Los moldes de inyección son herramientas esenciales en el proceso de fabricación del plástico. Crean piezas inyectando plástico fundido en la cavidad de un molde. Las dos mitades principales del molde -el núcleo y la cavidad- forman las características internas y externas de la pieza de plástico. Este proceso implica varios componentes y técnicas de ingeniería de precisión que garantizan series de producción repetibles y de alta calidad para diversas industrias.
Esta guía proporciona información detallada sobre diseño de moldes, selección de materiales, consideraciones críticas de diseño y prácticas de mantenimiento, con conocimientos prácticos sobre aplicaciones reales en distintos sectores.
1. ¿Qué son los moldes de moldeo por inyección?
Los moldes de moldeo por inyección son herramientas de fábrica que se utilizan para dar forma sólida al plástico fundido mediante la inyección a presión de un material plástico en un molde. Esa cavidad tiene una forma precisa para reflejar la forma final del producto, por lo que el molde suele estar formado por dos componentes:
- Cara del núcleo: La configuración interior de la pieza moldeada, incluyendo cosas como agujeros, roscas u otras formas complejas. El lado del núcleo es esencial para formar la geometría interior del producto.
- Lado de la cavidad: Define la geometría exterior y las características de la pieza. Este lado entra directamente en contacto con el plástico fundido y da forma a la superficie exterior del componente final.
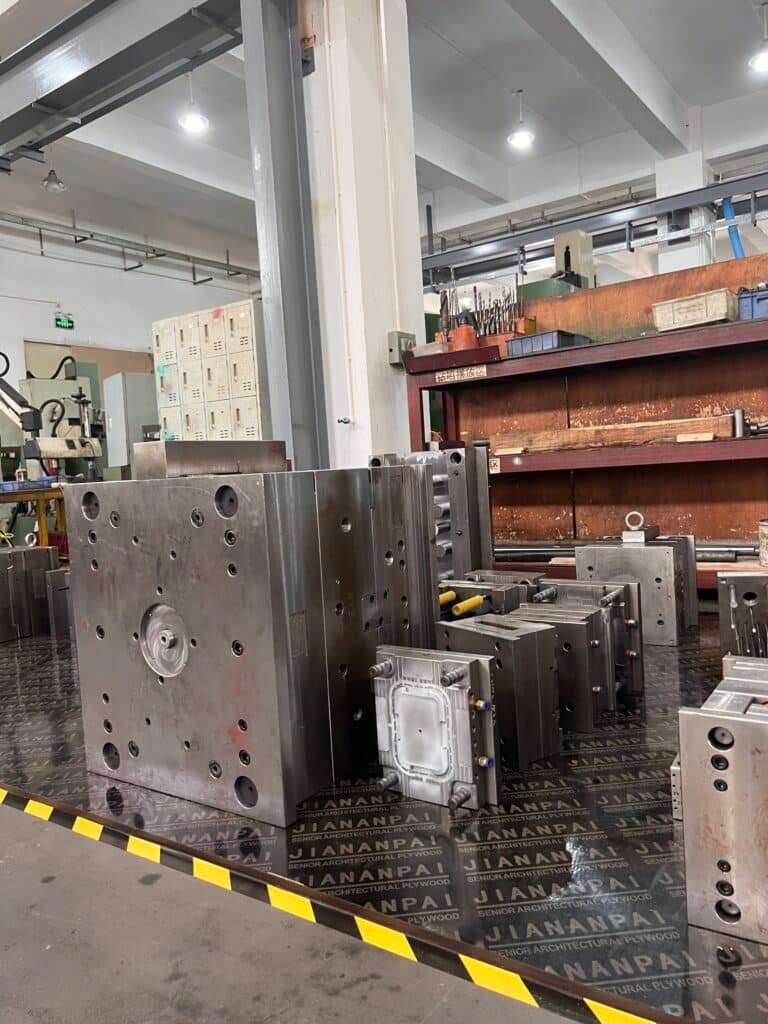
Funciones clave de los moldes de moldeo por inyección:
- Distribución del material: Una red de canales (bebederos, canaletas y compuertas) dirige el plástico fundido dentro del molde. De este modo, el material se distribuye uniformemente en todas las cavidades y fluye a toda la sección del molde.
- Refrigeración: Los moldes de moldeo por inyección incluyen canales de refrigeración que hacen pasar refrigerante (agua la mayoría de las veces) a través del molde. Esto ayuda a enfriar y solidificar el polímero líquido que se ha inyectado, lo que permite extraer fácilmente las piezas de los moldes sin que se deformen.
- Expulsión: Una vez que el plástico se ha coalescido y enfriado, los pasadores o placas del operario empujan el componente moldeado desde el catéter. Esto permite liberar la pieza de forma segura sin dañar el molde ni la propia pieza.
2. Componentes básicos de un molde

Cada molde tiene una serie de componentes básicos que desempeñan papeles vitales en el moldeo por inyección. Los siguientes componentes son esenciales para un rendimiento óptimo del molde:
Componente | Propósito | Material |
Base del molde | Sujeta y alinea los componentes del molde | Acero P20, 718H |
Cavidad y núcleo | Define la forma de la pieza | Acero H13, aluminio (Al7075) |
Sistema eyector | Empuja las piezas hacia fuera después de enfriarlas | SKD61, acero endurecido |
Canales de refrigeración | Regula la temperatura para mantener la eficacia | Aleaciones de cobre, acero inoxidable |
Respiraderos | Libera el aire y los gases atrapados durante el moldeo | Ranuras mecanizadas (0,02-0,03 mm) |
Base del molde
La base del molde es un componente importante que mantiene todos los elementos del molde en su sitio, garantizando su correcta alineación. A menudo, la base está fabricada en acero P20 o 718H, lo que proporciona un ajuste duradero y de precisión que se mecaniza con facilidad.

Cavidad y núcleo
La cavidad dentro de las superficies del molde define las características externas de la pieza, mientras que el núcleo define sus características internas. Las piezas se fabrican con materiales resistentes al calor y al desgaste, como el acero H13, o con aleaciones de aluminio, como el Al7075, que se utiliza sobre todo para prototipos rápidos y de bajo volumen.
Sistema eyector
Estos permiten que la pieza acabada se enfríe, y el sistema eyector la empuja fuera del molde una vez que está fría. El objetivo de este sistema es expulsar la pieza de forma segura sin dañar la parte del molde mediante pasadores o placas eyectoras de acero endurecido (por ejemplo, SKD61).

Canales de refrigeración
Los canales de refrigeración se integran en el interior del molde para regular la temperatura y optimizar los tiempos de ciclo. Suelen estar hechos de aleaciones de cobre y acero inoxidable, con la alta conductividad térmica necesaria para ayudar a enfriar la pieza de forma rápida y uniforme.
Respiraderos
Los respiraderos son pequeñas ranuras o canales de mecanizado que permiten la salida del aire o gas atrapado durante la inyección. Si no están bien ventilados, el aire atrapado puede crear defectos en la pieza (por ejemplo, burbujas o huecos, acumulación de presión, etc.) y, en consecuencia, el fallo de la pieza.
3. Tipos de moldes de moldeo por inyección
Los moldes de moldeo por inyección son de varios tipos según las distintas necesidades de fabricación, como la producción de grandes volúmenes o las aplicaciones especializadas.
① Moldes de dos placas
Tipo: El diseño de molde más sencillo y barato consiste en dos líneas de partición. El canal permite el flujo pasivo de plástico en la cavidad, y una línea de separación separa el núcleo y la cavidad.
Lo mejor para: Las piezas que requieren geometrías sencillas sin acciones laterales son las mejores para los moldes de dos placas; algunos ejemplos son los tapones de botella, los clips de automoción y los pequeños bienes de consumo.
Tiempo de ciclo: El tiempo de ciclo de los moldes de dos placas oscila entre 15 y 30 segundos, lo que permite producir componentes sencillos a alta velocidad.
② Moldes de tres placas
Estructura: Dos líneas de separación separan el sistema de canales de las piezas. Las líneas de separación pueden ser sencillas o incluir diseños más complejos, como moldes con varias cavidades que permiten formar varias piezas en cada ciclo de moldeo.
Ideal para: Los moldes de tres placas son ideales para la producción multicavidad, lo que significa pequeños conectores electrónicos o grandes cantidades de bienes de consumo.
Desventajas: La principal desventaja de los moldes de tres placas es el coste adicional de las herramientas, ya que estos moldes de moldeo por inyección pueden ser un 20-30% más caros que los moldes de dos placas debido a su mayor complejidad.
③ Moldes de canal caliente
Estructura: Los moldes de canal caliente están diseñados con un colector calentado que mantiene el plástico fundido a medida que se desplaza por los canales. No hay bebedero, lo que también reduce los residuos.
Ventajas: Los moldes de canal caliente son más eficientes porque eliminan el desperdicio de bebederos, y los tiempos de ciclo son más rápidos (5-15% menos de tiempo de ciclo que los sistemas de canal frío).
Coste: Los sistemas de canal caliente suelen ser un 30-50% más caros que los de canal frío debido a la complejidad de los elementos calefactores y del sistema de colectores.
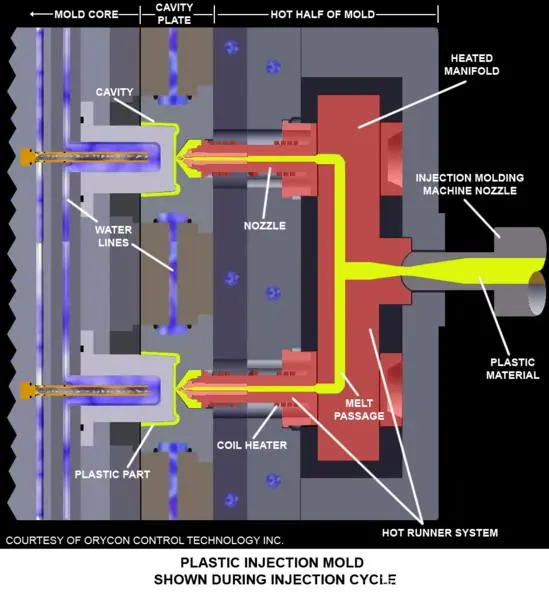
④ Moldes de sobremoldeo/inserción
Proceso: El sobremoldeo consiste en inyectar un segundo material, generalmente plástico pero también metal, sobre la superficie de un sustrato existente. Un ejemplo es la utilización de plásticos blandos y duros; este proceso puede utilizarse para unir dos materiales distintos.
Aplicaciones: El sobremoldeo se utiliza ampliamente en dispositivos médicos con sensores incorporados, mangos suaves al tacto para herramientas manuales y componentes multimaterial en sistemas electrónicos.

4. Materiales para moldes: Elección de la aleación adecuada
Seleccionar el material adecuado para el molde es fundamental para conseguir la durabilidad, el acabado y el rendimiento deseados. Estos son algunos de los materiales para moldes más utilizados:
Material | Pros | Contras | Lo mejor para |
Acero P20 | Asequible, buena pulibilidad | Baja resistencia al desgaste | Prototipos, bajo volumen (<50k ciclos) |
Acero para herramientas H13 | Alta resistencia al calor, duradero | Caro, pesado | Producción de gran volumen |
Aluminio (7075-T6) | Mecanizado ligero y rápido | Vida útil limitada (~10k disparos) | Creación de prototipos, producción de bajo volumen |
Cobre berilio | Conductividad térmica superior | Tóxico durante el mecanizado | Zonas de refrigeración de alta velocidad |
Acero P20
Una elección habitual en prototipos al momento hasta la producción de bajo volumen. (Asequible, muy buena pulibilidad). De hecho, su resistencia al desgaste es inferior a la de otros materiales, como el acero H13.
Acero para herramientas H13
Se necesitan series de producción de gran volumen, y el acero para herramientas H13 se utiliza ampliamente por su mayor resistencia al calor y durabilidad. Sin embargo, es más caro y pesado, lo que repercute en el coste total del utillaje.
Aluminio (7075-T6)
Dave: Ligeras y rápidas de mecanizar, las aleaciones de aluminio (por ejemplo, 7075-T6) son ideales para prototipos y fabricación de bajo volumen. En cambio, los moldes de aluminio, aunque pueden fabricarse con mayor rapidez y coste, suelen tener una vida útil más corta, por lo que no son tan buenos para aplicaciones de gran volumen.
Cobre berilio
El cobre berilio se emplea en zonas de refrigeración de alta velocidad debido a su alta conductividad térmica. Sin embargo, es tóxico cuando se mecaniza, por lo que requiere precauciones de seguridad especializadas.
5. Consideraciones críticas de diseño
El diseño del molde también es vital para el proceso de moldeo por inyección. Las consideraciones de diseño incluyen diversos elementos que afectan a la eficacia del molde, la calidad de la pieza final y los tiempos del ciclo de producción.
① Diseño de compuertas
Una compuerta es el punto por el que el plástico fundido entra en la cavidad del molde. Los tipos de compuertas son compuertas de borde, compuertas submarinas y compuertas de punta caliente.
Edge Gates: mejor para piezas planas, resulta en muy poco daño cosmético a la superficie moldeada.
Compuertas submarinas: Estas compuertas son perfectas para piezas pequeñas como engranajes, ya que recortan automáticamente cualquier exceso de material.
Compuertas de punta caliente: característica de los sistemas de canal caliente para garantizar acabados superficiales limpios y sin recortes adicionales.
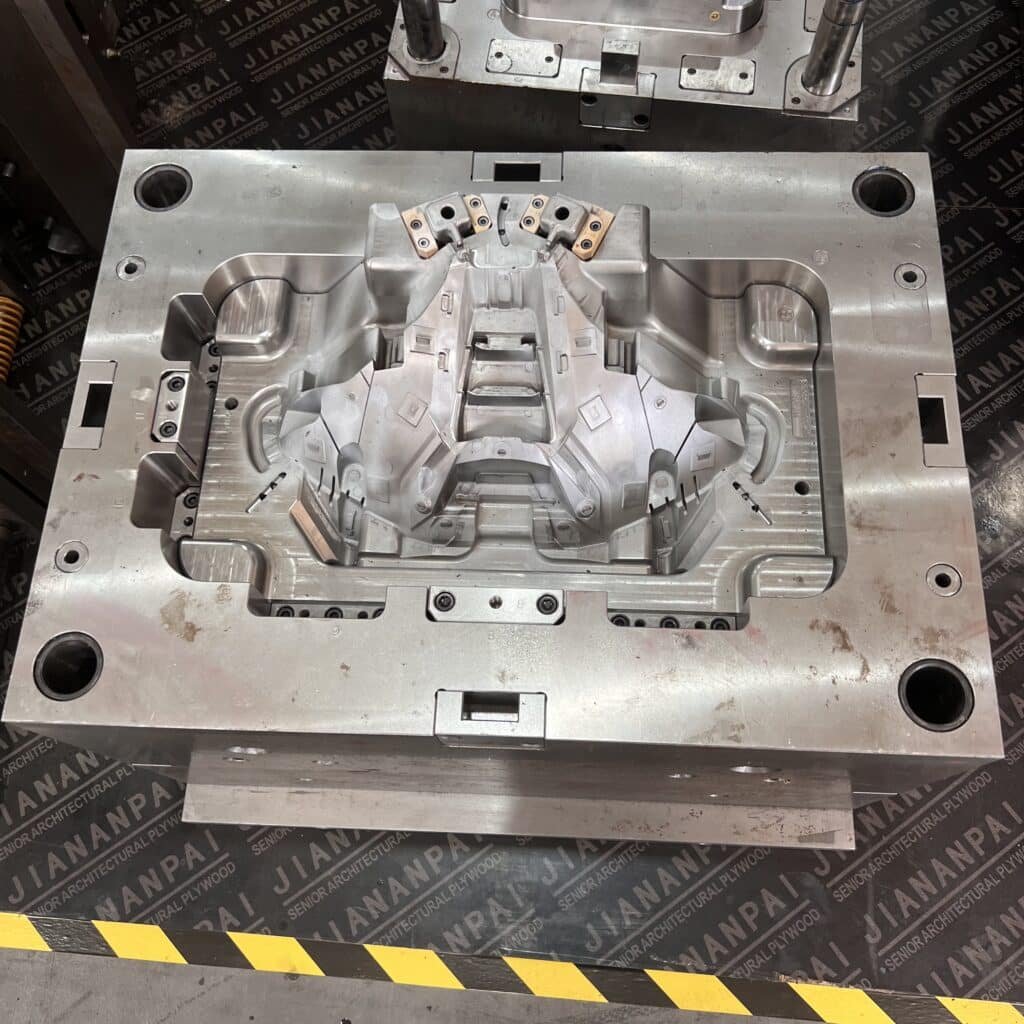
② Ángulos de calado
Los ángulos de desmoldeo son las conicidades de los lados de la cavidad del molde que ayudan a extraer la pieza del molde. Generalmente, el ángulo de desmoldeo mínimo es de 1°-2° para superficies texturizadas y de 0,5° para núcleos pulidos. No respetar los ángulos de desmoldeo adecuados puede hacer que las piezas se atasquen en el molde, aumentando la tasa de desechos y reduciendo la eficiencia general de la producción.
③ Optimización de la refrigeración
La refrigeración es uno de los factores más importantes en el moldeo por inyección. Esta disminución prolonga los tiempos del ciclo de producción al tiempo que reduce la calidad de la pieza. El tiempo de refrigeración suele representar entre el 50 y el 60% de la duración del ciclo. Las nuevas tecnologías, como los canales de refrigeración conformados impresos en 3D, pueden ayudar a optimizar la refrigeración, lo que se traduce en tiempos de ciclo más cortos y una mayor eficiencia de la producción.
6. Mantenimiento y prolongación de la vida útil
Un mantenimiento adecuado del molde es crucial para mantener la consistencia de la calidad de las piezas y aumentar la vida útil del molde. Las actividades de mantenimiento habituales incluyen la lubricación de los pasadores eyectores, el pulido de las cavidades y el endurecimiento de los núcleos de acero. Con un mantenimiento adecuado, los moldes de moldeo por inyección pueden durar muchos años con una eficacia óptima.
Prácticas de mantenimiento:
- Diariamente: Engrasar los pasadores eyectores, inspeccionar el desgaste y limpiar las caras del molde.
- Mensual: Mezcle las cavidades del molde con pasta de diamante para obtener un acabado superficial liso;
- Anualmente: El endurecimiento de los núcleos de acero mediante nitruración puede prolongar la vida útil del molde hasta 100.000 ciclos.
Si no se realiza un mantenimiento adecuado, la vida útil del molde disminuirá drásticamente. Por ejemplo, si los moldes de acero H13 no se mantienen con regularidad, su vida útil puede disminuir un 40 %, lo que conlleva más sustituciones y, en consecuencia, tiempos de inactividad más largos en la producción.
7. Aplicaciones específicas de la industria
Los moldes de moldeo por inyección se utilizan en diversas industrias, cada una de ellas con requisitos específicos para el diseño de moldes, la selección de materiales y los procesos de producción.
Industria | Requisitos del moho | Borde del molde BFY |
Médico | Materiales conformes con la FDA, certificación ISO 13485 | Moldeo validado en sala blanca |
Automóvil | Acabados de alto brillo, tolerancias estrechas (±0,02 mm) | Inspección CMM interna y asistencia PPAP |
Electrónica de consumo | Micromoldeo (piezas de <1 g), blindaje EMI | Sobremoldeo de LSR para juntas estancas |
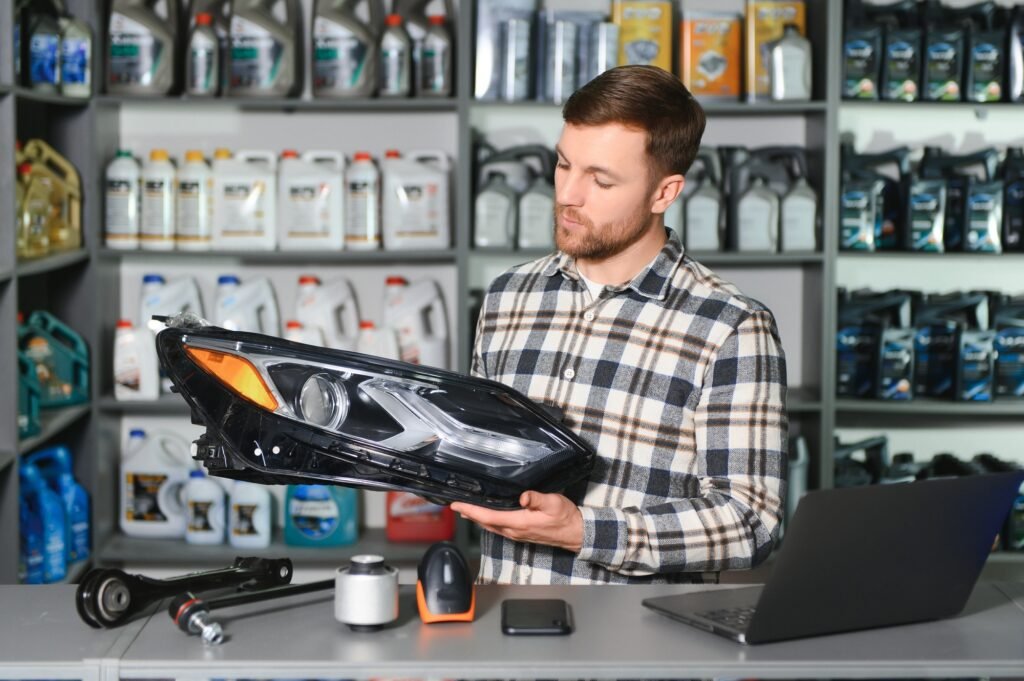
Las 10 preguntas más frecuentes sobre moldes de inyección
1. ¿Qué materiales se utilizan habitualmente para los moldes de moldeo por inyección?
Los moldes suelen ser de acero templado (por ejemplo, P20, H13) para grandes volúmenes de producción o de aluminio (por ejemplo, 7075-T6) para prototipos y series pequeñas. El acero ofrece durabilidad (más de 500.000 ciclos), mientras que el aluminio reduce costes y plazos de entrega.
2. ¿Cómo elijo entre moldes de acero y moldes de aluminio?
- Moldes de acero: Lo mejor para >100.000 unidades, geometrías complejas y tolerancias ajustadas (±0,01 mm).
- Moldes de aluminio: Ideales para prototipos o <10.000 unidades, ofrecen un plazo de entrega un 50% más rápido y unos costes un 30-40% más bajos.
3. ¿Cuál es la vida útil típica de un molde de inyección?
- Moldes de acero: 500.000-1.000.000 de ciclos con un mantenimiento adecuado.
- Moldes de aluminio: 5.000-10.000 ciclos. Factores como la abrasividad del material (p. ej., resinas vitrificadas) y los métodos de refrigeración afectan a la longevidad.
4. ¿Cuánto cuesta un molde de inyección a medida?
Los costes oscilan entre 5.000-5.000-100.000+, dependiendo de:
- Material: Acero frente a aluminio.
- Complejidad: Acciones laterales, socavones o microcaracterísticas.
- Tamaño: Los moldes más grandes requieren más material y tiempo de mecanizado.
5. ¿Cuál es el plazo de fabricación de un molde a medida?
- Moldes de aluminio: 2-4 semanas.
- Moldes de acero: 6-12 semanas. Los servicios acelerados pueden reducir los plazos en un 30%, pero aumentan los costes en un 15-25%.
6. ¿Qué medidas de control de calidad garantizan la precisión del molde?
Los proveedores reputados utilizan:
- MMC (máquina de medición por coordenadas): Verifica tolerancias de ±0,005 mm.
- Análisis del flujo del molde: Predice y previene defectos como el alabeo.
- Certificación ISO 9001: Garantiza procesos estandarizados.
7. ¿Puede modificar un molde existente para cambiar el diseño?
Sí, pero los costes dependen de la complejidad:
- Cambios menores (por ejemplo, cambio de tamaño de la puerta): 500-500-2.000, 1-2 semanas.
- Revisiones importantes (por ejemplo, añadir núcleos): 3.000-3.000-15.000, 3-6 semanas.
8. ¿Cómo gestionan el mantenimiento y las reparaciones del moho?
Oferta de proveedores:
- Mantenimiento preventivo: Limpieza periódica, lubricación y sustitución de componentes.
- Reparaciones de emergencia: asistencia 24 horas al día, 7 días a la semana, para problemas críticos (por ejemplo, grietas en cavidades).
- Reacondicionamiento: Pulido o reendurecimiento de superficies desgastadas.
9. ¿En qué sectores están especializados para la producción de moldes?
Los mejores proveedores sirven:
- Médico: Moldes conformes a la FDA para jeringuillas o implantes.
- Automoción: Moldes multicavidad para salpicaderos o conectores.
- Electrónica de consumo: Moldes de alto brillo para carcasas de smartphones.
10. ¿Qué tipo de apoyo postproducción ofrecen?
- Asistencia técnica: Solución de defectos de piezas u optimización de procesos.
- Documentación: Archivos de diseño de moldes, registros de mantenimiento y certificaciones de materiales.
- Piezas de repuesto: Acceso inmediato a pasadores eyectores, correderas o calentadores.
Conclusión
Los moldes de moldeo por inyección son fundamentales para producir componentes de plástico de alta calidad en diversas industrias. El tipo de molde, el material y las opciones de mantenimiento adecuados pueden optimizar la producción, reducir costes y garantizar la calidad del producto. La impresión 3D y los dispositivos fotónicos orgánicos son ejemplos de aplicaciones específicas con sus propios requisitos (como la morfología de características submicrónicas) que son posibles gracias a un diseño de molde y un rendimiento de selección de materiales óptimos.

Para moldes de precisión, BFY Mold ofrece asistencia experta en diseño para fabricación (DFM), sistemas de moldes híbridos rentables y servicios de mantenimiento del ciclo de vida completo. BFY Mold es su socio para moldes de inyección de alta calidad, ya sea en medicina, automoción o electrónica.