Литье под давлением прозрачных изделий — например, оптических линз, корпусов медицинских приборов или потребительской упаковки — требует тщательного внимания к чистоте материала, точности процесса и целостности поверхности. Даже такие незначительные дефекты, как пузырьки, следы потеков или помутнения, могут сделать изделия непригодными для использования, поэтому каждый этап, от подготовки материала до проектирования пресс-формы, имеет решающее значение.
В этом руководстве рассматриваются семь обязательных факторов, включая передовые протоколы сушки, контроль температуры пресс-формы и методы полировки оптического класса, для обеспечения кристально чистых результатов. При производстве компонентов из ПММА или поликарбоната эти стратегии минимизируют повторные работы и соответствуют отраслевым стандартам прозрачности и долговечности.
Стандарты отделки поверхности для прозрачных изделий
Прозрачные пластики требуют строгих стандартов качества поверхности из-за их высокой светопропускной способности. Такие дефекты, как разметка, поры, обесцвечивание и плохой блеск, недопустимы. Каждый аспект процесса литья под давлением — материалы, оборудование, пресс-формы и дизайн изделий — должен отвечать строгим требованиям.

Формование прозрачных изделий: Устранение помутнения и пузырьков
Прозрачные пластмассы обычно имеют высокую температуру плавления и плохую текучесть. Чтобы обеспечить качество продукции, необходимо точно настроить такие параметры процесса, как температура бочки, давление впрыска и скорость впрыска. Это гарантирует, что пластик заполнит форму, не вызывая внутреннего напряжения, деформации или растрескивания.
Сушка материала для обеспечения целостности прозрачного полимера
Обеспечение чистоты материала
Примеси в пластике могут повлиять на прозрачность. Во время хранения, транспортировки и подачи материалы должны быть герметично закрыты, чтобы оставаться чистыми. Влага в сырье может вызвать разрушение при нагревании, поэтому необходимо тщательно высушить материал. Используйте сушильный бункер и обеспечьте фильтрацию и осушение поступающего воздуха.
Очистка оборудования для обеспечения чистоты прозрачных продуктов
Чистка ствола, винта и аксессуаров
Для предотвращения загрязнения очищайте шнек и принадлежности средством для очистки шнека перед использованием и после остановки. Если чистящее средство недоступно, можно использовать смолы PE или PS. Во время временных остановок снижайте температуру в сушилке и бочке, чтобы предотвратить разложение сырья.
Дизайн пресс-формы для глянцевых прозрачных изделий
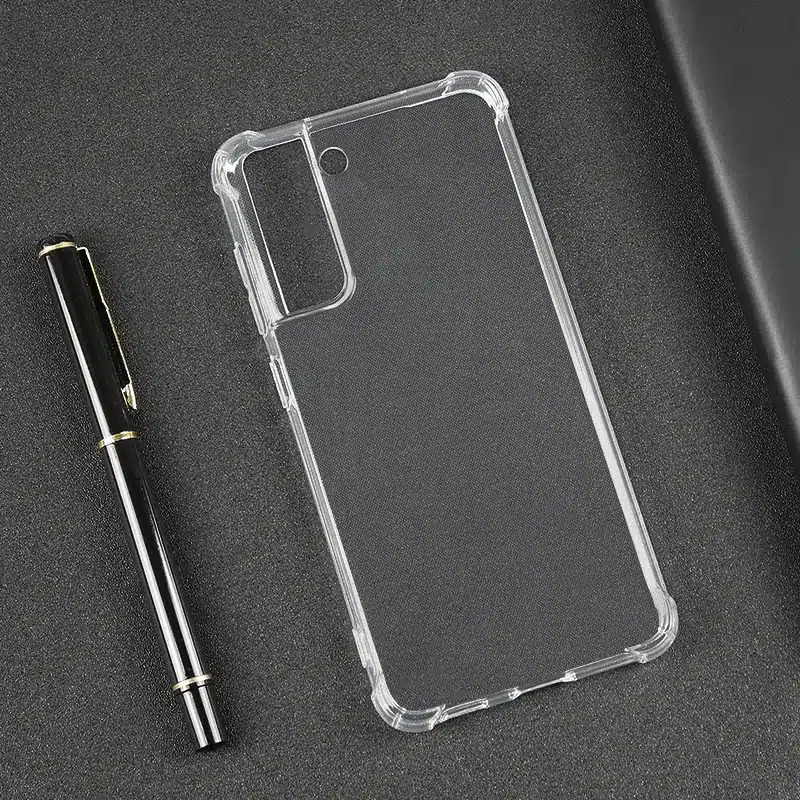
Проектирование для качества
Чтобы избежать дефектов поверхности:
1. Обеспечьте равномерную толщину стенок и достаточный уклон при распалубке.
2. Постепенно переходите от одного угла к другому, чтобы избежать острых краев.
3. При необходимости используйте широкие, короткие полозья и правильно расположенные ворота с охлаждающими колодцами.
4. Поддерживайте гладкие поверхности формы с низкой шероховатостью и достаточным количеством вентиляционных отверстий.
Поверхность и толщина стенок пресс-формы
Поверхности пресс-формы должны быть гладкими, с низкой шероховатостью (предпочтительно менее 0,8). Обеспечьте достаточную вентиляцию для отвода воздуха и газов из расплава. Избегайте слишком тонких стенок, минимальная толщина которых должна составлять 1 мм, за исключением ПЭТ.
Параметры инжекции для кристально чистых прозрачных продуктов
Оптимальные параметры инъекции
Для минимизации внутренних напряжений и дефектов поверхности:
1. Используйте специальный шнек и насадку с регулируемой температурой.
2. Используйте более высокую температуру впрыска в пределах разложения смолы.
3. Применяйте высокое давление впрыска, чтобы преодолеть вязкость расплавленного материала, но не настолько высокое, чтобы вызвать деформацию.
4. Выбирайте низкую скорость впрыска, предпочтительно используя многоступенчатый впрыск «медленный-быстрый-медленный».
5. Во избежание образования впадин и пузырей сократите время выдержки под давлением и цикл формования.
6. Используйте низкую скорость вращения шнека и противодавление для предотвращения разрушения материала.
7. Точный контроль температуры пресс-формы для оптимального охлаждения и качества продукции.
Предотвращение дефектов при формовке прозрачных изделий
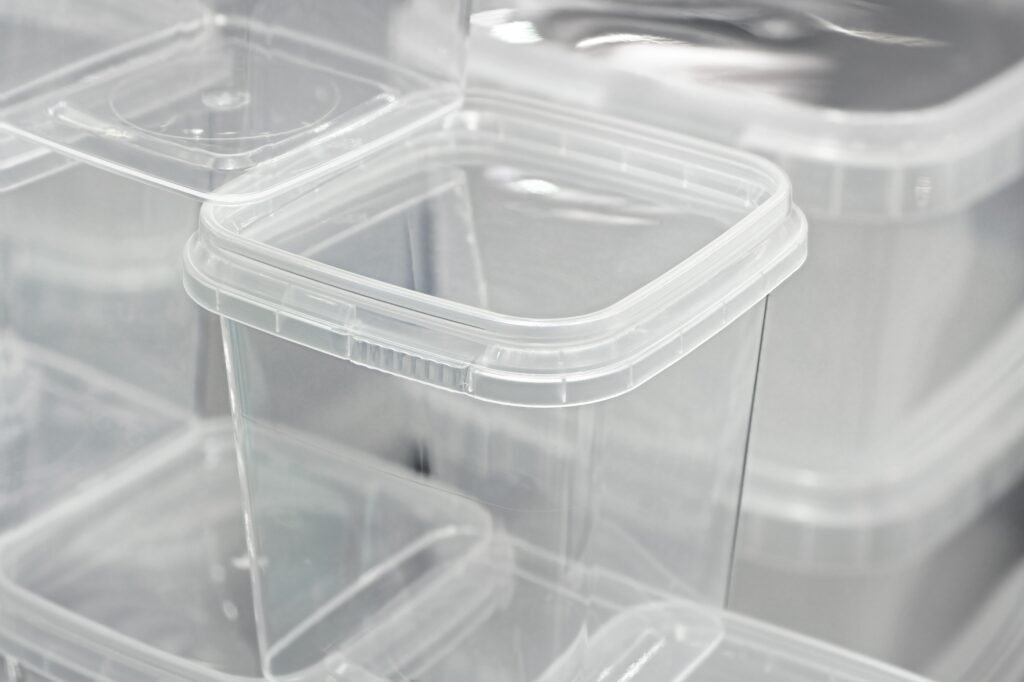
Использование разделительных агентов и переработанных материалов
Сведите к минимуму использование разделительных средств, чтобы предотвратить ухудшение качества поверхности. При использовании переработанных материалов убедитесь, что их доля не превышает 20 %.
Пост-обработка продуктов
Некоторые материалы, например ПЭТ, требуют последующей обработки для устранения внутреннего напряжения. ПММА следует сушить при температуре 70-80℃ в течение 4 часов, а ПК — нагревать при температуре 110-135℃, причем продолжительность обработки зависит от типа изделия. Для достижения хороших механических свойств ПЭТ должен подвергаться двунаправленному вытяжению.