Comprender el ciclo de producción del moldeo por inyección
En el caso de la competencia cada vez más feroz en la producción de moldeo por inyección, la mejora de la eficiencia de la producción es un problema digno de atención. He aquí cómo mejorar el ciclo de inyección.
El ciclo de inyección de una máquina de moldeo por inyección accionada por presión de aceite se refiere al período comprendido entre el inicio del cierre del molde y el siguiente cierre del molde. El cierre del molde se divide generalmente en cuatro secciones: cierre rápido del molde, cierre lento del molde, protección del molde a baja presión y bloqueo del molde a alta presión. La inyección comienza una vez finalizado el cierre del molde a alta presión y se divide en varias etapas. La cavidad del molde se llena de plástico fundido durante la inyección. Cuando se llena la cavidad del molde, la presión aumenta y el control final de la infusión es inadecuado, el producto acabado producirá un borde áspero.

La conservación de la presión comienza una vez finalizada la inyección. El enfriamiento empieza después de llenar la cavidad del molde, es decir, comienza a partir de la conservación de la presión. Cuando el molde se enfría, el producto acabado se encoge. La presión de retención rellena la depresión formada por la contracción a través del canal de flujo frío que aún no se ha solidificado, y la presión de retención es generalmente inferior a la presión de inyección para que el producto acabado esté lleno al desmoldar (sin abolladuras). Cuando el canal de flujo frío se solidifica, se puede terminar la retención de presión. El mantenimiento de la presión puede dividirse en varias secciones, y la presión de mantenimiento de la presión de cada sección es diferente (generalmente disminuye paso a paso), que se divide por tiempo.
El peso o la abolladura del producto acabado fija el tiempo de retención total. Ajústalo a partir de un tiempo de mantenimiento corto, y aumenta un poco el tiempo de mantenimiento en cada moldeo por inyección, hasta que el peso del producto acabado ya no aumente o la abolladura de producción sea aceptable, no será necesario aumentar el tiempo de mantenimiento.
Muchos productos de paredes finas no necesitan mantener la presión porque la capa interior del producto acabado se solidifica inmediatamente después de la inyección.

El parámetro de tiempo de enfriamiento establecido por la máquina de moldeo por inyección es un período que va desde la finalización del mantenimiento de la presión hasta la apertura del molde, pero el enfriamiento comienza tan pronto como la cavidad del molde se llena de plástico. El propósito del tiempo de enfriamiento es permitir que el producto terminado continúe enfriándose y solidificándose, sin deformarse debido a la expulsión. Hay que decir que el tiempo de enfriamiento se basa en experimentos. Al principio, el almacenamiento se realiza simultáneamente. El tiempo de enfriamiento es más largo que el tiempo de almacenamiento, o el tiempo de almacenamiento puede ser más largo que el tiempo de enfriamiento. Si el tiempo de almacenamiento es más largo que el tiempo de enfriamiento, indica que la capacidad de plastificación del tornillo es insuficiente, lo que afecta al ciclo de producción.
Por lo tanto, aumentar la capacidad de plastificación es la forma de acortar el tiempo de ciclo en este caso, y el objetivo es acortar el tiempo de almacenamiento.
El producto terminado se empuja hacia fuera una o muchas veces, el dedal se cerrará de nuevo, y el siguiente ciclo comienza inmediatamente, la máquina de moldeo por inyección de codo de nuevo diseño tiene un camino de aceite de cierre regenerativo (función de cierre diferencial), para esforzarse por una mayor velocidad de cierre, bajo la premisa de que el molde no se ve afectado por el alto impacto, adecuado para su uso. La sujeción de alto voltaje adopta la fuerza de sujeción más baja que puede hacer que el producto terminado no produzca rebabas, lo que puede acortar el tiempo requerido para una sección de sujeción de alto voltaje.
Los moldes, las barras de la máquina de moldeo por inyección, las uniones de palanca y el encofrado también prolongarán su vida útil debido a las bajas fuerzas de sujeción. Pueden utilizarse altas velocidades de inyección en la sección de inyección si el producto acabado no produce defectos como burbujas o quemaduras. El uso de la presión de inyección más baja reduce la fuerza de sujeción necesaria (fuerza de expansión), mientras que el uso de la temperatura de barril más baja reduce el tiempo de enfriamiento.
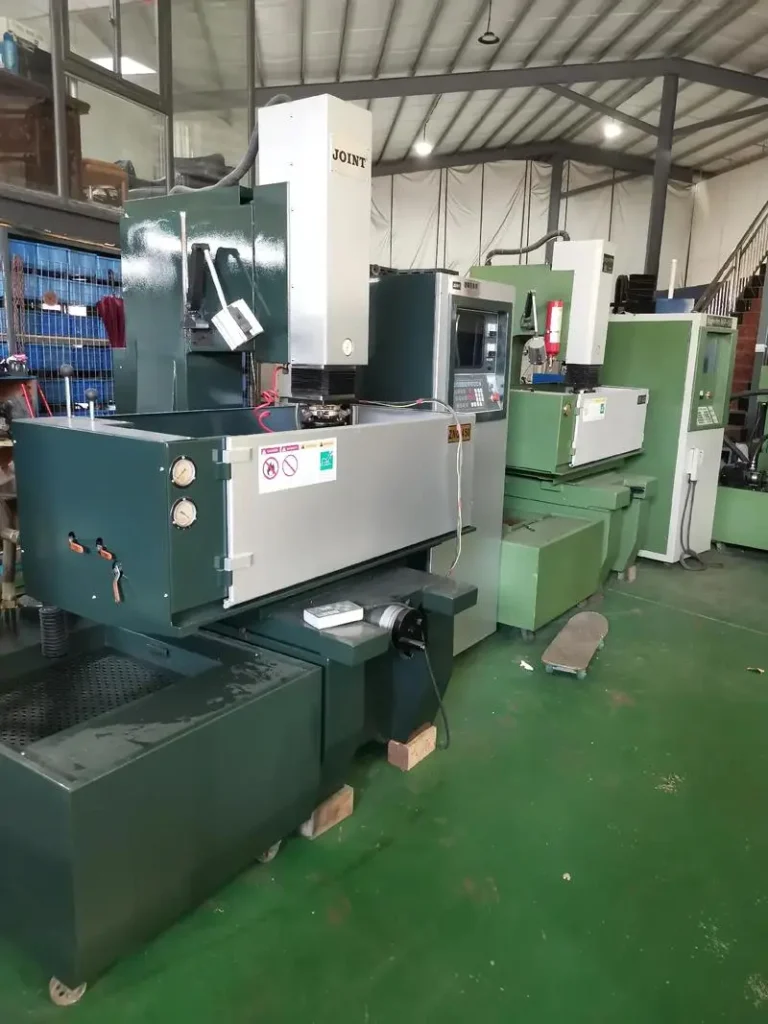
El tiempo de enfriamiento está relacionado con la eficacia del intercambio de calor del molde, y el diseño del molde adecuado puede mejorar la eficacia del intercambio de calor. Sin embargo, cuando está permitido, el enfriamiento por agua helada puede acortar el tiempo de enfriamiento. El enfriamiento por agua helada provoca la condensación del molde, y el ventilador seco y el dispositivo de cierre hermético del molde pueden reducir el punto de rocío y evitar la condensación.
Si la capacidad de plastificación no es suficiente para afectar al ciclo de producción, se puede hacer lo siguiente en el diseño del tornillo y en el ajuste de los parámetros:
a: El tornillo de malla puede aumentar la capacidad de plastificación.
b: Los tornillos de gran diámetro pueden aumentar la capacidad de plastificación.
c: Aumentar la profundidad de la ranura del tornillo puede aumentar la capacidad de plastificación.
d: El aumento de la velocidad del tornillo puede aumentar la capacidad de plastificación (algunos plásticos sensibles al cizallamiento, como el PVC, el PET, etc., no pueden utilizar este método).
e: Reducir al máximo la contrapresión aumentará la velocidad de plastificación.
f: La boquilla de sellado a presión de aceite se utiliza para plastificar el molde al abrir y cerrar.
g: El uso de un diseño de pre-plastificante puede hacer que el tornillo plastificado en el ciclo, excepto para la inyección y el tiempo de mantenimiento de la presión.
h: El uso de un dispositivo de sujeción a presión, de modo que el tornillo de la sección de sujeción a presión también pueda plastificarse.
El cable de reserva (expulsión) antes y después de la alimentación consume mucho tiempo y debe sustituirse por una boquilla de resorte o una junta de presión de aceite, eliminando la acción del cable de reserva. El molde se abre a la máxima velocidad sin desgarrar el producto acabado y sin producir un gran ruido de apertura. Algunas máquinas de moldeo por inyección tienen un equipo de descompresión antes de abrir el molde, y la apertura del molde a alta velocidad no producirá ruido.
Para lograr una posición de parada precisa en la apertura de alta velocidad, se puede utilizar una válvula de freno o un control de bucle cerrado. En la pequeña máquina de moldeo por inyección con una pequeña fuerza de eyección, se puede utilizar la eyección neumática, que es mayor que la velocidad de eyección de presión de aceite. La eyección eléctrica es más rápida que la neumática. Usando el control independiente de aceite, gas o circuito, puede realizar la función de eyección lateral de apertura de matriz de eyección múltiple.
Varias eyecciones de algunos productos acabados pueden ser eyecciones vibratorias de máquinas de moldeo por inyección. No es necesario retirar completamente el dedal cada vez para acortar el tiempo de las eyecciones múltiples. La expulsión final puede comenzar al mismo tiempo que el cierre. Como el recorrido del dedal es relativamente corto, el dedal siempre está completamente hacia atrás antes de que se cierre el molde.
Conclusión sobre la eficiencia de la producción de moldeo por inyección
Mediante la aplicación de estas estrategias, los fabricantes pueden reducir considerablemente el ciclo de producción del moldeo por inyección, lo que se traduce en una mayor eficacia y competitividad en el mercado. La supervisión y los ajustes continuos optimizarán aún más estos procesos, garantizando una producción de alta calidad al tiempo que se minimizan los tiempos de producción.