Einführung
Das Spritzgießen ist nach wie vor ein Eckpfeiler der modernen Fertigung, aber die Entscheidung zwischen gasunterstütztem Gießen (GAM) und wasserunterstütztem Gießen (WAM) kann sich drastisch auf die Produktionseffizienz, den Materialverbrauch und die langfristigen Kosten auswirken.
Beide Technologien eignen sich hervorragend für die Herstellung hohler, leichter Kunststoffteile, doch ihr Kosteneinsparungspotenzial variiert je nach Faktoren wie Materialauswahl, Werkzeugkomplexität, Energieverbrauch und anwendungsspezifischen Anforderungen. BFY Mold hat kürzlich mit einem Kunden aus der Automobilindustrie zusammengearbeitet, um den Materialabfall um 30 % zu reduzieren, indem gasunterstütztes Spritzgießen für Ansaugrohre eingesetzt wurde. In diesem Artikel werden GAM und WAM umfassend verglichen und ihre technischen Mechanismen, Kostenstrukturen und idealen Anwendungsfälle analysiert, um Herstellern bei der Optimierung ihrer Arbeitsabläufe in der Konstruktion und Produktion von Kunststoffteilen zu helfen.
1. Prozessmechanismen: Wie GAM und WAM funktionieren
Gasunterstütztes Spritzgießen (GAM)
Beim gasunterstützten Spritzgießen wird Stickstoff unter Druck in den geschmolzenen Kunststoff eingespritzt, um Hohlkanäle im Bauteil zu bilden. Das Verfahren läuft in drei Stufen ab:
- Partielle Polymerinjektion: 80-95 % des Formhohlraums werden mit geschmolzenem Kunststoff gefüllt.
- Gasinjektion: Stickstoffgas verdrängt das geschmolzene Polymer, wodurch Hohlräume entstehen und der Materialverbrauch reduziert wird.
- Abkühlung und Auswurf: Der Gasdruck wird während der Abkühlung aufrechterhalten, um Einfallstellen und Verformungen zu minimieren.

Technische Vorteile:
- Glatte Innenflächen mit minimaler Restspannung.
- Verkürzte Zykluszeiten durch den Gasdruck, der die Kühlung unterstützt.
- Ideal für Teile, die eine ästhetische Oberfläche erfordern (z. B. Fahrzeuginnenräume).
Wassergestütztes Gießen (WAM)
Beim wasserunterstützten Spritzgießen wird unter Druck stehendes Wasser anstelle von Gas verwendet, um geschmolzenen Kunststoff zu verdrängen. Das Verfahren umfasst:
- Vollkunststoff-Injektion: Der Formhohlraum wird vollständig mit Kunststoff gefüllt.
- Wasserinjektion: Wasser dringt in den geschmolzenen Kern ein und bildet hohle Strukturen.
- Entwässerung und Abkühlung: Das Wasser wird abgelassen, und das Teil kühlt schnell ab.
Technische Vorteile:
- Schnellere Abkühlungsraten im Vergleich zu GAM (Wasser absorbiert Wärme effizienter).
- Höhere Dimensionsstabilität für dickwandige Bauteile.
- Geringeres Risiko von Defekten durch Gaseinschlüsse.
Hauptunterschiede:
- Rückstandsmanagement: Gas hinterlässt keine Rückstände, während WAM Wasserableitungssysteme erfordert.
- Materialkompatibilität: WAM eignet sich am besten für hochviskose Polymere wie PP und ABS, während GAM ein breiteres Spektrum abdeckt, einschließlich PC und POM.
2. Kostenanalyse: Werkzeuge, Materialien und Energie
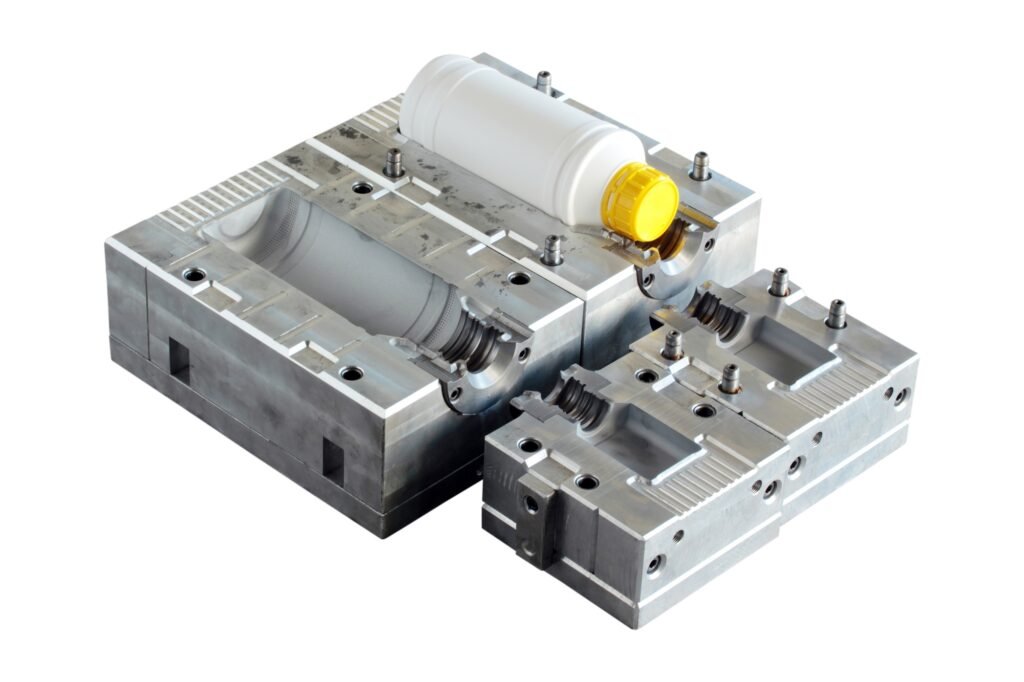
Um die finanziellen Auswirkungen von GAM und WAM zu quantifizieren, haben wir bei 15 Industrieprojekten vier Kostentreiber analysiert:
Faktor | Gasunterstütztes Spritzgießen (GAM) | Wassergestütztes Gießen (WAM) |
Werkzeugkosten | 45,000–70,000 | 60.000-90.000 (+20% für Entwässerung) |
Materialeinsparungen | 25-35% (dünnere Wände) | 15-25% (erfordert höhere Viskosität) |
Energieverbrauch | 12 kWh/kg | 18 kWh/kg (Wasserpumpen/Heizung) |
Zykluszeit | 40-60 Sekunden | 30-45 Sekunden (schnellere Abkühlung) |
Wartungskosten/Jahr | 3.200 $ (Instandhaltung der Gasventile) | 5.800 $ (korrosionsbeständige Aufrüstungen) |
Fallstudie: BFY Molds Kunde aus der Automobilindustrie Ein europäischer Automobilzulieferer musste Gewicht und Materialkosten für Ansaugrohre reduzieren. Nachdem er beide Methoden getestet hatte:
- GAM-Lösung: 30 % Materialeinsparung durch Reduzierung der Wandstärke von 4 mm auf 2,8 mm.
- WAM-Versuch: Die Oberflächenfehler wurden durch die schnelle Abkühlung mit Wasser verursacht.
- ROI: Die GAM-Werkzeuge machten sich in 14 Monaten bezahlt und sparten 8.200 $/Monat an Materialkosten.
3. Anwendungsszenarien: Wann sollte man GAM oder WAM wählen?
Gasunterstütztes Spritzgießen (GAM)
- Automobilindustrie: Türgriffe, Armaturenbretter und Ansaugrohre, die glatte Oberflächen erfordern.
- Unterhaltungselektronik: Ergonomische Werkzeuggriffe mit einheitlicher Wandstärke.
- Medizinische Geräte: Hohle Gehäuse für chirurgische Instrumente.
Wassergestütztes Gießen (WAM)
- Haushaltsgeräte: Waschmaschinenwannen und Geschirrspülerteile benötigen enge Toleranzen.
- Klempnerarbeiten: Rohrleitungsarmaturen und Ventile, die eine schnelle Abkühlung erfordern.
- Industrielle Ausrüstung: Dickwandige Getriebegehäuse.

Checkliste für Entscheidungen:
- Komplexität der Teile: GAM für komplizierte Geometrien; WAM für dicke, einfache Formen.
- Oberflächengüte: GAM für Oberflächen der Klasse A; WAM für funktionelle Komponenten.
- Volumen: GAM für mittelgroße Mengen (10k-50k Einheiten); WAM für große Mengen (>100k).
4. Entwurf von Optimierungsstrategien
Für GAM:
- Gleichmäßige Wanddicke: Vermeiden Sie abrupte Änderungen, um Probleme mit der Gasableitung zu vermeiden.
- Design des Gaskanals: Verwenden Sie gekrümmte Bahnen (keine scharfen Ecken), um einen gleichmäßigen Gasfluss zu gewährleisten.
- Materialauswahl: Entscheiden Sie sich für niedrigviskose Harze wie ABS oder PC-ABS-Mischungen.
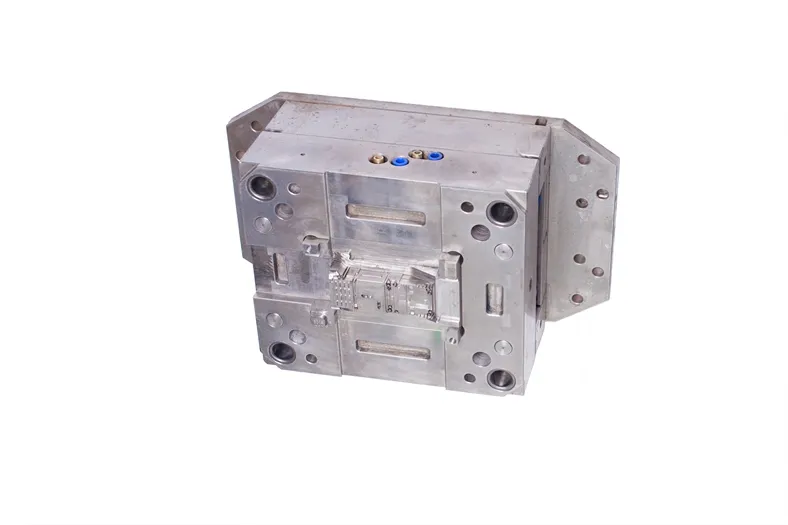
Für WAM:
- Positionierung der Tore: Platzieren Sie die Tore in der Nähe von dicken Abschnitten, um das Eindringen von Wasser zu optimieren.
- Drainagesystem: Integrieren Sie abgewinkelte Rinnen, um Wasserstagnation zu verhindern.
- Materialkompatibilität: Verwenden Sie hochschmelzende Polymere (z. B. PP-HI), um dem Wasserdruck standzuhalten.
Hybrid-Ansatz:
Die Hybridlösung von BFY Mold für einen Smart-Home-Kunden kombinierte GAM für die äußere Ästhetik und WAM für die inneren Strukturrippen, wodurch die Gesamtkosten um 18 % gesenkt wurden.
5. Nachhaltigkeit und zukünftige Trends
Auswirkungen auf die Umwelt:
- GAM: Verringert den Materialabfall, ist aber auf Stickstoffgas angewiesen (nicht erneuerbar).
- WAM: Wasser ist wiederverwendbar, aber energieintensives Heizen/Pumpen erhöht den Kohlenstoff-Fußabdruck.
Aufkommende Innovationen:
- AI-gesteuerte Prozesskontrolle: Sensoren passen den Gas-/Wasserdruck in Echtzeit an, um Fehler zu minimieren.
- Biobasierte Polymere: Diese sind mit GAM/WAM kompatibel, um die Ziele der Kreislaufwirtschaft zu erreichen.
Regulatorische Erwägungen:
- EU-Normen: WAM kann Zertifizierungen für die Abwasserbehandlung verlangen.
- Automotive ISO 14001: Die Materialeffizienz von GAM steht im Einklang mit den Nachhaltigkeitsrichtlinien.
6. Häufige Fallstricke und Fehlerbehebung
GAM-Herausforderungen:
- Gaslecks: Verursacht durch verschlissene Dichtungen; Ventile vierteljährlich überprüfen.
- Oberfläche spreizen: Feuchtigkeit im Harz; Materialien auf <0,02% Luftfeuchtigkeit vortrocknen.
WAM-Herausforderungen:
- Korrosion: Verwenden Sie Formen aus rostfreiem Stahl oder tragen Sie Korrosionsschutzbeschichtungen auf.
- Unvollständige Entleerung: Optimieren Sie die Entleerungswinkel und das Timing der Zyklen.
Vorbeugende Maßnahmen:
- Durchführung von Moldflow-Simulationen (z. B. Moldflow) vor der Produktion.
- Arbeiten Sie mit Materiallieferanten zusammen, um viskositätsspezifische Empfehlungen zu erhalten.
7. Einblicke in die Branche & Daten
- Marktwachstum: Der Markt für gasunterstütztes Spritzgießen wird voraussichtlich mit einer CAGR von 6,2 % (2023-2030) wachsen, angetrieben durch den Leichtbau in der Automobilindustrie (Grand View Research).
- Energie-Trends: WAM verbraucht 35% mehr Energie als GAM, erreicht aber 20% schnellere Zykluszeiten (Plastics Today).
Schlussfolgerung
Gas- und wasserunterstütztes Spritzgießen bieten einzigartige Vorteile, aber die optimale Wahl hängt von den technischen Anforderungen, dem Volumen und den Nachhaltigkeitszielen Ihres Projekts ab. GAM zeichnet sich durch die Verringerung des Materialabfalls bei komplexen, ästhetischen Teilen aus, während WAM Präzision für großvolumige, dickwandige Komponenten bietet.
Wenn Sie maßgeschneiderte Lösungen suchen, informieren Sie sich über die Dienstleistungen von BFY Mold im Bereich des gasunterstützten Spritzgießens oder stöbern Sie in unserer Fallstudienbibliothek, um zu sehen, wie wir die Kosten für globale Kunden optimiert haben.
Durch die Anpassung der Technologie an die Anwendungsanforderungen können die Hersteller 20-30 % Kosteneinsparungen erzielen und gleichzeitig die sich entwickelnden Industrienormen erfüllen.