Einführung
Das Kunststoffspritzgießen ist das Rückgrat der modernen Fertigung und ermöglicht die Massenproduktion präziser, langlebiger Komponenten. B2B-Kunden stehen jedoch vor drei entscheidenden Herausforderungen: Kostenoptimierung, Materialauswahl und Effizienz bei hohen Stückzahlen. Dieser Leitfaden befasst sich eingehend mit diesen Prioritäten und stützt sich auf Branchendaten, Fallstudien aus der Praxis und Vergleiche der wichtigsten Thermoplaste wie ABS, Polypropylen (PP) und Polycarbonat (PC).
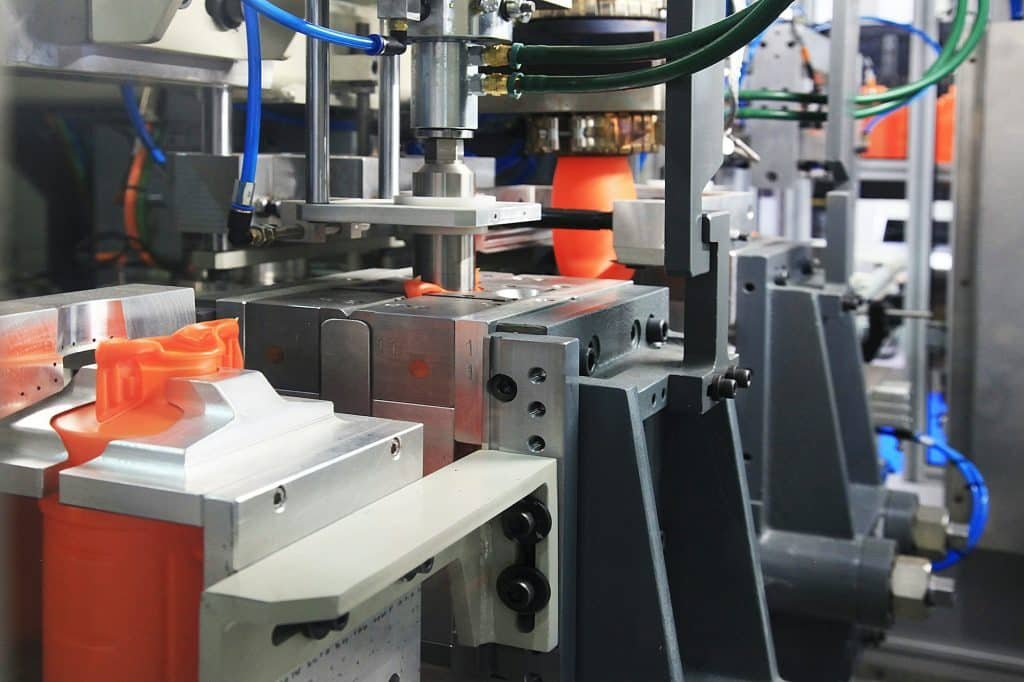
Strategien zur Kostenoptimierung beim Kunststoff-Spritzgießen
1.1 Verkürzung der Zykluszeiten ohne Qualitätseinbußen
Die Zykluszeit wirkt sich direkt auf die Kosten aus. Wenn beispielsweise ein 30-Sekunden-Zyklus um 10 % verkürzt wird, lassen sich pro Maschine jährlich 18.000 $ einsparen. Die Techniken umfassen:
- Kontrolle der Formtemperatur: Halten Sie eine Abweichung von ±2°C ein, um Defekte zu vermeiden.
- Automatisierte Auswurfsysteme: Reduzierung der Ausfallzeiten um 15 %.

1.2 Minimierung von Materialabfällen
Ein durchschnittliches Werk verschwendet 4-8 % der Rohstoffe. Lösungen:
- Integration von Regenerat: Mischen Sie 20-30% Mahlgut mit neuem Harz.
- KI-gesteuerte prädiktive Analytik: Reduzieren Sie Überfüllungen um 12 %.
Fallstudie: Der Automobilzulieferer TechMold Inc. senkte seine Kosten um 22 % durch IoT-gestützte Echtzeitüberwachung und Mahlgutoptimierung.
Leitfaden zur Auswahl von Thermoplastmaterialien für B2B-Einkäufer
2.1 Vergleich der wichtigsten Eigenschaften: ABS vs. PP vs. PC
Eigentum | ABS | Polypropylen (PP) | Polycarbonat (PC) |
Kosten (USD/kg) | 2.1–2.5 | 1.3–1.8 | 3.0–3.5 |
Hitzebeständigkeit | 85°C | 100°C | 135°C |
Schlagfestigkeit | Hoch | Mäßig | Sehr hoch |
Am besten für | Automobil-Innenausstattung | Lebensmittelverpackungen | Medizinische Geräte |
2.2 Wann sollte man sich für technische Kunststoffe entscheiden?
Für stark beanspruchte Anwendungen (z. B. in der Luft- und Raumfahrt) sollten Sie dies in Betracht ziehen:
- PEEK: 90-120/kg, widersteht 250°C.
- Ultem (PEI): 40 % leichter als Stahl, FDA-konform.
Skalierung großvolumiger Spritzgießprozesse
3.1 Konstruktion von Mehrkavitätenformen
Ein 64-Kavitäten-Werkzeug produziert 8-mal mehr Teile pro Stunde als ein 8-Kavitäten-System, benötigt aber mehr:
- Ausgewuchtete Läufersysteme: ±1% Gewichtsabweichungstoleranz.
- Konforme Kühlkanäle: Verkürzung der Kühlzeit um 30 %.

3.2 Integration der schlanken Produktion
- SMED (Single-Minute Exchange of Die): Reduziert den Werkzeugwechsel auf <10 Minuten.
- TPM (Total Productive Maintenance): Steigern Sie die OEE (Overall Equipment Effectiveness) auf 85%+.
FAQs: Schmerzpunkte beim Kunststoff-Spritzgießen angehen
1. Wie viel kostet eine Kunststoffspritzgussform?
Die Formen reichen von 3.000 (einfache) bis zu 100.000+ (hochpräzise Mehrkavitätenformen).
2. Können recycelte Kunststoffe im Spritzgussverfahren verwendet werden?
Ja, aber beschränken Sie das Nachschleifen auf 30 % für Strukturteile, um die Festigkeit zu erhalten.
3. Wie hoch ist die Mindestbestellmenge (MOQ) für kundenspezifische Teile?
Normalerweise 1.000-10.000 Einheiten, je nach Komplexität der Form.
4. Wie kann man Verzug bei dünnwandigen Teilen verhindern?
Verwenden Sie Materialien mit geringer Schrumpfung (z. B. PP: 1,5-2,5 %) und optimieren Sie die Anschnittkonstruktion.
5. Welche Industriezweige profitieren am meisten vom High-Volume-Molding?
Automobilbau, Unterhaltungselektronik und Herstellung medizinischer Geräte.
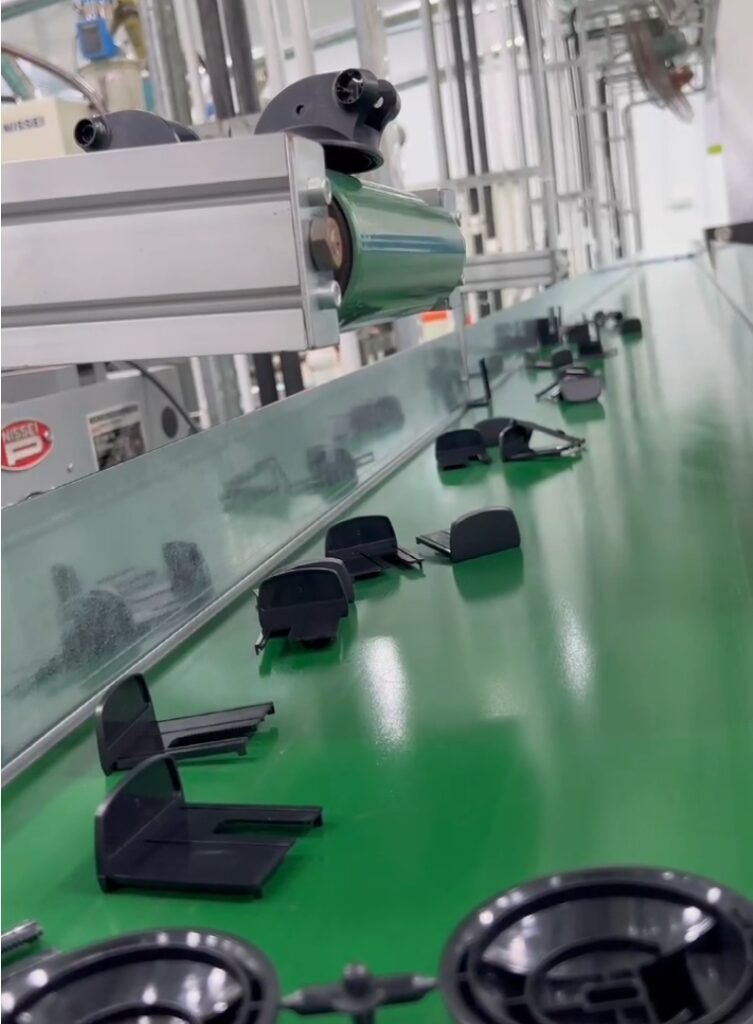
Schlussfolgerung
Bei der Optimierung des Kunststoffspritzgusses kommt es auf ein ausgewogenes Verhältnis zwischen Kosten, Materialwissenschaft und skalierbaren Prozessen an. Durch den Einsatz fortschrittlicher Kühltechnologien, datengesteuerter Materialauswahl und schlanker Methoden können Hersteller Kosteneinsparungen von 20-30 % erzielen und gleichzeitig strenge Qualitätsstandards einhalten.
Sind Sie bereit, Ihren Spritzgussprozess zu optimieren?
Kontaktieren Sie uns für ein kostenloses Audit Ihrer Produktionslinie und Materialstrategie.