The methods used by most medical product mold manufacturers in the fine production stage are generally grinding, electrical production, and fitter treatment. At this stage, many technical parameters such as parts deformation, internal stress, form and position tolerance, and dimensional accuracy need to be controlled, which is more difficult to operate in specific production practices, but there are a variety of effective empirical methods, including:

1. Precision Control in Medical-Grade Mold Manufacturing
In the production of mold accessories, an overall guiding idea is to adapt to different materials, shapes, and technical requirements. It has a certain plasticity and can achieve good production results through the control of the production.
2. Heat Treatment for Durable Medical Mold Components
The heat treatment process of the parts requires the parts to obtain the required hardness while controlling the internal stress to ensure the stability of the dimensions when the parts are made and different materials are treated differently. In recent years, with the development of the mold industry, the types of materials used have increased. In addition to Cr12, 40Cr, Cr12MoV, and cemented carbide, you can also choose some high working strength, strong convex, die, and new material powder alloy steel (such as V10, ASP23, etc.).
For V10, APS23, and other powder alloy steel parts, because they can withstand high temperatures, the secondary hardening process is used during quenching, 1050-1080 fire, 490-520 high-temperature multiple quenching, can obtain higher impact toughness and stability.
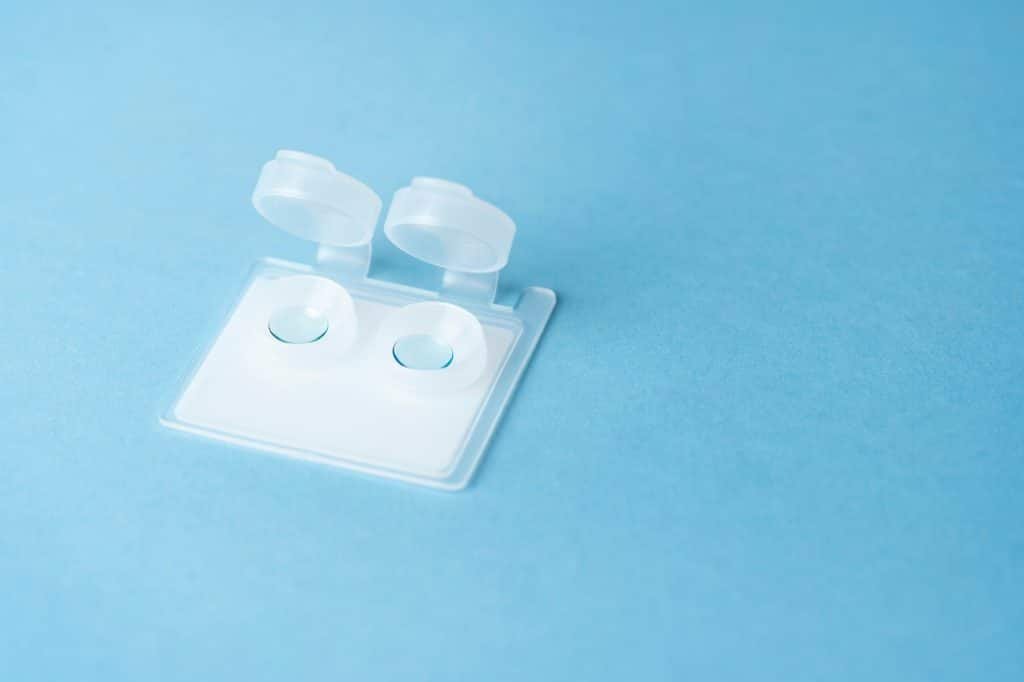
3. Mold Quality Assurance for Medical Device Compliance
Medical product mold manufacturers believe that the quality of the mold directly determines the quality of the product. In the field of medical devices, molds also affect the quality and productivity of medical device products. However, with the improvement of medical device technical indicators, especially in technical fields such as micro-medical plastics, domestic equipment technology has been greatly tested. In the face of this rapidly growing trend of medical devices, how to keep the main technology of casting molding consistent with it and seize the opportunity?
4. Abrasive Grinding Techniques for High-Tolerance Molds
There are three main types of machine tools for grinding: surface grinding machines, internal grinding machines, and tool grinding machines. In fine grinding, the occurrence of grinding deformation and grinding cracks should be strictly controlled, and small cracks are also reflected in the subsequent production. Therefore, the polishing inlet should be small and large, the coolant should be sufficient, and the parts with dimensional tolerances within 0.01 mm should be ground to a certain temperature as far as possible.
5. Polishing Medical Molds for Surface Finish & Sterility
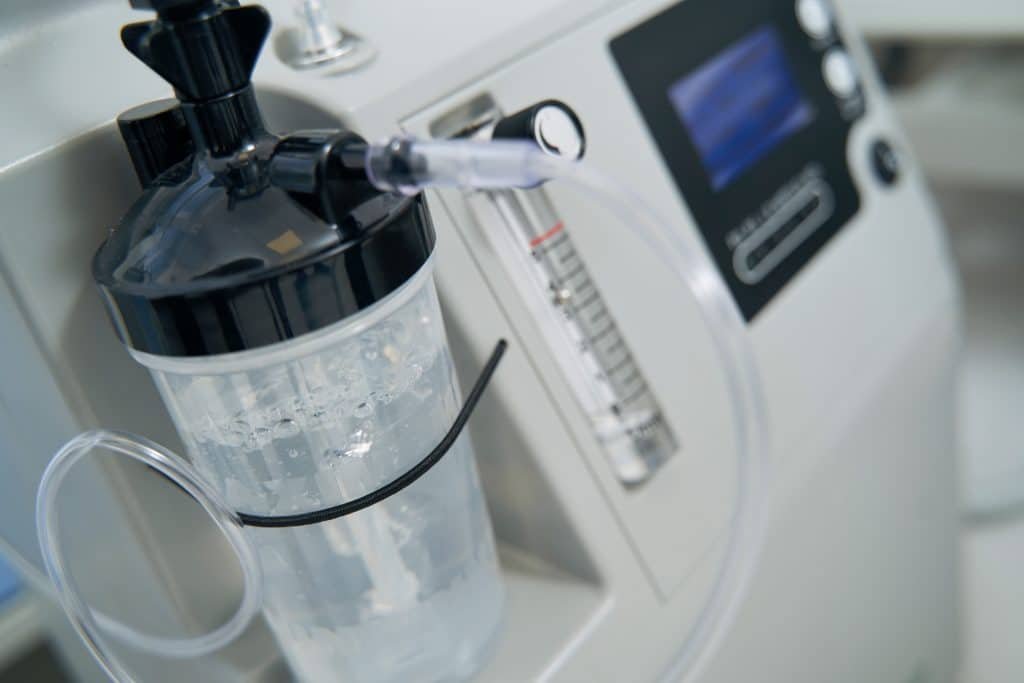
Medical product mold manufacturers believe that it is very important to choose the right sand wheel when polishing. For the high vanadium and high molybdenum state of die steel, the GD single crystal corundum wheel is more suitable. The diamond sand wheel with an organic binder is preferred when making cemented carbide and materials with high quenching hardness. The self-grinding property of the organic binder sand wheel is good, the rougher the parts after grinding, Ra=0.2m.
In recent years, with the application of new materials, the sand wheel should be trimmed in time during grinding to keep the sand wheel sharp. When the sand wheel is passivated, it will slide and squeeze on the surface of the component, which will burn the surface of the component and reduce its strength. The production of plate accessories is mostly made with a plane grinder, and long and thin plate accessories are often encountered in the production process, which is more difficult to make.
Therefore, during production, due to the adsorption of magnetic force, the deformation of the parts is close to the surface of the workbench. After the part is removed, the part is deformed again, and the thickness measurement is consistent, but the parallelism does not meet the requirements. Therefore, the solution can be ground by natural cutting. When grinding, the outline pad is laid under the parts, the four sides are separated, and the production is a small entrance and multi-light.
If you are interested in medical product Mold, please contact BFY Mold.