아크릴 사출 성형 제품은 선명하고 다양한 용도로 인기가 있지만 변형 및 기포와 같은 결함이 발생하기 쉽습니다. 제조 공정에서 최적의 결과를 얻으려면 이러한 문제를 해결하는 방법을 이해하는 것이 중요합니다. 이 기사에서는 이러한 결함을 최소화하여 고품질 사출 성형 제품을 생산할 수 있는 실용적인 솔루션과 모범 사례를 살펴봅니다.
사출 성형 공정 중에 제품의 뒤틀림과 변형이 있다고 가정해 보겠습니다. 이 경우 주로 금형 설계에서 해결해야하며 성형 조건의 조정 효과는 최소화됩니다.
사출 성형 제품의 뒤틀림 및 변형에 대한 솔루션
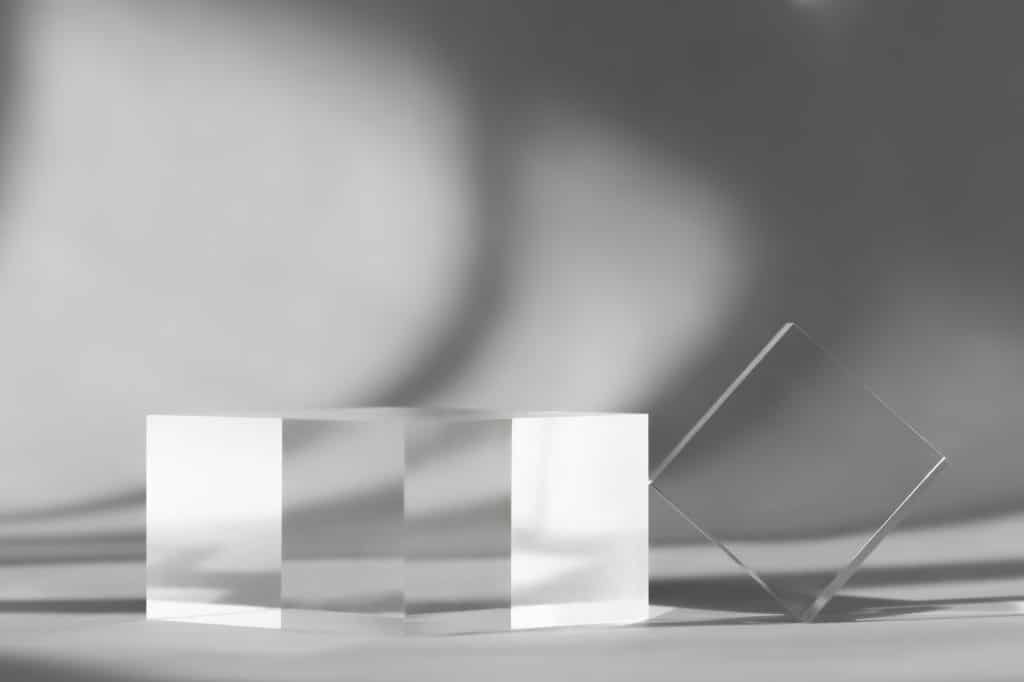
1단계: 성형 조건으로 인한 잔류 응력으로 인해 변형이 발생하는 경우 사출 압력을 낮추거나 금형을 높이고 금형 온도를 균일하게 만들거나 수지 온도를 높이거나 어닐링 방법을 사용하여 응력을 제거할 수 있습니다.
2단계: 릴리스 불량으로 인해 응력 변형이 발생하는 경우 푸시로드의 개수나 면적을 늘리고 릴리스 경사를 설정하여 해결할 수 있습니다.
3단계: 냉각 방법이 적합하지 않고 냉각 시간이 균일하지 않거나 불충분한 경우, 냉각 방법을 조정하고 냉각 시간을 연장할 수 있습니다. 예를 들어 냉각 루프를 가능한 한 변형에 가깝게 배치할 수 있습니다.
4 단계 : 성형 수축으로 인한 변형의 경우 금형 설계를 수정해야합니다. 그중 가장 중요한 것은 제품의 벽 두께를 일정하게 만드는 데주의를 기울이는 것입니다. 때로는 필요한 경우 제품의 변형을 측정하고 반대 방향으로 트리밍하여 금형을 수정해야하는 경우가 있습니다.
일반적으로 수축률이 큰 수지, 즉 결정성 수지(예: AS 폴리포름알데히드, 나일론, 폴리프로필렌, 폴리에틸렌, PET 수지 등)는 비정질 수지(예: 아크릴 수지, 폴리염화비닐, 폴리스티렌, ABS 수지 및 AS 수지 등)보다 변형이 더 큽니다. 또한 유리 섬유 강화 수지는 섬유 배향이 있기 때문에 변형도 큽니다.
버블의 원인을 해결하는 방법
제품의 벽 두께가 두꺼우면 외부 표면의 냉각 속도가 중앙보다 빠르기 때문에 냉각과 함께 중앙의 수지 쪽이 수축하고 표면으로 팽창하여 중앙이 불충분하게 채워집니다. 이 상황은 진공 기포가 형성되기 쉽습니다. 주요 해결책은 다음과 같습니다:
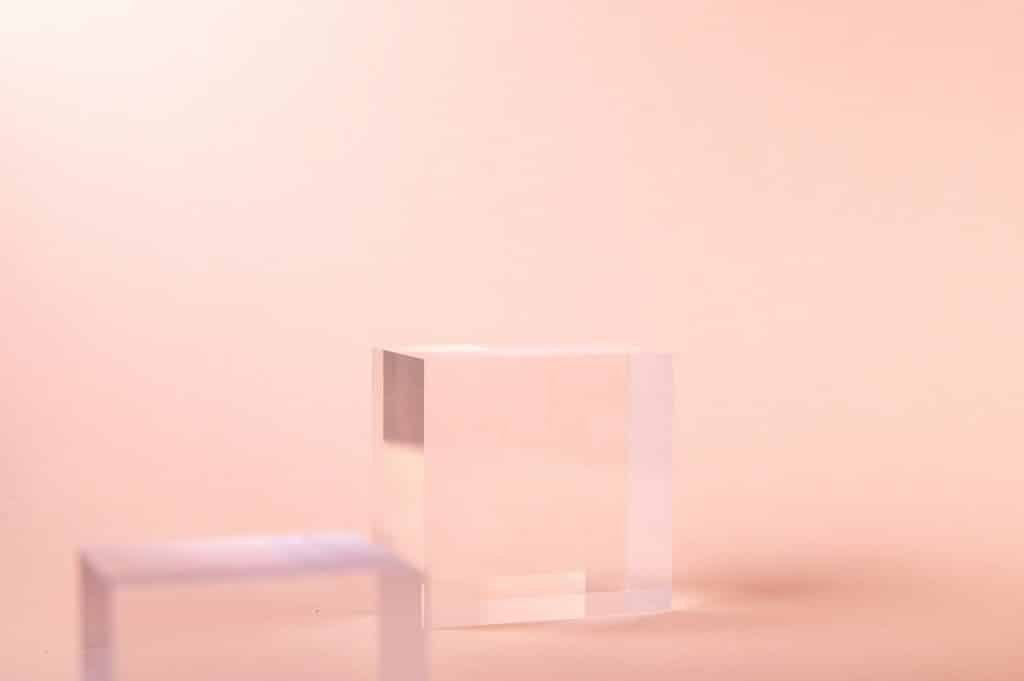
a) 벽 두께에 따라 적절한 게이트 및 러너 크기를 결정합니다. 일반적으로 게이트 높이는 제품 벽 두께의 50~60%여야 합니다.
b) 게이트가 봉인될 때까지 일정량의 보충 주입 재료가 남습니다.
c) 주입 시간은 게이트 밀봉 시간보다 약간 길어야 합니다.
d) 사출 속도를 줄이고 사출 압력을 높입니다.
e) 용융점도 등급이 높은 재료가 사용됩니다.
사출 성형 시 휘발성 기포 문제 해결
a) 완전히 건조시킵니다.
b) 분해 가스의 발생을 방지하기 위해 수지 온도를 낮춥니다.
c) 유동성 저하로 인한 기포는 수지와 금형의 온도를 높이고 사출 속도를 높임으로써 해결할 수 있습니다.