Les produits en acrylique moulés par injection sont appréciés pour leur clarté et leur polyvalence, mais ils peuvent être sujets à des défauts tels que des déformations et des bulles. Il est essentiel de comprendre comment résoudre ces problèmes pour obtenir des résultats optimaux dans votre processus de fabrication. Dans cet article, nous allons explorer les solutions pratiques et les meilleures pratiques pour minimiser ces défauts et garantir la production de produits de moulage par injection de haute qualité.
Supposons qu’il y ait un gauchissement et une déformation du produit pendant le processus de moulage par injection. Dans ce cas, le problème doit être résolu principalement à partir de la conception du moule, et l’effet d’ajustement des conditions de moulage est minime.
Solutions pour le gauchissement et la déformation des produits moulés par injection
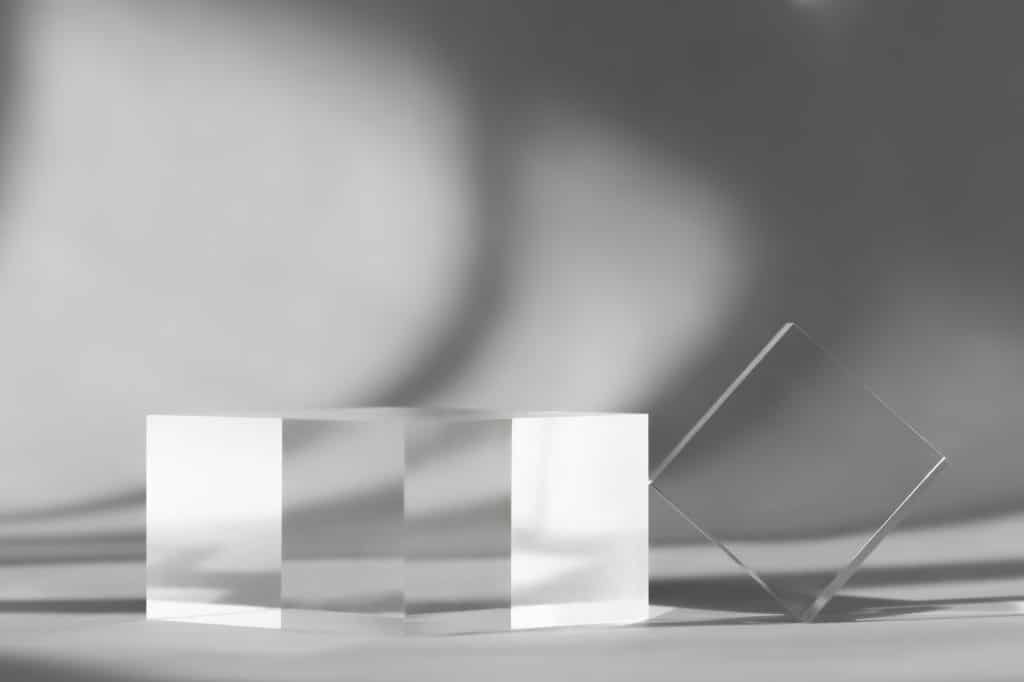
ÉTAPE 1 : Lorsque les contraintes résiduelles dues aux conditions de moulage provoquent des déformations, elles peuvent être éliminées en réduisant la pression d’injection, en surélevant le moule et en uniformisant sa température, en augmentant la température de la résine ou en utilisant la méthode du recuit.
ÉTAPE 2 : Lorsque la déformation sous contrainte est due à un mauvais relâchement, elle peut être résolue en augmentant le nombre ou la surface de la tige de poussée et en réglant la pente de relâchement.
ÉTAPE 3 : Lorsque la méthode de refroidissement ne convient pas et que le temps de refroidissement n’est pas uniforme ou insuffisant, la méthode de refroidissement peut être ajustée et le temps de refroidissement peut être prolongé. Par exemple, une boucle de refroidissement peut être placée aussi près que possible de la déformation.
ÉTAPE 4 : Pour la déformation causée par le retrait de formage, la conception du moule doit être corrigée. Parmi ces corrections, la plus importante est de veiller à ce que l’épaisseur de la paroi du produit soit cohérente. Parfois, en cas de nécessité, il est nécessaire de corriger le moule en mesurant la déformation du produit et en le taillant dans la direction opposée.
Les résines à fort taux de retrait, généralement cristallines (telles que les résines polyformaldéhyde, nylon, polypropylène, polyéthylène et PET, etc.) ont une déformation plus importante que les résines amorphes (telles que les résines acryliques, le chlorure de polyvinyle, le polystyrène, les résines ABS et les résines AS, etc.) En outre, comme la résine renforcée par des fibres de verre présente une coordination des fibres, la déformation est également importante.
Comment résoudre les causes des bulles
Lorsque la paroi du produit est plus épaisse, la vitesse de refroidissement de la surface extérieure est plus rapide que celle du centre, de sorte qu’avec le refroidissement, le côté résine du centre se rétracte et s’étend à la surface, de sorte que le centre est insuffisamment rempli. Cette situation est propice à la formation de bulles de vide. Les principales solutions sont les suivantes :
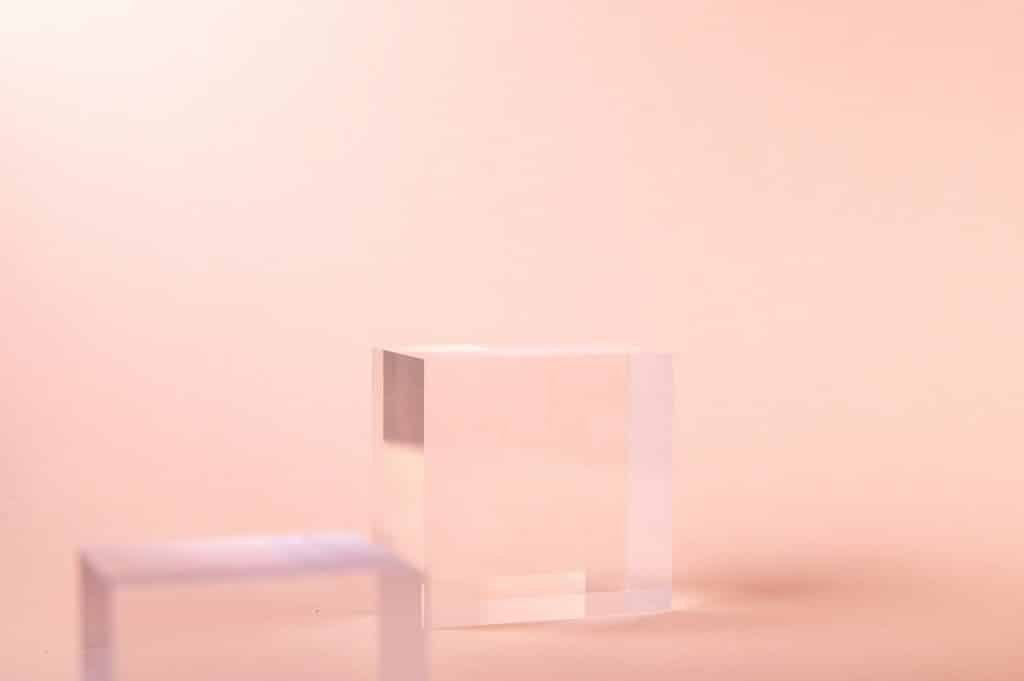
a) Déterminer la taille raisonnable de la porte et de la glissière en fonction de l’épaisseur de la paroi. En règle générale, la hauteur de la porte doit être comprise entre 50 et 60 % de l’épaisseur de la paroi du produit.
b) Jusqu’à ce que la porte soit scellée, il reste une certaine quantité de matériau d’injection supplémentaire.
c) Le temps d’injection doit être légèrement plus long que le temps de scellement de la porte.
d) Réduire la vitesse d’injection et augmenter la pression d’injection.
e) Des matériaux à haute viscosité à l’état fondu sont utilisés.
Résoudre les problèmes de bulles de gaz volatils dans le moulage par injection
a) Pré-séchage complet.
b) Réduire la température de la résine pour éviter la production de gaz de décomposition.
c) Les bulles causées par une mauvaise fluidité peuvent être résolues en augmentant la température de la résine et du moule et en augmentant la vitesse d’injection.