플라스틱 프로젝트에 있어 올바른 제조 방법을 선택하는 것은 균형과 비용 절감 모두를 위해 매우 중요합니다. 자동차 부품, 의료 기기, 소비재 모두 성능과 경제성에 직접적인 영향을 미칩니다. 사출 성형, 열성형 또는 추가 대량 생산은 이러한 선택과 직결됩니다. 이 튜토리얼에서는 재료 호환성, 생산량, 툴링 비용, 리드 타임, 산업 표준 등 5가지 종속 요소를 세분화하여 엔지니어와 설계자가 전략을 목표에 맞추는 데 도움을 줍니다. 프로토타이핑에서 대량 생산에 이르기까지, 추종자가 아닌 훌륭한 리더가 되어 비용이 많이 드는 오버런으로 인해 최적의 제조 결정을 내릴 수 있는 기회를 놓치지 마세요.

플라스틱 프로젝트 범위 및 산업 요구 사항 정의
플라스틱은 다양한 산업 분야에서 무수히 많은 용도로 사용되는 다재다능한 소재입니다. 포장재부터 자동차 부품, 소비재, 의료 기기에 이르기까지 플라스틱은 현대 제조업에서 중요한 역할을 담당하고 있습니다. 플라스틱 부품을 생산하기 위해 선택한 방법은 최종 제품의 품질, 비용 및 기능에 큰 영향을 미칠 수 있습니다. 따라서 올바른 제조 방법을 선택하는 것은 모든 플라스틱 프로젝트의 성공을 위해 필수적입니다.
플라스틱 프로젝트에 적합한 제조 방법을 선택하는 것은 품질과 비용 효율성을 보장하는 데 필수적입니다. 사출 성형과 CNC 가공을 비롯한 다양한 기술을 사용할 수 있으므로 프로젝트의 구체적인 요구 사항을 이해하는 것이 중요합니다. 이 가이드는 효율성과 정밀성을 유지하면서 플라스틱 프로젝트 결과를 최적화하기 위한 주요 고려 사항을 강조하여 의사 결정 과정을 탐색하는 데 도움이 됩니다.
플라스틱 프로젝트의 재료 호환성 및 성능 기준
올바른 제조 방법을 선택하는 첫 번째 단계는 프로젝트의 구체적인 요구 사항을 이해하는 것입니다. 여기에는 설계 복잡성, 재료 특성, 생산량, 비용 제약, 제품의 용도를 비롯한 여러 요소에 대한 자세한 분석이 포함됩니다.
설계의 복잡성과 정밀성:
일부 제조 방법은 단순한 디자인에 더 적합한 반면, 다른 제조 방법은 복잡한 형상을 높은 정밀도로 처리할 수 있습니다. 예를 들어 사출 성형은 공차가 엄격한 복잡한 부품을 생산하는 데 이상적인 반면, 회전 성형은 덜 복잡한 디테일의 크고 속이 빈 물체를 만드는 데 더 적합합니다.
머티리얼 속성:
플라스틱마다 강도, 유연성, 온도 저항성, 화학적 안정성 등 다양한 특성이 있습니다. 최종 제품이 원하는 사양을 충족하려면 선택한 제조 방법이 재료와 호환되어야 합니다. 예를 들어 열가소성 플라스틱은 일반적으로 사출 성형에 사용되는 반면, 열경화성 플라스틱은 압축 성형에 사용되는 경우가 많습니다.
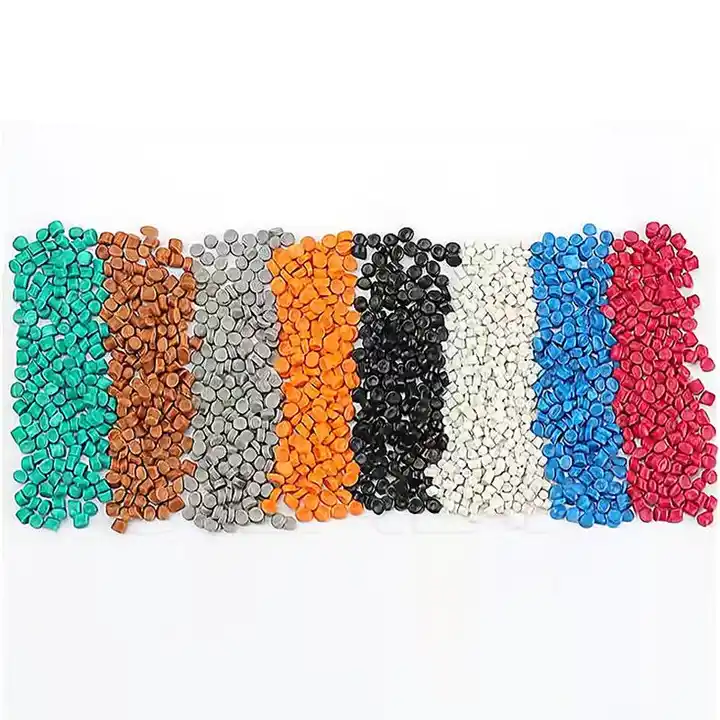
생산량:
생산 규모는 중요한 요소입니다. 일부 방법은 대규모 생산에 비용 효율적인 반면, 다른 방법은 소량 배치 또는 프로토타입 제작에 더 적합합니다. 대량 생산의 경우, 사출 성형과 블로우 성형은 효율성과 일관된 부품을 빠르게 생산할 수 있는 능력 때문에 선호됩니다. 반대로 3D 프린팅과 CNC 가공은 소량 생산 또는 맞춤형 부품에 이상적입니다.
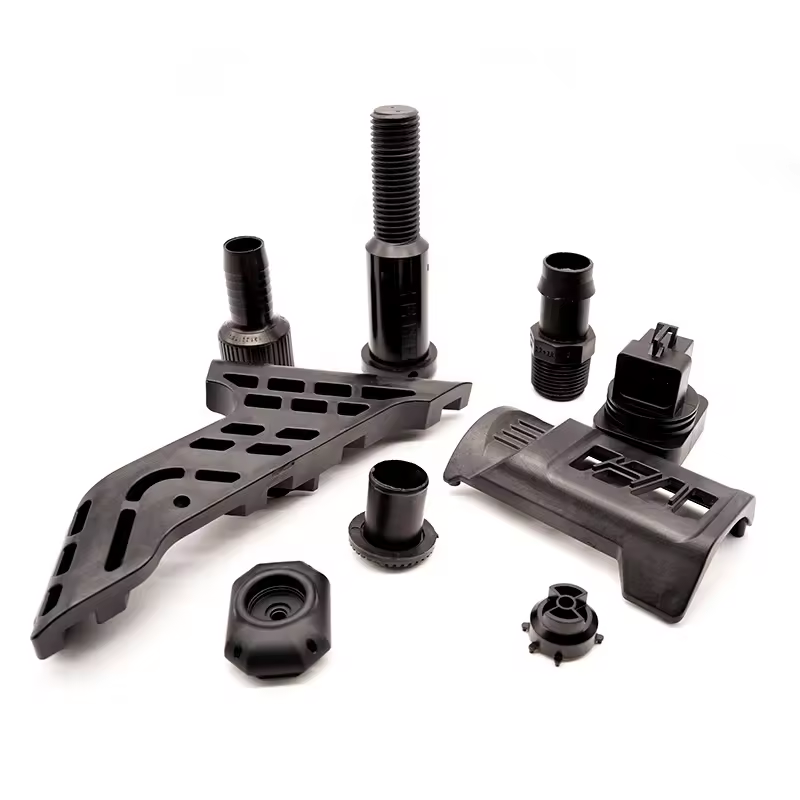
비용 고려 사항:
예산 제약은 의사 결정 과정에서 중요한 역할을 합니다. 툴링 및 장비에 대한 초기 투자는 제조 방식에 따라 다릅니다. 사출 성형은 금형에 상당한 초기 투자가 필요하므로 소량 생산에는 적합하지 않습니다. 반면 3D 프린팅은 초기 비용은 낮지만 대량 생산 시 단위당 비용이 높습니다.
애플리케이션 및 성능:
제품의 용도에 따라 필요한 성능 특성이 결정됩니다. 예를 들어 의료 기기는 높은 정밀도와 생체 적합성이 필요하며, 이는 의료용 재료를 사용한 사출 성형과 같은 특정 제조 방법을 통해 달성할 수 있습니다. 마찬가지로 자동차 부품은 내구성과 내열성이 요구되므로 제조 공정 및 재료 선택에 영향을 미칩니다.
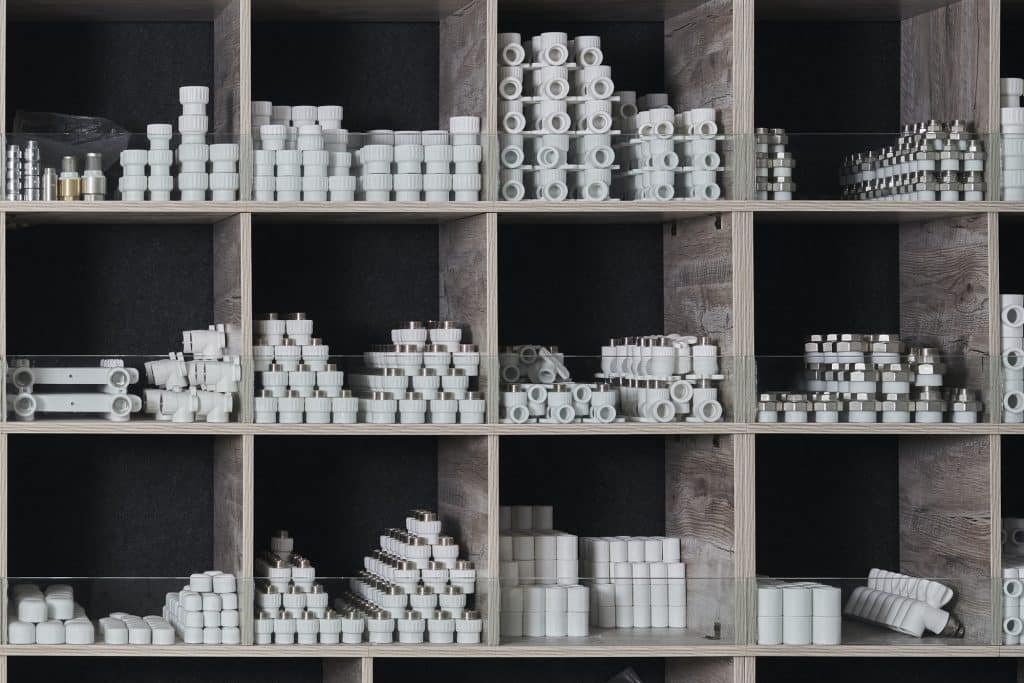
플라스틱 프로젝트의 일반적인 제조 방법
사출 성형:
이 방법은 용융된 플라스틱을 금형 캐비티에 주입하여 원하는 모양으로 냉각 및 응고시키는 방식입니다. 사출 성형은 대량 생산에 매우 효율적이며 반복성과 정밀도가 뛰어납니다. 복잡한 부품에 적합하며 열가소성 플라스틱과 열경화성 수지를 포함한 다양한 재료를 사용할 수 있습니다.
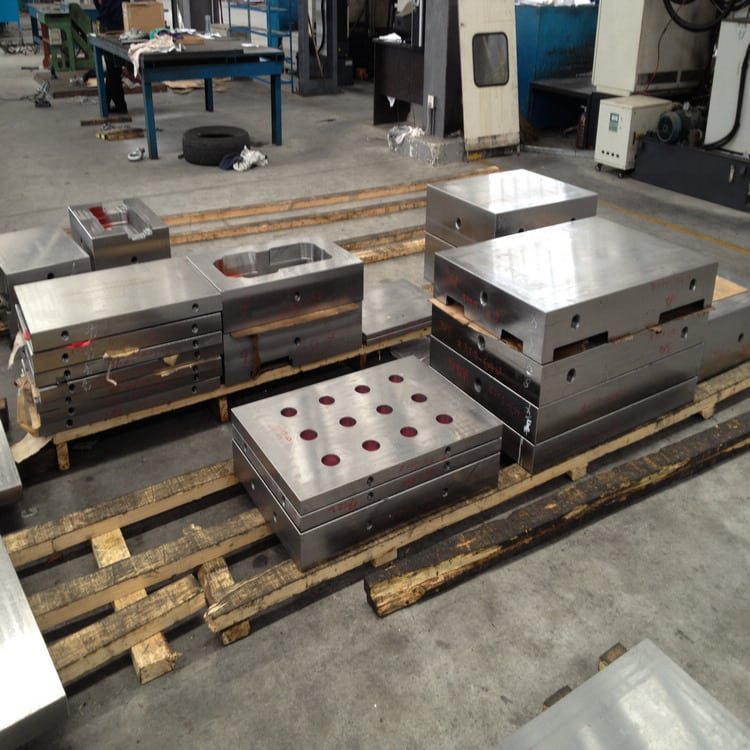
블로우 몰딩:
주로 병이나 용기와 같은 속이 빈 물체를 생산하는 데 사용되는 블로우 성형은 금형 내부에 가열된 플라스틱 패리슨을 부풀려 원하는 모양을 만드는 방식입니다. 이 방법은 벽이 얇은 균일한 부품을 대량으로 생산하는 데 이상적입니다.

회전 성형:
이 공정에서는 플라스틱 분말을 금형 안에 넣고 가열한 다음 여러 축을 따라 회전시킵니다. 플라스틱이 녹아 금형 내부를 코팅하여 냉각되면 속이 빈 부품이 만들어집니다. 회전 성형은 탱크나 놀이기구와 같이 형상이 단순하고 속이 빈 대형 제품에 적합합니다.
열성형:
열성형에는 플라스틱 시트를 유연해질 때까지 가열한 다음 금형 위에 성형하는 과정이 포함됩니다. 진공 또는 압력을 사용하여 시트가 금형의 모양에 맞게 성형됩니다. 이 방법은 비교적 단순한 디자인의 중대형 부품에 비용 효율적이며 일반적으로 포장, 트레이 및 자동차 부품에 사용됩니다.
3D 프린팅:
적층 제조라고도 하는 3D 프린팅은 디지털 모델에서 부품을 레이어별로 제작합니다. 이 방법은 매우 다재다능하며 소량 생산, 프로토타이핑 및 맞춤형 부품에 적합합니다. 복잡한 디자인과 빠른 반복이 가능하지만 대규모 생산에는 비용 효율적이지 않을 수 있습니다.

압축 성형:
압축 성형에서는 예열된 플라스틱 소재를 가열된 금형 캐비티에 넣은 다음 상단 금형으로 닫습니다. 압력이 가해지면 재료가 경화되면서 금형의 모양에 맞게 변형됩니다. 이 방법은 고강도 부품에 적합하며 일반적으로 대형, 평면 또는 곡선형 부품에 사용됩니다.
결론
플라스틱 프로젝트에 적합한 제조 방법을 선택하는 것은 프로젝트 요구 사항, 재료 특성, 생산량, 비용 제약 및 응용 분야 요구 사항을 철저히 이해해야 하는 다각적인 결정입니다. 각 제조 방법에는 고유한 장점과 한계가 있으므로 모든 요소를 신중하게 평가하는 것이 중요합니다. 설계 복잡성, 재료 호환성, 생산 규모, 예산 및 성능 기준을 고려하여 제조업체는 플라스틱 프로젝트의 성공과 효율성을 보장하는 가장 적합한 방법을 선택할 수 있습니다. 사출 성형의 정밀성, 3D 프린팅의 다양성, 열성형 성형의 비용 효율성 등 올바른 선택은 고품질, 기능성, 경제성을 갖춘 플라스틱 제품으로 이어질 것입니다.