La fluidité de l’ABS se situe entre le PS et le PC dans le processus de moulage par injection de l’ABS. La fluidité est influencée par la température et la pression lors de la détection, la pression d’injection ayant une influence globale légèrement plus importante. Par conséquent, des pressions d’injection élevées sont généralement utilisées au cours du processus de moulage pour améliorer le comportement de remplissage et réduire la viscosité de la matière fondue.
L’ABS est obtenu par copolymérisation d’acrylonitrile, de butadiène et de styrène et est communément appelé plastique acrylonitrile-butadiène-styrène. Les ratios de ces trois monomères peuvent être modifiés pour créer des ABS ayant des températures de fusion et des caractéristiques d’écoulement différentes. Différents matériaux ABS peuvent être produits à des fins diverses en combinant l’ABS avec d’autres plastiques ou additifs, tels que la qualité choc, la qualité résistante à la chaleur, la qualité ignifuge, la qualité transparente, la qualité renforcée et la qualité galvanoplastique.
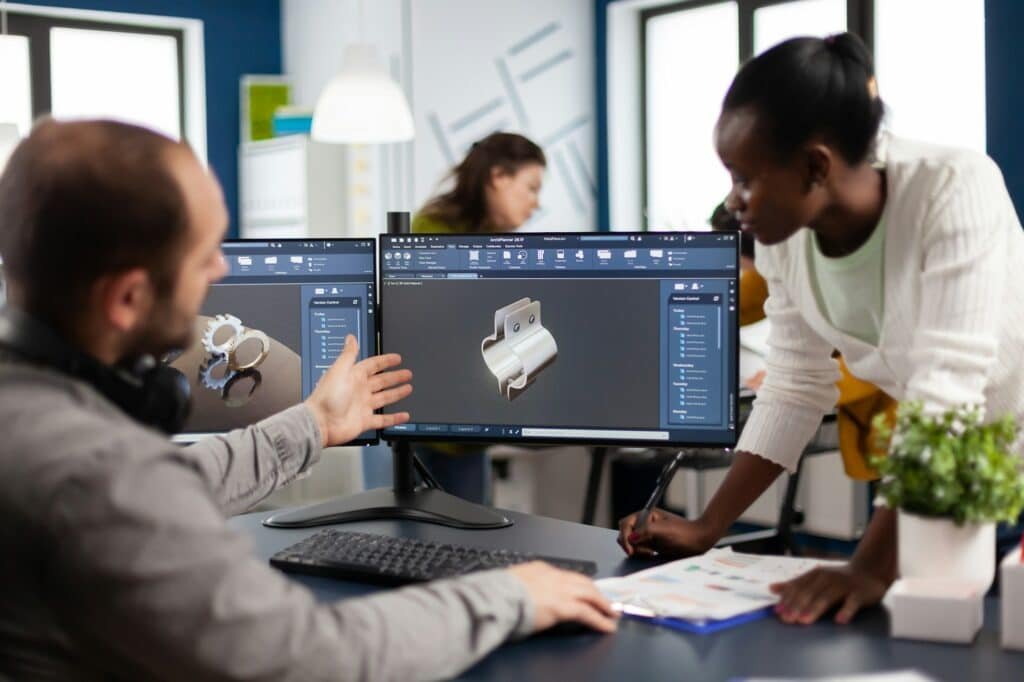
1. Traitement des matières plastiques
Le taux d’absorption d’eau de l’ABS est d’environ 0,2%-0.8%, et pour l’ABS de qualité générale, il est cuit à 80-85 ° C pendant 2-4 heures dans le four ou 1-2 heures avec une trémie de séchage à 80 ℃ avant le traitement de moulage par injection de l’ABS. Pour les composants PC contenant de l’ABS résistant à la chaleur, la température de séchage est ajustée de manière appropriée à 100 ℃, et le temps de séchage spécifique peut être déterminé par extrusion d’air.
La proportion de matériaux recyclés ne doit pas dépasser 30 %, et l’ABS de qualité galvanique ne peut pas utiliser de matériaux recyclés.
2. Sélection de la machine de moulage par injection
Une machine de moulage par injection standard (rapport longueur-diamètre de la vis 20:1, taux de compression supérieur à 2, pression d’injection supérieure à 150 MPa) peut être utilisée. Si un mélange maître de couleur est utilisé ou si l’apparence du produit exige un matériau de haute qualité, une vis de petit diamètre peut être sélectionnée. La force de serrage est déterminée en fonction de 4700-6200t/m2, selon la qualité du plastique et les exigences du produit.
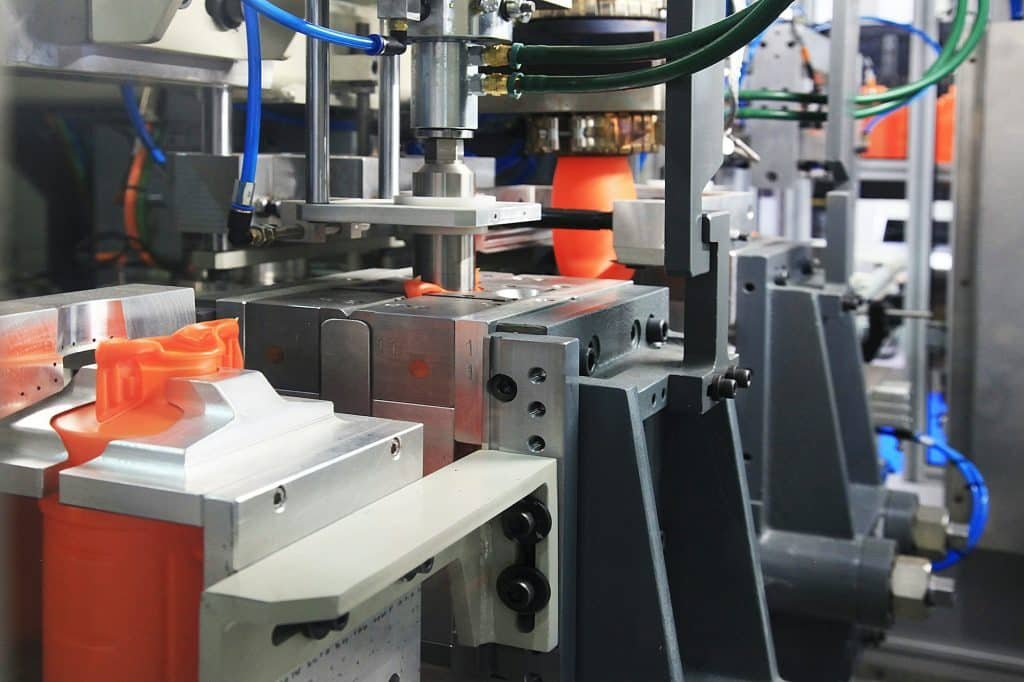
3. Conception du moule et de la porte
La température du moule peut être réglée à 60-65℃. Le diamètre de la coulisse est de 6 à 8 mm. La largeur de la porte est d’environ 3 mm, l’épaisseur est la même que celle du produit, et la longueur de la porte est inférieure à 1 mm. L’évent a une largeur de 4 à 6 mm et une épaisseur de 0,025 à 0,05 mm.
4. Température de fusion
Elle peut être déterminée avec précision par la méthode de l’injection d’air. Pour les différentes qualités, les températures de fusion sont également différentes, il est recommandé de les fixer comme suit :
- Classe d’impact : 220℃-260℃, 250℃ est préférable.
- Qualité du placage : 250℃-275℃, 270℃ est préférable.
- Grade de résistance à la chaleur : 240℃-280℃, avec 265℃-270℃ est mieux.
- Grade ignifuge : 200℃-240℃, 220℃-230℃ est mieux.
- Niveau de transparence : 230℃-260℃, 245℃ est préférable.
- Qualité renforcée par des fibres de verre : 230℃-270℃
Pour les produits présentant des exigences élevées en matière de surface, on utilise des températures de fusion et de moulage plus élevées.
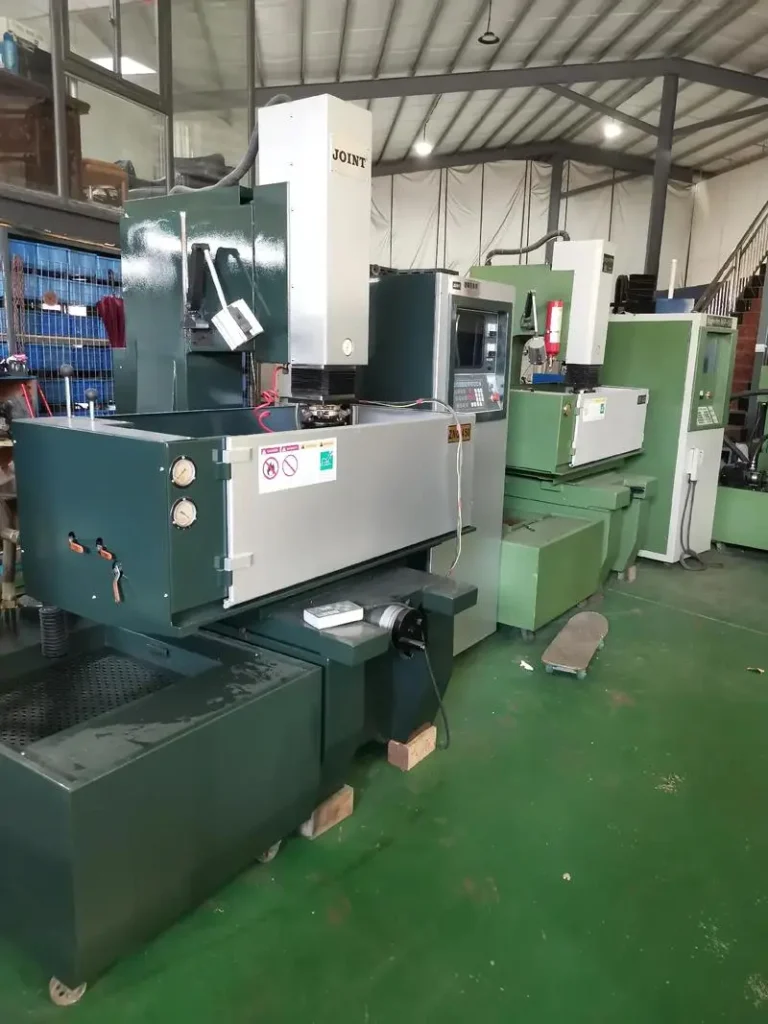
5. Vitesse d’injection
La catégorie « feu » doit être utilisée à vitesse lente, la catégorie « chaleur » à vitesse rapide. Lors du moulage par injection de l’ABS, si les exigences de surface du produit sont élevées, il convient d’utiliser la vitesse de contrôle du feu du moulage par injection à grande vitesse et en plusieurs étapes.
6. Contre-pression
Dans des circonstances normales, plus la contre-pression est faible, mieux c’est. La contre-pression couramment utilisée est de 0,5 MPa, et le matériel de teinture doit utiliser une contre-pression plus élevée pour rendre le mélange de couleurs uniforme.
7. Durée de conservation
À une température de 265 ° C, le temps de séjour de l’ABS dans le tube de fusion ne devrait pas dépasser 5-6 minutes. Le temps de retardateur de flamme est plus courte, si vous avez besoin d’arrêter, vous devez d’abord abaisser la température réglée à 100℃, puis nettoyer le tube de fusion avec ABS universel. Le mélange nettoyé doit être placé dans de l’eau froide pour éviter toute décomposition supplémentaire.
Si vous devez remplacer un matériau ABS par un autre plastique, vous devez d’abord nettoyer le tube de fusion avec du PS, du PMMA ou du PE. Certains produits ABS ne posent aucun problème lorsqu’ils viennent d’être mis en circulation, mais ils se décolorent au bout d’un certain temps, ce qui peut être dû à une surchauffe ou au fait que le plastique est resté trop longtemps dans le cylindre de fusion.
8. Post-traitement des produits
En général, les produits ABS ne nécessitent pas de post-traitement, seuls les produits galvanisés doivent être cuits (70-80℃, 2-4 heures) pour passivation des traces de surface, et les produits qui doivent être plaqués ne peuvent pas utiliser d’agents de démoulage, et les produits doivent être emballés immédiatement après avoir été retirés.
9. Le moulage doit faire l’objet d’une attention particulière
Il existe plusieurs qualités d’ABS (en particulier des qualités ignifuges), et l’adhérence de la matière fondue à la surface de la vis après la plastification est très importante, et elle se décomposera après une longue période. Lorsque la situation ci-dessus se produit, il est nécessaire de retirer la section d’homogénéisation et la compression de la vis pour essuyer le test, et de nettoyer régulièrement la vis avec du PS.