Lors du moulage par injection de matériaux PC, des problèmes se posent souvent, tels que des bulles dispersées de manière irrégulière sur la surface du produit ou des particules de bulles fines et denses. Comment résoudre les problèmes de bulles et de cloques lors du moulage par injection de PC ?
Raisons des problèmes courants de traitement du moulage par injection de PC :
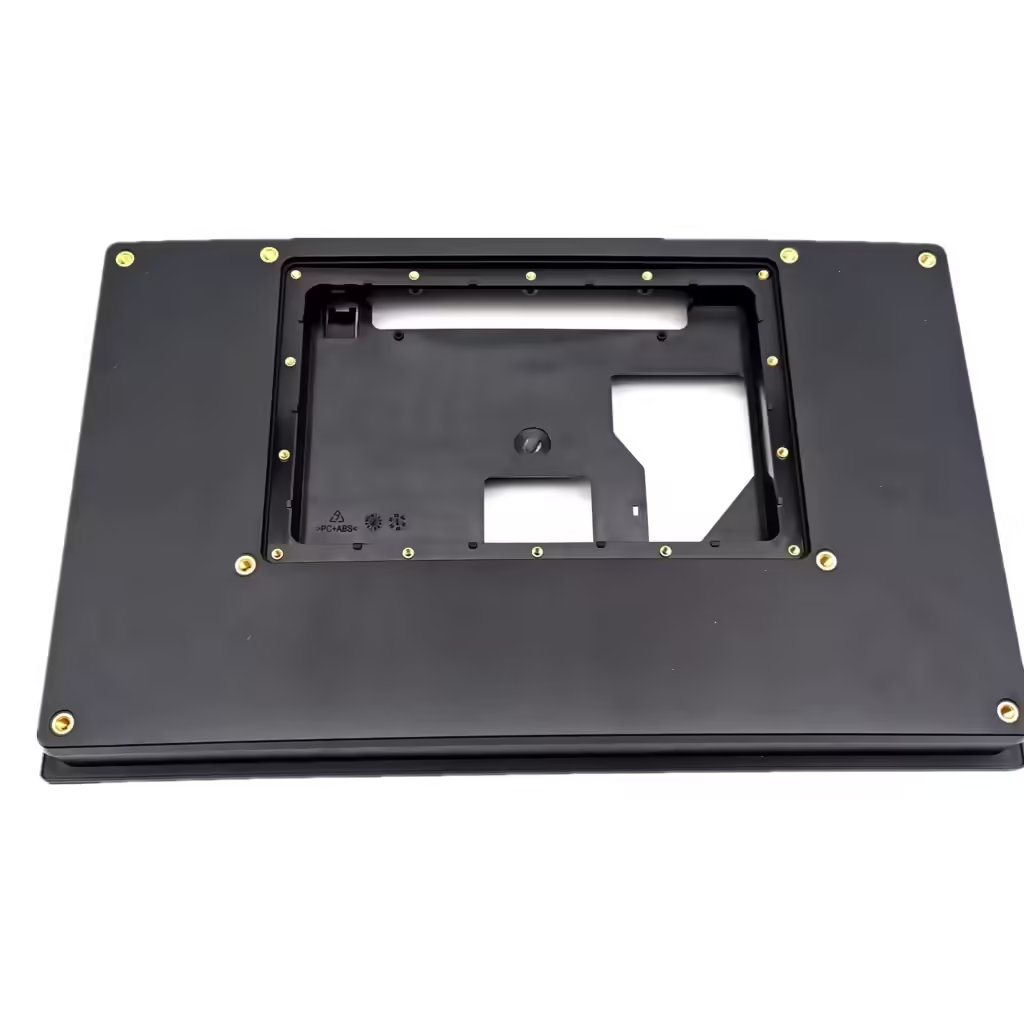
1. Des bulles sont disséminées de manière irrégulière à la surface du produit, principalement causées par la vapeur d’eau.
2. Si les particules de bulles sont relativement fines et denses, elles sont principalement réparties autour de la porte du produit, formant des lignes en forme de rayon ou d’éventail, qui sont principalement dues à l’air.
3. Lorsque la cavité du moule comporte de nombreux angles, que la différence d’épaisseur est trop importante, qu’il y a de nombreux inserts ou que la position de la porte est inappropriée, la matière fondue s’écoule dans la cavité du moule, remuant l’air dans le moule pour former des courants de Foucault, et des traînées d’air se forment dans certaines parties. Par exemple, dans les panneaux d’interrupteurs et de prises des produits électriques moulés, cette situation se produit souvent parce que les prises, les interfaces et les interrupteurs sont tous concentrés au même endroit. La solution à ce défaut consiste à modifier le moule, à renforcer l’échappement du moule et à optimiser la position de la porte ; d’autre part, il faut réduire le taux de remplissage du moule, en particulier le taux d’injection dans les zones présentant des traces d’air.
4. La principale raison de la production de gaz de décomposition est que la température de fusion est trop élevée.
5. Une autre raison importante est que le PC lui-même est de mauvaise qualité et facile à décomposer. Le PC est également sensible aux produits chimiques et se décompose facilement.
6. Le gaz de solvant est principalement lié à la qualité des opérations de production, telles qu’un nettoyage incorrect de la barrique, un excès d’additifs, etc.
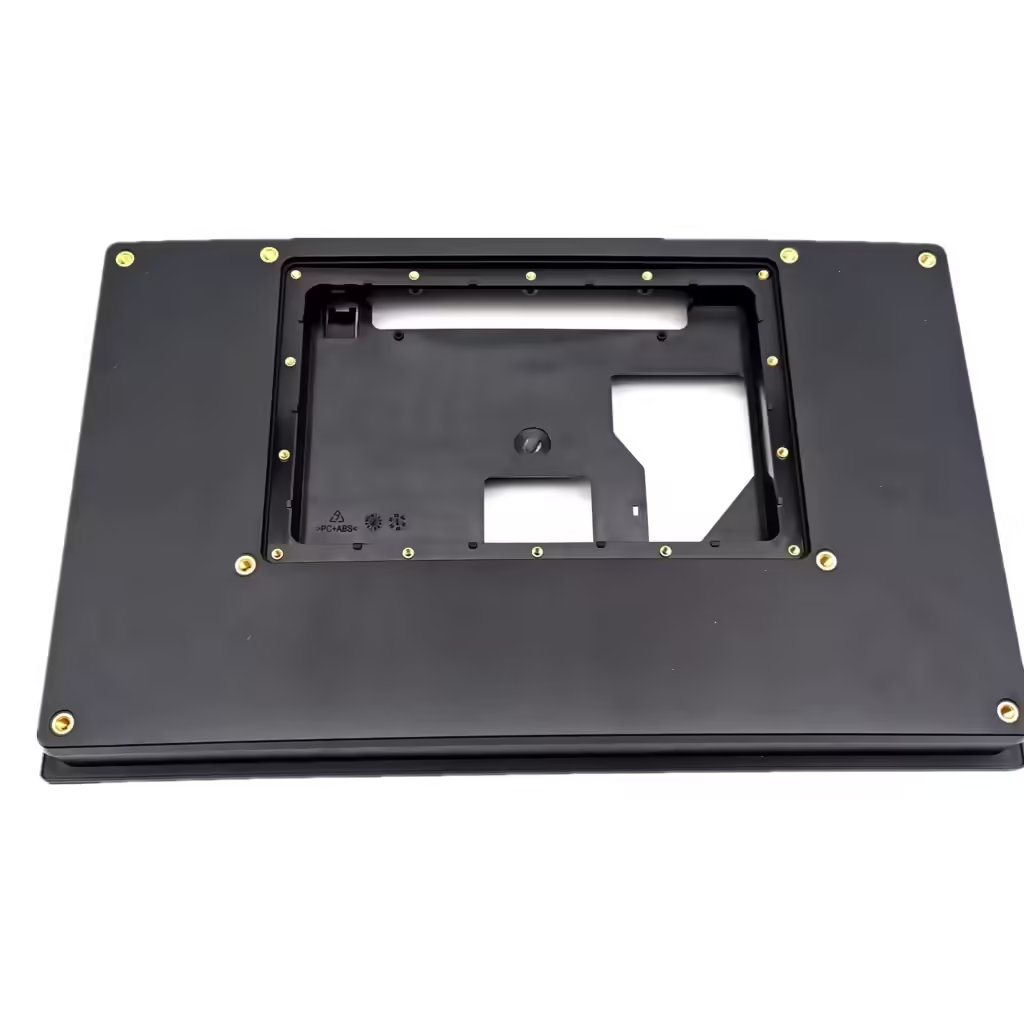
Solution :
Lorsque l’épaisseur de la paroi du produit est importante, la surface extérieure se refroidit plus rapidement que la partie centrale. Au fur et à mesure du refroidissement, la résine de la partie centrale se rétracte et se dilate vers la surface, ce qui entraîne un sous-remplissage de la partie centrale et la formation de bulles de vide.
1. Les principales solutions sont les suivantes :
a) En fonction de l’épaisseur de la paroi, déterminer la taille raisonnable de la porte et de la glissière. En règle générale, la hauteur de la porte doit être comprise entre 50 et 60 % de l’épaisseur de la paroi du produit.
b) Jusqu’à ce que la porte soit scellée, il reste une certaine quantité de matériau d’injection supplémentaire.
c) Le temps d’injection doit être légèrement plus long que le temps de scellement de la porte.
d) Réduire la vitesse d’injection et augmenter la pression d’injection,
e) Utiliser des matériaux à haute viscosité à l’état fondu.
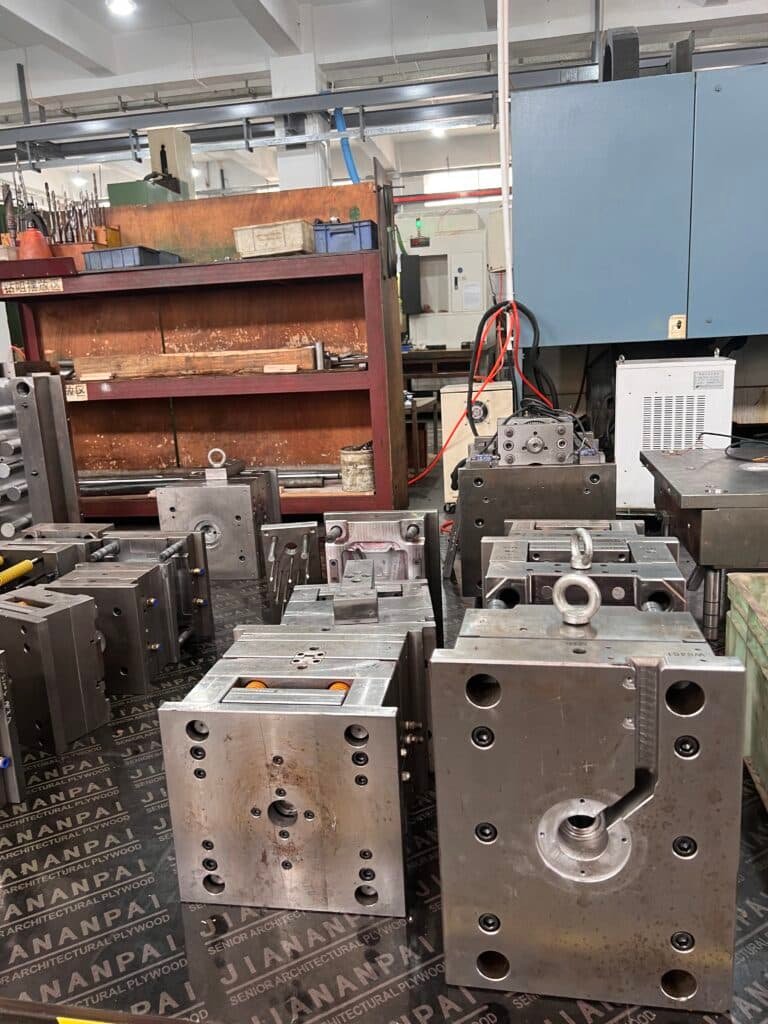
2. Les principales solutions aux bulles causées par la génération de gaz volatils sont les suivantes :
a) Effectuer un pré-séchage suffisant.
b) Réduire la température de la résine pour éviter la production de gaz de décomposition.
3. Les bulles causées par une mauvaise fluidité peuvent être résolues en augmentant la température de la résine et du moule et en augmentant la vitesse d’injection.
BFY Mold intègre la conception et la formation des produits et se charge principalement du développement et de la conception des moules en plastique, de la conception et de la fabrication des moules, du moulage par injection des produits, du traitement de la surface des produits et d’autres services. Avec plus de 20 ans d’expérience dans la conception et la fabrication de moules, l’industrie du moulage par injection peut créer des moules compétitifs pour vous. Contactez-nous dès aujourd’hui pour une optimisation gratuite de vos dessins.