1. Vue d’ensemble du moulage par injection à basse pression
Le moulage par injection à basse pression (LPIM) est une méthode de moulage dans laquelle le matériau est injecté dans le moule dans un environnement à basse pression, contrairement au moulage par injection conventionnel. Ce procédé est fréquemment utilisé pour l’encapsulation de composants électroniques et d’éléments fragiles, ainsi que pour l’étanchéité à l’air et au gaz.

2. Fonctionnement du procédé de moulage à basse pression
Processus de moulage à basse pression Dans le processus de moulage à basse pression, les matériaux thermoplastiques tels que le polyamide (PA) sont chauffés et les matériaux fondus sont injectés dans une cavité. La pression d’injection élevée et faible minimise les contraintes sur les pièces, ce qui en fait l’un des meilleurs résultats pour les pièces délicates.
Étapes du processus de moulage à basse pression :
- Chargement des matériaux : Les thermoplastiques sont fondus dans la machine.
- Préparation des moules : Nettoyer et préparer les moules, généralement à l’aide d’agents de démoulage.
- Injection : Le matériau fondu est introduit dans une chambre sous une pression contrôlée.
- Refroidissement : Le composant durcit en refroidissant dans le moule.
- L’éjection : L’éjection est la phase au cours de laquelle le produit moulé est retiré.
3. Avantages du moulage à basse pression
Les pressions douces préservent les pièces sensibles : Protéger les composants
- Temps de cycle réduits : Une pression plus faible permet un refroidissement plus rapide.
- Conception plus facile du moule : Des pressions réduites permettent d’obtenir des moules moins rigides.
- Durable : Plus besoin d’encapsulation secondaire [Waste reduction]
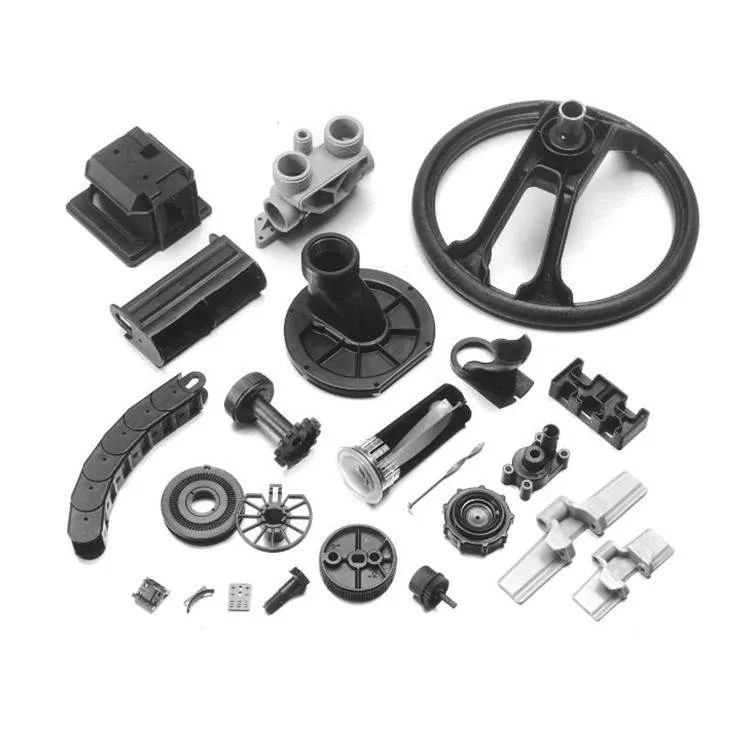
4. Inconvénients du moulage à basse pression
Le moulage à basse pression présente des avantages, mais aussi des inconvénients :
- Restrictions concernant les matériaux : Tous les thermoplastiques ne conviennent pas, par exemple le polyamide.
- Coût de l’installation électrique – Les matériaux spécialisés à basse pression peuvent faire grimper les coûts.
- Faible précision des détails : Les géométries élevées peuvent ne pas être possibles.
5. Cas d’utilisation dans les différents secteurs
Moulage à froid et diverses applications de moulage par injection à basse pression
- Électronique : Capteurs, connecteurs et encapsulation des circuits.
- Automobile : Couvre le câblage et les composants électroniques délicats.
- Dispositifs médicaux : Pièces scellées et biocompatibles.
- Biens de consommation : Composants durables et étanches des appareils électroménagers.
6. Moulage à basse pression et moulage par injection traditionnel
Fonctionnalité | Moulage à basse pression | Moulage par injection traditionnel |
Pression d’injection | Plus bas | Plus élevé |
Compatibilité des matériaux | Limitée | Large |
Applications | Délicatesse/Encapsulation | Production de masse |
Coût de l’outillage | Plus bas | Plus élevé |
Durée du cycle | Plus rapide | Plus lent |
7. Moulage à basse pression – Éléments à prendre en compte lors du lancement des projets
Gardez ces points à l’esprit lorsque vous concevez un projet de moulage à basse pression :
- Sélection des matériaux : Choisir des thermoplastiques compatibles avec l’application.
- Conception des pièces Des pièces simples peuvent conduire à des moules simples, mais aussi à des coûts plus faibles.
- Ne pas aller trop loin dans la complexité – Une plus grande précision n’est pas obtenue en raison d’une moindre précision.
- Volume de production adapté : Production moyenne à faible.
8. Défauts courants et stratégies d’amélioration du moulage à basse pression
Voici quelques défauts du moulage à basse pression et les moyens d’y remédier :
Défaut | Cause | Stratégie d’amélioration |
Déformation | Refroidissement inégal | Assurer des températures uniformes dans les moules |
Remplissage incomplet | Faible pression d’injection | Augmenter la vitesse/pression d’injection |
Flash | Mauvais serrage du moule | Amélioration de l’adaptation au moule et de la force de serrage |
Bulles d’air | Air emprisonné dans le matériau | Dégazage du matériau avant l’injection |
9. À propos de BFY Mold
BFY Mold est un fournisseur de confiance de solutions de moulage par injection et de fabrication de moules, offrant des services tels que la production de masse, la production à la demande, l’usinage CNC et l’étincelle miroir. Grâce à notre usine et à nos années d’expertise, nous fournissons des pièces conçues avec précision et adaptées à vos besoins.
Les 10 questions les plus fréquemment posées sur le moulage par injection à basse pression
1. Qu’est-ce que le moulage par injection à basse pression et en quoi diffère-t-il du moulage par injection traditionnel ?
Dans le moulage traditionnel, le moulage par injection à basse pression (MIBP) utilise une pression de 20 à 200 psi (contre 1 000 à 30 000 psi) pour encapsuler des composants délicats tels que des composants électroniques ou des capteurs. Il minimise les contraintes sur les pièces fragiles, réduit les déchets de matériaux et permet des cycles plus rapides (10 à 30 secondes).
2. Quels sont les matériaux compatibles avec le moulage par injection à basse pression ?
Les matériaux les plus courants sont les suivants
- Thermoplastiques : Polyamide (PA), polyuréthane thermoplastique (TPU).
- Fondus à chaud : Acétate d’éthylène-vinyle (EVA) pour l’étanchéité.
- Silicones : Pour une résistance à haute température (jusqu’à 150°C).
3. Quelles sont les industries qui bénéficient le plus du moulage par injection à basse pression ?
- Électronique : Encapsulation de cartes de circuits imprimés, de connecteurs et de faisceaux de câbles.
- Automobile : Capteurs d’étanchéité et éclairage LED.
- Médical : Imperméabilisation des composants de dispositifs implantables.
4. Comment la méthode LPIM réduit-elle les coûts de production par rapport aux méthodes traditionnelles ?
- Coûts d’outillage réduits : Les moules en aluminium coûtent 30 à 50 % de moins que les moules en acier.
- Réduction des déchets de matériaux : Un dosage précis permet de réduire les déchets de 15 à 25 %.
- Économies d’énergie : Les machines à basse pression consomment 40 % d’énergie en moins.
5. Quelles sont les tolérances que l’on peut obtenir avec le moulage par injection à basse pression ?
Le LPIM permet généralement d’obtenir des tolérances de ±0,1-0,3 mm, ce qui convient à l’encapsulation de composants électroniques sensibles. Pour des tolérances plus étroites (±0,05 mm), des processus hybrides avec finition CNC peuvent être nécessaires.
6. Comment les fournisseurs assurent-ils la qualité des processus de moulage à basse pression ?
- Validation du processus : Analyse de l’écoulement du moule pour prévoir les vides ou les pièges à air.
- Inspections en ligne : Des systèmes de vision automatisés vérifient la présence de défauts tels qu’un remplissage incomplet.
- Certifications : ISO 9001 et IATF 16949 pour les applications automobiles.
7. Le LPIM peut-il gérer des géométries complexes ou des composants multimatériaux ?
Oui. LPIM excelle dans :
- Surmoulage : Collage de thermoplastiques sur des métaux ou des céramiques.
- Microcaractéristiques : Encapsulation de composants avec des espaces aussi réduits que 0,2 mm.
- Moulage en plusieurs fois : superposition de matériaux pour obtenir des propriétés hybrides (par exemple, rigide + flexible).
8. Quel est le délai de réalisation typique des projets de moulage par injection à basse pression ?
- Prototypage : 1 à 2 semaines avec des moules imprimés en 3D ou des moules souples.
- Production : 4 à 8 semaines (y compris la fabrication du moule). Les services accélérés permettent de réduire les délais de 30 % pour les commandes urgentes.
9. Quelle est la durabilité du moulage par injection à basse pression ?
LPIM est respectueux de l’environnement grâce à
- Matériaux recyclables : Le TPU et le PA sont largement recyclables.
- Efficacité énergétique : Réduction de la consommation d’énergie de la machine.
- Réduction des déchets : <5% de déchets de matériaux contre 10-15% dans le moulage traditionnel.
10. Quels services post-moulage les fournisseurs proposent-ils pour les composants LPIM ?
- Revêtement conforme : Résistance accrue à l’humidité pour l’électronique.
- Marquage au laser : Numéros de série ou logos permanents.
- Essais fonctionnels : Contrôles de la continuité électrique, validation de l’étanchéité IP67.