Acrylic injection molding products are popular for their clarity and versatility, but they can be prone to defects such as deformation and bubbles. Understanding how to address these issues is crucial for achieving optimal results in your manufacturing process. In this article, we’ll explore practical solutions and best practices to minimize these defects, ensuring the production of high-quality injection molding products.
Suppose there is warping and deformation of the product during the injection molding process. In that case, it should be mainly solved from the mold design, and the adjustment effect of the molding conditions is minimal.
Solutions for Warping and Deformation in Injection Molding Products
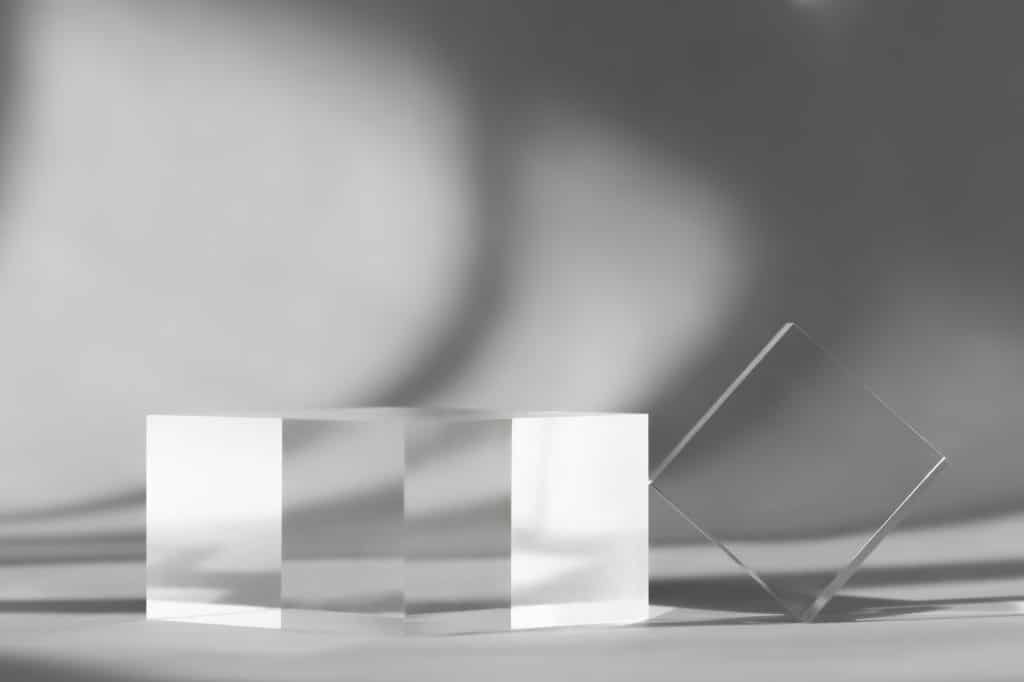
STEP 1: When residual stress caused by molding conditions causes deformation, the stress can be eliminated by reducing the injection pressure, raising the mold and making the mold temperature uniform, raising the resin temperature, or using the annealing method.
STEP 2: When the stress deformation is caused by poor release, it can be solved by increasing the number or area of the push rod and setting the release slope.
STEP 3: When the cooling method is not suitable and the cooling time is not uniform or insufficient, the cooling method can be adjusted and the cooling time can be extended. For example, a cooling loop may be placed as close to the deformation as possible.
STEP 4: For the deformation caused by the forming shrinkage, the design of the mold must be corrected. Among them, the most important thing is to pay attention to making the wall thickness of the product consistent. Sometimes, in the case of necessity, it is necessary to correct the mold by measuring the deformation of the product and trimming it in the opposite direction.
Resins with large shrinkage rates, generally crystalline resins (such AS polyformaldehyde, nylon, polypropylene, polyethylene, and PET resins, etc.) have larger deformation than amorphous resins (such as acrylic resins, polyvinyl chloride, polystyrene, ABS resins and AS resins, etc.). In addition, because the glass fiber-reinforced resin has fiber coordination, the deformation is also large.
How to Solve the Causes of Bubbles
When the wall thickness of the product is thicker, the cooling rate of the outer surface is faster than that of the center, so that with the cooling, the resin side of the center shrinks and expands to the surface, so that the center is filled insufficiently. This situation is prone to the formation of vacuum bubbles. The main solutions are:
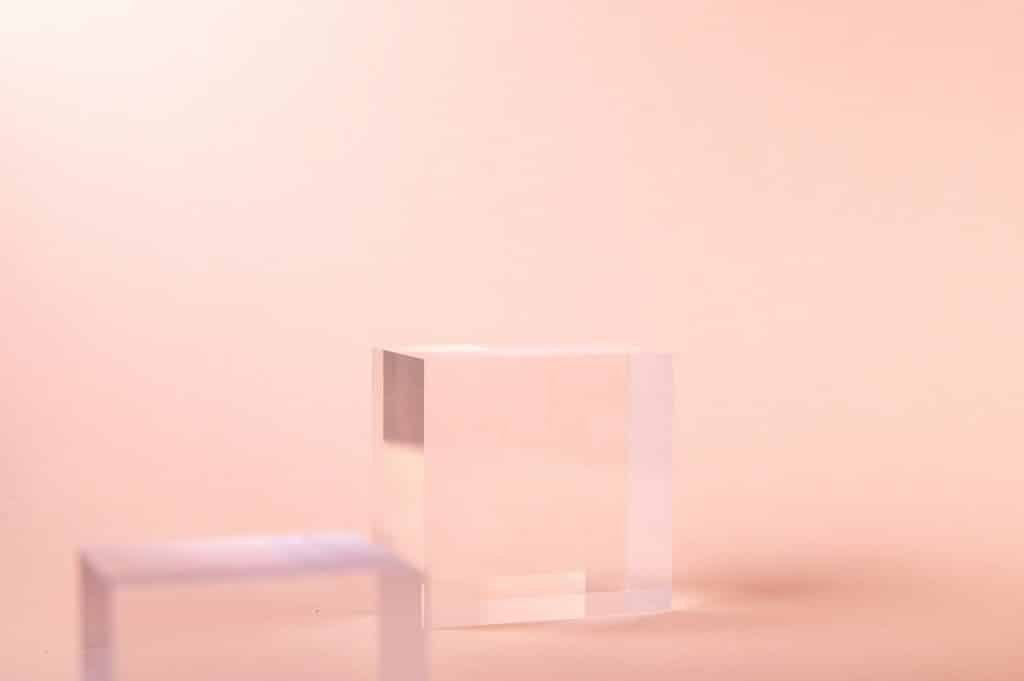
a) Determine the reasonable gate and runner size according to the wall thickness. Generally, the gate height should be 50% to 60% of the wall thickness of the product.
b) Until the gate is sealed, a certain amount of supplementary injection material is left.
c) The injection time should be slightly longer than the gate sealing time.
d) Reduce the injection speed and increase the injection pressure.
e) Materials with high melt viscosity grade are used.
Addressing Volatile Gas Bubble Issues in Injection Molding
a) Fully pre-dry.
b) Reduce the resin temperature to avoid the generation of decomposition gas.
c) The bubbles caused by poor fluidity can be solved by increasing the temperature of the resin and the mold and increasing the injection speed.