Acrylnitril-Butadien-Styrol (ABS) ist ein Eckpfeiler der modernen Fertigung und bekannt für seine unübertroffene Ausgewogenheit von Festigkeit, Haltbarkeit und Verarbeitbarkeit. Seit seiner Kommerzialisierung in den 1950er Jahren hat ABS die Branchen von der Automobilindustrie bis zur Unterhaltungselektronik revolutioniert und bietet eine leichte und dennoch robuste Alternative zu Metallen und anderen Kunststoffen. Dieser Artikel bietet eine umfassende Analyse des ABS-Kunststoffs, unterstützt durch Vergleichsgrafiken und Einblicke in die Gesetzgebung, um kritische Fragen über seine Sicherheit, Umweltauswirkungen und Anwendungen auf dem US-Markt zu beantworten.
1. Was ist ABS-Kunststoff?
ABS ist ein thermoplastisches Polymer, das aus drei Monomeren hergestellt wird:
- Acrylnitril (15-35%): Verbessert die chemische/thermische Stabilität.
- Butadien (5-30%): Eine gummiartige Phase für Schlagzähigkeit
- Styrol (40-60%): Sorgt für Steifigkeit und eine glänzende Oberfläche.
Darüber hinaus ermöglicht die Konstruktion von ABS eine hervorragende Oberflächenbeschaffenheit und Verschleißfestigkeit, so dass die Produkte nicht nur langlebig sind, sondern auch gut aussehen. Dank der Ausgewogenheit seiner Moleküle kann es extremen Verarbeitungstechniken wie Spritzguss und Extrusion unterzogen werden, ohne dass es zu einem Verlust seiner Eigenschaften kommt.

Wichtige Eigenschaften:
Eigentum | Wertebereich | Relevanz der Anwendung |
Zugfestigkeit | 29–45 MPa | Strukturelle Komponenten |
Schlagzähigkeit | 200–400 J/m | Stoßstangen für Autos, Spielzeug |
Schmelzpunkt | 105–125°C | Hitzebeständige Gehäuse |
Dichte | 1.04–1.06 g/cm³ | Leichte Konsumgüter |
2. Der Herstellungsprozess von ABS
Die Herstellung von ABS erfolgt durch Emulsionspolymerisation:
- Monomer-Mischung: Acrylnitril, Butadien und Styrol werden kombiniert.
- Reaktion: Polymerisiert bei 50-150°C mit Initiatoren (z.B. Peroxiden).
- Compoundierung: Zusatzstoffe (UV-Stabilisatoren, Flammschutzmittel) werden gemischt.
- Pelletieren: Extrudiert und zu Pellets geschnitten.
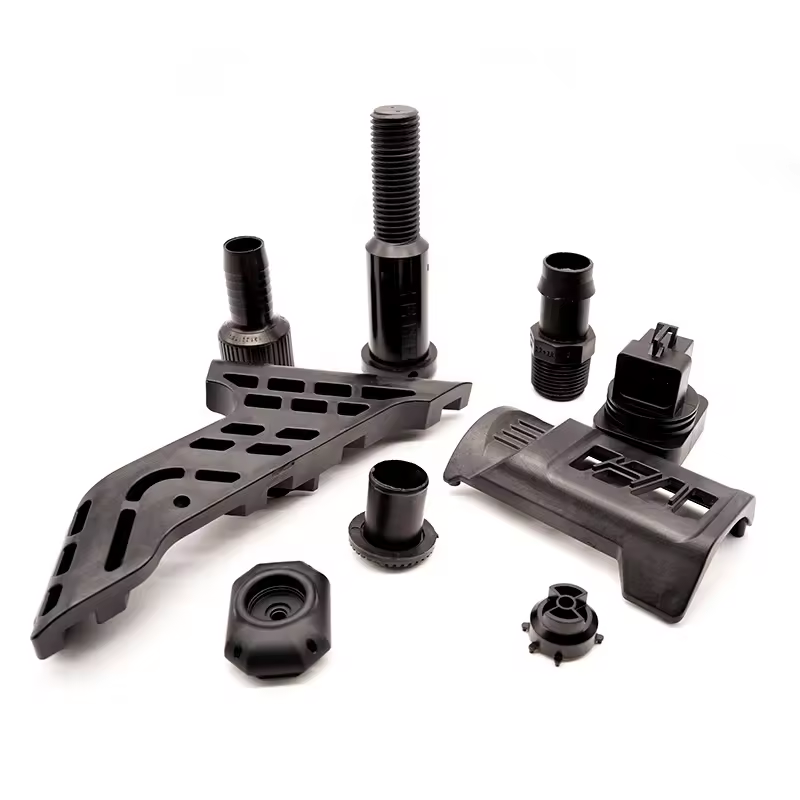
Energieverbrauch:
- ABS: 85–100 MJ/kg
- Polypropylen (PP): 70-85 MJ/kg
- Polycarbonat (PC): 110-130 MJ/kg
3. Ist ABS-Kunststoff sicher?
Die Sicherheit ist ein entscheidender Aspekt bei allen Materialien, die in Produkten für den Verbraucher verwendet werden. ABS-Kunststoff gilt aufgrund seiner chemischen Inertheit und Stabilität unter normalen Gebrauchsbedingungen als sicher. Umfangreiche Forschungsarbeiten und behördliche Bewertungen haben bestätigt, dass ABS im täglichen Gebrauch keine schädlichen Stoffe abgibt. Daher eignet es sich besonders für Produkte, die in engem Kontakt mit dem Menschen stehen – von Automobilkomponenten und Elektronikgehäusen bis hin zu Spielzeug und Küchengeräten.
ABS ist FDA-konform für Anwendungen mit Lebensmittelkontakt und von der CPSC als ungiftig für Spielzeug zertifiziert.

Sicherheitsfaktoren:
- Kein BPA/Phthalate: Im Gegensatz zu PVC werden bei ABS keine endokrin wirksamen Zusatzstoffe verwendet.
- Thermische Stabilität: Minimale Ausgasung unter 80°C.
- Auslaugungstests: <0,1 ppm Styrolmigration (FDA-Grenzwert: 0,5 ppm).
Fallstudie: Ein US-amerikanischer Spielzeughersteller reduzierte Rückrufe um 60 %, nachdem er von PVC auf ABS umgestellt hatte.
4. Gemeinsame Anwendungen für ABS
ABS-Kunststoff ist auch ein weit verbreitetes Material für das Spritzgießen aufgrund seiner ausgezeichneten Eigenschaften wie Schlagzähigkeit, Haltbarkeit und einfache Verarbeitung. Deshalb wird es von der Automobil- bis zur Unterhaltungselektronikindustrie häufig verwendet. ABS wird zum Beispiel häufig im Automobilsektor verwendet, wo Armaturenbrettformteile und Innenverkleidungsteile hohen Stoßbelastungen und niedrigen Temperaturen standhalten müssen, ohne ihre Form oder Integrität zu verlieren. Im Bereich der Unterhaltungselektronik wird ABS häufig zur Herstellung von Druckergehäusen, Fernbedienungen und Gehäusen für Elektrowerkzeuge verwendet, bei denen eine glatte Oberfläche und eine präzise Formgebung von größter Bedeutung sind. Dank dieser Qualität eignet sich ABS-Kunststoff auch für die Spielzeugindustrie, wo die Herstellung ungiftiger, langlebiger Produkte von größter Bedeutung ist. Dies zeigt sich bei Produkten wie Actionfiguren und Bausteinen.

Industrie | Anwendungsfall | Nutzen Sie |
Automobilindustrie | Armaturenbrett | Schlagfestigkeit, UV-Stabilität |
Elektronik | Tasten der Tastatur | Steifigkeit, ästhetische Ausführung |
Medizinische | Gehäuse der Geräte | Sterilisierbarkeit (autoklavierbar) |
Spielzeug | LEGO-Steine | Ungiftig, farbecht |
5. ABS vs. andere Materialien
Am stärksten konkurriert ABS-Kunststoff mit anderen handelsüblichen Polymermaterialien wie Polycarbonat (PC), Polypropylen (PP) und Polyethylen (PE). Diese Materialien haben einzigartige Stärken, aber ABS ist eher ein Mittelding. Während Polycarbonat eine bessere Klarheit und Schlagfestigkeit aufweist, ist es in der Regel teurer und weniger widerstandsfähig gegen Kratzer auf der Oberfläche, zum Beispiel. Polypropylen und Polyethylen sind zwar chemikalienbeständig und flexibel, haben aber nicht die Steifigkeit und die ästhetischen Vorteile von ABS.
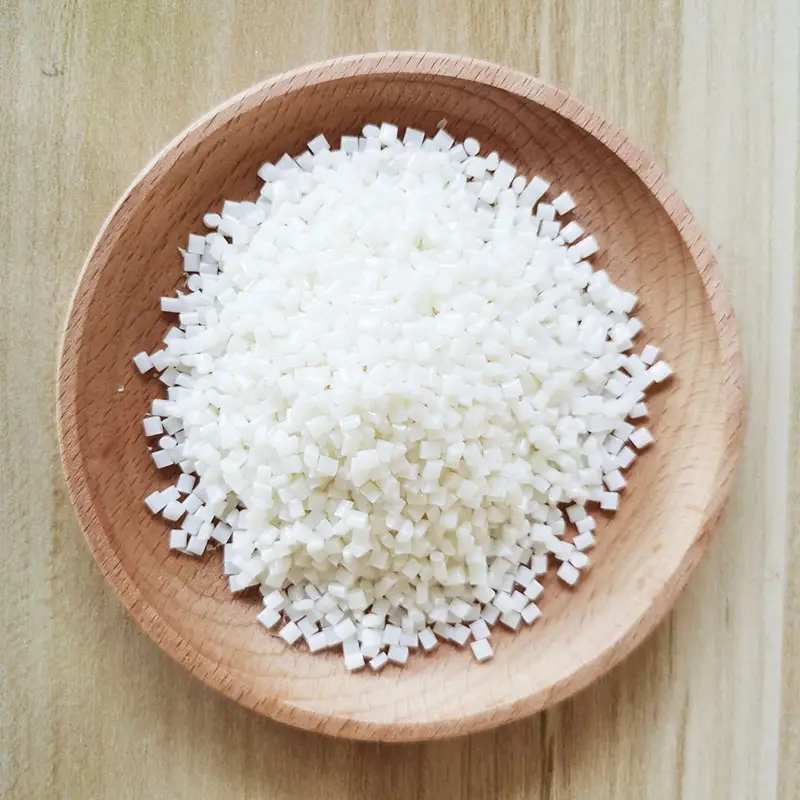
Eigentum | ABS | PC | PP |
Schlagfestigkeit | Hoch | Sehr hoch | Niedrig |
Kosten ($/kg) | 2.5–3.5 | 4.5–6.0 | 1.8–2.5 |
Recyclability | Mäßig | Niedrig | Hoch |
UV-Beständigkeit | Messe | Ausgezeichnet | Schlecht |
6. Umweltauswirkungen von ABS
- Recycling-Rate: 18-22% in den USA (im Vergleich zu 30% für PET).
- Herausforderungen: Begrenzte Kreislaufsysteme; 65 % der ABS landen auf Mülldeponien.
Innovationen:
- Chemisches Recycling: Zerlegung von ABS in Monomere (70 % Ausbeute).
- Bio-ABS: 30% pflanzlicher Anteil (z.B. Terluran® ECO).
7. Einhaltung von Vorschriften in den USA
- FDA: Food Contact Substance Notification (FCN) für Küchengeräte.
- CPSC: ASTM F963-17 Zertifizierung für Spielzeug.
- UL 94: Entflammbarkeitsklasse V-0 für Elektronik.
8. Kosten von ABS-Kunststoff beim Spritzgießen
Was die Kosten betrifft, so ist ABS-Kunststoff im Vergleich zu anderen Hochleistungsthermoplasten eine kostengünstige Materialoption, die für die Massenproduktion attraktiv ist. Je nach Sorte und Marktbedingungen kostet ABS-Kunststoff in der Regel zwischen $1,50 und $3,00 pro Pfund. Wie bei anderen Thermoplasten hängen die Kosten für das Spritzgießen mit ABS von Faktoren wie der Komplexität des Formdesigns, den Zykluszeiten und dem Produktionsvolumen ab.
So können beispielsweise bei einer Großserie von einfachen Gehäusen für Konsumgüter durch Skaleneffekte niedrige Stückkosten erzielt werden, wohingegen gut detaillierte kundenspezifische Teile, die komplexe Werkzeuge und anfängliche Formkosten erfordern, hierher gehören. Um Kosteneffizienz zu erreichen, werden diese Kosten in der Regel über große Produktionsläufe amortisiert, was zeigt, dass ABS-Kunststoff nach wie vor ein erschwingliches Material für eine breite Palette von Fertigungsanwendungen ist.
Schlussfolgerung
ABS-Kunststoff ist nach wie vor eine vielseitige, sichere Wahl für Hersteller, die ein Gleichgewicht zwischen Leistung und Einhaltung von Vorschriften schaffen. Auch wenn sein ökologischer Fußabdruck eine Herausforderung darstellt, ebnen Fortschritte beim Recycling und biobasierte Alternativen den Weg für eine nachhaltige Nutzung.