Le moulage par injection est un procédé de fabrication courant utilisé pour produire un large éventail de produits en plastique, allant des simples articles ménagers aux composants automobiles complexes.
Un aspect essentiel de ce processus est la conception et l’optimisation des moules, en particulier des moules multi-empreintes. Les moules multi-empreintes permettent la production simultanée de plusieurs pièces en un seul cycle d’injection, ce qui améliore considérablement la productivité et réduit les coûts. Cependant, l’optimisation des moules multi-empreintes en vue d’une meilleure production par moulage par injection nécessite un examen minutieux de divers facteurs afin de garantir une qualité et une efficacité constantes.
Comprendre les moules multi-empreintes
Les moules multi-empreintes comportent plusieurs cavités à l’intérieur d’une seule base de moule, chaque cavité produisant une pièce par cycle. Le principal avantage des moules multi-empreintes est leur capacité à produire plusieurs pièces simultanément, ce qui permet d’augmenter les cadences et de réduire les temps de cycle. Ils sont donc particulièrement adaptés à la production de gros volumes. Toutefois, la conception et l’optimisation des moules multi-empreintes sont plus complexes que celles des moules mono-empreintes en raison de la nécessité d’un remplissage uniforme, d’une qualité constante et d’un refroidissement efficace.
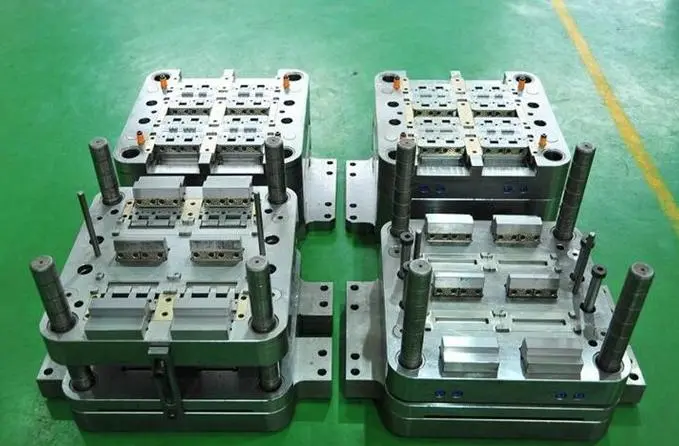
Considérations clés pour l’optimisation
1. Conception et agencement du moule
La conception et l’agencement du moule sont essentiels pour obtenir des performances optimales. Les facteurs à prendre en compte sont les suivants
- Disposition des cavités : La disposition des cavités doit minimiser la distance que le plastique fondu doit parcourir, afin d’assurer un remplissage uniforme. Les dispositions les plus courantes sont les dispositions équilibrées et symétriques.
- Système d’écoulement : Le système de canaux doit être conçu pour équilibrer le flux de plastique fondu dans chaque cavité. Il s’agit de placer stratégiquement les vannes et les canaux pour assurer une distribution égale de la pression et de la température.
- Canaux de refroidissement : Un refroidissement efficace est essentiel pour réduire les temps de cycle et éviter les défauts. La conception des canaux de refroidissement doit permettre un refroidissement uniforme dans toutes les cavités, en minimisant les gradients thermiques et les déformations.
2. Sélection des matériaux
Le choix du matériau approprié pour le moule et les pièces moulées est essentiel. Les matériaux des moules doivent présenter une conductivité thermique élevée, une résistance à l’usure et une solidité suffisante pour supporter les rigueurs du moulage par injection.
Pour les pièces moulées, le matériau doit présenter des propriétés d’écoulement, des taux de rétrécissement et des propriétés mécaniques appropriés afin de garantir une production de haute qualité.
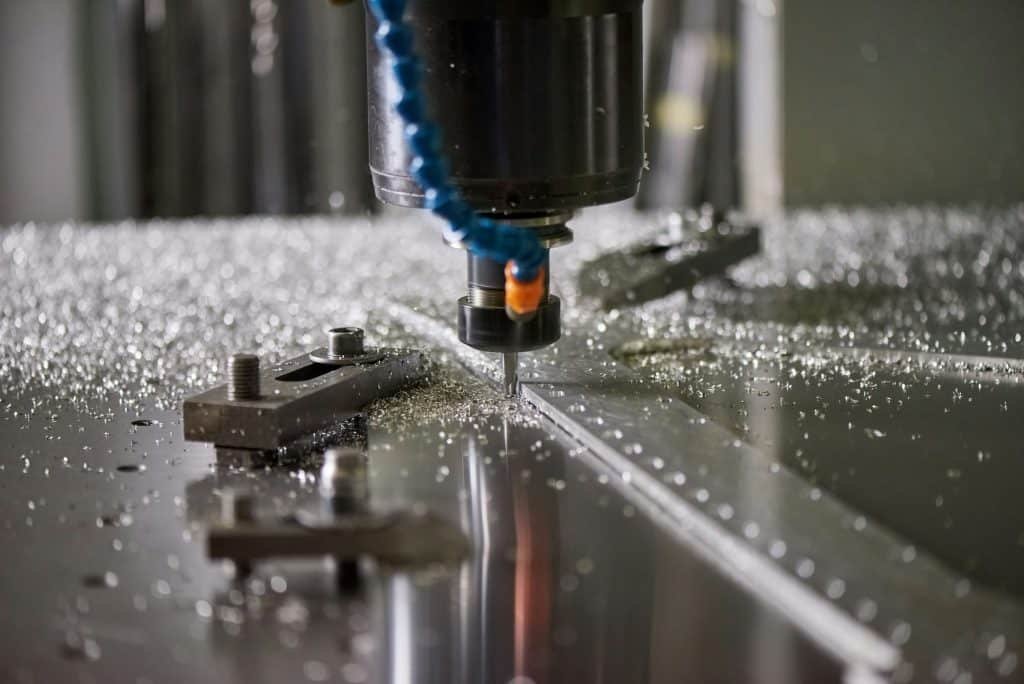
3. Paramètres du processus
L’optimisation des paramètres du processus est essentielle pour obtenir une qualité et une efficacité constantes. Les paramètres clés à prendre en compte sont les suivants
- Pression et vitesse d’injection : elles doivent être réglées de manière à assurer un remplissage uniforme de toutes les cavités sans provoquer de contraintes ou de défauts excessifs.
- Contrôle de la température : Le maintien d’une température constante de la matière fondue et du moule est essentiel pour assurer un écoulement et un refroidissement uniformes. Des systèmes avancés de contrôle de la température peuvent aider à atteindre cet objectif.
- Temps de cycle : Réduire le temps de cycle sans compromettre la qualité est un objectif primordial. Cela implique d’optimiser les phases d’injection, de refroidissement et d’éjection.
4. Simulation et analyse
L’utilisation d’outils d’ingénierie assistée par ordinateur (IAO) pour la simulation de l’écoulement des moules peut considérablement améliorer le processus d’optimisation. La simulation permet de prédire le comportement de l’écoulement, l’efficacité du refroidissement et les défauts potentiels, ce qui permet aux concepteurs de prendre des décisions et de procéder à des ajustements en connaissance de cause avant la production réelle.
Stratégies d’amélioration de la production
1. Remplissage équilibré
Il est essentiel d’assurer un remplissage équilibré de toutes les cavités pour garantir une qualité constante. Pour ce faire, il faut
- Analyse des flux : Effectuez une analyse du débit pour identifier les déséquilibres potentiels et adaptez la conception des canaux et des vannes en conséquence.
- Vannes : L’utilisation de vannes permet de contrôler avec précision le processus de remplissage et de s’assurer que chaque cavité se remplit uniformément.
2. Refroidissement efficace
Un refroidissement efficace est essentiel pour réduire les temps de cycle et prévenir les défauts. Les stratégies sont les suivantes :
- Canaux de refroidissement conformes : Ces canaux épousent la forme de la pièce, ce qui permet un refroidissement plus efficace et plus uniforme que les canaux traditionnels en ligne droite.
- Technologies de refroidissement avancées : Les technologies telles que les chicanes, les bulles et les caloducs peuvent améliorer l’efficacité du refroidissement.
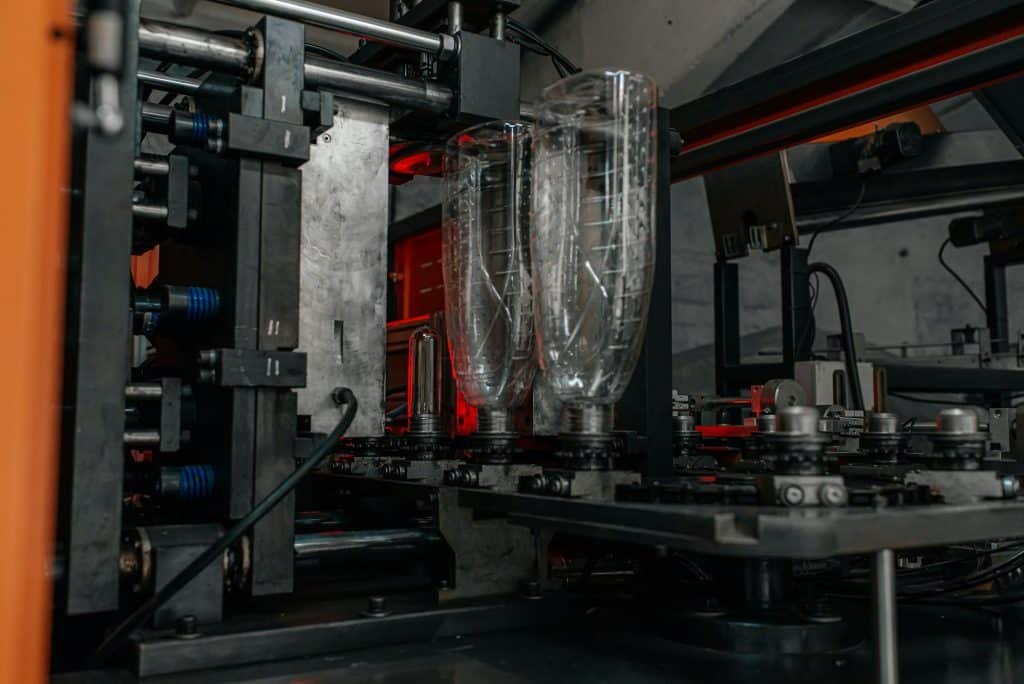
3. Contrôle de la qualité
Le maintien d’une qualité élevée dans toutes les cavités nécessite des mesures de contrôle de la qualité rigoureuses :
- Capteurs dans le moule : L’utilisation de capteurs pour surveiller la température, la pression et le débit à l’intérieur du moule peut fournir des données en temps réel permettant d’ajuster le processus.
- Entretien régulier : Effectuer un entretien régulier des moules et des machines afin d’éviter l’usure qui peut entraîner des défauts.
Études de cas et applications
1. L’industrie automobile
Dans l’industrie automobile, les moules multi-empreintes sont utilisés pour produire des composants tels que les tableaux de bord, les poignées de porte et les couvercles de moteur. L’optimisation de ces moules consiste à garantir une qualité uniforme dans toutes les cavités afin de répondre à des normes de sécurité et de performance rigoureuses. Des techniques telles que la simulation de flux, les vannes et les systèmes de refroidissement avancés sont couramment utilisées.
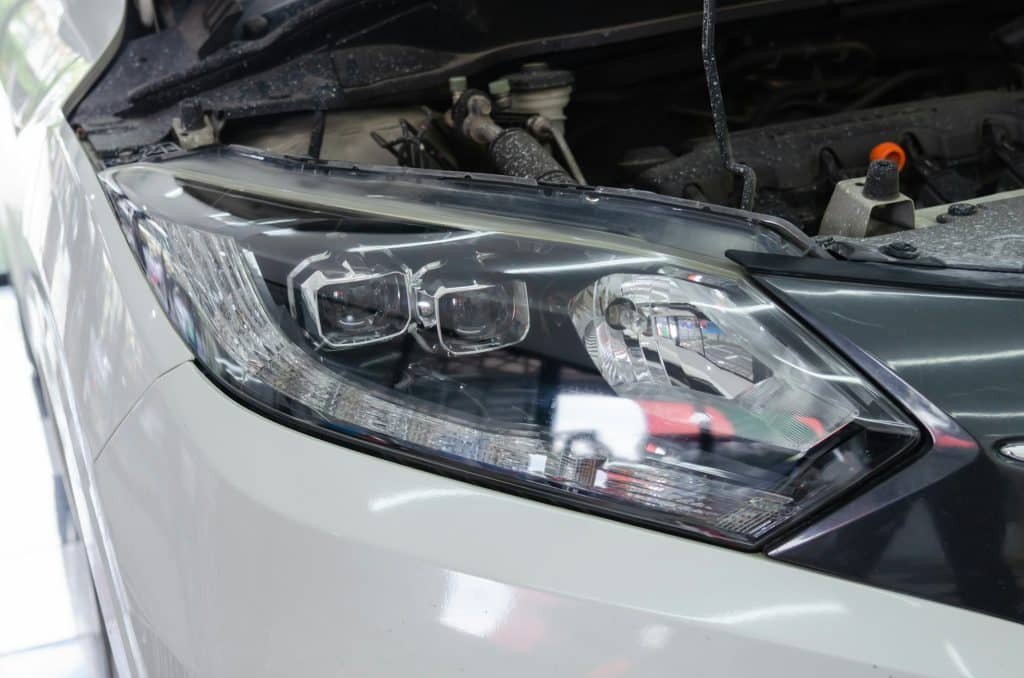
2. Biens de consommation
Pour les biens de consommation à grand volume tels que les capsules de bouteilles, l’optimisation des moules multi-empreintes est cruciale pour répondre à la demande et maintenir la rentabilité. Dans ce secteur, il est essentiel de disposer de systèmes d’écoulement efficaces, de temps de cycle rapides et de mesures robustes de contrôle de la qualité.

Tendances futures
L’avenir de l’optimisation des moules multi-empreintes repose sur les progrès de la technologie et des matériaux. Les tendances émergentes sont les suivantes :
- Impression 3D de moules : La fabrication additive permet de créer des géométries de moules complexes et des canaux de refroidissement conformes, ce qui améliore les performances et réduit les délais.
- Fabrication intelligente : L’intégration de l’IoT et de l’IA dans le moulage par injection peut permettre une surveillance en temps réel et une maintenance prédictive, ce qui optimise encore l’efficacité de la production.
L’optimisation des moules multi-empreintes pour améliorer la production de moulage par injection est un processus à multiples facettes qui implique un examen minutieux de la conception du moule, de la sélection des matériaux, des paramètres du processus et des techniques de simulation avancées. En mettant en œuvre des stratégies telles qu’un remplissage équilibré, un refroidissement efficace et un contrôle qualité rigoureux, les fabricants peuvent obtenir une productivité plus élevée, une qualité constante et des coûts réduits. La technologie continuant à progresser, l’avenir offre des possibilités prometteuses d’optimisation et d’innovation dans le domaine du moulage par injection.