Le moulage par injection de produits transparents, tels que les lentilles optiques, les boîtiers d’appareils médicaux ou les emballages de produits de consommation, exige une attention méticuleuse à la pureté des matériaux, à la précision du processus et à l’intégrité de la finition de la surface. Même des imperfections mineures telles que des bulles, des marques d’écoulement ou un voile peuvent rendre les produits inutilisables, d’où l’importance de chaque étape, de la préparation des matériaux à la conception des moules.
Ce guide présente sept facteurs non négociables, notamment des protocoles de séchage avancés, le contrôle de la température du moule et des techniques de polissage de qualité optique, afin de garantir des résultats d’une clarté cristalline. Qu’il s’agisse de produire des composants en PMMA ou en polycarbonate, ces stratégies minimisent les retouches et s’alignent sur les normes industrielles en matière de transparence et de durabilité.
Normes d’état de surface pour la clarté des produits transparents
Les plastiques transparents requièrent des normes de qualité de surface strictes en raison de leur forte transmission de la lumière. Les défauts tels que les marques, les pores, la décoloration et le manque de brillance sont inacceptables. Chaque aspect du processus de moulage par injection – matériaux, équipement, moules et conception du produit – doit répondre à des exigences strictes.

Moulage de produits transparents : Élimination du voile et des bulles
Les plastiques transparents ont généralement des points de fusion élevés et une mauvaise fluidité. Pour garantir la qualité du produit, il est nécessaire de régler avec précision les paramètres du processus, tels que la température du cylindre, la pression d’injection et la vitesse d’injection. Cela permet de s’assurer que le plastique remplit le moule sans provoquer de contraintes internes, de déformations ou de fissures.
Séchage des matériaux pour l’intégrité des polymères transparents
Garantir la pureté des matériaux
Les impuretés dans le plastique peuvent affecter la transparence. Pendant le stockage, le transport et l’alimentation, les matériaux doivent être scellés pour rester propres. L’humidité contenue dans les matières premières peut entraîner une dégradation lorsqu’elles sont chauffées, c’est pourquoi un séchage complet est essentiel. Utilisez une trémie de séchage et veillez à ce que l’air d’entrée soit filtré et déshumidifié.
Nettoyage des équipements pour la pureté des produits transparents
Nettoyage du canon, de la vis et des accessoires
Prévenir la contamination en nettoyant la vis et les accessoires avec un produit de nettoyage pour vis avant l’utilisation et après l’arrêt. Si un agent de nettoyage n’est pas disponible, des résines PE ou PS peuvent être utilisées. Pendant les arrêts temporaires, réduire la température du sécheur et du tonneau pour éviter la dégradation des matières premières.
Conception de moules pour les produits transparents à haute brillance
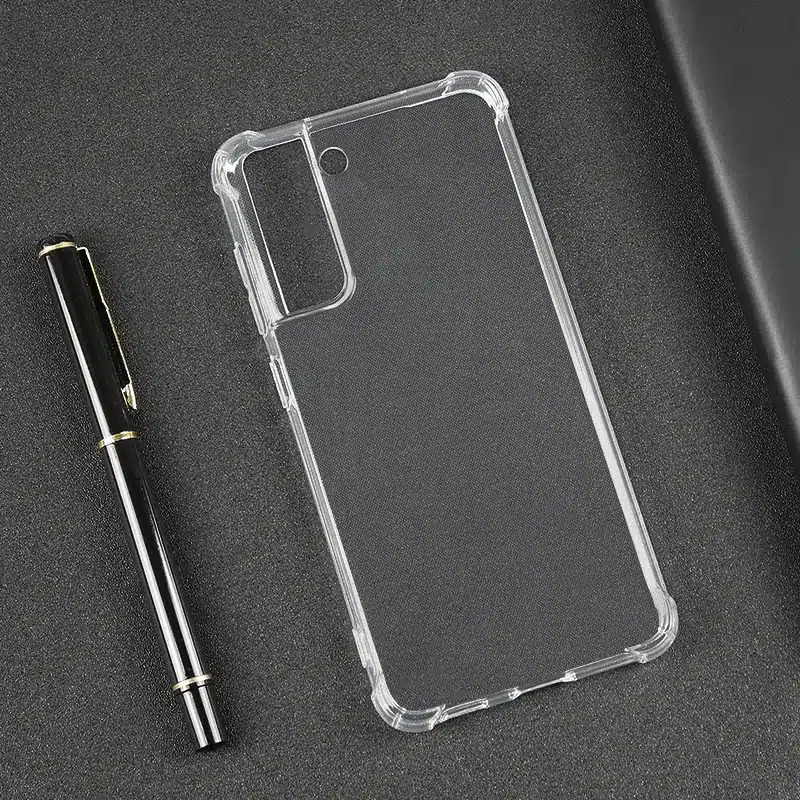
Concevoir pour la qualité
Pour éviter les défauts de surface :
1. Assurer une épaisseur de paroi uniforme et une pente de démoulage suffisante.
2. Les angles sont progressivement modifiés afin d’éviter les arêtes vives.
3. Utiliser des couloirs larges et courts et des portes bien placées avec des puits de refroidissement si nécessaire.
4. Veiller à ce que les surfaces des moules soient lisses, peu rugueuses et bien ventilées.
Surface du moule et épaisseur de la paroi
Les surfaces des moules doivent être lisses, avec une faible rugosité (de préférence inférieure à 0,8). Assurer une ventilation adéquate pour évacuer l’air et les gaz de la matière fondue. Éviter les parois trop fines, avec une épaisseur minimale de 1 mm, sauf pour le PET.
Paramètres d’injection pour les produits transparents cristallins
Paramètres d’injection optimaux
Pour minimiser les contraintes internes et les défauts de surface :
1. Utiliser une vis spéciale et une buse à température contrôlée.
2. Utiliser une température d’injection plus élevée dans les limites de décomposition de la résine.
3. Appliquer une pression d’injection élevée pour surmonter la viscosité du matériau fondu, mais pas au point de provoquer une déformation.
4. Opter pour une vitesse d’injection faible, en utilisant de préférence une injection lente-rapide-lente en plusieurs étapes.
5. Le temps de maintien de la pression et le cycle de moulage doivent être courts pour éviter les dépressions et les bulles.
6. Utiliser une vitesse de vis et une contre-pression faibles pour éviter la dégradation du matériau.
7. Contrôle précis de la température du moule pour un refroidissement optimal et une bonne qualité du produit.
Prévention des défauts dans le post-moulage de produits transparents
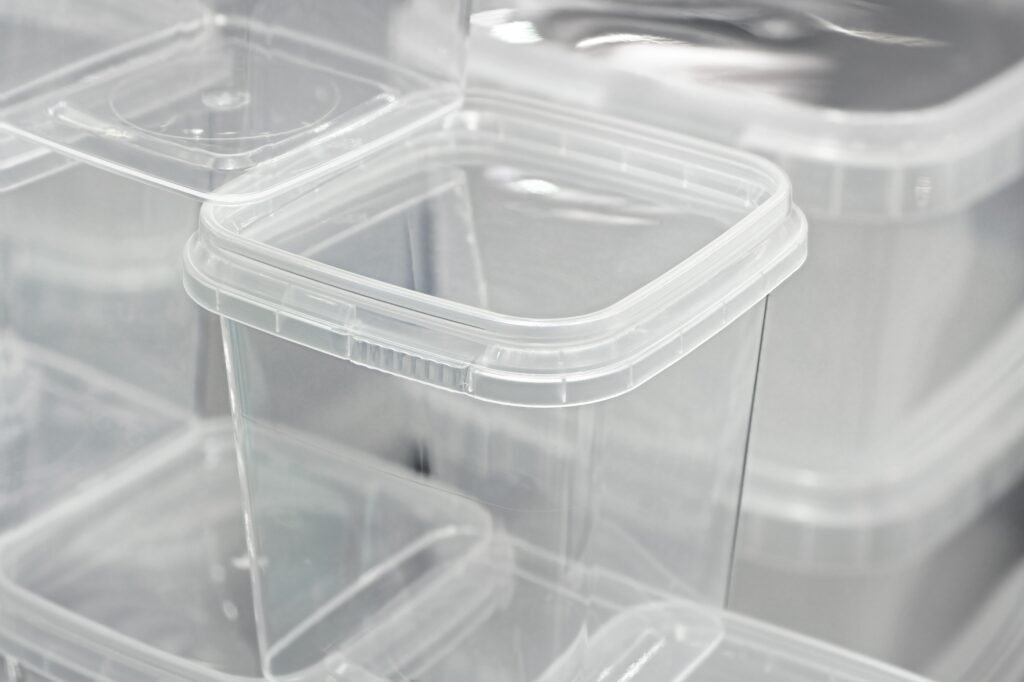
Utilisation d’agents de démoulage et de matériaux recyclés
Réduire au minimum l’utilisation d’agents de démoulage pour éviter la détérioration de la qualité de la surface. En cas d’utilisation de matériaux recyclés, veiller à ce qu’ils ne dépassent pas 20 %.
Post-traitement des produits
Certains matériaux, comme le PET, nécessitent un post-traitement pour éliminer les tensions internes. Le PMMA doit être séché à 70-80℃ pendant 4 heures, et le PC doit être chauffé à 110-135℃, la durée dépendant du produit. Le PET doit subir un étirage bidirectionnel pour obtenir de bonnes propriétés mécaniques.