Введение
По мере сокращения жизненного цикла изделий и сокращения маржи в гиперконкурентной отрасли бытовой электроники производители сталкиваются с почти экзистенциальной задачей: обеспечить высококачественные пластиковые компоненты при все более низких затратах. Эта задача была крайне важна для ведущего новатора в области носимых медицинских технологий, поскольку существующие процессы литья под давлением истощали ресурсы, задерживали запуск и не соответствовали стандартам точности.
Сотрудничество с BFY Mold — единственный реальный прорыв, который наш клиент смог осуществить в срок, — это снижение общих производственных затрат на 40 % при одновременном ускорении вывода продукции на рынок и повышении ее надежности. В данном примере рассматриваются технические стратегии, инновации в области материалов и оптимизация цепочки поставок, которые позволили осуществить эту трансформацию, и предоставляются практические рекомендации для брендов электроники, стремящихся добиться успеха в условиях растущей чувствительности к затратам.
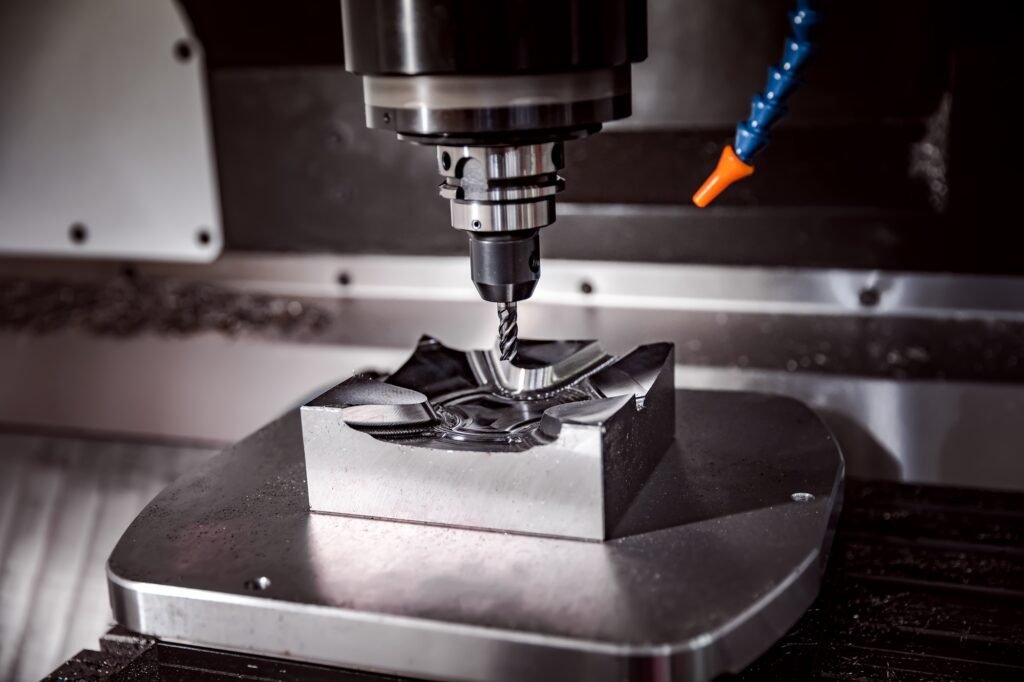
Проблема: баланс между стоимостью, скоростью и точностью
Для одного из наших клиентов, разрабатывающего смарт-часы и трекеры активности с объемом производства более 5 миллионов устройств в год, получение инструментов для обеспечения точности данных оказалось сложной задачей. Их борьба отражает общеотраслевые проблемы:
- Отходы материала: Традиционные конструкции приводили к 15-процентному избытку материала при производстве пресс-формы (в основном это были смеси ABS/PC).
- Задержки при изготовлении прототипов: 2-3 недели на корректировку пресс-форм при каждом изменении дизайна и остановке запуска продукта.
- Ограничения оффшорного поставщика: Несмотря на то, что стоимость труда у офшорных поставщиков была ниже, они не могли поддерживать требования по допуску ±0,05 мм, что приводило к нестабильному качеству.
«Нам нужен был партнер, который понимал бы как передовые инженерные разработки, так и актуальность потребительской электроники», — говорит руководитель производственного отдела компании Client. «Каждый сэкономленный доллар и каждый сэкономленный день имели значение».
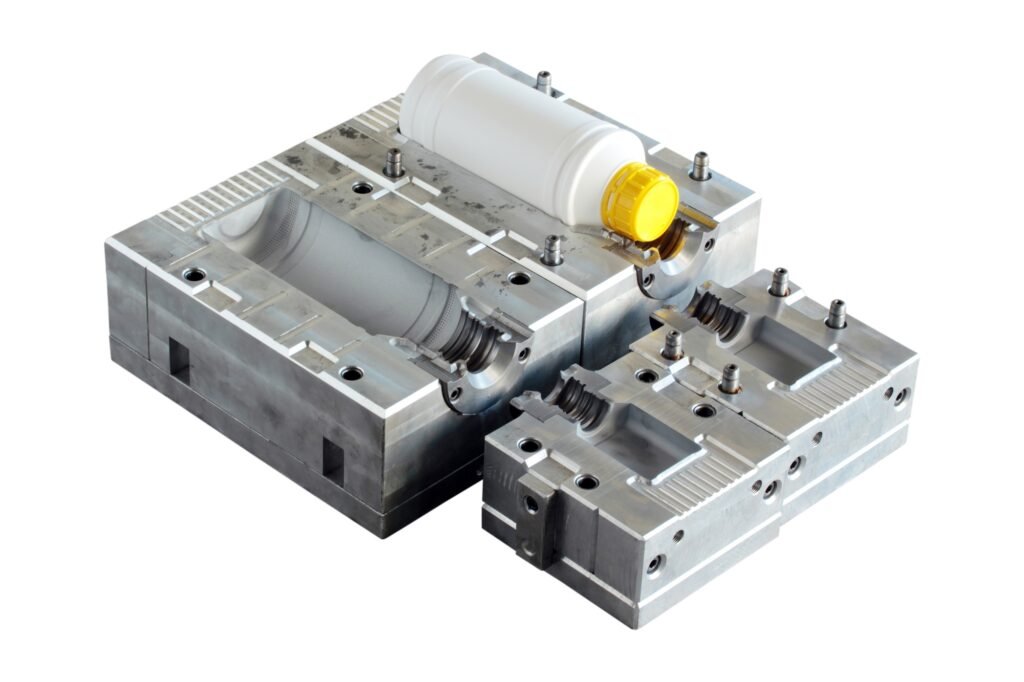
Решение: Трехсторонняя стратегия BFY Mold
1. Оптимизация проектирования пресс-форм на заказ
Проблема: Устаревшая регулировка пресс-форм методом проб и ошибок приводила к потере времени и материалов.
Инновации:
- Моделирование процесса формования: Инженеры BFY Mold использовали передовое программное обеспечение для моделирования, чтобы проанализировать течение полимера, схемы охлаждения и распределение напряжений.
- Определил оптимальное расположение ворот, что позволило сократить расход материалов на 12 %.
- Предсказанные следы раковин и риски коробления, сокращение числа пробных итераций с 5 до 2.
- Эффективность одногнездной формы: Вопреки отраслевым нормам, в которых предпочтение отдается многогнездным пресс-формам, моделирование показало, что одногнездная конструкция с ускоренным временем цикла (на 18 % быстрее) лучше подходит для потребностей клиента в малых и средних объемах производства.
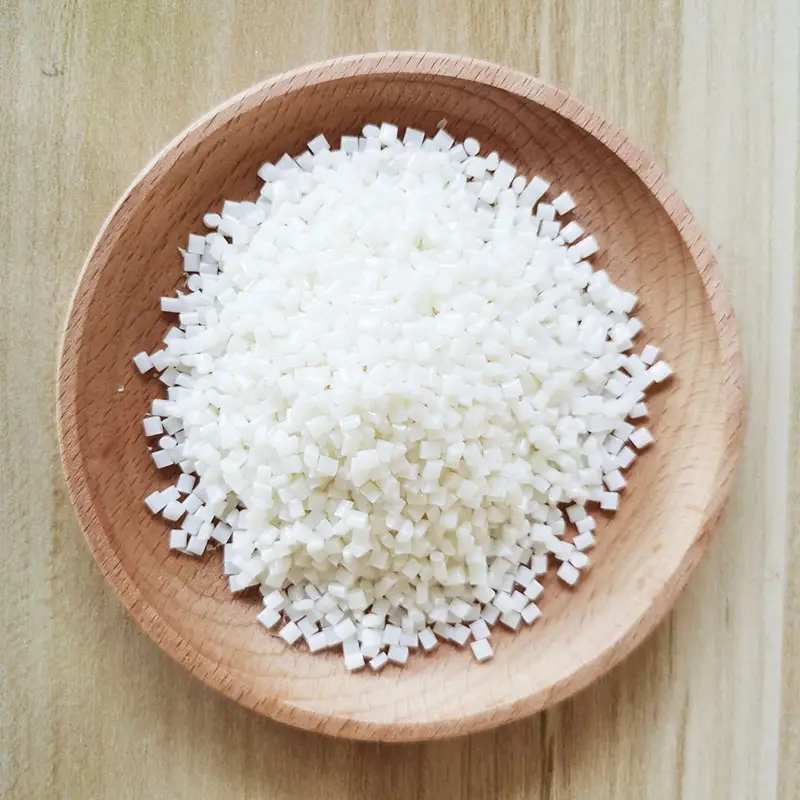
Результат:
- Экономия материалов на 12%: Снижение расхода ABS/PC на единицу продукции.
- Ускоренное на 50% создание прототипов: 48-часовые циклы моделирования заменили недели физических испытаний.
2. Производство гибридных пресс-форм: Стоимость в сравнении с долговечностью
Проблема: формы из цельной стали были долговечны, но непомерно дороги (28 000 долларов за комплект).
Инновации:
- Алюминиево-стальные композитные формы:
Алюминиевое обрамление: Снижение стоимости пресс-формы для производства на 35% (18 200 долларов за комплект).
Вставки со стальным сердечником: Сохраняют точность в течение 500 000+ циклов, что очень важно для крупносерийной электроники.
- Конформные охлаждающие каналы:
Напечатанные на 3D-принтере каналы повторяют контуры формы, повышая эффективность охлаждения на 25%.
Время охлаждения сократилось с 15 до 11 с, что позволило свести к минимуму тепловую деформацию.
Сравнительные данные:
Метрика | Традиционная форма | Гибридная пресс-форма BFY Mold |
Первоначальная стоимость | $28,000 | $18,200 |
Сокращение времени цикла | – | 18% |
Срок службы инструмента | 1M циклов | 500 000 циклов (с возможностью обновления) |
3. Локализованная цепочка поставок и поиск материалов
Проблема: Оффшорное производство вызывало логистические задержки и скрытые расходы.
Инновации:
- Замена отечественных материалов:
- Заменили импортный Sabic ST-800 ABS на модифицированную местную альтернативу, которая на 22% дешевле и сертифицирована по стандарту UL94 V-0.
- Сотрудничал с материаловедами, чтобы повысить огнестойкость носимых устройств.
- Интегрированный производственный центр:
- Создано специализированное предприятие в Шэньчжэне, Китай, где совместно размещены производство пресс-форм, литье под давлением и контроль качества.
- Сократите время изготовления с 8 до 4 недель.
«Вертикальная интеграция BFY Mold стала переломным моментом», — отметил директор по цепочке поставок бизнес-партнера. «Мы избавились от 60% логистических накладных расходов и получили возможность контролировать производство в режиме реального времени».

Ощутимые результаты: Не ограничиваясь снижением затрат
- 40% Общая экономия средств:
- Материал: 12%
- Инструментарий: 35%
- Логистика: 60%
- Ускоренный выход на рынок:
- Циклы создания прототипов сократились на 50 %, что позволило ускорить запуск продукта на 6 недель.
- Захватил праздничные продажи 2024 года, увеличив доход на 2,3 млн долларов.
- Усиленный контроль качества:
- Точность размеров: ±0,03 мм (превосходит первоначальные цели).
- Уровень брака снизился с 12 % до 2 %, что позволило свести к минимуму повторную обработку после производства.
- Стратегические партнерства:
- Статья в журнале Plastics Today привлекла внимание 3 компаний из списка Fortune 500, занимающихся производством электроники.
- Расширение сотрудничества с литьем под давлением на заказ, включая корпуса наушников TWS и датчики IoT.
Почему BFY Mold? Техническое преимущество для брендов электроники

- Собственная база данных Moldflow: Используйте 1 000+ исторических симуляций для проектов бытовой электроники.
- Двойные сертификаты: Сертификация производства по стандарту ISO 9001, обеспечивающая межотраслевое соответствие.
- Гибкие производственные модели: Поддержка малосерийных партий (1 000+ единиц) идеально подходит для итеративных технологических продуктов.
Заключение: План действий для производителей электроники
Их путешествие подчеркивает важный урок: в бытовой электронике инновации касаются не только характеристик продукта — они касаются переосмысления самого производства. Сочетая дизайн, управляемый искусственным интеллектом, гибридную оснастку и локальную гибкость, компания BFY Mold обеспечила 40%-ное снижение затрат без ущерба для качества и скорости.
Финальный CTA:
«Готовы изменить свой процесс литья под давлением?
Свяжитесь с командой инженеров BFY Mold по электронной почте, чтобы получить бесплатный аудит проекта. Давайте спроектируем ваш экономический прорыв».