Spritzgießen ist ein weit verbreitetes Herstellungsverfahren, das die Massenproduktion von Kunststoffteilen mit hoher Präzision und Effizienz ermöglicht. Ob bei der Herstellung komplexer Geometrien oder bei der Produktion großer Mengen identischer Teile – das Spritzgießen ist in vielen Branchen unverzichtbar, z. B. in der Automobil-, Konsumgüter-, Elektronik- und Medizintechnik. Im Folgenden werden wir die wichtigsten Schritte des Spritzgießprozesses erläutern: Schließen, Einspritzen, Kühlen und Auswerfen, wobei die Feinheiten und die Bedeutung jeder Phase hervorgehoben werden.
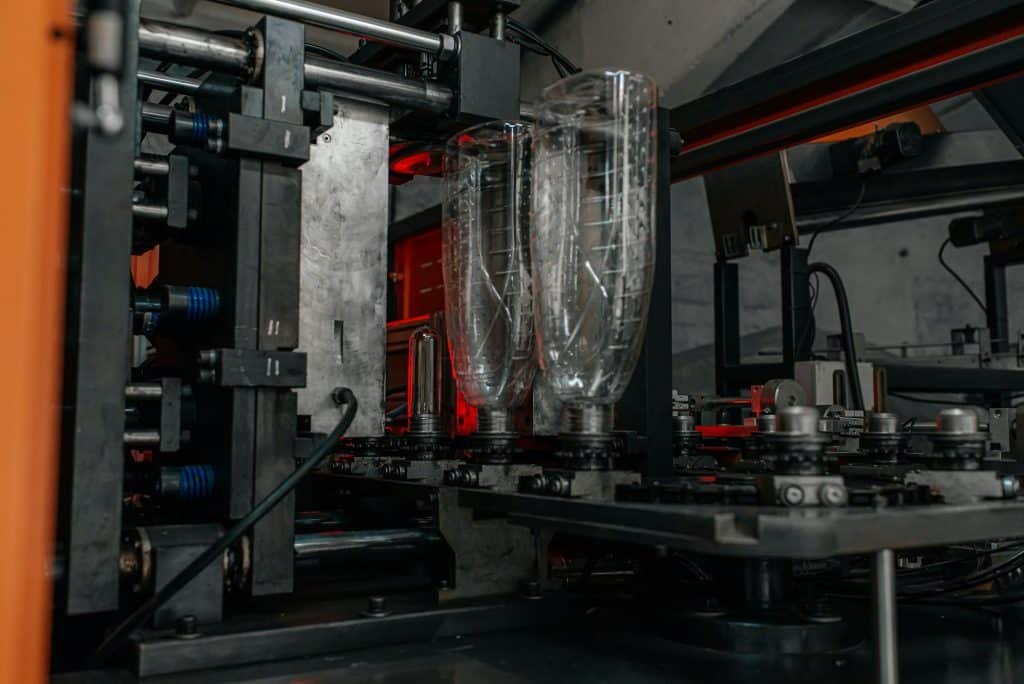
1. Einspannen: Vorbereitung der Form
Der Spritzgießprozess beginnt mit dem Schließen, das für die Fixierung der Form unerlässlich ist. Die Form besteht aus zwei Hälften: der Kavität und dem Kern. Diese Hälften müssen genau ausgerichtet und unter erheblichem Druck zusammengehalten werden, um sicherzustellen, dass der geschmolzene Kunststoff ordnungsgemäß im Formhohlraum enthalten ist.
Die Schließeinheit, ein wesentlicher Bestandteil der Spritzgießmaschine, ist für diese Aufgabe zuständig. Sie besteht aus einer feststehenden Aufspannplatte (an der die eine Hälfte des Werkzeugs befestigt ist) und einer beweglichen Aufspannplatte (die die andere Hälfte hält). Die Schließeinheit übt Kraft aus, um die Form zu schließen und sie während der Einspritz- und Abkühlphase geschlossen zu halten.
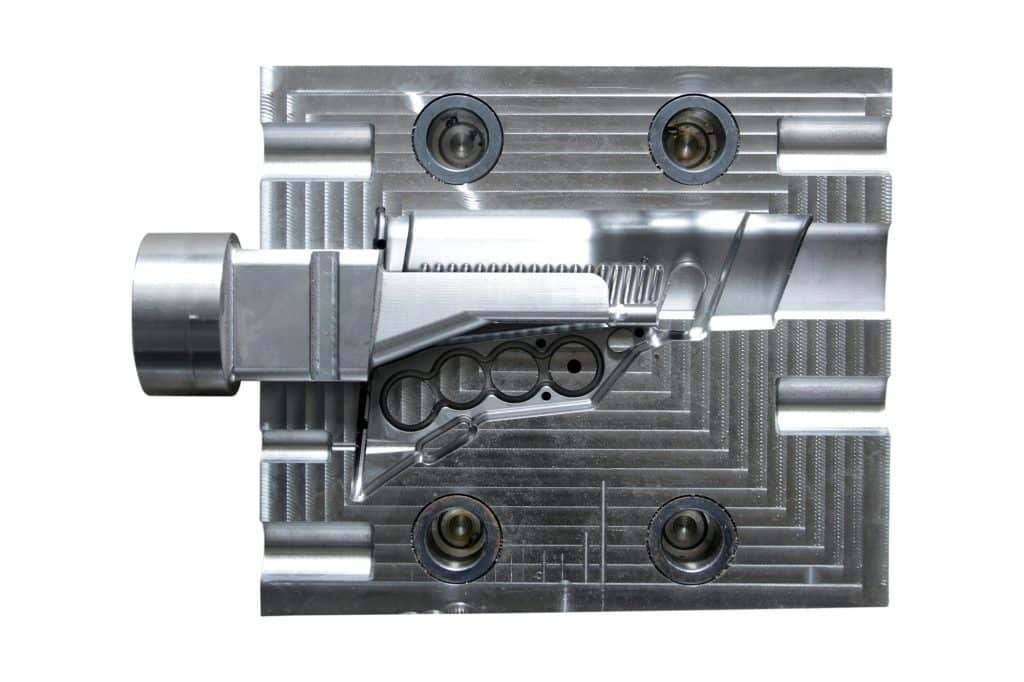
Das richtige Klemmen ist aus mehreren Gründen wichtig:
- Verhinderung von Leckagen: Sicherstellen, dass der geschmolzene Kunststoff während des Einspritzens nicht aus dem Formhohlraum austritt.
- Beibehaltung der Ausrichtung: Halten Sie die Formhälften perfekt ausgerichtet, um Teile mit genauen Abmessungen zu produzieren.
- Druckfestigkeit: Halten Sie die Form fest, um dem hohen Druck standzuhalten, der von der Spritzeinheit ausgeübt wird.
Die erforderliche Schließkraft hängt von der Größe und Komplexität des Teils sowie vom verwendeten Material ab. Eine korrekte Kalibrierung der Schließeinheit gewährleistet eine effiziente und fehlerfreie Produktion.
2. Injektion: Füllen der Form
Sobald die Form sicher eingespannt ist, beginnt die Einspritzphase. In diesem Schritt wird das Kunststoffgranulat geschmolzen und der geschmolzene Kunststoff in den Formhohlraum gespritzt. Und so funktioniert’s:
- Schmelzen des Kunststoffs: Das Kunststoffgranulat wird in den Zylinder der Spritzgießmaschine eingefüllt, wo es durch elektrische Heizelemente erhitzt wird, bis es einen geschmolzenen Zustand erreicht. Die Temperatur muss sorgfältig kontrolliert werden, um sicherzustellen, dass der Kunststoff richtig geschmolzen wird, ohne sich zu zersetzen.
- Einspritzen: Eine sich hin- und herbewegende Schnecke oder ein Kolben im Inneren des Zylinders drückt den geschmolzenen Kunststoff durch eine Düse in den Formhohlraum. Dieser Vorgang muss schnell und mit hoher Präzision erfolgen, um sicherzustellen, dass der Formhohlraum gefüllt ist, bevor der Kunststoff abkühlt und sich verfestigt.
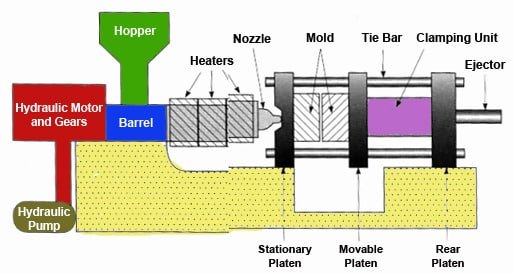
Zu den wichtigsten Überlegungen während der Injektionsphase gehören:
- Einspritzgeschwindigkeit und -druck: Diese Parameter müssen optimiert werden, um sicherzustellen, dass der Formhohlraum gleichmäßig gefüllt wird und keine Defekte wie Luftblasen oder unvollständige Füllung auftreten.
- Materialfluss: Die Fließeigenschaften des geschmolzenen Kunststoffs müssen kontrolliert werden, um Probleme wie Bindenähte, Verzug und Einfallstellen zu vermeiden.
3. Abkühlen: Erstarren des Teils
Nachdem der Formhohlraum mit geschmolzenem Kunststoff gefüllt ist, beginnt die Abkühlphase. Die Abkühlung ist entscheidend, da sie den Kunststoff verfestigt und die endgültigen Eigenschaften des Formteils bestimmt.
- Wärmeübertragung: Die Wärme aus der Kunststoffschmelze wird an die Form übertragen, die in der Regel mit einem Wasser- oder Kühlmittelsystem gekühlt wird, das durch Kanäle in der Form zirkuliert. Eine effiziente Wärmeübertragung ist wichtig, um die Zykluszeiten zu minimieren und eine gleichbleibende Teilequalität zu gewährleisten.
- Abkühlzeit: Die für die Abkühlung benötigte Zeit hängt von verschiedenen Faktoren ab, darunter die Art des Kunststoffs, die Dicke des Teils und die Kühleffizienz der Form. Eine unzureichende Kühlzeit kann zu Defekten wie Verformungen führen, während eine zu lange Kühlzeit die Produktionseffizienz verringern kann.
Die richtige Kühlung stellt sicher, dass das Teil korrekt erstarrt, seine vorgesehene Form beibehält und ohne Verformungen zum Auswerfen bereit ist.
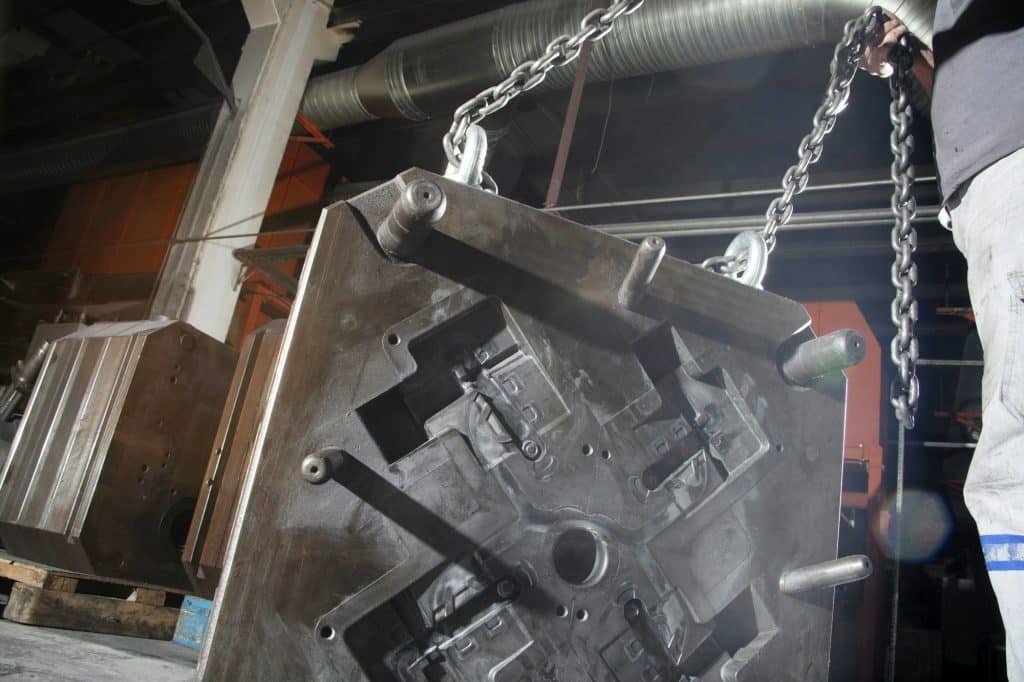
4. Auswerfen: Freigeben des Teils
Der letzte Schritt im Spritzgießprozess ist das Auswerfen. Sobald das Teil abgekühlt und erstarrt ist, muss es vorsichtig aus der Form entnommen werden, um Schäden zu vermeiden.
- Öffnen der Form: Die Schließeinheit löst ihren Halt und die Formhälften werden getrennt.
- Auswerfersystem: Auswerferstifte, -platten oder Luftstöße werden verwendet, um das Teil aus dem Formhohlraum zu drücken. Die Konstruktion des Auswerfersystems muss sorgfältig durchdacht sein, um einen reibungslosen und beschädigungsfreien Ausstoß zu gewährleisten.
- Handhabung: Das neu geformte Teil wird abgeholt, geprüft und zur nächsten Produktionsstufe gebracht, z. B. zur Nachbearbeitung, Montage oder Verpackung.
Ein effektiver Auswurf ist entscheidend für die Erhaltung der Qualität des Teils und die Vorbereitung der Form für den nächsten Spritzzyklus.
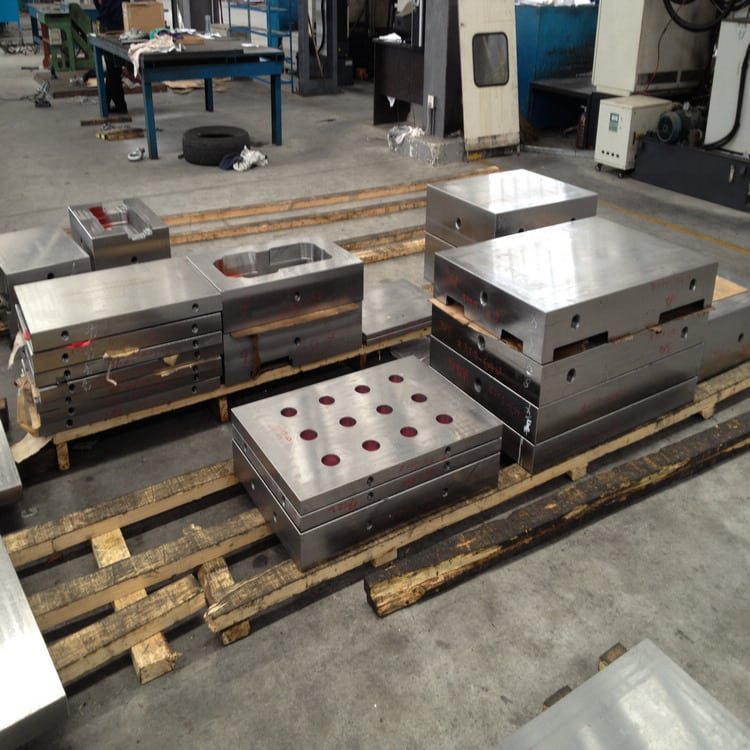
Zusammenfassung
Das Verständnis der einzelnen Schritte des Spritzgießprozesses – Einspannen, Einspritzen, Kühlen und Auswerfen – macht die Präzision und Komplexität deutlich, die mit der Herstellung hochwertiger Kunststoffteile verbunden sind. Jede Phase erfordert akribische Aufmerksamkeit für Details und Optimierung, um Effizienz, Genauigkeit und Konsistenz in der Fertigung zu gewährleisten.
BFY Mold hat sich auf erstklassige Dienstleistungen im Bereich Spritzguss und Formenbau spezialisiert. Unser hochmodernes Werk ist für die Massenproduktion, die Produktion auf Abruf, die CNC-Bearbeitung, das Spiegeln und vieles mehr ausgestattet. Mit unserem Engagement für Qualität und Innovation sind wir bestrebt, erstklassige Produkte zu liefern, die genau Ihren Spezifikationen entsprechen.

Kontaktieren Sie uns noch heute, um mehr über unsere Dienstleistungen zu erfahren und darüber, wie wir Sie bei Ihrem nächsten Projekt unterstützen können.