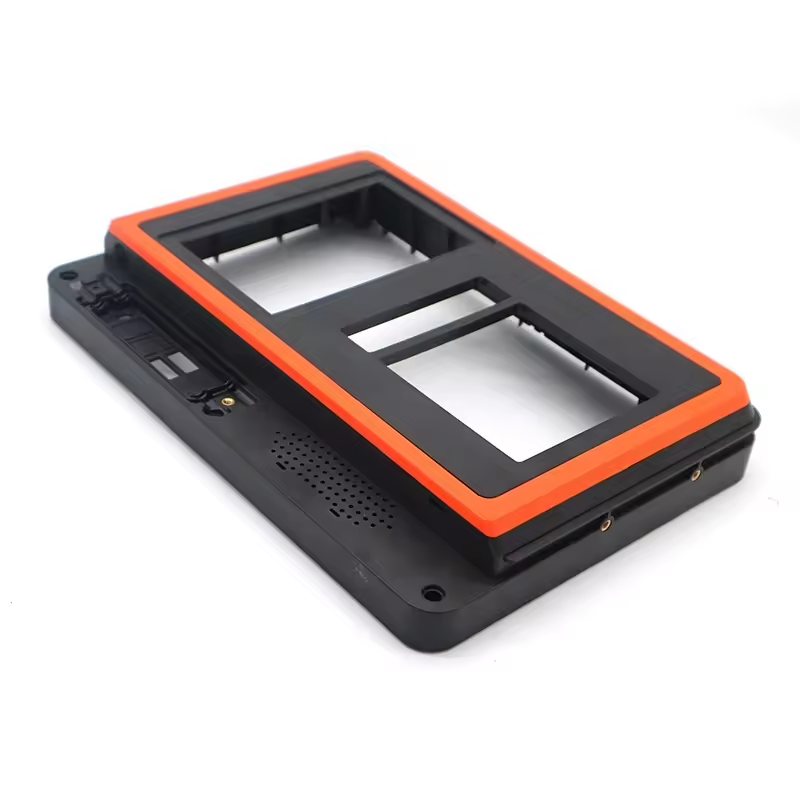
Çift vuruşlu enjeksiyon, yüksek ürün kalitesi, yönetilebilir deformasyon, daha kısa döngü süreleri ve üstten kalıplamaya kıyasla daha yüksek verim sunarken %7 daha düşük malzeme israfı ve %20-%30 daha düşük üretim maliyetleri sağlar.
B. Üst Kalıplama (İkincil Kalıplama)

İki plastik malzeme aynı makineye enjekte edilemez ve iki aşamalı kalıplamaya tabi tutulamaz. Bir kalıp setinden çıkarıldıktan sonra ürünler ikincil kalıplama için diğerine girer. Dolayısıyla, bu yöntem tipik olarak iki kalıp seti gerektirir ve özel bir iki vuruşlu enjeksiyon makinesi gerektirmez. Kalıp yapısı tek renkli enjeksiyon kalıplarına benzer, öncelikle malzeme füzyon noktaları için enjeksiyon parametrelerinin ayarlanmasına dayanır.
Üst kalıplama, yumuşak parçalar için TPU, TPR, sert bileşenler için ABS, PC ve PP gibi yaygın malzemelerle, esas olarak yumuşak bir malzemeyi sert bir malzeme üzerine kapsüller.
Ek Kontrast Noktaları:
1. Boşluk şekilleri her kalıplama yöntemi için farklılık göstererek farklı ürünler oluştururken, çekirdek şekilleri aynı kalır.
2. Ön ve arka kalıpların 180 derece döndürüldükten sonra hizalanması sağlanmalıdır. Bu kontrol tasarım sırasında çok önemlidir.
3. 210mm’lik küçük bir mesafe ile iğne deliklerinin konumu için dikkat gereklidir. Daha büyük kalıplar, enjeksiyon makinesindeki yetersiz uzunluk nedeniyle kalıp içinde tasarlanmış uzun pimlerle ek pim deliklerine ihtiyaç duyabilir. Arka kalıp tabanına iki adet yerleştirme halkası yerleştirilmelidir.
4. Ön kalıp panelinin ve A plakasının toplam kalınlığı 170 mm’den az olmamalıdır. Bu enjeksiyon makinesi modeli için büyük ve küçük kalıp kalınlıkları ve iğne deliği mesafeleri dahil olmak üzere diğer referans verilerini dikkatlice inceleyin.
5. Üç plakalı kalıplar için, özellikle yumuşak malzeme kapıları için fırlatmanın fizibilitesini sağlayarak, mümkün olduğunda kapıları otomatik fırlatma için tasarlayın.
6. Ön taraftaki yolluk derinliği 65 mm’yi geçmemelidir. Üst yolluktan kalıp embriyosunun merkezine kadar olan mesafe en az 150 mm olmalıdır.

7. İkinci enjeksiyon sırasında boşluk hasarını önlemek için, ilk şekillendirilen ürün konumunda bazı boşluk alanları tasarlamayı düşünün. Ancak, ikinci kalıplama sırasında yüksek enjeksiyon basıncı altında olası deformasyonu göz önünde bulundurarak her bir sızdırmazlık noktasının sağlamlığından emin olun.
8. İkinci kalıplamadaki diğer boşlukla daha sıkı bir sıkıştırma sağlamak ve sızdırmazlık elde etmek için enjeksiyon sırasında ilk şekillendirilen ürün boyutlarının biraz daha büyük olmasına izin verin.
9. İkinci enjeksiyon sırasında plastik akışının ilk şekillendirilen ürünü etkileyerek deformasyona yol açıp açmayacağını değerlendirin. Eğer öyleyse, iyileştirmeler arayın.
10. A ve B plakalarını kapatmadan önce, ön kalıp sürgüsünün veya kaldırıcının yeniden konumlandırma sırasında ürüne zarar vermediğinden emin olun. Eğer öyleyse, önce A ve B plakalarının kapanmasını, ardından kaydırıcı veya kaldırıcının sıfırlanmasını sağlamak için bir çözüm bulun.
11. Düzgün akış sağlamak için hem boşluk hem de çekirdek için su yollarını optimize edin ve dengeleyin.
12. Vakaların %99’unda, önce sert parçayı, ardından yumuşak parçayı enjekte edin, çünkü yumuşak parça deformasyona daha yatkındır.