Au cours du processus de moulage par injection, comment faire face à la température élevée de la machine de moulage par injection, vous devez comprendre ses effets néfastes et apprendre à y faire face.
Si la température de la machine de moulage par injection augmente trop, il existe cinq risques majeurs : déformation thermique mécanique, réduction de la viscosité de l’huile, déformation du joint en caoutchouc, accélération de l’oxydation de l’huile et réduction de la pression de l’air.
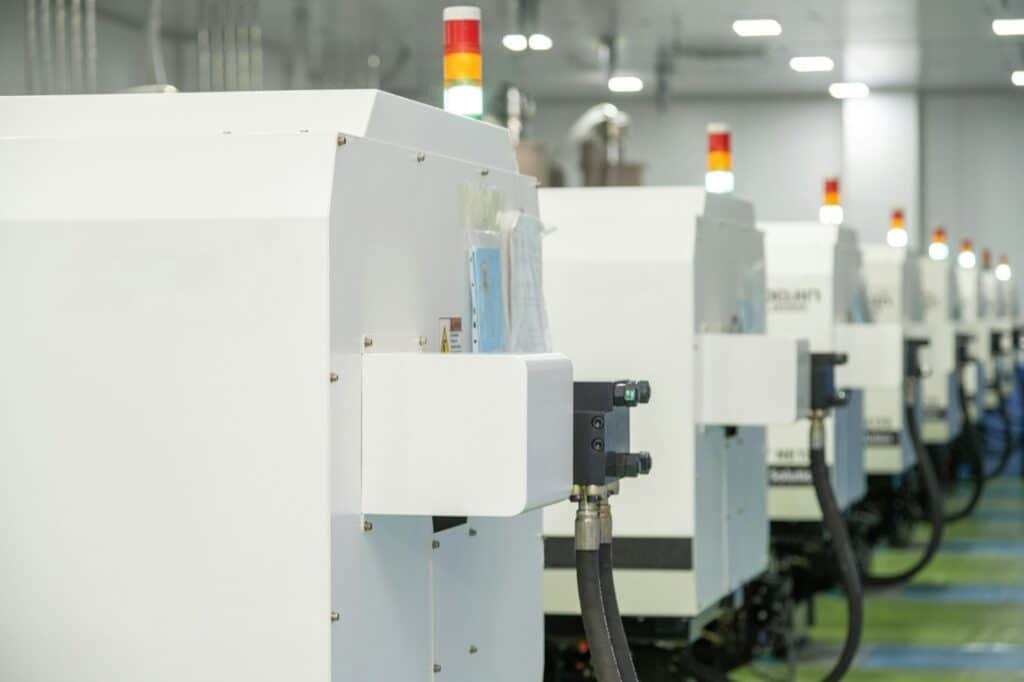
Risques liés aux températures élevées dans la production
Déformation thermique des machines
Les pièces mobiles ayant des coefficients de dilatation thermique différents dans les composants hydrauliques sont bloquées en raison de l’écart d’adaptation plus faible, ce qui entraîne une défaillance de l’action, affecte la précision de la transmission du système hydraulique et conduit à une mauvaise qualité de fonctionnement des pièces.
Réduire la viscosité de l’huile
L’augmentation de la température de la machine de moulage par injection entraîne une diminution de la viscosité de l’huile, une augmentation des fuites et une réduction significative de l’efficacité volumétrique de la pompe et de l’efficacité de l’ensemble du système. Lorsque la viscosité de l’huile diminue, le film d’huile des pièces mobiles telles que la vanne à glissière s’amincit et se coupe, et la résistance au frottement augmente, ce qui accroît l’usure.
Déformation du joint en caoutchouc
L’augmentation de la température de la machine de moulage par injection déforme les joints en caoutchouc, accélère leur vieillissement et réduit les performances et la durée de vie des joints, ce qui entraîne des fuites.
Accélérer la détérioration par oxydation de l’huile
L’augmentation de la température des machines de moulage par injection accélère l’oxydation et la détérioration de l’huile, précipite les substances bitumineuses et réduit la durée de vie de l’huile hydraulique. Les précipités obstruent les trous d’amortissement et les orifices des vannes à fente, ce qui bloque la vanne de pression et l’empêche de fonctionner, et le pipeline métallique est étiré et plié, voire cassé.
La qualité de fonctionnement des composants se détériore
L’augmentation de la température de la machine de moulage par injection entraîne une détérioration de la qualité des composants, et l’air dissous dans l’huile s’échappe, créant des poches d’air qui réduisent les performances du système hydraulique.
La température de fonctionnement idéale du système hydraulique doit se situer entre 45 et 50 degrés, car le système hydraulique est conçu en fonction d’une viscosité d’huile sous pression sélectionnée. Cependant, la viscosité change en fonction de la température de l’huile, ce qui affecte les composants du système, tels que les cylindres et les valves hydrauliques. Il est facile de réduire la précision du contrôle et la sensibilité de la réponse, en particulier pour les machines d’injection de précision. Par ailleurs, une température trop élevée accélère le vieillissement du joint, qui durcit et se brise.
Si la température est trop basse, la consommation d’énergie de traitement est importante et la vitesse de fonctionnement est réduite. Il est donc nécessaire d’accorder une attention particulière à la température de fonctionnement de l’huile hydraulique. Les raisons d’une température élevée de l’huile sont diverses, mais la plupart d’entre elles sont attribuées à une défaillance du circuit d’huile ou à une défaillance du système de refroidissement.
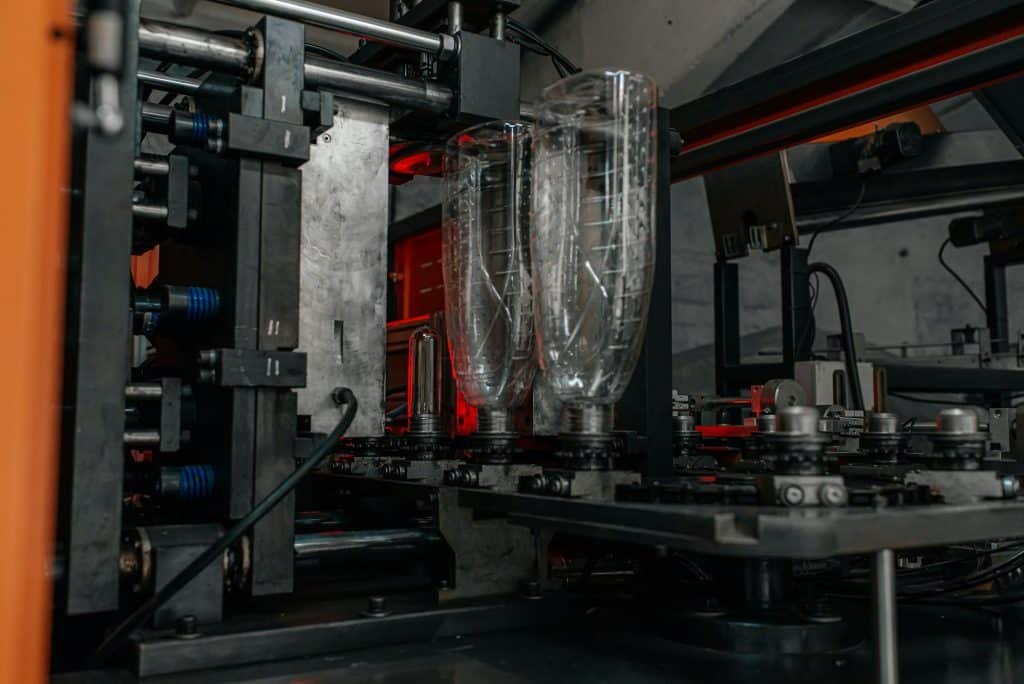
Méthode de traitement de la surchauffe de la machine de moulage par injection
(1) En fonction des différentes exigences de charge, il est fréquent de vérifier et d’ajuster la pression de la soupape de décharge pour qu’elle soit parfaitement adaptée.
(2) Sélection raisonnable de l’huile hydraulique, en particulier de la viscosité de l’huile, en fonction des conditions, utiliser autant que possible une viscosité plus faible pour réduire la perte de friction due à la viscosité.
(3) Améliorer les conditions de lubrification des pièces mobiles afin de réduire les pertes par frottement, ce qui contribue à réduire la charge de travail et la chaleur.
(4) Améliorer la qualité et la précision de l’assemblage des composants et des systèmes hydrauliques, contrôler strictement l’écart entre les pièces assemblées et améliorer les conditions de lubrification. Le matériau d’étanchéité à faible coefficient de frottement et la structure d’étanchéité améliorée sont utilisés pour réduire autant que possible la puissance de démarrage du cylindre hydraulique afin de réduire la chaleur générée par la perte de frottement mécanique.
(5) Ajouter des dispositifs de refroidissement si nécessaire.