El moldeo por inyección de productos transparentes -como lentes ópticas, carcasas de dispositivos médicos o envases de consumo- exige una atención meticulosa a la pureza del material, la precisión del proceso y la integridad del acabado superficial. Incluso pequeñas imperfecciones como burbujas, marcas de flujo o bruma pueden inutilizar los productos, por lo que todas las etapas, desde la preparación del material hasta el diseño del molde, son críticas.
Esta guía desglosa siete factores no negociables, incluidos protocolos avanzados de secado, control de la temperatura del molde y técnicas de pulido de calidad óptica, para garantizar resultados cristalinos. Tanto si se producen componentes de PMMA como de policarbonato, estas estrategias minimizan la repetición de trabajos y se ajustan a las normas del sector en materia de transparencia y durabilidad.
Normas de acabado superficial para la claridad de los productos transparentes
Los plásticos transparentes requieren normas estrictas de calidad superficial debido a su alta transmisión de luz. Defectos como marcas, poros, decoloración y poco brillo son inaceptables. Todos los aspectos del proceso de moldeo por inyección -materiales, equipos, moldes y diseño del producto- deben cumplir requisitos estrictos.

Moldeo de productos transparentes: Eliminación de brumas y burbujas
Los plásticos transparentes suelen tener puntos de fusión elevados y poca fluidez. Para garantizar la calidad del producto, es necesario ajustar los parámetros del proceso, como la temperatura del barril, la presión de inyección y la velocidad de inyección. Así se garantiza que el plástico llene el molde sin causar tensiones internas, deformaciones o grietas.
Secado de materiales para la integridad de polímeros transparentes
Garantizar la pureza del material
Las impurezas del plástico pueden afectar a la transparencia. Durante el almacenamiento, el transporte y la alimentación, los materiales deben sellarse para que permanezcan limpios. La humedad en las materias primas puede causar degradación cuando se calientan, por lo que es esencial un secado completo. Utilice una tolva de secado y asegúrese de que el aire de entrada esté filtrado y deshumidificado.
Limpieza de equipos para una mayor pureza de los productos transparentes
Limpieza del cañón, tornillo y accesorios
Prevenga la contaminación limpiando el tornillo y los accesorios con un agente limpiador de tornillos antes de su uso y después de su parada. Si no se dispone de un producto de limpieza, pueden utilizarse resinas de PE o PS. Durante las paradas temporales, reduzca la temperatura del secador y del barril para evitar la degradación de las materias primas.
Diseño de moldes para productos transparentes de alto brillo
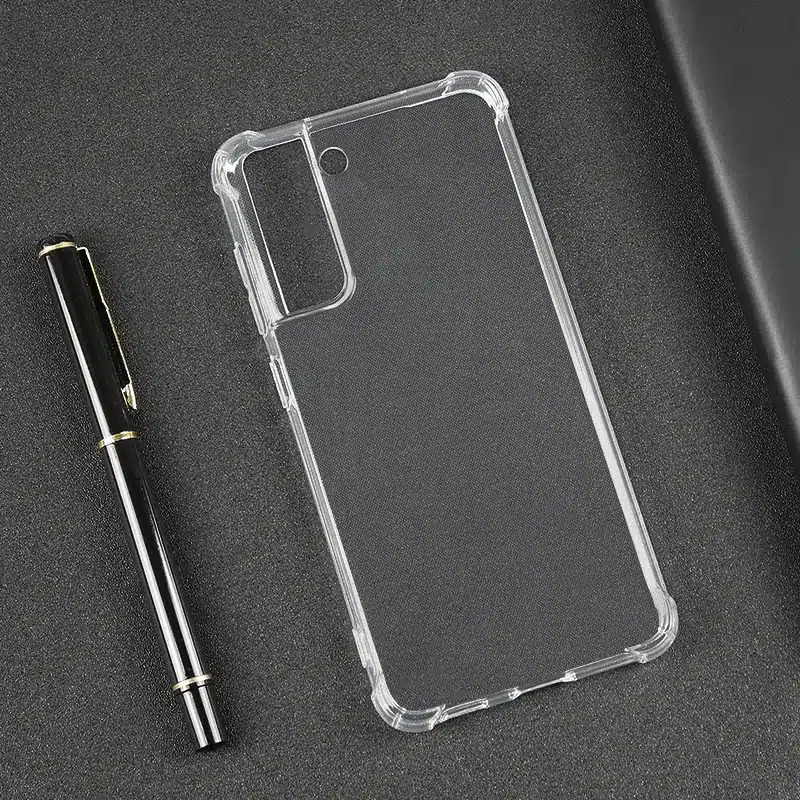
Diseñar para la calidad
Para evitar defectos superficiales:
1. Asegurar un espesor de pared uniforme y una pendiente de desmoldeo suficiente.
2. Transición gradual de las esquinas para evitar bordes afilados.
3. Utilice guías anchas y cortas y, si es necesario, compuertas colocadas adecuadamente con pozos de refrigeración.
4. Mantener las superficies de los moldes lisas, con poca rugosidad y ventilación adecuada.
Superficie del molde y espesor de la pared
Las superficies del molde deben ser lisas, con poca rugosidad (preferiblemente inferior a 0,8). Garantizar una ventilación adecuada para evacuar el aire y los gases de la masa fundida. Evitar paredes demasiado finas, con un espesor mínimo de 1 mm, excepto para PET.
Parámetros de inyección para productos transparentes como el cristal
Parámetros óptimos de inyección
Para minimizar las tensiones internas y los defectos superficiales:
1. Utilice un tornillo especial y una boquilla de temperatura controlada.
2. Utilice una temperatura de inyección más alta dentro de los límites de descomposición de la resina.
3. Aplique una presión de inyección alta para superar la viscosidad del material fundido, pero no tan alta como para provocar deformaciones.
4. Optar por una velocidad de inyección baja, utilizando preferentemente una inyección multietapa lenta-rápida-lenta.
5. Mantenga el tiempo de mantenimiento de la presión y el ciclo de moldeo cortos para evitar depresiones y burbujas.
6. Utilice una velocidad de tornillo y una contrapresión bajas para evitar la degradación del material.
7. Controle con precisión la temperatura del molde para obtener una refrigeración y una calidad del producto óptimas.
Prevención de defectos en el postmoldeo de productos transparentes
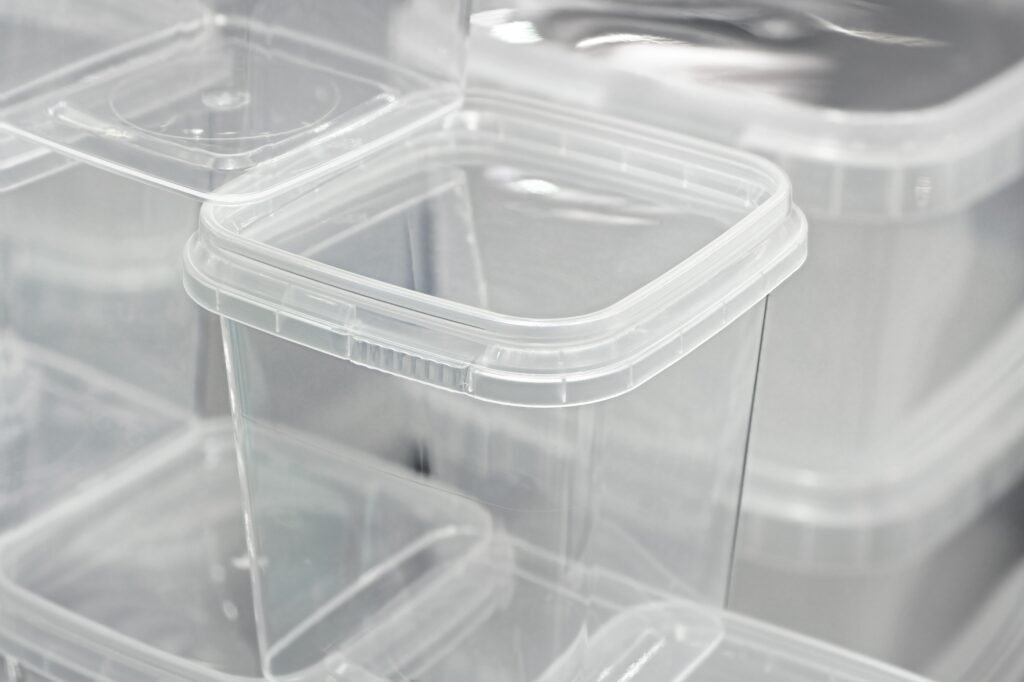
Uso de agentes desmoldeantes y materiales reciclados
Minimizar el uso de agentes desmoldeantes para evitar el deterioro de la calidad de la superficie. Cuando utilice materiales reciclados, asegúrese de que no superan el 20%.
Tratamiento posterior de los productos
Algunos materiales, como el PET, requieren un tratamiento posterior para eliminar las tensiones internas. El PMMA debe secarse a 70-80℃ durante 4 horas, y el PC debe calentarse a 110-135℃, con una duración que depende del producto. El PET debe someterse a estirado bidireccional para conseguir buenas propiedades mecánicas.