La machine de moulage par injection de plastique est l’un des équipements les plus couramment utilisés dans la fabrication de moules en plastique. Elle permet de fondre des matières plastiques dans des abrasifs à haute température et sous pression afin de fabriquer des produits de différentes formes.
En fonction des différents besoins et du champ d’application, les machines à injecter les matières plastiques peuvent être divisées en une variété de types et de modèles. Cet article présente les types et les caractéristiques des machines de moulage par injection de matières plastiques afin de vous aider à mieux comprendre la sélection et l’utilisation des machines de moulage par injection.

Classification des modes d’injection
1. Machine de moulage par extrusion
L’extrudeuse est adaptée aux produits de longue section en tuyaux et en bois. Le plastique fond et extrude le moule à l’aide d’une vis rotative, ce qui se caractérise par une grande capacité de travail et une qualité de produit stable.
2. Machine de moulage par injection
La machine à jet de plastique est le type de machine à plastique le plus courant. Elle convient à la production de produits plastiques de formes diverses, tels que les appareils japonais, les boîtiers de produits électroniques, etc. Elle introduit le plastique fondu dans l’outil abrasif par l’intermédiaire du dispositif de jet pour créer la forme de produit souhaitée, avec une grande précision de production et une bonne qualité de surface.
3. Machine de moulage par soufflage
La machine de moulage par soufflage convient à la production de produits en plastique creux, tels que les bouteilles, les conteneurs, etc. Le plastique fondu peut être placé dans le moule en plastique, et le plastique peut être soufflé avec de l’air à haute pression pour créer l’aspect désiré du produit, qui a les caractéristiques d’une forte capacité de travail et d’un produit léger.
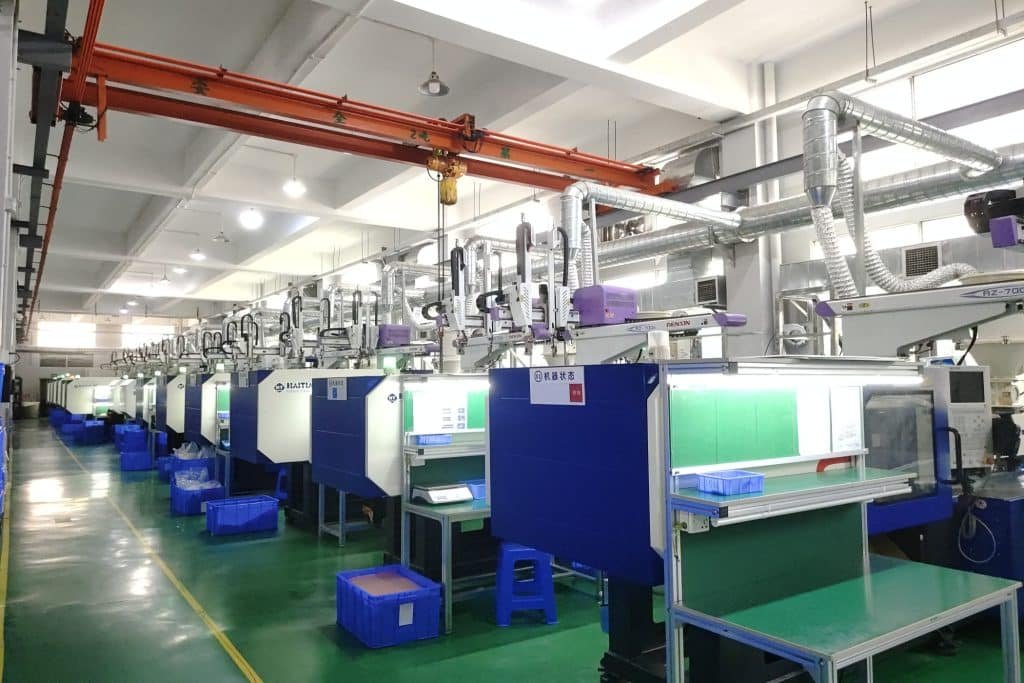
Classification des caractéristiques structurelles
1. Machine de moulage par injection horizontale
La machine horizontale pour matières plastiques est un type de machine pour matières plastiques dont la structure et le fonctionnement sont simples. L’équipement d’introduction et les abrasifs sont situés au même niveau, ce qui convient à la production de pièces en plastique, de connecteurs électroniques et d’autres petits produits.
2. Machine de moulage par injection verticale
Une machine verticale pour matières plastiques est une machine compacte et de petite taille. L’équipement d’introduction et les outils abrasifs sont situés sur la même surface verticale, ce qui convient à la production de produits à hauteur limitée tels que les composants intérieurs d’automobiles et les connecteurs de fibres optiques.
Classification des méthodes de moulage par injection
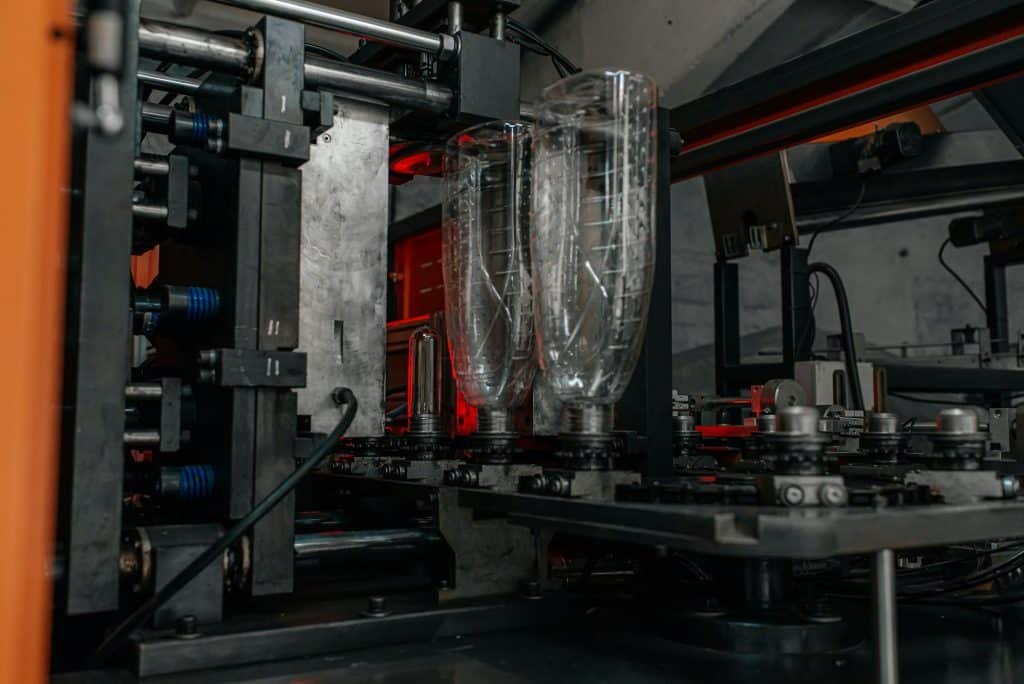
1. Machine de moulage par injection à canaux froids
La machine à plastique à canal froid est une machine à plastique courante, adaptée à la production de grandes quantités de produits. Elle introduit le plastique fondu dans la cavité de l’abrasif par le canal froid à l’intérieur de l’abrasif, puis le refroidit et le sèche rapidement grâce à l’unité de réfrigération. Après le moulage, le produit est déchargé en fonction du dispositif de jet, avec une forte capacité de travail et des caractéristiques de faible consommation.
2. Machine plastique à canaux chauds
La machine à canal chaud est adaptée à la production de produits très demandés ayant une belle apparence et des spécifications strictes. Grâce au système de chauffage du moule en plastique, le plastique fondu est immédiatement introduit dans la cavité abrasive afin d’éviter le reflux de la solution et les déchets causés par le canal froid, ce qui permet d’économiser de l’énergie, de réduire les émissions et d’obtenir des produits de bonne qualité.
Quel que soit le type de machine plastique, il est important de choisir le modèle adapté à votre production. Après avoir sélectionné la machine, il convient de prêter attention à la taille du produit, aux caractéristiques du matériau, à la productivité et à d’autres facteurs, et de communiquer pleinement avec le fabricant de la machine pour garantir l’amélioration des performances et du niveau de production.