이 기사에서는 두 가지 측면에서 이중 사출 성형 제품을 종합적으로 이해할 수 있습니다. 첫 번째는 그 생산 공정 특성이며, 두 번째는 사출 금형 형태입니다.
투샷 사출 성형의 생산 공정 특성
1. 이중 사출 성형기는 동일한 구조와 사양을 가진 두 세트의 플라스틱화 사출 장치를 포함합니다. 생산 방법에 따라 노즐은 특수 구조를 갖거나, 동일한 구조를 가진 두 개의 구성 요소 금형을 장착하여 회전 및 교환이 가능해야 합니다.
주입 성형 시, 두 개의 주입 성형 장치에서 용융 온도, 주입 압력, 주입 용융량 및 기타 공정 파라미터는 동일해야 합니다. 두 개의 주입 성형 장치에서 공정 파라미터의 변동 차이를 최소화해야 합니다.
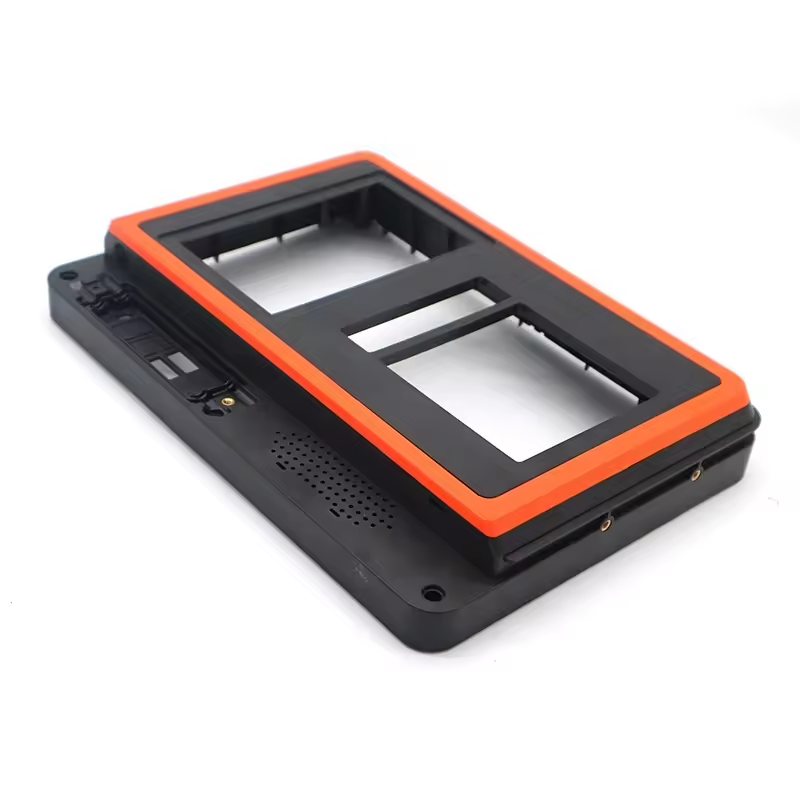
2. 일반적인 사출 성형 플라스틱 제품과 비교할 때, 이중 사출 플라스틱 제품의 용융 온도와 사출 압력은 더 높은 파라미터 값을 적용해야 합니다. 주요 이유는 이중 사출 성형의 금형 유동 채널이 상대적으로 길고, 구조가 복잡하며, 사출 용융 재료의 유동 저항이 더 크기 때문입니다.
3. 이중 사출 성형 플라스틱 제품은 고온 용융 온도와 유동 채널 내 장시간 체류로 인한 분해를 방지하기 위해 열적 안정성이 우수하고 용융 점도가 낮은 원재료를 선택해야 합니다. 폴리올레핀 수지, 폴리스티렌, 및 ABS 재료는 가장 널리 사용되는 플라스틱입니다.
4. 투샷 플라스틱 제품의 사출 성형에서 두 가지 색상의 용융 재료 성형이 금형에서 잘 융합되어 사출 성형 제품의 성형 품질을 보장하기 위해 더 높은 용융 온도, 더 높은 금형 온도, 더 높은 사출 압력 및 사출 속도를 사용해야합니다.
투샷 금형 구조 형태

전통적인 두 단계 주입 금형은 두 가지 형태로 구분됩니다: “펀치 이동”과 “펀치 회전”.
a: 펀치 번역 주사위에는 두 개의 딥과 하나의 펀치가 있습니다.
b: 첫 번째 카트리지가 발사되면 펀치와 첫 번째 다이(die)가 닫힙니다. 첫 번째 플라스틱의 주입을 완료합니다. 첫 번째 유형의 플라스틱이 굳은 후,concave와 펀치가 분리되며, 첫 번째 유형의 플라스틱으로 형성된 반제품은 펀치에 남아 펀치와 함께 두 번째 concave 다이와 정렬된 위치로 이동합니다. 사출 성형기가 닫힌 후, 두 번째 실린더에 두 번째 플라스틱이 주입됩니다. 두 번째 플라스틱이 굳은 후, 사출 성형기는 금형을 열고 완성된 제품을 제거합니다.
c: 펀치 회전 형식의 두 개의 다이로 구성된 이중 다이에는 두 개의 오목한 다이와 두 개의 뒤쪽이 맞닿은 조합으로 구성된 회전 가능한 펀치가 있습니다. 두 개의 실린더를 갖춘 양면 사출 성형기. 두 번째 실린더는 사출 성형기의 사출 방향과 수직 방향으로 설계되도록 제안되었습니다. 두 가지 다른 플라스틱을 동시에 사출할 수 있습니다. 두 종류의 사출된 플라스틱이 굳으면 사출 성형기가 열리고 완성된 제품을 자동으로 배출합니다. 제품을 제거한 후 “회전식 펀치”는 180도 회전됩니다. 사출 성형기가 닫히고 다음 사이클로 진행됩니다.
d: 첫 번째와 두 번째 실린더의 펀치 이동 방식은 차례로 주입됩니다. 펀치 회전 방식의 첫 번째와 두 번째 실린더는 동시에 주입됩니다. 따라서 동일한 제품에 대해 펀치 회전 방식의 생산 효율은 펀치 이동 방식의 두 배입니다.