1. Sélection de la résine PP et optimisation de la pression
L’augmentation de la pression d’injection peut améliorer la résistance à la traction des pièces moulées par injection en PP. Comparé à d’autres plastiques rigides, le PP a une plus grande élasticité, de sorte que la densité des pièces moulées par injection augmentera avec l’augmentation de la pression, ce qui est une caractéristique relativement importante. Lorsque la densité des pièces en plastique augmente, leur résistance à la traction augmente naturellement en conséquence, alors qu’elle diminue lorsque la densité diminue.
Toutefois, lorsque la densité atteint la valeur maximale que le PP peut atteindre, une nouvelle augmentation de la pression ne continuera pas à accroître la résistance à la traction. Au contraire, elle augmentera la contrainte interne résiduelle des pièces moulées par injection, ce qui les rendra cassantes. Il est donc conseillé de faire preuve de modération. Des situations similaires se produisent avec d’autres matériaux, mais le degré d’importance peut varier.
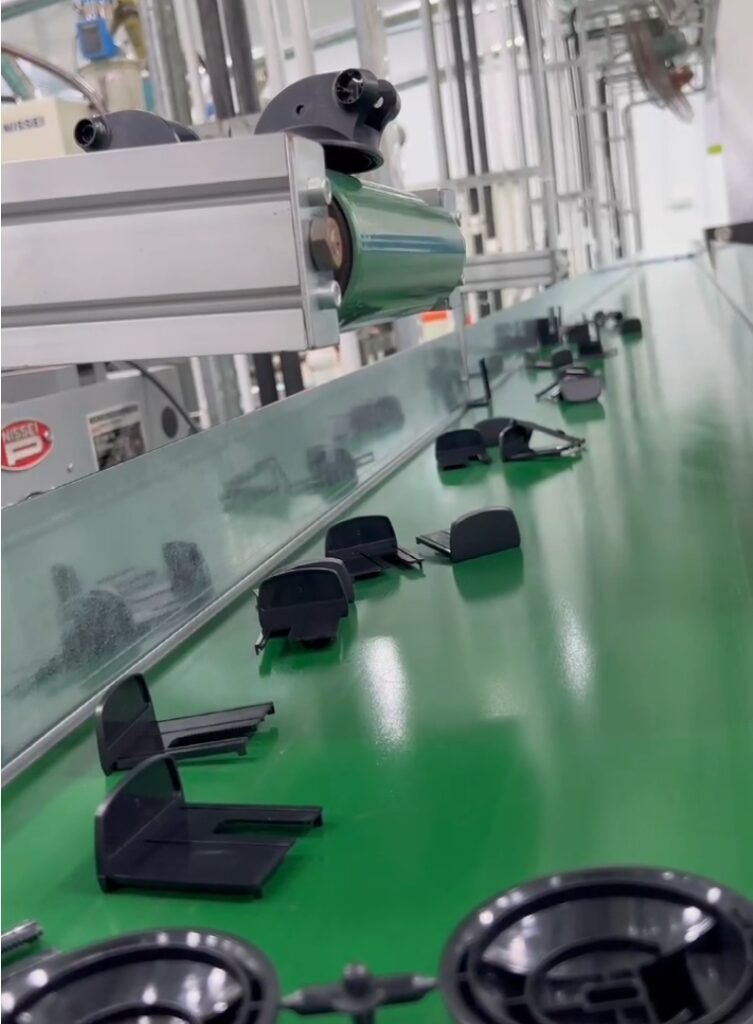
2. Stabiliser la température du moule grâce à la circulation d’huile chaude
Le moulage par injection d’huile chaude peut améliorer la résistance des pièces en POM et en nylon. Le nylon et le POM sont des matières plastiques cristallines. L’utilisation d’une machine à huile chaude pour le moulage par injection permet de ralentir la vitesse de refroidissement des pièces moulées, ce qui augmente la cristallinité du plastique. En même temps, le ralentissement de la vitesse de refroidissement réduit les contraintes internes résiduelles des pièces moulées.
Par conséquent, la résistance aux chocs et la résistance à la traction des pièces en nylon et en POM moulées par injection à l’aide d’une machine à huile chaude seront améliorées en conséquence. Il convient de noter que les dimensions des pièces en nylon et en POM moulées par injection à l’aide d’une machine à huile chaude peuvent différer légèrement de celles des pièces moulées par injection à l’eau, et que les pièces en nylon peuvent être légèrement plus grandes.
3. Prévenir la fragilité grâce à la maîtrise de la vitesse de fusion
La vitesse de la colle fondue ne doit pas être trop rapide. Même avec une injection de PVC à 180°C, la formation de colle peut se produire si la vitesse de la colle fondue est trop rapide. En général, lorsque le matériau PVC à 90 degrés est injecté à 180°C, la température est suffisante et la formation de colle ne pose généralement pas de problème.
Toutefois, en raison de la négligence de l’opérateur ou de l’accélération intentionnelle de la vitesse de la colle fondue pour augmenter la production, la vis se rétracte souvent très rapidement, par exemple en deux ou trois secondes, lorsque la vis se rétracte à plus de la moitié de la grande quantité de colle fondue, le matériau PVC n’est pas suffisamment chauffé et agité, ce qui entraîne la formation de colle en raison d’une température de fusion et d’un mélange inégaux, entraînant une détérioration significative de la résistance et de la ténacité des pièces moulées par injection.

Par conséquent, lors du moulage par injection d’un matériau en PVC, veillez à ne pas régler arbitrairement la vitesse de la colle fondue à plus de 100 tr/min. Si elle doit être réglée assez rapidement, n’oubliez pas d’augmenter la température du matériau de 5 à 10°C ou d’augmenter la contre-pression de la colle fondue en conséquence.
Il faut également veiller à vérifier régulièrement s’il y a des problèmes de formation de colle, faute de quoi des pertes importantes risquent de se produire. Étant donné que la plupart des gens n’accordent généralement pas trop d’attention à cette question, nous insistons particulièrement sur le fait qu’il faut y prêter attention pendant la production et effectuer des contrôles réguliers.
Inversement, il convient également de noter que si la vitesse de fusion de la colle est trop lente, même le moulage par injection d’un matériau en PVC à 90 degrés à 180°C peut entraîner des problèmes de brûlure de la colle, en particulier avec le PVC transparent, ce qui se traduit par de nombreuses taches noires et des marques d’air sur les pièces moulées.