Plastic is a versatile material used in countless applications across various industries. From packaging to automotive parts, consumer goods to medical devices, plastics play a crucial role in modern manufacturing. The method chosen to produce plastic parts can significantly affect the quality, cost, and functionality of the final product. Therefore, selecting the right manufacturing method is essential for the success of any plastic project.
Understanding the Requirements
The first step in choosing the right manufacturing method is understanding the specific requirements of the project. This involves a detailed analysis of several factors including the design complexity, material properties, production volume, cost constraints, and the intended application of the product.
Design Complexity and Precision:
Some manufacturing methods are better suited for simple designs, while others can handle complex geometries with high precision. For instance, injection molding is ideal for producing intricate parts with tight tolerances, whereas rotational molding is more suited for creating large, hollow objects with less intricate details.
Material Properties:
Different plastics have varying properties such as strength, flexibility, temperature resistance, and chemical stability. The chosen manufacturing method must be compatible with the material to ensure the final product meets the desired specifications. For example, thermoplastics are commonly used in injection molding, while thermosetting plastics are often used in compression molding.
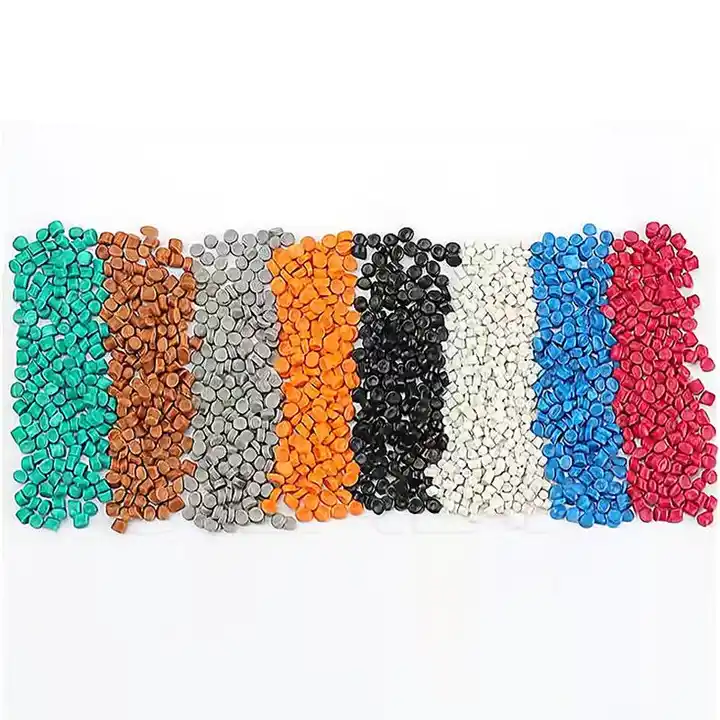
Production Volume:
The scale of production is a critical factor. Some methods are cost-effective for large-scale production, while others are more suitable for small batches or prototyping. For high-volume production, injection molding and blow molding are preferred due to their efficiency and ability to produce consistent parts quickly. Conversely, 3D printing and CNC machining are ideal for low-volume production or custom parts.
Cost Considerations:
Budget constraints play a significant role in the decision-making process. The initial investment for tooling and equipment varies across different manufacturing methods. Injection molding requires a significant upfront investment in molds, making it less suitable for low-volume production. On the other hand, 3D printing has lower initial costs but higher per-unit costs for mass production.
Application and Performance:
The intended use of the product will dictate the necessary performance characteristics. For example, medical devices require high precision and biocompatibility, which can be achieved through specific manufacturing methods like injection molding with medical-grade materials. Similarly, automotive parts require durability and heat resistance, influencing the choice of manufacturing process and materials.
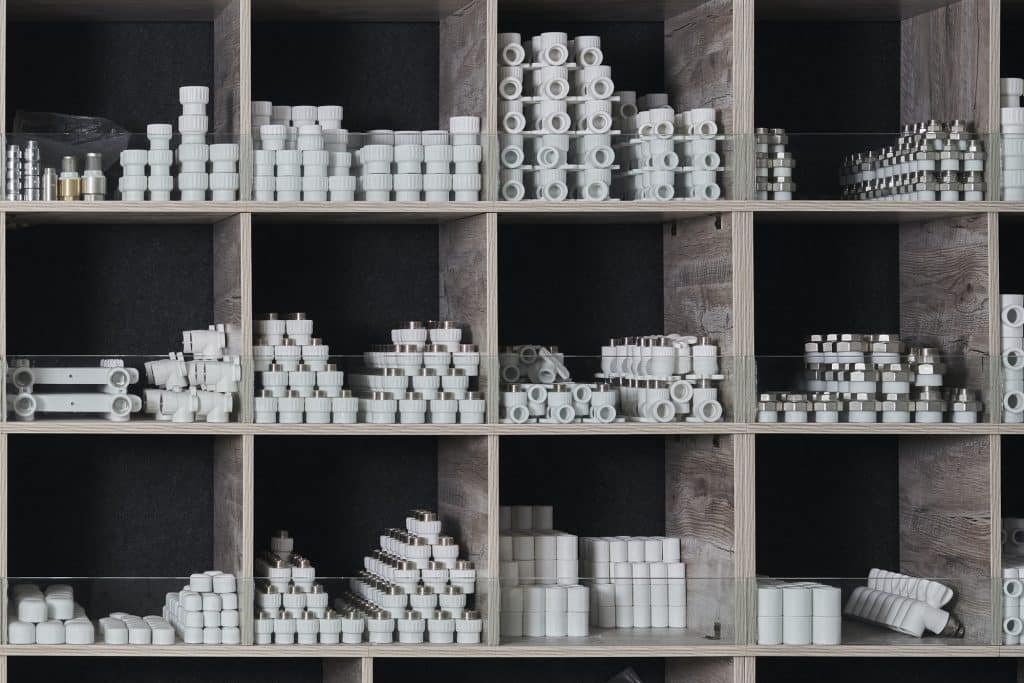
Common Manufacturing Methods
Injection Molding:
This method involves injecting molten plastic into a mold cavity, where it cools and solidifies into the desired shape. Injection molding is highly efficient for large-scale production and offers excellent repeatability and precision. It is suitable for complex parts and allows for the use of a wide range of materials, including thermoplastics and thermosets.
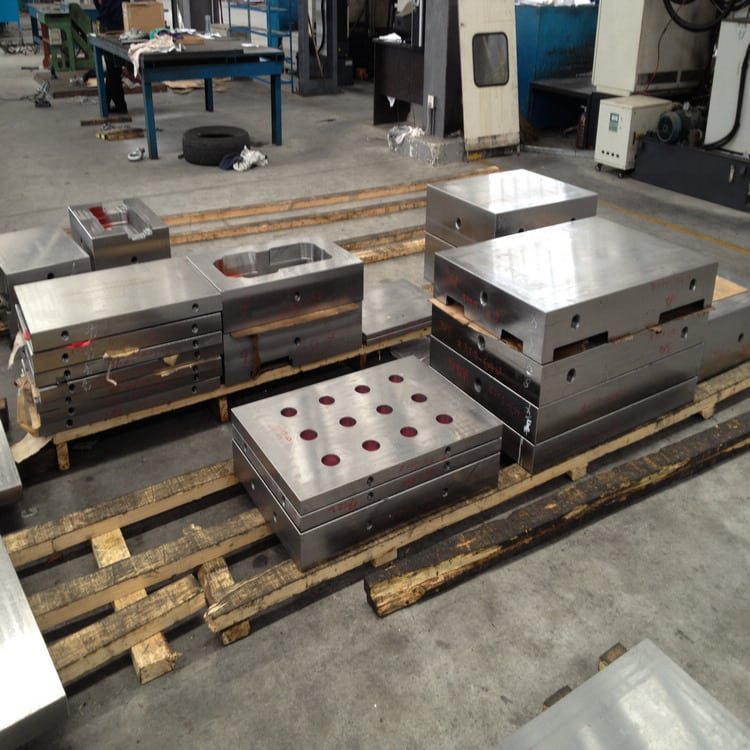
Blow Molding:
Primarily used for producing hollow objects like bottles and containers, blow molding involves inflating a heated plastic parison inside a mold to form the desired shape. This method is ideal for high-volume production of uniform parts with thin walls.

Rotational Molding:
In this process, a plastic powder is placed inside a mold, which is then heated and rotated along multiple axes. The plastic melts and coats the interior of the mold, creating a hollow part once it cools. Rotational molding is suitable for large, hollow items with simple geometries, such as tanks and playground equipment.
Thermoforming:
Thermoforming involves heating a plastic sheet until it becomes pliable, then forming it over a mold. Vacuum or pressure is used to ensure the sheet conforms to the mold’s shape. This method is cost-effective for medium to large parts with relatively simple designs, commonly used for packaging, trays, and automotive components.
3D Printing:
Also known as additive manufacturing, 3D printing builds parts layer by layer from a digital model. This method is highly versatile and suitable for low-volume production, prototyping, and custom parts. It allows for complex designs and rapid iterations, though it may not be as cost-effective for large-scale production.

Compression Molding:
In compression molding, a preheated plastic material is placed into a heated mold cavity, which is then closed with a top mold. The pressure applied forces the material to conform to the mold’s shape as it cures. This method is suitable for high-strength parts and is commonly used for large, flat, or curved parts.
Conclusion
Choosing the right manufacturing method for plastic projects is a multifaceted decision that requires a thorough understanding of the project requirements, material properties, production volume, cost constraints, and application needs. Each manufacturing method has its own set of advantages and limitations, making it crucial to evaluate all factors carefully. By considering the design complexity, material compatibility, production scale, budget, and performance criteria, manufacturers can select the most appropriate method to ensure the success and efficiency of their plastic projects. Whether it’s the precision of injection molding, the versatility of 3D printing, or the cost-effectiveness of thermoforming, the right choice will lead to high-quality, functional, and economically viable plastic products.