Çoğu tıbbi ürün kalıp üreticisinin ince üretim aşamasında kullandığı yöntemler genellikle taşlama, elektrikli üretim ve fitter işlemidir. Bu aşamada, parça deformasyonu, iç gerilim, form ve pozisyon toleransı ve boyutsal doğruluk gibi birçok teknik parametrenin kontrol edilmesi gerekir, bu da belirli üretim uygulamalarında çalıştırılması daha zordur, ancak aşağıdakiler de dahil olmak üzere çeşitli etkili ampirik yöntemler vardır:

1. Medikal Sınıf Kalıp İmalatında Hassas Kontrol
Kalıp aksesuarlarının üretiminde genel bir yol gösterici fikir, farklı malzemelere, şekillere ve teknik gereksinimlere uyum sağlamaktır. Belirli bir plastisiteye sahiptir ve üretimin kontrolü sayesinde iyi üretim sonuçları elde edebilir.
2. Dayanıklı Tıbbi Kalıp Bileşenleri için Isıl İşlem
Parçaların ısıl işlem süreci, parçalar yapılırken ve farklı malzemelere farklı işlemler uygulandığında boyutların stabilitesini sağlamak için iç gerilimi kontrol ederken parçaların gerekli sertliği elde etmesini gerektirir. Son yıllarda kalıp endüstrisinin gelişmesiyle birlikte kullanılan malzeme türleri de artmıştır. Cr12, 40Cr, Cr12MoV ve semente karbürün yanı sıra, bazı yüksek çalışma mukavemetli, güçlü dışbükey, kalıp ve yeni malzeme toz alaşımlı çelikleri (V10, ASP23 vb.) de seçebilirsiniz.
V10, APS23 ve diğer toz alaşımlı çelik parçalar için, yüksek sıcaklıklara dayanabildikleri için, su verme sırasında ikincil sertleştirme işlemi kullanılır, 1050-1080 ateş, 490-520 yüksek sıcaklıkta çoklu su verme, daha yüksek darbe tokluğu ve stabilite elde edebilir.
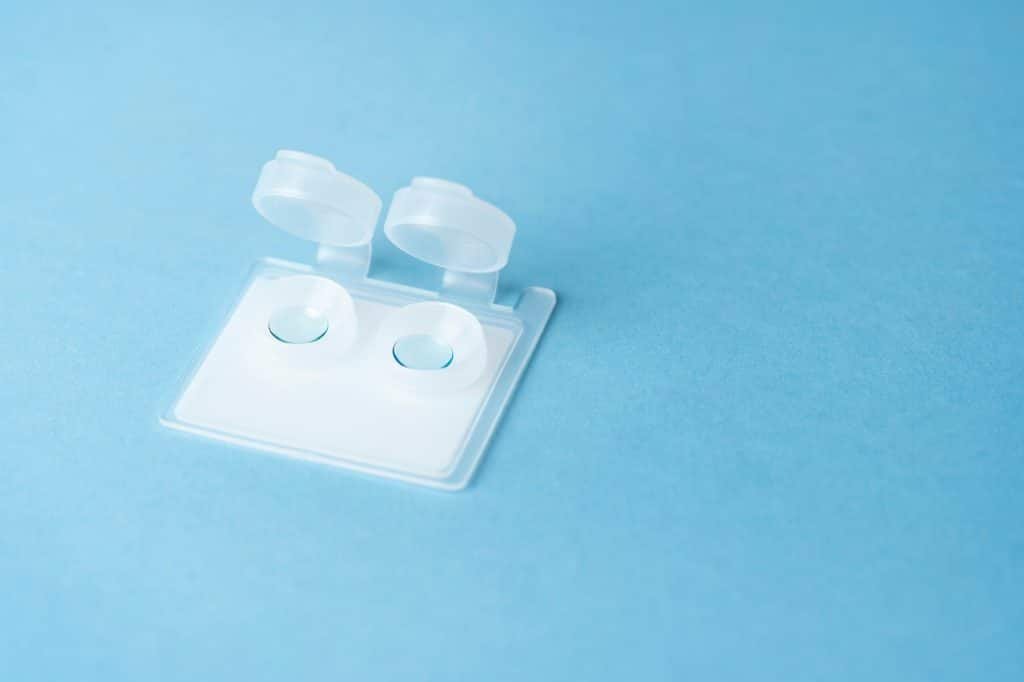
3. Tıbbi Cihaz Uyumluluğu için Kalıp Kalite Güvencesi
Tıbbi ürün kalıp üreticileri, kalıbın kalitesinin ürünün kalitesini doğrudan belirlediğine inanmaktadır. Tıbbi cihazlar alanında kalıplar da tıbbi cihaz ürünlerinin kalitesini ve verimliliğini etkilemektedir. Bununla birlikte, özellikle mikro-medikal plastikler gibi teknik alanlarda tıbbi cihaz teknik göstergelerinin iyileştirilmesiyle birlikte, yerli ekipman teknolojisi büyük ölçüde test edilmiştir. Hızla büyüyen bu tıbbi cihaz trendi karşısında, döküm kalıplamanın ana teknolojisini bununla nasıl tutarlı tutabilir ve fırsatı nasıl yakalayabiliriz?
4. Yüksek Toleranslı Kalıplar için Aşındırıcı Taşlama Teknikleri
Taşlama için üç ana tip takım tezgahı vardır: yüzey taşlama makineleri, iç taşlama makineleri ve takım taşlama makineleri. İnce taşlamada, taşlama deformasyonu ve taşlama çatlaklarının oluşumu sıkı bir şekilde kontrol edilmelidir ve küçük çatlaklar da sonraki üretime yansır. Bu nedenle, parlatma girişi küçük ve büyük olmalı, soğutma sıvısı yeterli olmalı ve 0,01 mm içinde boyut toleransları olan parçalar mümkün olduğunca belirli bir sıcaklığa kadar taşlanmalıdır.
5. Yüzey İşlemi ve Sterilite için Tıbbi Kalıpların Parlatılması
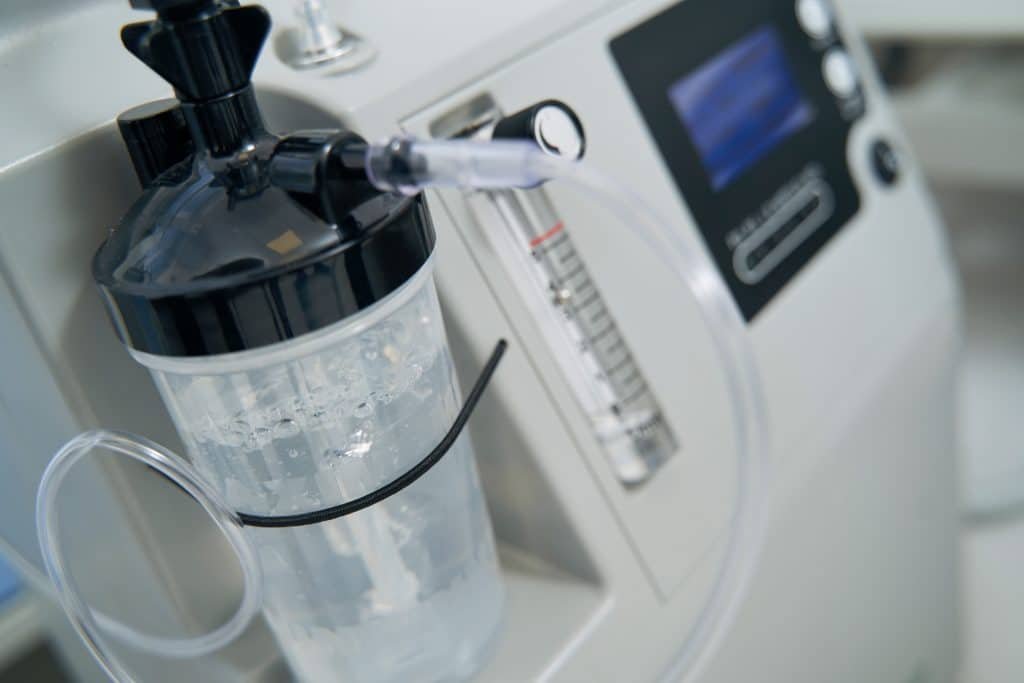
Tıbbi ürün kalıp üreticileri, parlatma sırasında doğru kum tekerleğini seçmenin çok önemli olduğuna inanmaktadır. Kalıp çeliğinin yüksek vanadyum ve yüksek molibden durumu için GD tek kristal korundum tekerleği daha uygundur. Semente karbür ve yüksek su verme sertliğine sahip malzemeler üretilirken organik bağlayıcılı elmas kum tekerleği tercih edilir. Organik bağlayıcılı kum tekerleğinin kendi kendini taşlama özelliği iyidir, taşlamadan sonra parçalar ne kadar pürüzlü olursa Ra=0,2m’dir.
Son yıllarda, yeni malzemelerin uygulanmasıyla birlikte, zımpara çarkını keskin tutmak için taşlama sırasında zımpara çarkı zamanında kesilmelidir. Kum çarkı pasifleştiğinde, bileşenin yüzeyinde kayacak ve sıkışacak, bu da bileşenin yüzeyini yakacak ve mukavemetini azaltacaktır. Plaka aksesuarlarının üretimi çoğunlukla bir düz taşlama makinesi ile yapılır ve üretim sürecinde genellikle yapımı daha zor olan uzun ve ince plaka aksesuarlarıyla karşılaşılır.
Bu nedenle, üretim sırasında, manyetik kuvvetin adsorpsiyonu nedeniyle, parçaların deformasyonu tezgah yüzeyine yakındır. Parça çıkarıldıktan sonra, parça tekrar deforme olur ve kalınlık ölçümü tutarlıdır, ancak paralellik gereksinimleri karşılamaz. Bu nedenle, çözüm doğal kesme ile taşlanabilir. Taşlama sırasında, anahat pedi parçaların altına yerleştirilir, dört taraf ayrılır ve üretim küçük bir giriş ve çok ışıklıdır.
Tıbbi ürün Kalıbı ile ilgileniyorsanız, lütfen BFY Kalıp ile iletişime geçin.