Die Fließfähigkeit von ABS liegt beim ABS-Spritzgießverfahren zwischen PS und PC. Die Fließfähigkeit wird durch die Temperatur und den Druck bei der Erkennung beeinflusst, wobei der Einfluss des Einspritzdrucks einen geringfügig größeren Gesamteinfluss hat. Daher werden während des Spritzgießprozesses in der Regel hohe Einspritzdrücke verwendet, um das Füllverhalten zu verbessern und die Viskosität der Schmelze zu verringern.
ABS wird durch Copolymerisation von Acrylnitril, Butadien und Styrol hergestellt und ist gemeinhin als Acrylnitril-Butadien-Styrol-Kunststoff bekannt. Die Verhältnisse dieser drei Monomere können variiert werden, um ABS mit unterschiedlichen Schmelztemperaturen und Fließeigenschaften herzustellen. Verschiedene ABS-Materialien können für unterschiedliche Zwecke hergestellt werden, indem ABS mit anderen Kunststoffen oder Additiven gemischt wird, z.B. schlagzäh, hitzebeständig, flammhemmend, transparent, verstärkt und galvanisch.
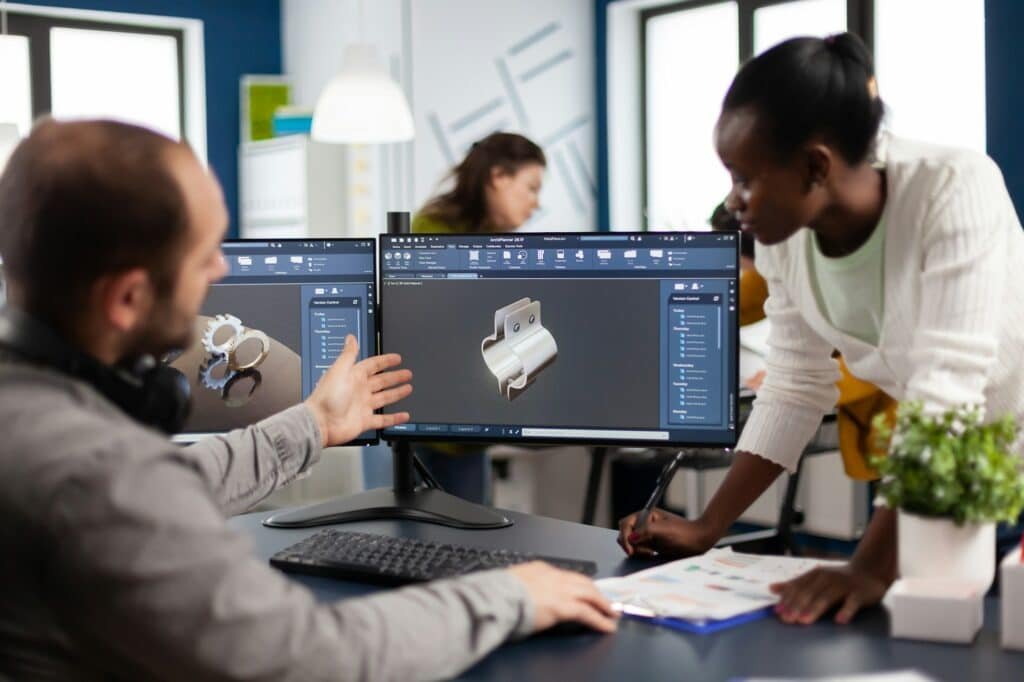
1. Plastische Behandlung
Die Wasserabsorptionsrate von ABS beträgt etwa 0,2%-0.8%, und für allgemeines ABS wird es vor der ABS-Spritzgussverarbeitung bei 80-85 ° C für 2-4 Stunden im Ofen oder 1-2 Stunden mit einem Trocknungstrichter bei 80 ℃ getrocknet. Für hitzebeständige ABS-haltige PC-Komponenten wird die Trocknungstemperatur entsprechend auf 100 ℃ eingestellt, und die spezifische Trocknungszeit kann durch Luftextrusion bestimmt werden.
Der Anteil an recyceltem Material darf 30 % nicht überschreiten, und für die galvanische Beschichtung von ABS darf kein recyceltes Material verwendet werden.
2. Auswahl der Spritzgießmaschine
Es kann eine Standard-Spritzgießmaschine (Schneckenlänge-Durchmesser-Verhältnis 20:1, Kompressionsverhältnis größer als 2, Einspritzdruck größer als 150 MPa) verwendet werden. Wenn Farbmasterbatch verwendet wird oder das Aussehen des Produkts einen hohen Materialanteil erfordert, kann eine Schnecke mit kleinem Durchmesser gewählt werden. Die Schließkraft wird je nach Kunststoffsorte und Produktanforderungen auf 4700-6200t/m2 festgelegt.
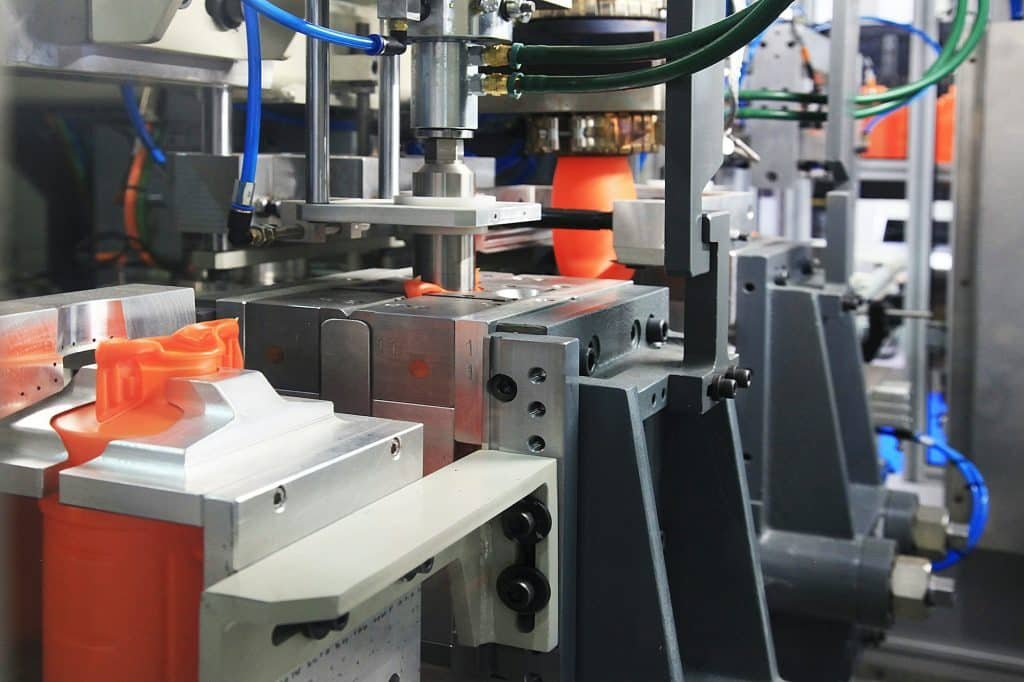
3. Form- und Anschnittdesign
Formtemperatur kann auf 60-65℃ eingestellt werden. Laufraddurchmesser 6-8mm. Die Anschnittbreite beträgt etwa 3 mm, die Dicke ist die gleiche wie das Produkt, und die Anschnittlänge ist weniger als 1 mm. Die Entlüftung ist 4-6 mm breit und 0,025-0,05 mm dick.
4. Schmelztemperatur
Sie kann durch die Luftinjektionsmethode genau bestimmt werden. Für verschiedene Sorten sind die Schmelztemperaturen auch unterschiedlich, es wird empfohlen, sie wie folgt einzustellen:
- Schlagfestigkeit: 220℃-260℃, 250℃ ist vorzuziehen
- Beschichtungsgrad: 250℃-275℃, 270℃ ist vorzuziehen
- Hitzebeständigkeit: 240℃-280℃, wobei 265℃-270℃ besser ist
- Flammenhemmend: 200℃-240℃, besser 220℃-230℃
- Transparenzgrad: 230℃-260℃, 245℃ ist vorzuziehen
- Glasfaserverstärkte Qualität: 230℃-270℃
Für Produkte mit hohen Oberflächenanforderungen werden höhere Schmelz- und Formtemperaturen verwendet.
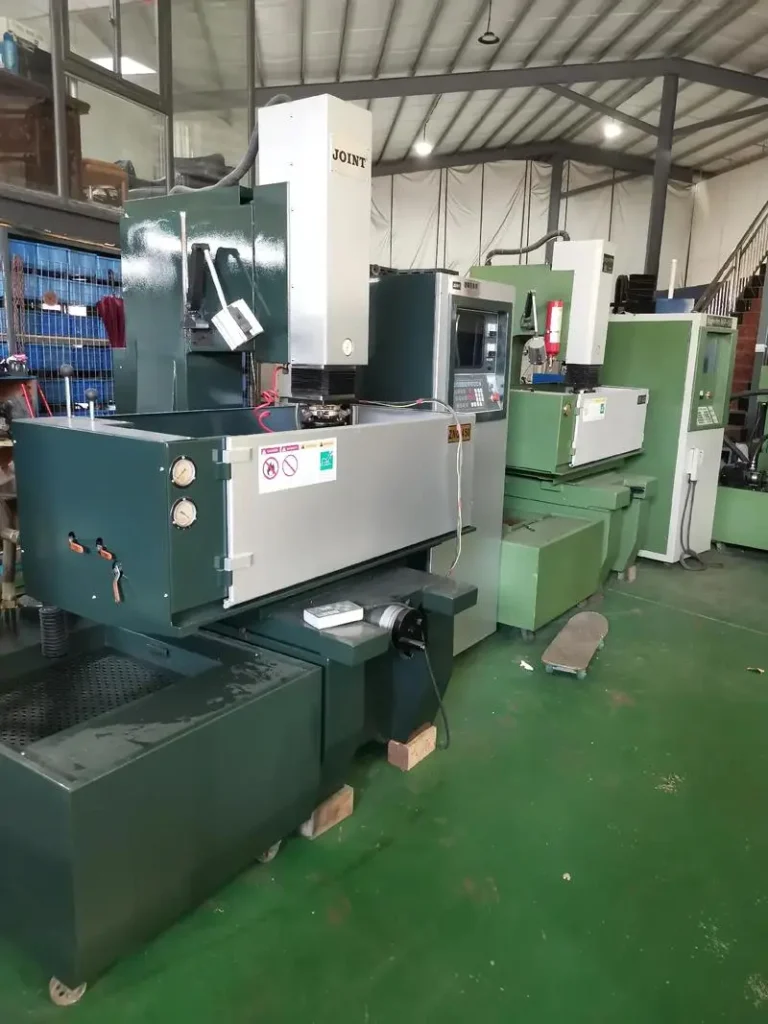
5. Einspritzgeschwindigkeit
Für die Brandklasse sollte eine langsame Geschwindigkeit verwendet werden, für die Wärmeklasse eine schnelle. Während ABS-Spritzgießen, wenn die Anforderungen an die Oberfläche des Produkts hoch sind, sollte die Rate der Feuer Kontrolle der High-Speed-und Multi-Stage-Spritzgießen verwendet werden.
6. Gegendruck
Unter normalen Umständen ist der Gegendruck umso besser, je niedriger er ist. Der üblicherweise verwendete Gegendruck beträgt 0,5 MPa, und das Färbematerial muss einen höheren Gegendruck aufweisen, um die Farbmischung einheitlich zu machen.
7. Verweildauer
Bei einer Temperatur von 265 °C sollte die Verweilzeit von ABS im Schmelzrohr 5-6 Minuten nicht überschreiten. Die flammhemmende Zeit ist kürzer, wenn Sie stoppen müssen, sollten Sie zuerst die eingestellte Temperatur auf 100℃ senken und dann das Schmelzrohr mit Universal-ABS reinigen. Die gereinigte Mischung sollte in kaltes Wasser gelegt werden, um eine weitere Zersetzung zu verhindern.
Wenn Sie ABS-Material gegen andere Kunststoffe austauschen möchten, müssen Sie zunächst das Schmelzrohr mit PS, PMMA oder PE reinigen. Bei einigen ABS-Produkten gibt es keine Probleme, wenn sie gerade erst freigegeben wurden. Nach einer gewissen Zeit kommt es zu Verfärbungen, die durch Überhitzung oder einen zu langen Aufenthalt des Kunststoffs im Schmelzzylinder verursacht werden können.
8. Nachbearbeitung der Produkte
Im Allgemeinen müssen ABS-Produkte nicht nachbehandelt werden, nur galvanisierte Produkte müssen eingebrannt werden (70-80℃, 2-4 Stunden), um Oberflächenspuren zu passivieren, und Produkte, die galvanisiert werden müssen, dürfen keine Trennmittel verwenden, und die Produkte sollten sofort nach dem Entfernen verpackt werden.
9. Bei der Formgebung sollten Sie besonders auf folgende Punkte achten
Es gibt verschiedene ABS-Qualitäten (insbesondere flammhemmende Qualitäten), und die Adhäsion der Schmelze an der Schraubenoberfläche nach der Plastifizierung ist sehr groß, und sie wird sich nach langer Zeit zersetzen. Wenn die oben genannte Situation auftritt, ist es notwendig, den Homogenisierungsabschnitt und die Kompression der Schraube herauszuziehen, um den Test zu wischen, und die Schraube regelmäßig mit PS zu reinigen.