L’acrylonitrile butadiène styrène (ABS) est une pierre angulaire de la fabrication moderne, réputée pour son équilibre inégalé entre résistance, durabilité et facilité de traitement. Depuis sa commercialisation dans les années 1950, l’ABS a révolutionné des secteurs allant de l’automobile à l’électronique grand public, en offrant une alternative légère mais robuste aux métaux et autres plastiques. Cet article fournit une analyse complète du plastique ABS, étayée par des graphiques comparatifs et des informations sur la réglementation, afin de répondre aux questions essentielles concernant sa sécurité, son impact sur l’environnement et ses applications sur le marché américain.
1. Qu’est-ce que le plastique ABS ?
L’ABS est un polymère thermoplastique fabriqué à partir de trois monomères :
- Acrylonitrile (15-35%) : Améliore la stabilité chimique/thermique.
- Butadiène (5-30%) : Une phase caoutchouteuse pour la résistance aux chocs
- Styrène (40-60%) : Assure la rigidité et une finition brillante.
En outre, la construction de l’ABS permet d’obtenir une excellente finition de surface et une résistance à l’usure, ce qui garantit que les produits ne sont pas seulement durables, mais qu’ils ont aussi fière allure. L’équilibre de ses molécules lui permet d’être soumis à des techniques de traitement extrêmes, notamment le moulage par injection et l’extrusion, avec une faible perte de propriétés.

Propriétés principales :
Propertya | Plage de valeurs | Pertinence de l’application |
Résistance à la traction | 29–45 MPa | Composants structurels |
Résistance aux chocs | 200–400 J/m | Pare-chocs automobiles, jouets |
Point de fusion | 105–125°C | Boîtiers résistants à la chaleur |
Densité | 1.04–1.06 g/cm³ | Biens de consommation légers |
2. Le processus de fabrication de l’ABS
La production d’ABS fait appel à la polymérisation en émulsion :
- Mélange de monomères : L’acrylonitrile, le butadiène et le styrène sont combinés.
- Réaction : Polymérisation à 50-150°C avec des initiateurs (par exemple, des peroxydes).
- Compoundage : Les additifs (stabilisateurs UV, retardateurs de flamme) sont mélangés.
- Granulation : Extrusion et découpe en granulés de matières premières.
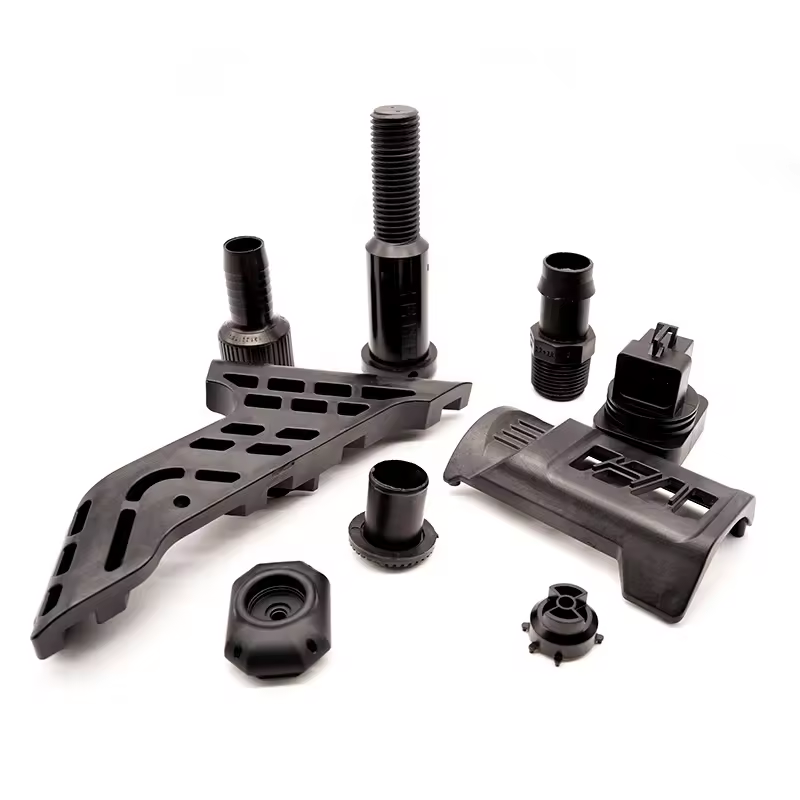
Consommation d’énergie :
- ABS: 85–100 MJ/kg
- Polypropylène (PP) : 70-85 MJ/kg
- Polycarbonate (PC) : 110-130 MJ/kg
3. Le plastique ABS est-il sûr ?
La sécurité est une préoccupation essentielle pour tout matériau utilisé dans les produits destinés aux consommateurs. Le plastique ABS est généralement considéré comme sûr en raison de son inertie chimique et de sa stabilité dans des conditions d’utilisation normales. Des recherches approfondies et des évaluations réglementaires ont confirmé que l’ABS ne libère pas de substances nocives lors d’une utilisation quotidienne. Il est donc particulièrement adapté aux produits en contact étroit avec les êtres humains, qu’il s’agisse de composants automobiles, de boîtiers électroniques, de jouets ou d’appareils de cuisine.
L’ABS est conforme aux normes de la FDA pour les applications en contact avec les aliments et certifié non toxique par la CPSC pour les jouets.

Facteurs de sécurité :
- Pas de BPA ni de phtalates : Contrairement au PVC, l’ABS ne contient pas d’additifs perturbateurs endocriniens.
- Stabilité thermique : Dégagement gazeux minime en dessous de 80°C.
- Tests de lixiviation : <0,1 ppm de migration de styrène (limite FDA : 0,5 ppm).
Étude de cas : Un fabricant de jouets américain a réduit les rappels de 60 % après avoir remplacé le PVC par l’ABS.
4. Applications courantes de l’ABS
Le plastique ABS est également un matériau largement utilisé pour le moulage par injection en raison de son excellent équilibre de propriétés, qui comprend une bonne résistance aux chocs, la durabilité et la facilité de traitement. C’est pourquoi tout le monde l’utilise couramment, de l’industrie automobile à l’industrie de l’électronique grand public. Par exemple, l’ABS est couramment utilisé dans le secteur automobile, où les pièces moulées du tableau de bord et les garnitures intérieures doivent résister à des chocs importants et à des températures basses sans perdre leur forme ou leur intégrité. Dans le secteur de l’électronique grand public, l’ABS est couramment utilisé pour produire des boîtiers d’imprimantes, des télécommandes et des boîtiers d’outils électriques, où une finition lisse et un moulage précis sont primordiaux. Cette qualité fait que le plastique ABS est également bien adapté à l’industrie du jouet, où la création de produits non toxiques et durables est primordiale. Cette qualité est évidente dans des produits tels que les figurines et les blocs de construction.

L’industrie | Cas d’utilisation | Bénéfice |
Automobile | Panneaux du tableau de bord | Résistance aux chocs, stabilité aux UV |
Électronique | Touches du clavier | Rigidité, finition esthétique |
Médical | Boîtiers d’appareils | Stérilisable (en autoclave) |
Jouets | Briques LEGO | Non toxique, inaltérable |
5. ABS et autres matériaux
La concurrence la plus importante pour le plastique ABS est celle d’autres matériaux polymères commerciaux tels que le polycarbonate (PC), le polypropylène (PP) et le polyéthylène (PE). Ces matériaux présentent des atouts uniques, mais l’ABS tend à se situer dans une position intermédiaire. Si le polycarbonate offre une meilleure clarté et une meilleure résistance aux chocs, il est généralement plus cher et moins résistant aux rayures de surface, par exemple. Le polypropylène et le polyéthylène, bien que présentant une résistance chimique et une flexibilité, n’ont pas la rigidité et les avantages esthétiques de l’ABS.
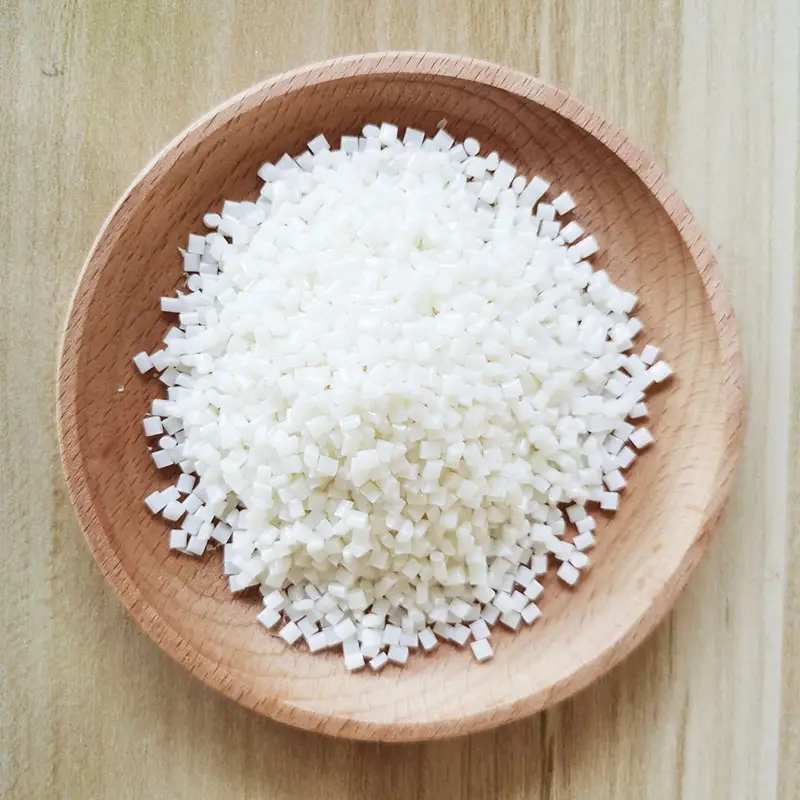
Propertya | ABS | PC | PP |
Résistance aux chocs | Haut | Très élevé | Faible |
Coût ($/kg) | 2.5–3.5 | 4.5–6.0 | 1.8–2.5 |
Recyclabilité | Modéré | Faible | Haut |
Résistance aux UV | Juste | Excellent | Pauvre |
6. Impact environnemental de l’APA
- Taux de recyclage : 18-22 % aux États-Unis (contre 30 % pour le PET).
- Défis : Les systèmes en boucle fermée sont limités ; 65% des ABS finissent dans les décharges.
Innovations :
- Recyclage chimique : Décomposition de l’ABS en monomères (rendement de 70 %).
- Bio-ABS : 30% de contenu végétal (par exemple, Terluran® ECO).
7. Conformité réglementaire aux États-Unis
- FDA : Food Contact Substance Notification (FCN) pour les ustensiles de cuisine.
- CPSC : certification ASTM F963-17 pour les jouets.
- UL 94 : Classement d’inflammabilité V-0 pour l’électronique.
8. Coût du plastique ABS dans le moulage par injection
En ce qui concerne le coût, le plastique ABS est un matériau économique par rapport à d’autres thermoplastiques à haute performance, ce qui constitue une option intéressante pour la production de masse. En fonction des qualités et des conditions du marché, la résine ABS coûte généralement entre 1,50 et 3,00 dollars la livre. Comme pour les autres thermoplastiques, les coûts du moulage par injection de l’ABS dépendent de facteurs tels que la complexité de la conception du moule, les temps de cycle et le volume de production.
Par exemple, un grand volume de boîtiers simples pour des produits de consommation peut atteindre de faibles coûts unitaires grâce à des économies d’échelle, alors que des pièces personnalisées bien détaillées qui nécessitent un outillage complexe et des coûts initiaux de moulage ont leur place ici. Par souci de rentabilité, ces coûts sont généralement amortis sur de grandes séries de production, ce qui montre que le plastique ABS reste un matériau abordable pour une large gamme d’applications de fabrication.
Conclusion
Le plastique ABS reste un choix polyvalent et sûr pour les fabricants, car il permet d’équilibrer les performances et la conformité réglementaire. Bien que son empreinte environnementale pose des problèmes, les progrès réalisés en matière de recyclage et d’alternatives biosourcées ouvrent la voie à une utilisation durable.