Moules à cavité unique et moules à cavités multiples
Dans le domaine du moulage par injection, le choix du bon type de moule est crucial pour la réussite de votre projet. Le choix entre un moule mono-empreinte et un moule multi-empreintes peut avoir un impact significatif sur l’efficacité de la production, le coût et la qualité du produit final. Le présent document se penche sur les principales différences entre les moules mono-empreinte et les moules multi-empreinte, en explorant leurs structures, leurs avantages, leurs fonctions et la manière de choisir celui qui convient le mieux à vos besoins spécifiques.
Qu’est-ce que le moule à cavité unique ?

Un moule à cavité unique est conçu pour produire une seule pièce par cycle d’injection. Ce type de moule est souvent utilisé lorsque la précision est essentielle ou lorsque le volume de production ne justifie pas la complexité et le coût d’un moule multi-empreintes. Les moules à simple empreinte sont plus simples à concevoir et comportent moins de pièces mobiles, ce qui les rend plus faciles à gérer et à entretenir.
L’un des principaux avantages des moules à empreinte unique est leur capacité à produire des pièces de haute qualité et homogènes. Comme il n’y a qu’une seule cavité, les variations ou les incohérences entre les pièces sont moins probables. Ceci est particulièrement important pour les industries où la précision et le contrôle de la qualité sont primordiaux, telles que les applications médicales ou aérospatiales.
Qu’est-ce que le moule multi-empreintes ?
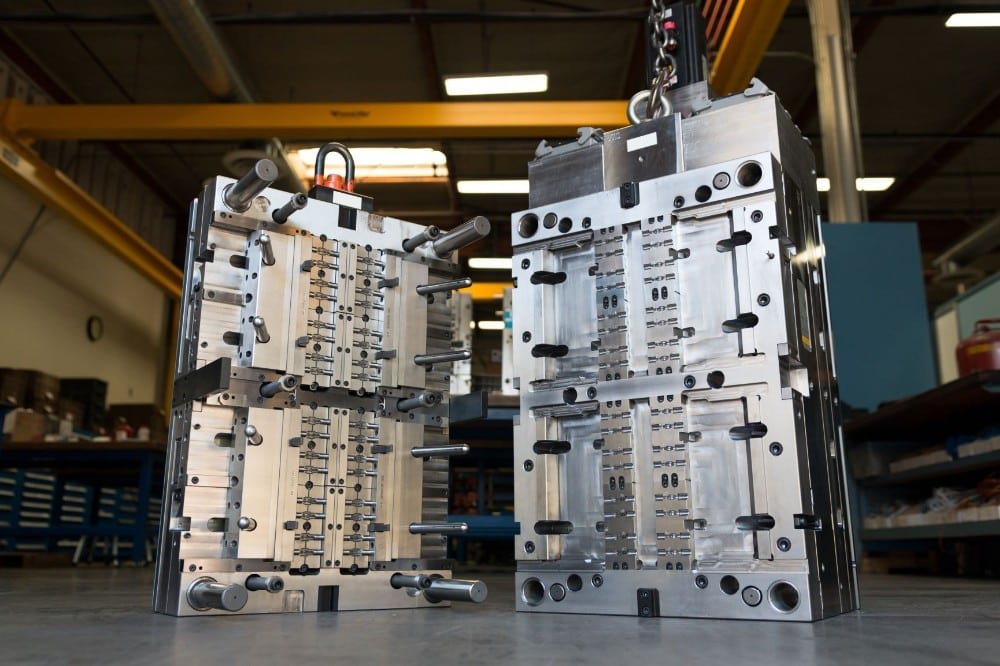
En revanche, un moule multi-empreintes est conçu pour produire plusieurs pièces identiques en un seul cycle d’injection. Le nombre de cavités peut varier considérablement, certains moules contenant deux, quatre, huit cavités, voire plus. Ce type de moule est idéal pour la production en grande série, où l’objectif est de maximiser le rendement et de minimiser la durée du cycle.
Les moules multi-empreintes sont couramment utilisés dans les industries où de grandes quantités de pièces sont requises dans un court laps de temps, comme dans les biens de consommation ou la fabrication automobile. La possibilité de produire plusieurs pièces simultanément permet de réaliser d’importantes économies sur le plan des coûts par pièce, ainsi que d’accroître l’efficacité du processus de production.
Comparaison des structures : Moule à cavité unique ou à cavités multiples
La structure de base des moules mono-empreinte et multi-empreinte comprend des éléments similaires : une base de moule, une empreinte, un noyau, des canaux de refroidissement et un système de canaux de coulée. Toutefois, la complexité de la conception augmente avec les moules multi-empreintes.
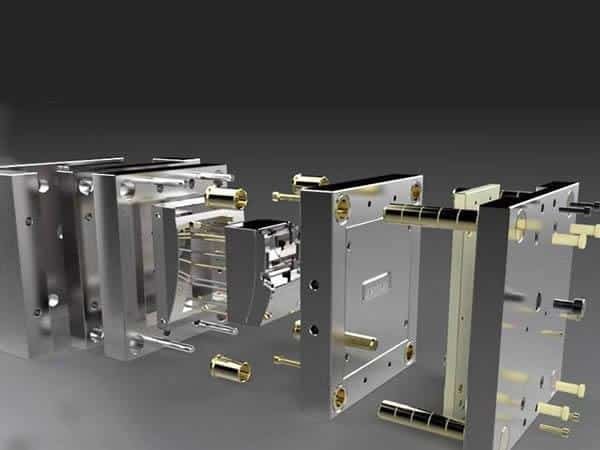
- Structure du moule à cavité unique : Le moule à cavité unique se compose d’une cavité et d’un noyau. La cavité forme la forme de la pièce, tandis que le noyau est la partie qui façonne les surfaces intérieures. Les canaux de refroidissement sont placés stratégiquement pour assurer un refroidissement uniforme de la pièce moulée, ce qui réduit la probabilité de défauts. Le système de coulée d’un moule à simple cavité est plus simple, car il ne doit acheminer la matière en fusion que dans une seule cavité.
- Structure des moules à cavités multiples : Les moules multi-empreintes, bien que fondés sur les mêmes principes, sont plus complexes. Plusieurs cavités et noyaux sont disposés dans la même base de moule, chacun nécessitant un alignement précis pour assurer une production uniforme. Le système de coulée doit être conçu de manière à acheminer la matière en fusion de façon homogène vers chaque cavité, ce qui peut s’avérer difficile à réaliser. En outre, les canaux de refroidissement doivent être soigneusement conçus pour garantir que toutes les pièces refroidissent à la même vitesse, afin d’éviter les variations de qualité.
La complexité des moules à cavités multiples s’étend également à la base du moule, qui doit être suffisamment robuste pour résister à la force de serrage accrue nécessaire pour maintenir les cavités multiples ensemble pendant le processus d’injection. Cela nécessite souvent l’utilisation de matériaux de qualité supérieure et un usinage plus précis, ce qui entraîne des coûts initiaux plus élevés que pour les moules à cavité unique.
Avantages des moules à cavité unique

- Précision et qualité : Avec une seule cavité, le risque de variation entre les pièces est minimisé, ce qui garantit une qualité constante.
- Une conception plus simple : La conception simple des moules à simple cavité les rend plus faciles à fabriquer, à entretenir et à dépanner.
- Coût initial moins élevé : La structure plus simple des moules à simple empreinte se traduit généralement par des coûts d’outillage moins élevés, ce qui en fait une option rentable pour les volumes de production faibles à moyens.
- Temps de préparation plus rapides : Avec moins de composants à aligner et à gérer, les moules à cavité unique nécessitent souvent moins de temps de préparation, ce qui permet de réduire les délais d’exécution pour les productions en petites séries.
Avantages des moules multi-empreintes
- Efficacité de production accrue : Les moules multi-empreintes peuvent produire plusieurs pièces en un seul cycle, ce qui augmente considérablement le rendement de la production et réduit la durée totale du cycle.
- Coût inférieur par pièce : Bien que le coût initial d’un moule multi-empreintes soit plus élevé, le coût par pièce diminue à mesure que le volume de production augmente, ce qui en fait une solution rentable pour la production à grande échelle.
- Qualité constante sur plusieurs pièces : Lorsqu’ils sont correctement conçus et entretenus, les moules multi-empreintes peuvent produire des pièces d’une qualité constante dans toutes les empreintes, ce qui garantit l’uniformité de la production de masse.
- Utilisation optimisée des matériaux : Les moules multi-empreintes peuvent permettre une meilleure utilisation des matériaux, réduisant ainsi les déchets et améliorant l’efficacité globale de la production.
Fonction des moules à cavité unique et à cavités multiples
La fonction première des moules à une ou plusieurs empreintes est de façonner le matériau fondu en une pièce finie. Toutefois, leurs fonctions et applications spécifiques peuvent varier en fonction des besoins de production :
Moules à cavité unique :
Ils conviennent parfaitement aux petites séries, au développement de prototypes ou aux situations où la précision et la qualité des pièces sont essentielles. Ils sont également idéaux pour les pièces plus grandes qui nécessitent une conception de moule plus simple.
Moules à cavités multiples :
Idéal pour la production en grande série où l’efficacité et le rendement sont les principales préoccupations. Les moules multi-empreintes sont couramment utilisés dans des secteurs tels que l’automobile, l’électronique grand public et l’emballage, où des milliers, voire des millions de pièces doivent être produites rapidement et régulièrement.

Comment choisir entre les moules à une ou plusieurs cavités ?
Le choix du bon type de moule dépend de plusieurs facteurs clés :
- Volume de production : Si votre projet nécessite de nombreuses pièces, un moule multi-empreintes peut être le choix le plus rentable et le plus efficace. Un moule à cavité unique peut être plus approprié pour les petites séries ou les pièces spécialisées.
- Complexité et taille des pièces : Les pièces complexes ou de grande taille peuvent être mieux adaptées aux moules mono-empreinte, qui permettent un contrôle et une assurance qualité plus précis. Les pièces plus petites et plus simples peuvent souvent être produites plus efficacement avec un moule multi-empreintes.
- Budget : Tenez compte à la fois du coût initial de l’outillage et du coût de production à long terme. Si les moules multi-cavités ont un coût initial plus élevé, ils peuvent permettre de réaliser des économies significatives dans le cadre d’une production en grande série. À l’inverse, les moules à cavité unique peuvent être plus économiques pour les projets à faible volume.
- Délai d’exécution : si votre projet est soumis à un délai serré, les moules multi-empreintes peuvent contribuer à accélérer la production en produisant plusieurs pièces simultanément. Toutefois, le délai plus long nécessaire à la conception et à la fabrication d’un moule multi-empreintes peut contrebalancer cet avantage.
- Exigences de qualité : Si votre projet exige le plus haut niveau de qualité et de précision, un moule à cavité unique peut être le meilleur choix, car il permet un contrôle plus méticuleux du processus de moulage.
10 questions clés pour une sélection optimale des fournisseurs
1. Quelles sont les principales différences entre les moules à cavité unique et les moules à cavités multiples ?
Les moules à cavité unique produisent une pièce par cycle, ce qui est idéal pour les prototypes ou les commandes de faible volume. Les moules multi-empreintes produisent 2-128+ pièces identiques par cycle, optimisés pour la production de masse.
2. Comment les coûts se comparent-ils entre les moules mono-empreinte et les moules multi-empreintes ?
- Moules à cavité unique : 5 000-20 000 (outillage plus simple).
- Moules à cavités multiples : 30 000-100 000+ (conceptions complexes, acier trempé).
Le coût par pièce diminue de 40 à 70 % avec les moules multi-empreintes pour les commandes de gros volumes.
3. Quand dois-je choisir un moule à simple empreinte ?
Choisissez une seule cavité pour :
- Prototypage : Tester les conceptions avant la production en série.
- Commandes de faible volume : 50 à 1 000 unités.
- Géométries complexes : La précision est de mise pour les pièces complexes.
4. Quelles sont les industries qui bénéficient le plus des moules multi-cavités ?
- Emballage : Couvercles et capsules à grand volume (par exemple, systèmes à 64 cavités).
- Électronique : Petits connecteurs, boîtiers.
- Médical : Seringues jetables, composants IV.
5. Quel est l’impact du choix du matériau de moulage sur les performances d’une cavité unique par rapport à celles d’une cavité multiple ?
- Cavité unique : Aluminium (coût moins élevé, délais plus courts).
- Multi-cavités : Acier trempé (H13, NAK80) pour la durabilité (500k+ cycles).
6. Quels sont les risques pour la qualité des moules multi-cavités ?
- Déséquilibre de la cavité : Une obturation inégale entraîne une variation dimensionnelle (±0,1 mm).
- Constance de l’usure : Les gros volumes risquent d’entraîner une dégradation inégale de l’outillage. L’analyse du flux des moules et la surveillance SPC permettent d’atténuer ce risque.
7. En quoi les temps de cycle diffèrent-ils entre les moules à cavité unique et les moules à cavité multiple ?
- Cavité unique : 30-60 secondes/cycle (varie en fonction de la taille de la pièce).
- Multi-cavités : 10-30 secondes/cycle (production simultanée de pièces).
8. Les moules multi-cavités peuvent-ils traiter différentes conceptions de pièces dans un seul outil ?
Oui. Les moules familiaux produisent plusieurs pièces uniques en un seul cycle, mais augmentent la complexité et le coût de 20 à 40 %.
9. Quelles certifications les fournisseurs doivent-ils posséder pour les moules multi-cavités ?
- ISO 9001 : Gestion de la qualité.
- IATF 16949 : pour les composants automobiles.
- Rapports d’analyse des flux de moulage : Valider l’équilibrage des cavités.
10. Comment évaluer l’expertise d’un fournisseur en matière de production de moules multi-cavités ?
- Portefeuille : Études de cas pour des moules de plus de 16 cavités.
- Précision garantie : tolérances de ±0,05 mm.
- Soutien à la maintenance : Inspections de l’outillage après la production.
Conclusion
Le choix entre les moules à cavité unique et les moules à cavités multiples implique une évaluation minutieuse de vos besoins de production, de votre budget, de votre calendrier et de vos exigences en matière de qualité. Les deux types de moules présentent des avantages uniques, et le bon choix dépend des exigences spécifiques de votre projet.
Chez BFY Mold, nous sommes spécialisés dans la fourniture de solutions de moulage par injection sur mesure pour répondre à vos exigences de production uniques. Que vous ayez besoin d’un moule à cavité unique pour des pièces de précision ou d’un moule à cavités multiples pour une production en grande quantité, notre équipe d’experts peut vous guider tout au long du processus. En mettant l’accent sur le moulage par injection et la fabrication de moules, la production de masse, la production à la demande, l’usinage CNC et l’étincelle miroir, notre usine interne garantit des résultats de haute qualité adaptés à vos spécifications. Laissez-nous vous aider à atteindre vos objectifs de production avec la bonne solution de moulage.