Derin Delik Delme Nedir?
Derin delik delme, çaplarından önemli ölçüde daha derin delikler oluşturmak için kullanılan bir işleme sürecidir. Bu işlem, 100:1’e kadar yüksek oranlar mümkün olsa da, 10:1’den daha büyük derinlik/çap oranına sahip delikler üretme kabiliyetiyle karakterize edilir. Derin delik delme, derin delik oluşturmada hassasiyet ve doğruluğun kritik olduğu endüstrilerde çok önemlidir. Süreç, deliklerde istenen derinliği ve kaliteyi elde etmek için özel delme araçları ve teknikleri kullanır.
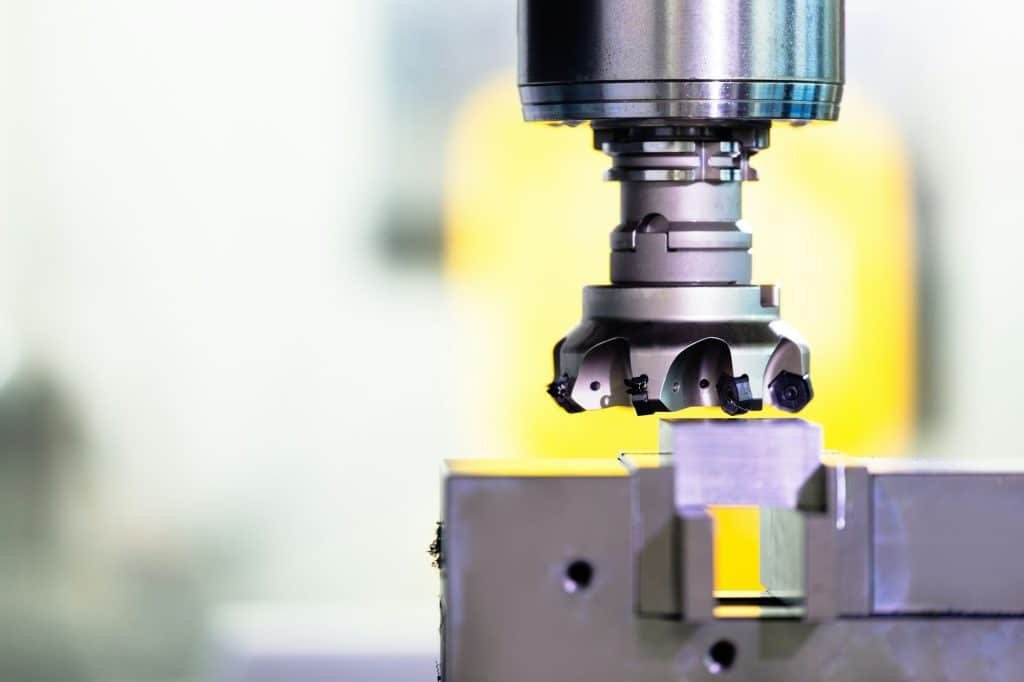
Parça Üretim Süreci
Çeşitli endüstrilerdeki çok çeşitli parçalara uygulanabilir. Bu işlemden yararlanan en yaygın parçalardan bazıları şunlardır:
Havacılık ve Uzay Bileşenleri:
- Uçak iniş takımları
- Hidrolik sistemler
- Yakıt sistemi bileşenleri
Otomotiv Parçaları:
- Krank milleri
- Eksantrik milleri
- Bağlantı çubukları
- Şanzıman milleri
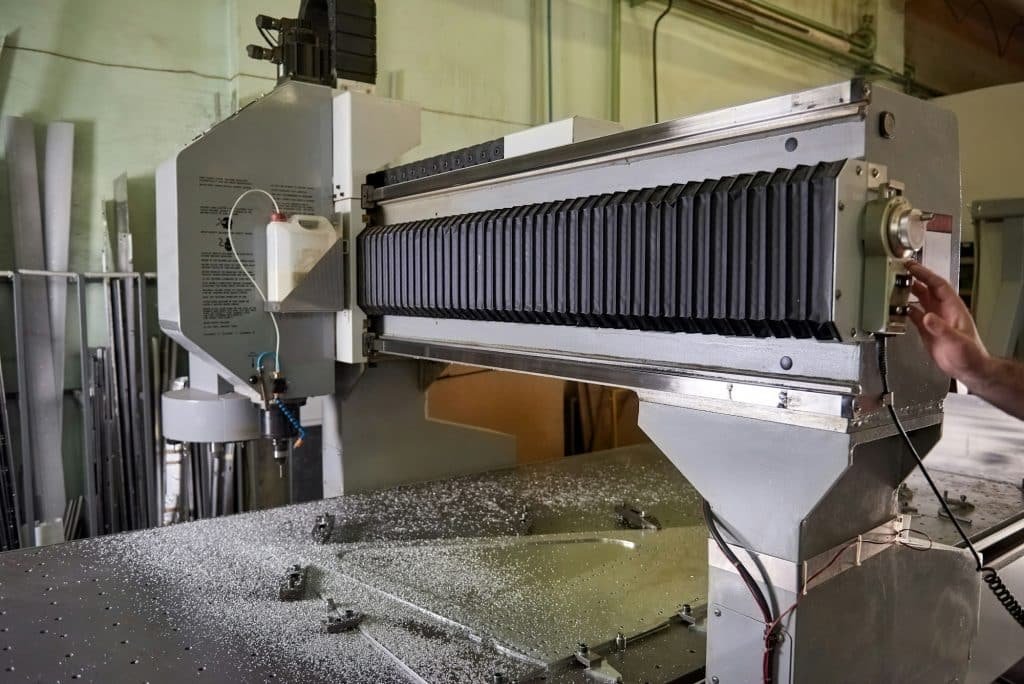
Tıbbi Cihazlar:
- Cerrahi aletler
- İmplantlar
- Hipodermik iğneler
Petrol ve Gaz Ekipmanları:
- Matkap yakaları
- Kuyu içi araçları
- Boru ve muhafaza bileşenleri
Kalıp ve Kalıp Bileşenleri:
- Kalıplarda soğutma kanalları
- İtici pimler
- Çekirdek pimleri
Endüstriyel Makineler:
- Makine takım milleri
- Hidrolik silindirler
- Pnömatik aktüatörler
Derin Delik Delme İşleminin Avantajları
Süreç, belirli uygulamalar için tercih edilen bir seçenek haline getiren çeşitli avantajlar sunar:
Hassasiyet ve Doğruluk:
Derin delik delme, sıkı toleranslar ve amaçlanan yoldan minimum sapma ile yüksek hassasiyet ve doğruluk sağlar. Bu, kesin özellikler ve hizalama gerektiren parçalar için çok önemlidir.
Yüzey İşlemi:
Proses mükemmel yüzey finisajları üreterek raybalama veya honlama gibi ikincil işlemlere olan ihtiyacı azaltır. Bu özellikle düzgün yüzeylerin düzgün çalışma için gerekli olduğu hidrolik ve pnömatik sistemler için faydalıdır.

Verimlilik:
Yüksek malzeme kaldırma oranlarına olanak tanıyan ve üretim süresini azaltan verimli bir süreçtir. Özel araçlar ve teknikler, kaliteden ödün vermeden daha hızlı delme sağlar.
Çok yönlülük:
Bu işlem metaller, alaşımlar ve kompozitler dahil olmak üzere çeşitli malzemelere uygulanabilir. Çok yönlülüğü, farklı malzeme gereksinimleri olan çeşitli endüstriler için uygun olmasını sağlar.
Maliyet-Etkinlik:
Birden fazla işleme operasyonuna olan ihtiyacı en aza indirerek ve yüksek kaliteli yüzeyler sağlayarak, derin delik delme genel üretim maliyetlerini azaltabilir. Derin deliklerin tek bir işlemle üretilebilmesi de maliyet tasarrufuna katkıda bulunur.
Geliştirilmiş Mekanik Özellikler:
Yorulma direncini ve mukavemetini artıran sıkıştırıcı artık gerilmeler oluşturarak belirli parçaların mekanik özelliklerini iyileştirebilir.
Uygulama Senaryoları
Derin ve hassas delikler gerektiren çeşitli uygulama senaryolarında kullanılır. Temel uygulama senaryolarından bazıları şunlardır:
- Havacılık ve Uzay Endüstrisi:
- Hidrolik ve Yakıt Sistemleri: Derin delik delme, sıvı transferi ve yapısal bütünlük için hassas, derin delikler gerektiren hidrolik ve yakıt sistemi bileşenlerinin üretiminde kritik öneme sahiptir.
- Yapısal Bileşenler: Uçak iniş takımları ve yapısal destekler, mukavemetten ödün vermeden ağırlığı azaltmak için genellikle derin deliklere ihtiyaç duyar.

- Motor Bileşenleri: Krank milleri ve eksantrik milleri, yağlama ve soğutma kanalları için derin ve hassas delikler gerektirir. Derin delik delme, bu bileşenlerin verimli ve güvenilir şekilde çalışmasını sağlar.
- Şanzıman Sistemleri: Optimum sıvı akışı ve mekanik performans için şanzıman millerinde derin delikler gereklidir.
- Cerrahi Aletler: Tıbbi aletlerde hassasiyet ve temizlik çok önemlidir. Bazen hipodermik iğneler ve cerrahi matkaplar gibi aletler için gerekli hassasiyeti sağlar.
- İmplantlar: Tıbbi implantların güvenli bir şekilde takılması ve vücuda entegrasyonu için genellikle derin delikler gerekir.
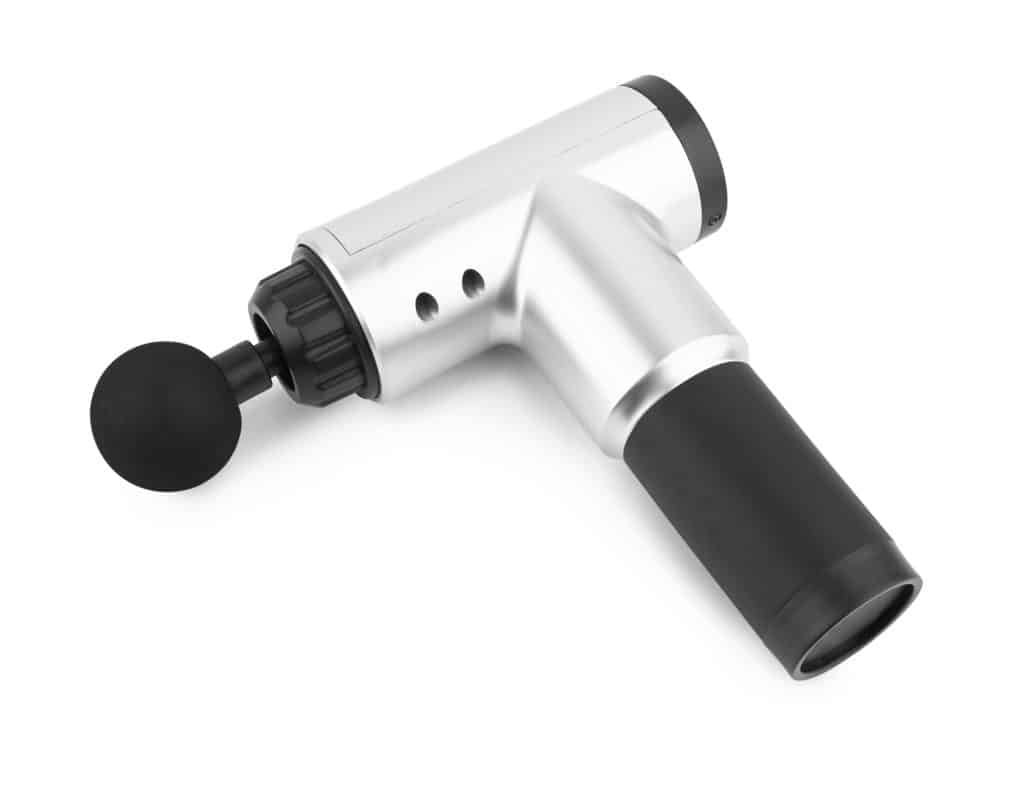
- Petrol ve Gaz Endüstrisi:
- Kuyu İçi Aletler: Petrol ve gaz endüstrisinde kullanılan sondaj ekipmanlarının zorlu ortamlarda etkili bir şekilde çalışabilmesi için derin deliklere ihtiyacı vardır. Derin delik delme, bu aletlerin dayanıklılığını ve işlevselliğini sağlar.
- Boru ve Muhafaza: Yüksek basınç ve sıcaklıklara dayanabilen boru ve muhafaza bileşenleri üretmek için gereklidir.
- Soğutma Kanalları: Plastik enjeksiyon kalıplamada kullanılan kalıplar ve kalıplar, sıcaklığı düzenlemek ve kalıplanmış parçaların kalitesini artırmak için derin soğutma kanalları gerektirir. Derin delik delme bu kanallar için gerekli hassasiyeti sağlar.
- Ejektör ve Maça Pimleri: Bu bileşenler, kalıplama sürecinde güvenli yerleştirme ve etkili işlev için derin deliklere ihtiyaç duyar.
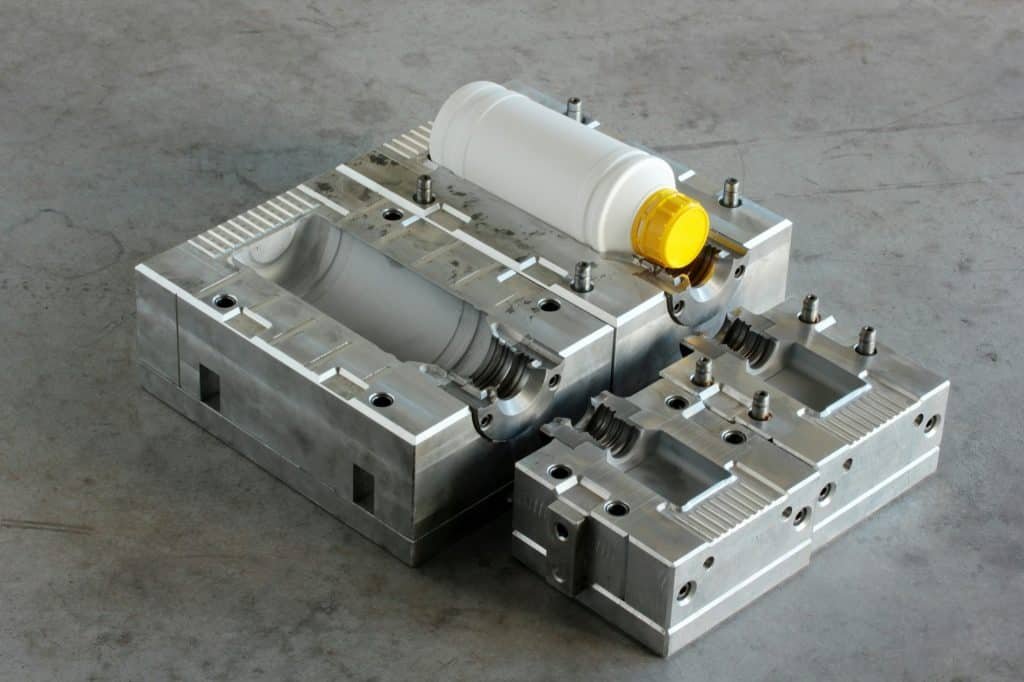
- Endüstriyel Makineler:
- Hidrolik ve Pnömatik Aktüatörler: Bu aktüatörler, sıvı geçişi ve mekanik hareket için derin deliklere dayanır. Derin delik delme, güvenilirliklerini ve performanslarını sağlar.
- Makine Takım Milleri: Soğutma sıvısı ve yağlama geçişi için iş millerinde derin delikler gereklidir. Bu deliklerdeki hassasiyet, takım tezgahlarının verimli çalışmasını sağlar.
Çözüm
Derin delik delme, çeşitli malzeme ve bileşenlerde hassas, derin delikler oluşturmak için vazgeçilmez bir işleme sürecidir. Mükemmel yüzey kalitesi ve sıkı toleranslara sahip yüksek kaliteli delikler üretme kabiliyeti, onu havacılık, otomotiv, medikal, petrol ve gaz, kalıp ve kalıp yapımı ve endüstriyel makinelerde tercih edilen bir seçenek haline getirmektedir. Derin delik delmenin hassasiyet, verimlilik, çok yönlülük ve maliyet etkinliği gibi avantajları, modern üretimdeki geçerliliğinin devam etmesini sağlar. Üreticiler, işlenebilecek parçaları, sunulan avantajları ve uygulama senaryolarını anlayarak ürünlerinin kalitesini ve performansını artırmak için derin delik delme işleminden yararlanabilir.