Introduction
Les défauts de moulage par injection coûtent aux fabricants jusqu’à 15 % de perte de matière et 20 % de retard de livraison par an. Qu’il s’agisse de marques d’enfoncement ou de déformation, même des problèmes mineurs peuvent entraîner des rappels coûteux, en particulier dans les secteurs réglementés tels que les dispositifs médicaux et l’automobile.
S’appuyant sur l’analyse par BFY Mold de plus de 10 000 cycles de production, ce guide dissèque les 5 principaux défauts de moulage par injection, leurs causes profondes et des solutions concrètes étayées par des données réelles. Donnez à votre équipe les moyens de réduire les taux de rebut et d’optimiser les temps de cycle.
1. Marques d’affaissement : Causes et corrections
A quoi ça ressemble : Dépressions superficielles localisées, souvent à proximité de nervures ou de bossages épais.
Localisation courante : renforcement de la coque des appareils électroménagers, colonne d’installation de l’intérieur de l’automobile.
Causes profondes :
- Pression de tassement insuffisante (rétrécissement du matériau pendant le refroidissement).
- Variations excessives de l’épaisseur de la paroi (par exemple, nervure de 4 mm contre base de 2 mm).
- Température élevée du moule ralentissant le refroidissement.

Les correctifs de BFY Mold :
- Température élevée du moule ralentissant le refroidissement.
- Augmentez la pression de remplissage de 50 % par défaut à 70-80 % et maintenez-la pendant 5 à 10 secondes (voir la fiche technique).
- Exemple : lors de la production d’une coque d’outil électrique, la pression de maintien est ajustée de 60MPa à 75MPa, et le taux de rétrécissement est réduit de 8 % à 1,5 %.
- Redéfinir la géométrie des pièces :
- L’épaisseur de l’armature est contrôlée à 50-60% de l’épaisseur de la paroi principale (par exemple 3 mm de la paroi principale → 1,5-1,8 mm de l’armature).
- Optimiser les canaux de refroidissement :
- L’ajout d’une voie d’eau secondaire à la zone à parois épaisses réduit le temps de refroidissement de 30 % (par exemple, de 15 secondes à 10 secondes).
Critères de vérification : Tester la stabilité dimensionnelle conformément à la norme ASTM D955. Une profondeur de rétrécissement <0,05 mm est qualifiée.
2. Le gauchissement : La perte de forme des pièces
Ce à quoi cela ressemble : Géométries courbées ou tordues, en particulier dans les pièces plates.
Matériaux à haute incidence : plastiques semi-cristallins (PP, nylon), matériaux renforcés de fibres de verre.
Causes profondes :
- Taux de refroidissement inégaux (par exemple, différence de température entre le haut et le bas du moule>15°C).
- Contraintes résiduelles dues à des vitesses d’injection élevées.
- Mauvaise orientation des fibres dans les plastiques renforcés.
Les correctifs de BFY Mold :
- Équilibrer le système de refroidissement :
- Utiliser une caméra thermique infrarouge pour détecter les différences de température des moules et ajuster le débit d’eau pour que la différence de température soit inférieure à 5°C.
- Cas : Une hélice de drone utilise une conception de refroidissement symétrique, réduisant la déformation de 0,8 mm à 0,2 mm.
- Réduire la vitesse d’injection :
- Réduire la vitesse d’injection de 90 % à 60-70 % pour réduire la contrainte de cisaillement (pour le nylon + 30 % de fibres de verre).
- Post-traitement par recuit :
- Réduisez la vitesse d’injection de 90 % à 60-70 % pour réduire les contraintes de cisaillement (pour le nylon + 30 % de fibres de verre). Recuire les matériaux à haute température tels que le PEEK (20°C au-dessus de la Tg, maintenir pendant 2 heures) pour libérer les contraintes internes.
Comparaison des données :
Conditions | Warpage (mm) | Rendement de la production |
Original | 0.75 | 72% |
Après optimisation | 0.18 | 95% |
3. Tirs courts : Remplissage incomplet
A quoi cela ressemble : Pièces manquant de sections, en particulier dans les zones minces.
Scénarios typiques : connecteurs électroniques à paroi mince (moins de 0,5 mm), moules à cavités multiples.
Causes profondes :
- Température de fusion basse (viscosité du matériau trop élevée).
- Ventilation inadéquate (l’air emprisonné empêche l’écoulement).
- Pression/vitesse d’injection insuffisante.
Les correctifs de BFY Mold :
- Augmenter la température de fusion
- La fluidité de l’ABS augmente de 40% de 230°C à 250°C (le risque de dégradation doit être surveillé).
- Ajouter/agrandir les évents :
- La profondeur de la rainure d’échappement passe de 0,015 mm à 0,025 mm (pour le matériau PC).
- Des inserts d’échappement auxiliaires sont ajoutés au plan de joint.
- Adopter des matériaux à haut débit :
- Indice de fusion du PP ordinaire 15g/10min → Indice de fusion du PP à haut débit 35g/10min (tel que Sabic PP67MH6).
Plan de traitement d’urgence : Lorsqu’un coup court se produit, vérifiez immédiatement l’état de l’anneau chauffant de la buse et de l’anneau de contrôle.
4. Flash : excès de matière sur les bords des pièces
A quoi ça ressemble : Fines ailettes en plastique le long des plans de joint ou des broches d’éjection.
Procédés à haut risque : moulage par injection multicolore, encapsulation de silicone.

Causes profondes :
- Décalage excessif entre la pression d’injection et la force de serrage.
- Composants du moule usés (par exemple, surfaces de séparation endommagées).
- Matériaux à faible viscosité (par exemple, silicone liquide LSR).
Les correctifs de BFY Mold :
- Ajuster la force de serrage :
- Calculer la force de serrage nécessaire à l’aide de la formule suivante : surface projetée (cm²) × pression du matériau (MPa) × facteur de sécurité 1,2.
- Cas de figure : Une palette en PP d’une surface projetée de 800 cm² nécessite une force de serrage : 800 × 35 × 1,2 = 336 tonnes → Choisir une machine de 350 tonnes.
- Entretien des moisissures :
- Polissez le plan de joint tous les 50 000 moules et maintenez la valeur Ra inférieure à 0,4μm.
- Réduire la vitesse d’injection :
- La vitesse d’injection du LSR passe de 50 % à 30 %, ce qui réduit le risque de débordement.
5. Lignes d’écoulement : Risques esthétiques et structurels
À quoi cela ressemble-t-il ? Motifs ondulés ou décoloration le long des voies d’écoulement.
Couramment utilisé dans les pièces transparentes (telles que les abat-jour en PC) et les surfaces très brillantes.
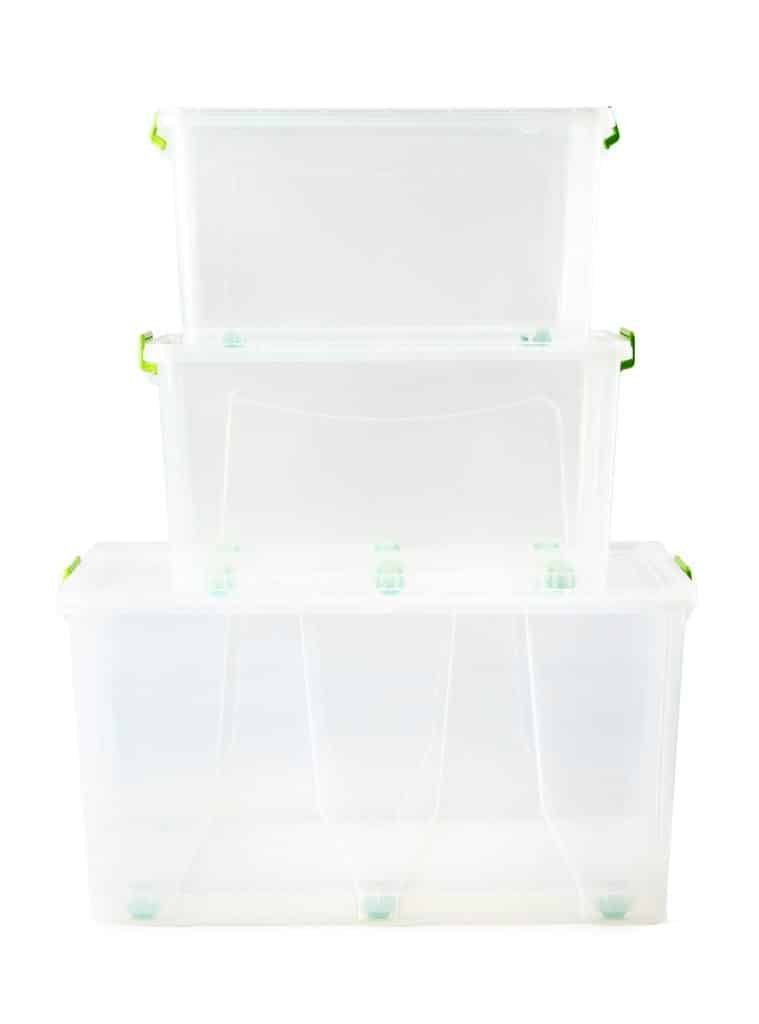
Causes profondes :
- Fluctuations de la température de la matière fondue (par exemple, fluctuations de ±10°C).
- Interférence multi-porte provoquant des collisions de fronts d’écoulement.
- Contamination ou humidité dans le matériau.
Les correctifs de BFY Mold :
- Stabiliser la température de fusion
- Vérifier le serpentin de chauffage et le thermocouple pour s’assurer que la fluctuation de la température de la barrique n’est pas trop importante.
- Optimiser l’emplacement des portes :
- Grâce à l’analyse de l’écoulement du moule, la différence de température du front d’écoulement a été contrôlée à 5°C près.
- Matériaux pré-séchés :
- Nylon séché à 85°C pendant 4 heures, teneur en humidité <0,15%.
Cas client : Le fabricant de lentilles LED a réduit le taux de défaut de la marque d’écoulement de 12 % à 0,3 % en ajustant la position de la porte et la température du moule à 110 °C.
Boîte à outils de prévention des défauts de BFY Mold
- Système de surveillance en temps réel : Des capteurs installés sur la machine suivent les courbes de pression et de température et déclenchent automatiquement une alarme lorsqu’elles s’écartent de la norme.
- Base de données des matériaux : Modèles de paramètres de processus pour plus de 1000 matériaux (tels que le temps de maintien et la vitesse de refroidissement).
- Service de réponse rapide : Fournir une assistance technique 24 heures sur 24, 7 jours sur 7, pour diagnostiquer à distance la cause première des défauts de moulage par injection.
Conclusion
Corrigez les marques d’enfoncement, les gauchissements, les bavures et bien plus encore grâce aux solutions éprouvées de BFY Mold pour les défauts de moulage par injection. Contactez-nous et optimisez la qualité de votre production dès aujourd’hui.