사출 성형 생산 주기 이해
사출 성형 생산 경쟁이 갈수록 치열해지는 상황에서 생산 효율성을 개선하는 것은 주목할 만한 문제입니다. 사출 주기를 개선하는 방법은 다음과 같습니다.
유압 구동 사출 성형기의 사출 사이클은 금형 폐쇄 시작부터 다음 금형 폐쇄까지의 기간을 말합니다. 금형 폐쇄는 일반적으로 빠른 금형 폐쇄, 느린 금형 폐쇄, 저압 금형 보호 및 고압 금형 잠금의 네 가지 섹션으로 나뉩니다. 고압 모드 잠금이 완료된 후 사출이 시작되며 여러 단계로 나뉩니다. 금형 캐비티는 사출 중에 용융된 플라스틱으로 채워집니다. 금형 캐비티가 채워지고 압력이 상승하고 주입의 최종 제어가 부적절하면 완제품의 가장자리가 거칠어집니다.

압력 유지는 사출이 완료된 후 시작됩니다. 냉각은 금형 캐비티가 채워진 후, 즉 압력 보존에서 시작됩니다. 금형이 냉각되면 완제품이 수축합니다. 보압은 아직 응고되지 않은 냉간 유로를 통해 수축으로 형성된 함몰 부위를 채우고, 보압은 일반적으로 사출 압력보다 낮기 때문에 탈형시 완제품이 가득 차도록합니다 (움푹 들어간 곳없이). 냉간 흐름 경로가 응고되면 압력 유지가 종료될 수 있습니다. 압력 유지는 여러 섹션으로 나눌 수 있으며 각 섹션의 압력 유지 압력은 다르며 (일반적으로 단계별로 감소) 시간으로 나뉩니다.
완성된 무게 또는 덴트에 따라 총 유지 시간이 설정됩니다. 짧은 홀딩 시간에서 조정하고 각 사출 성형마다 홀딩 시간을 조금씩 늘려 완제품의 무게가 더 이상 증가하지 않거나 생산 덴트가 허용 가능한 수준이 될 때까지 홀딩 시간을 늘릴 필요가 없습니다.
벽이 얇은 제품은 사출 직후 완제품의 내부 층이 굳기 때문에 압력을 유지할 필요가 없는 경우가 많습니다.

사출 성형기에서 설정하는 냉각 시간 매개 변수는 압력 유지가 완료된 후부터 금형 개방까지의 기간이지만, 금형 캐비티가 플라스틱으로 채워지는 즉시 냉각이 시작됩니다. 냉각 시간의 목적은 완제품이 배출로 인한 변형없이 계속 냉각되고 응고되도록하는 것입니다. 냉각 시간은 실험을 기반으로한다고 말해야합니다. 처음에는 저장이 동시에 수행됩니다. 냉각 시간이 보관 시간보다 길거나 보관 시간이 냉각 시간보다 길 수 있습니다. 보관 시간이 냉각 시간보다 길면 나사의 가소 화 용량이 부족하여 생산주기에 영향을 미치는 것을 나타냅니다.
따라서 이 경우 가소화 용량을 늘리는 것이 사이클 시간을 단축하는 방법이며, 목표는 보관 시간을 단축하는 것입니다.
완제품을 한 번 또는 여러 번 밀면 골무가 다시 닫히고 다음 사이클이 즉시 시작되며 새로 설계된 엘보우 사출 성형기는 재생 폐쇄 오일 경로 (차동 폐쇄 기능)를 사용하여 금형이 높은 충격의 영향을받지 않는다는 전제하에 더 높은 폐쇄 속도를 위해 노력하여 사용하기에 적합합니다. 고전압 클램핑은 완제품이 버링을 생성하지 않도록 할 수있는 가장 낮은 클램핑 력을 채택하여 고전압 클램핑 섹션에 필요한 시간을 단축 할 수 있습니다.
금형, 사출 성형기 봉, 토글 조인트 및 거푸집도 낮은 클램핑력으로 인해 수명이 연장됩니다. 완제품에 기포나 연소와 같은 결함이 발생하지 않는 경우 사출 섹션에서 높은 사출 속도를 사용할 수 있습니다. 가장 낮은 사출 압력을 사용하면 필요한 체결력(팽창력)이 감소하고, 가장 낮은 배럴 온도를 사용하면 냉각 시간이 단축됩니다.
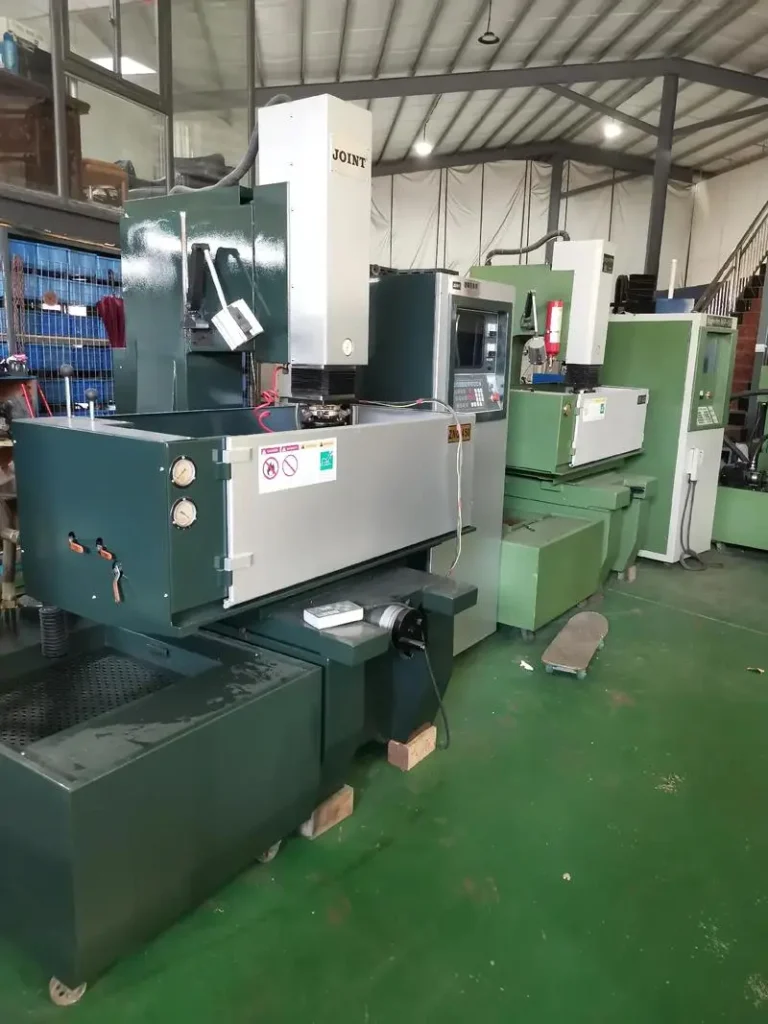
냉각 시간은 금형의 열 교환 효율과 관련이 있으며, 적절한 금형을 설계하면 열 교환 효율을 향상시킬 수 있습니다. 그러나 허용되는 경우 얼음물 냉각으로 냉각 시간을 단축할 수 있습니다. 얼음물 냉각으로 인해 금형이 응축되고 건식 팬과 밀봉 된 금형 잠금 장치가 이슬점을 줄이고 응축을 방지 할 수 있습니다.
가소화 용량이 생산 주기에 영향을 미칠 만큼 충분하지 않은 경우 나사 설계 및 파라미터 조정에서 다음을 수행할 수 있습니다:
a: 스크린 나사는 가소화 능력을 높일 수 있습니다.
b: 대구경 나사는 가소화 용량을 늘릴 수 있습니다.
c: 나사의 홈 깊이를 늘리면 가소화 용량을 늘릴 수 있습니다.
d: 나사의 속도를 높이면 가소화 능력을 높일 수 있습니다(PVC, PET 등과 같이 전단에 민감한 특정 플라스틱은 이 방법을 사용할 수 없음).
e: 배압을 최대한 줄이면 가소화 속도가 빨라집니다.
f: 오일 압력 밀봉 노즐은 금형을 열고 닫을 때 가소화하는 데 사용됩니다.
g: 사전 가소제 설계를 사용하면 사출 및 압력 유지 시간을 제외한 사이클에서 나사를 가소화할 수 있습니다.
h: 압력 유지 장치를 사용하여 압력 유지 섹션의 나사도 가소화할 수 있도록 합니다.
이송 전후의 백업 케이블(배출)은 시간이 많이 걸리며 스프링 노즐이나 오일 압력 씰로 교체하여 백업 케이블의 작동을 제거해야 합니다. 완제품이 찢어지거나 큰 개방 소음이 발생하지 않고 금형이 최고 속도로 열립니다. 일부 사출 성형기에는 금형을 열기 전에 감압 장비가 있으며 금형을 고속으로 열어도 소리가 나지 않습니다.
고속 개방에서 정확한 정지 위치를 달성하기 위해 브레이크 밸브 또는 폐쇄 루프 제어를 사용할 수 있습니다. 토출력이 작은 소형 사출기에서는 유압 토출 속도보다 높은 공압 토출을 사용할 수 있습니다. 전기 토출이 공압 토출보다 빠릅니다. 독립적 인 오일, 가스 또는 회로 제어를 사용하여 다중 배출 측면 개방 다이 측면 배출 기능을 실현할 수 있습니다.
일부 완제품의 여러 사출은 사출 성형기의 진동 사출일 수 있습니다. 여러 번의 사출 시간을 단축하기 위해 골무를 매번 완전히 빼낼 필요는 없습니다. 최종 배출은 마감과 동시에 시작될 수 있습니다. 골무의 이동 거리가 상대적으로 짧기 때문에 골무는 항상 금형이 잠기기 전에 완전히 후방으로 이동합니다.
사출 성형 생산 효율성에 대한 결론
이러한 전략을 구현함으로써 제조업체는 사출 성형 생산 주기를 크게 단축하여 시장에서 효율성과 경쟁력을 강화할 수 있습니다. 지속적인 모니터링과 조정을 통해 이러한 프로세스를 더욱 최적화하여 생산 시간을 최소화하면서 고품질의 결과물을 보장할 수 있습니다.