Einführung
Da die Produktlebenszyklen immer kürzer und die Gewinnspannen in der wettbewerbsintensiven Unterhaltungselektronikbranche immer geringer werden, stehen die Hersteller vor einer nahezu existenziellen Herausforderung: die Bereitstellung hochwertiger Kunststoffkomponenten zu immer niedrigeren Kosten. Diese Herausforderung war für einen führenden Innovator im Bereich der tragbaren Gesundheitstechnologie von entscheidender Bedeutung, da seine bestehenden kundenspezifischen Spritzgussverfahren Ressourcen verbrauchten, sich die Markteinführung verzögerte und die Präzisionsstandards nicht erfüllte.
Durch die Zusammenarbeit mit BFY Mold – der einzige echte Durchbruch, den unser Kunde rechtzeitig erzielen konnte – konnten die Gesamtproduktionskosten um 40 % gesenkt und gleichzeitig die Markteinführung beschleunigt und die Produktzuverlässigkeit verbessert werden. Diese Fallstudie untersucht die technischen Strategien, Materialinnovationen und Optimierungen der Lieferkette, die diesen Wandel ermöglichten, und bietet umsetzbare Informationen für Elektronikmarken, die in einem zunehmend kostensensitiven Umfeld erfolgreich sein wollen.
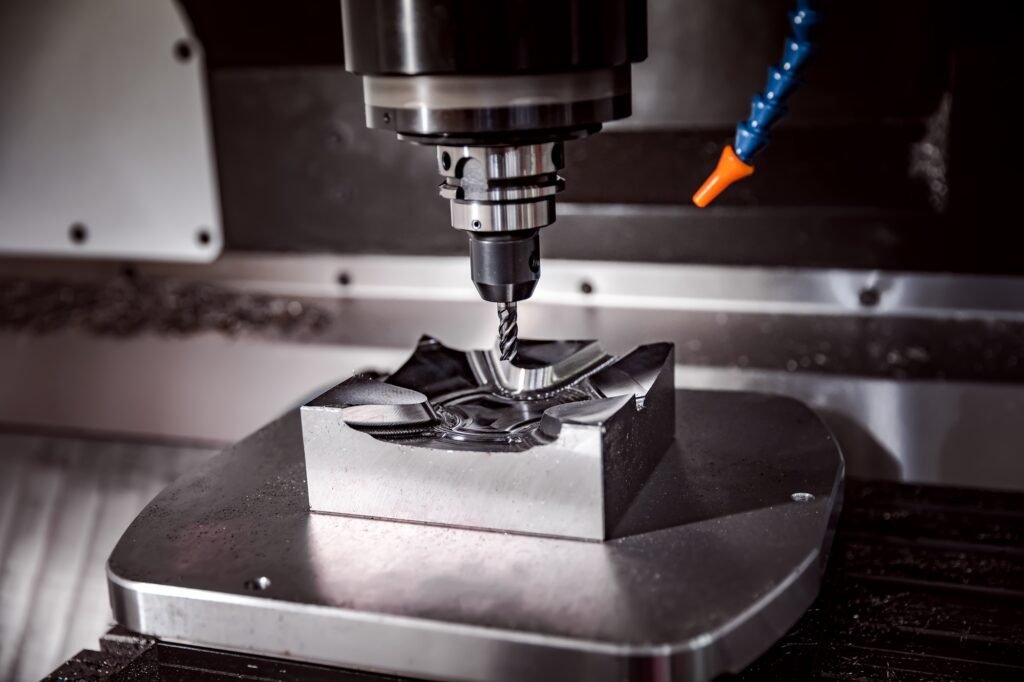
Die Herausforderung: Gleichgewicht zwischen Kosten, Geschwindigkeit und Präzision
Für einen unserer Kunden, der Smartwatches und Aktivitätstracker mit einem Produktionsvolumen von mehr als 5 Millionen Stück pro Jahr entwickelt, war es eine Herausforderung, die Werkzeuge zur Gewährleistung der Datengenauigkeit zu bekommen. Dieser Kampf spiegelte die Probleme der gesamten Branche wider:
- Materialabfall: Bei herkömmlichen Konstruktionen fielen bei der Formherstellung 15 % überschüssiges Material an (meist beibehaltene ABS/PC-Mischungen).
- Zeitverzögerungen bei der Prototypenherstellung: 2-3 Wochen für Formanpassungen bei jeder Designänderung, die die Produkteinführung stoppt.
- Beschränkung durch Offshore-Lieferanten: Obwohl Offshore-Lieferanten niedrigere Arbeitskosten hatten, konnten sie die Toleranzanforderung von ±0,05 mm nicht erfüllen, was zu uneinheitlicher Qualität führte.
„Wir brauchten einen Partner, der sowohl modernste Technik als auch die Dringlichkeit der Unterhaltungselektronik versteht“, so der Leiter der Fertigungsabteilung des Kunden. „Jeder eingesparte Dollar und jeder eingesparte Tag war wichtig“.
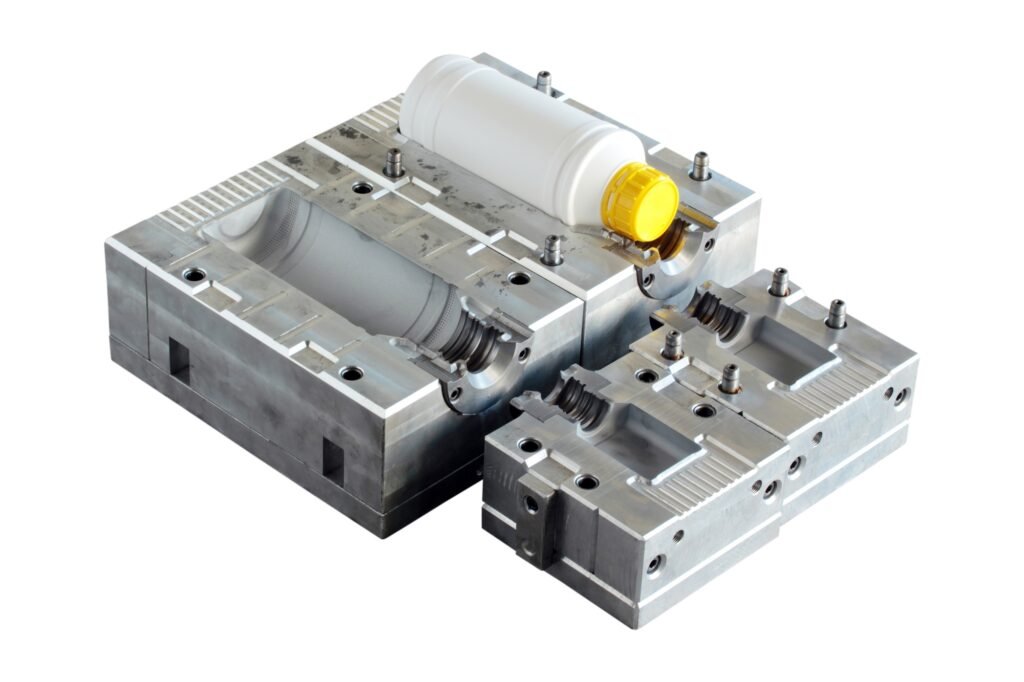
Die Lösung: Die dreigleisige Strategie von BFY Mold
1. Lokale Optimierung der kundenspezifischen Formgestaltung
Das Problem: Veraltete Trial-and-Error-Anpassungen der Formen verschwendeten Zeit und Material.
Innovation:
- Moldflow-Simulation: Die Ingenieure von BFY Mold setzten fortschrittliche Simulationssoftware ein, um den Polymerfluss, die Kühlungsmuster und die Spannungsverteilung zu analysieren.
- Identifizierung optimaler Torstandorte, wodurch der Materialverbrauch um 12 % gesenkt werden konnte.
- Vorhersage von Einfallstellen und Verzugsrisiken, Reduzierung der Versuchsiterationen von 5 auf 2.
- Einzelkavitäten-Effizienz: Im Gegensatz zu den Industrienormen, die Mehrkavitätenwerkzeuge bevorzugen, ergaben die Simulationen ein Einzelkavitätendesign mit beschleunigten Zykluszeiten (18 % schneller), das besser für die Anforderungen des Kunden bei kleinen bis mittleren Stückzahlen geeignet ist.
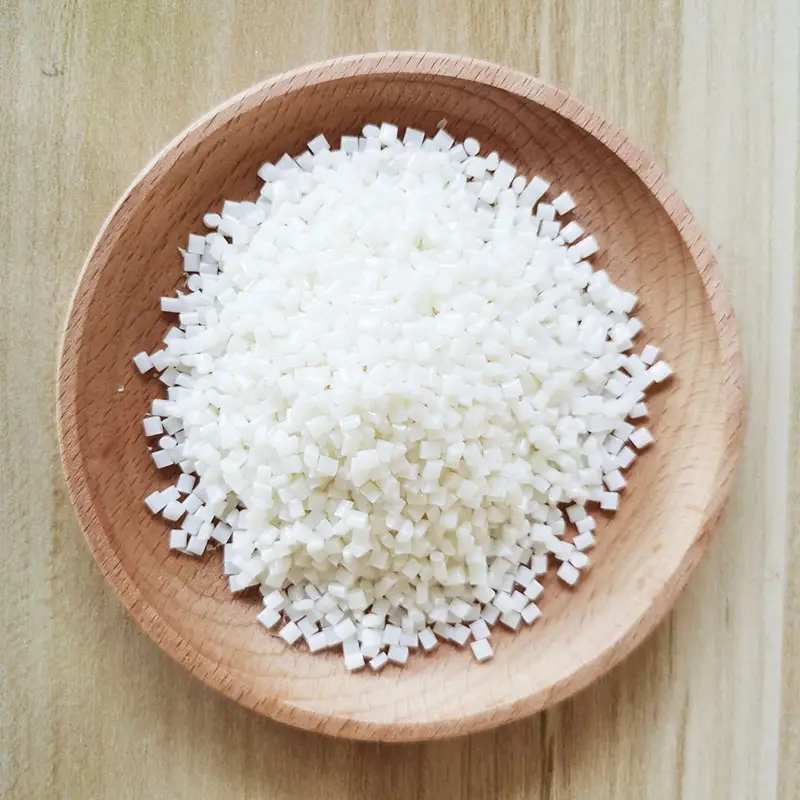
Ergebnis:
- 12% Materialeinsparung: Geringerer ABS/PC-Verbrauch pro Einheit.
- 50% schnelleres Prototyping: 48-Stunden-Simulationszyklen ersetzten wochenlange physische Versuche.
2. Hybride Formherstellung: Kosten vs. Langlebigkeit perfektioniert
Das Problem: Vollstahlformen waren zwar haltbar, aber unerschwinglich teuer (28.000 Dollar pro Satz).
Innovation:
- Aluminium-Stahl-Verbundwerkstoff-Formen:
Aluminium-Rahmen: Senkung der Herstellungskosten für die Form um 35 % ($18.200 pro Satz).
Stahlkern-Einsätze: Beibehaltung der Präzision für mehr als 500.000 Zyklen, entscheidend für hochvolumige Elektronik.
- Konforme Kühlkanäle:
Die 3D-gedruckten Kanäle folgten den Konturen der Form und verbesserten die Kühleffizienz um 25 %.
Die Abkühlzeit sank von 15 auf 11 Sekunden, wodurch die thermische Verformung minimiert wurde.
Vergleichende Daten:
Metrisch | Traditionelle Form | BFY Mold Hybrid Mold |
Anfängliche Kosten | $28,000 | $18,200 |
Reduzierung der Zykluszeit | – | 18% |
Lebensdauer der Werkzeuge | 1M Zyklen | 500K Zyklen (aufrüstbar) |
3. Lokalisierte Lieferkette und Materialbeschaffung
Problem: Die Offshore-Produktion verursachte logistische Verzögerungen und versteckte Kosten.
Innovation:
- Substitution von Inlandsmaterial:
- Ersetzung des importierten Sabic ST-800 ABS durch eine lokal modifizierte Alternative, die 22 % billiger und dennoch UL94 V-0 zertifiziert ist.
- Zusammenarbeit mit Materialwissenschaftlern zur Verbesserung des Flammschutzes für tragbare Geräte.
- Integriertes Produktionszentrum:
- Einrichtung eines eigenen Werks in Shenzhen, China, in dem die Bereiche Formenbau, kundenspezifischer Spritzguss und Qualitätskontrolle untergebracht sind.
- Verkürzung der Vorlaufzeiten von 8 Wochen auf 4 Wochen.
“Die vertikale Integration von BFY Mold war ein Wendepunkt”, so der Supply Chain Director von Business Partner. “Wir haben 60 % der Logistikkosten eingespart und eine Echtzeit-Überwachung der Produktion erhalten.”

Greifbare Ergebnisse: Mehr als Kostenreduzierung
- 40% Gesamtkosteneinsparung:
- Material: 12%
- Werkzeuge: 35%
- Logistik: 60%
- Schnelleres Time-to-Market:
- Die Prototyping-Zyklen wurden um 50 % verkürzt, wodurch die Produkteinführung um 6 Wochen beschleunigt werden konnte.
- Eroberung des Weihnachtsgeschäfts 2024, Steigerung der Einnahmen um 2,3 Millionen Dollar.
- Verbesserte Qualitätskontrolle:
- Maßgenauigkeit: ±0,03 mm (übertrifft die ursprünglichen Ziele).
- Die Fehlerquote sank von 12 % auf 2 %, was die Nacharbeit in der Produktion minimierte.
- Strategische Partnerschaften:
- Ein Artikel in Plastics Today, der Anfragen von 3 Fortune-500-Elektronikfirmen nach sich zog.
- Ausweitung der Zusammenarbeit mit dem kundenspezifischen Spritzgussverfahren auf TWS-Kopfhörergehäuse und IoT-Sensoren.
Warum BFY Mold? Technischer Vorsprung für Elektronikmarken

- Proprietäre Moldflow-Datenbank: Nutzen Sie mehr als 1.000 historische Simulationen für Projekte der Unterhaltungselektronik.
- Doppelte Zertifizierungen: ISO 9001 Produktionszertifizierung, die eine branchenübergreifende Konformität gewährleistet.
- Flexible Produktionsmodelle: Unterstützung von Kleinserien (1.000+ Einheiten), ideal für iterative technische Produkte.
Schlussfolgerung: Eine Blaupause für Elektronikhersteller
Ihre Reise unterstreicht eine wichtige Lektion: In der Unterhaltungselektronik geht es bei der Innovation nicht nur um Produktmerkmale – es geht darum, die Herstellung selbst neu zu erfinden. Durch die Kombination von KI-gesteuertem Design, hybriden Werkzeugen und lokaler Flexibilität konnte BFY Mold 40 % der Kosten einsparen, ohne Abstriche bei der Qualität oder Geschwindigkeit zu machen.
Endgültige CTA:
„Sind Sie bereit, Ihren individuellen Spritzgießprozess zu verändern?
Kontaktieren Sie das Engineering-Team von BFY Mold per E-Mail für eine kostenlose Projektprüfung. Lassen Sie uns Ihren Kostendurchbruch planen.“