Akrilik enjeksiyon kalıplama ürünleri netlikleri ve çok yönlülükleriyle popülerdir, ancak deformasyon ve kabarcıklar gibi kusurlara eğilimli olabilirler. Bu sorunların nasıl ele alınacağını anlamak, üretim sürecinizde optimum sonuçlar elde etmek için çok önemlidir. Bu makalede, bu kusurları en aza indirmek ve yüksek kaliteli enjeksiyon kalıplama ürünlerinin üretilmesini sağlamak için pratik çözümleri ve en iyi uygulamaları inceleyeceğiz.
Enjeksiyon kalıplama işlemi sırasında üründe eğrilme ve deformasyon olduğunu varsayalım. Bu durumda, esas olarak kalıp tasarımından çözülmelidir ve kalıplama koşullarının ayarlama etkisi minimumdur.
Enjeksiyon Kalıplama Ürünlerinde Çarpılma ve Deformasyon için Çözümler
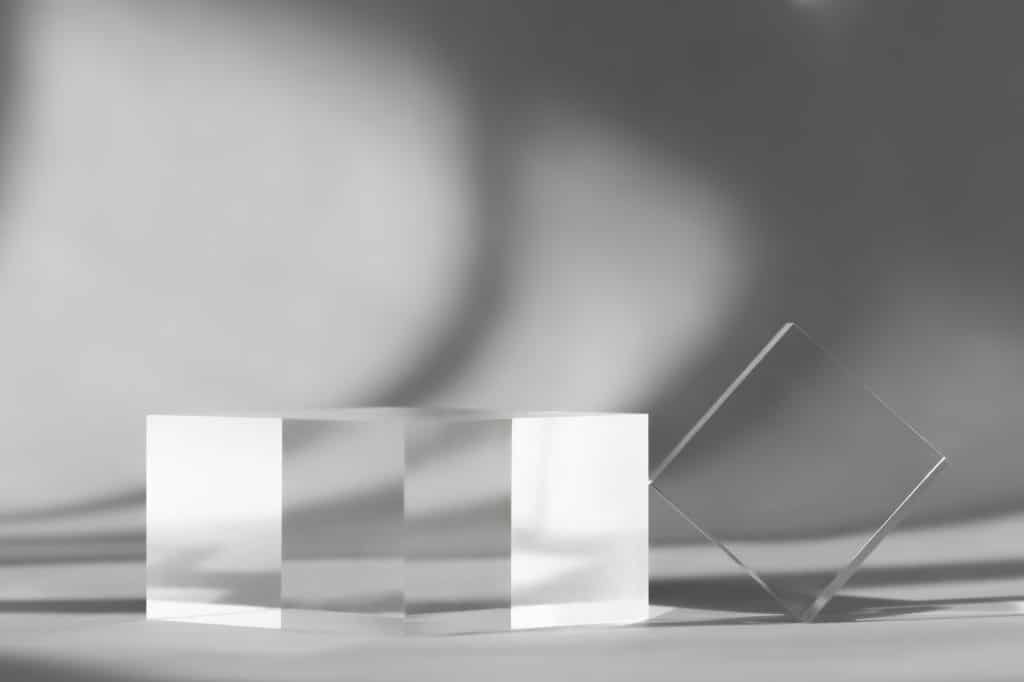
ADIM 1: Kalıplama koşullarının neden olduğu artık stres deformasyona neden olduğunda, stres enjeksiyon basıncını düşürerek, kalıbı yükselterek ve kalıp sıcaklığını tekdüze hale getirerek, reçine sıcaklığını yükselterek veya tavlama yöntemini kullanarak ortadan kaldırılabilir.
ADIM 2: Gerilim deformasyonu zayıf serbest bırakmadan kaynaklandığında, itme çubuğunun sayısını veya alanını artırarak ve serbest bırakma eğimini ayarlayarak çözülebilir.
ADIM 3: Soğutma yöntemi uygun olmadığında ve soğutma süresi eşit olmadığında veya yetersiz olduğunda, soğutma yöntemi ayarlanabilir ve soğutma süresi uzatılabilir. Örneğin, deformasyona mümkün olduğunca yakın bir soğutma döngüsü yerleştirilebilir.
ADIM 4: Şekillendirme büzülmesinin neden olduğu deformasyon için kalıbın tasarımı düzeltilmelidir. Bunlar arasında en önemlisi ürünün et kalınlığının tutarlı olmasına dikkat etmektir. Bazen zorunluluk durumunda ürünün deformasyonunu ölçüp ters yönde kırparak kalıbı düzeltmek gerekir.
Büyük büzülme oranlarına sahip reçineler, genellikle kristal reçineler (poliformaldehit, naylon, polipropilen, polietilen ve PET reçineleri gibi) amorf reçinelerden (akrilik reçineler, polivinil klorür, polistiren, ABS reçineleri ve AS reçineleri gibi) daha büyük deformasyona sahiptir. Ayrıca, cam elyaf takviyeli reçinede elyaf koordinasyonu olduğu için deformasyon da büyüktür.
Baloncukların Nedenleri Nasıl Çözülür?
Ürünün duvar kalınlığı daha kalın olduğunda, dış yüzeyin soğuma hızı merkezinkinden daha hızlıdır, böylece soğutma ile merkezin reçine tarafı büzülür ve yüzeye doğru genişler, böylece merkez yetersiz doldurulur. Bu durum vakum kabarcıklarının oluşmasına neden olur. Ana çözümler şunlardır:
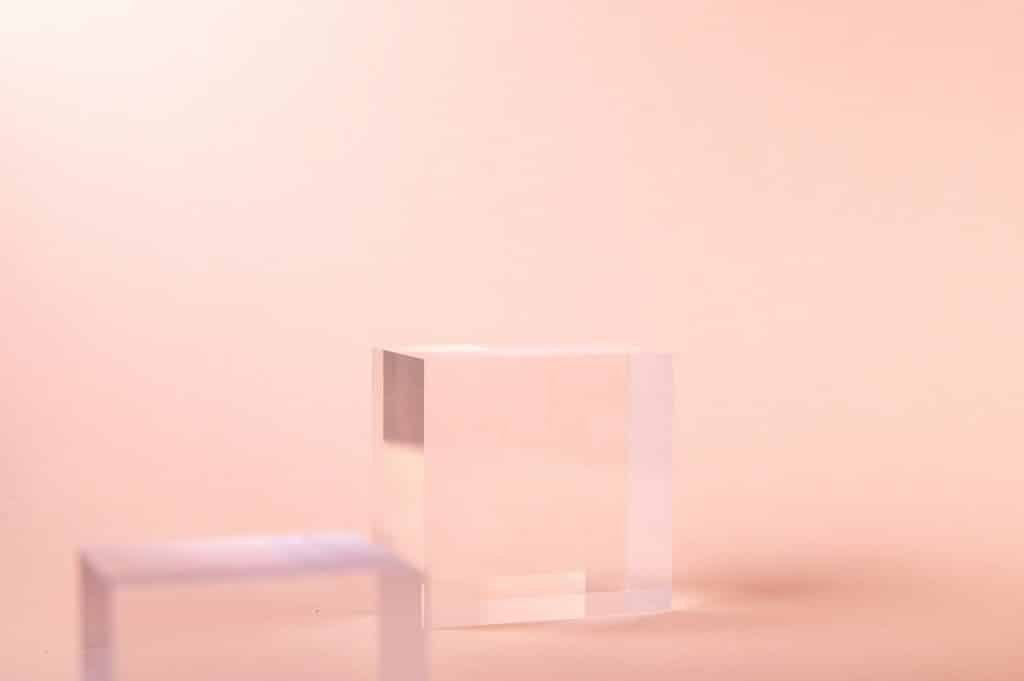
a) Duvar kalınlığına göre makul kapı ve yolluk boyutunu belirleyin. Genel olarak, kapı yüksekliği ürünün duvar kalınlığının %50 ila %60’ı arasında olmalıdır.
b) Kapı kapatılana kadar, belirli bir miktar ek enjeksiyon malzemesi bırakılır.
c) Enjeksiyon süresi, kapı mühürleme süresinden biraz daha uzun olmalıdır.
d) Enjeksiyon hızını düşürün ve enjeksiyon basıncını arttırın.
e) Yüksek eriyik viskozite derecesine sahip malzemeler kullanılır.
Enjeksiyon Kalıplamada Uçucu Gaz Kabarcığı Sorunlarının Ele Alınması
a) Tamamen ön kurutma.
b) Ayrışma gazı oluşumunu önlemek için reçine sıcaklığını düşürün.
c) Zayıf akışkanlığın neden olduğu kabarcıklar, reçine ve kalıp sıcaklığının artırılması ve enjeksiyon hızının artırılmasıyla çözülebilir.