현대 제조업의 방대한 환경에서 사출 성형 공정은 수많은 산업에서 사용되는 복잡한 플라스틱 부품 생산에 혁명을 일으킨 초석과 같은 존재입니다. 이 매우 다재다능하고 효율적인 기술은 세심하게 조율된 일련의 단계를 거쳐 플라스틱 원료를 정밀하고 복잡한 형태로 매끄럽게 변형합니다.
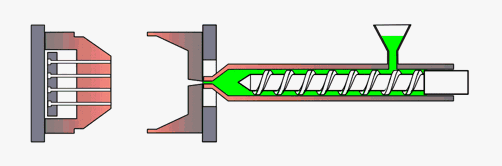
I. 사출 성형 개요
사출 성형 소개:
사출 성형은 용융된 플라스틱 재료를 금형 캐비티에 주입하여 냉각 및 응고시켜 궁극적으로 원하는 제품의 모양을 만드는 제조 공정입니다.
이 공정은 작고 복잡한 부품부터 크고 복잡한 구조물까지 다양한 품목의 생산에 널리 사용됩니다.
사출 성형기의 기본 구성 요소:
호퍼: 플라스틱 원재료가 호퍼를 통해 기계로 공급됩니다.
배럴: 배럴 내에서 플라스틱 소재는 용융 상태로 가열됩니다.
나사 또는 플런저: 용융된 플라스틱은 나사 또는 플런저 메커니즘을 사용하여 금형 캐비티에 주입됩니다.
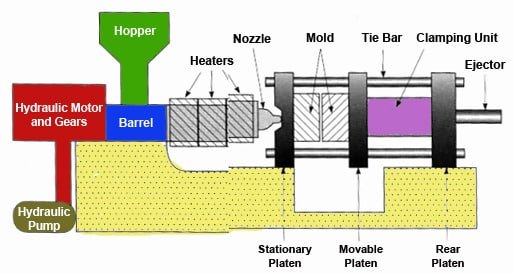
사출성형 공정
출처: www.sciencedirect.com
II. 사출 성형 공정 공개
클램핑:
첫 번째 단계는 금형을 닫고 용융된 플라스틱을 주입할 밀폐된 공간을 만드는 것입니다.
클램핑 유닛은 사출 및 냉각 단계에서 금형이 적절한 힘으로 닫힌 상태를 유지하도록 합니다.
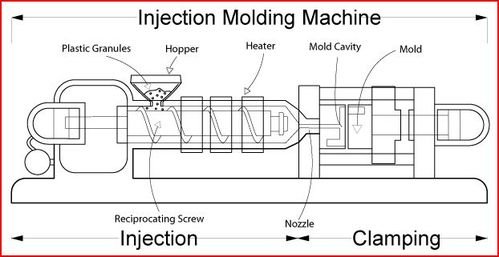
사출 성형기
출처: www.plasticsmanufacuringsystems.weebly.com
주입:
용융된 플라스틱 재료는 노즐을 통해 고압으로 금형 캐비티에 주입됩니다.
사출 단계에서는 금형을 채우고 결함을 방지하기 위해 정밀도가 필요합니다.

출처: www.researchgate.net
냉각:
금형이 채워지면 냉각 단계가 시작됩니다. 녹은 플라스틱이 굳어져 금형 모양이 만들어집니다.
냉각 시간은 제품의 최종 품질을 결정하는 데 매우 중요합니다.
III. 주입 후 단계 및 품질 보증
몰드 열기:
냉각 단계가 끝나면 금형이 열리고 새로 형성된 플라스틱 제품이 드러납니다.
이젝션 시스템은 제품을 금형 밖으로 밀어내는 데 도움을 줍니다.
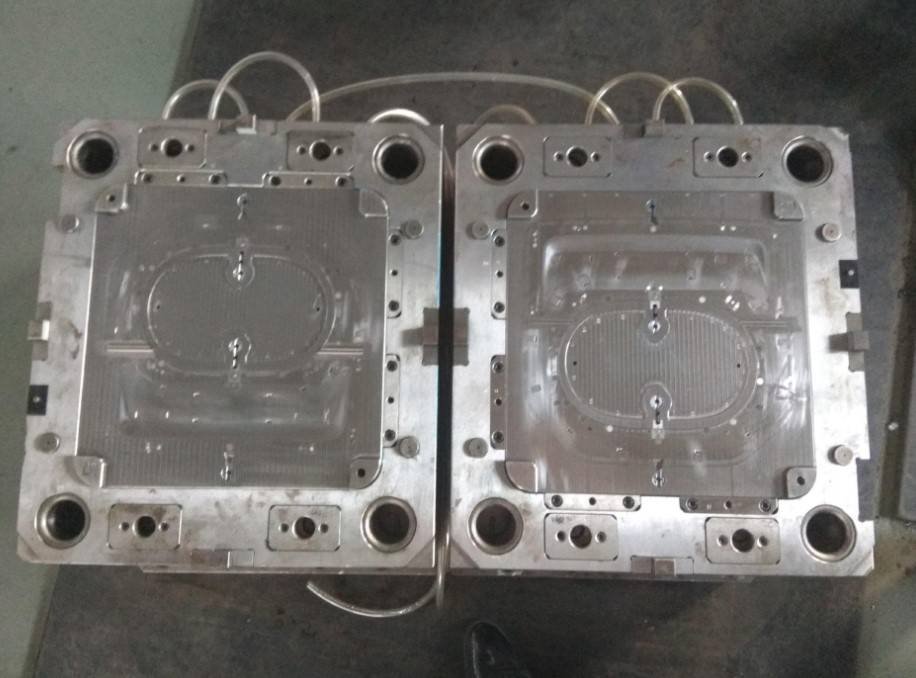
사출 금형 설계
트리밍 및 마무리:
플래시로 알려진 여분의 재료는 최종 제품이 사양을 충족하도록 잘라냅니다.
페인팅이나 조립과 같은 추가 마감 공정은 이 단계에서 수행할 수 있습니다.
품질 보증:
성형 제품이 설계 사양을 충족하는지 확인하기 위해 엄격한 품질 검사를 실시합니다.
결함이 있는 품목을 식별하여 생산 라인에서 제거합니다.
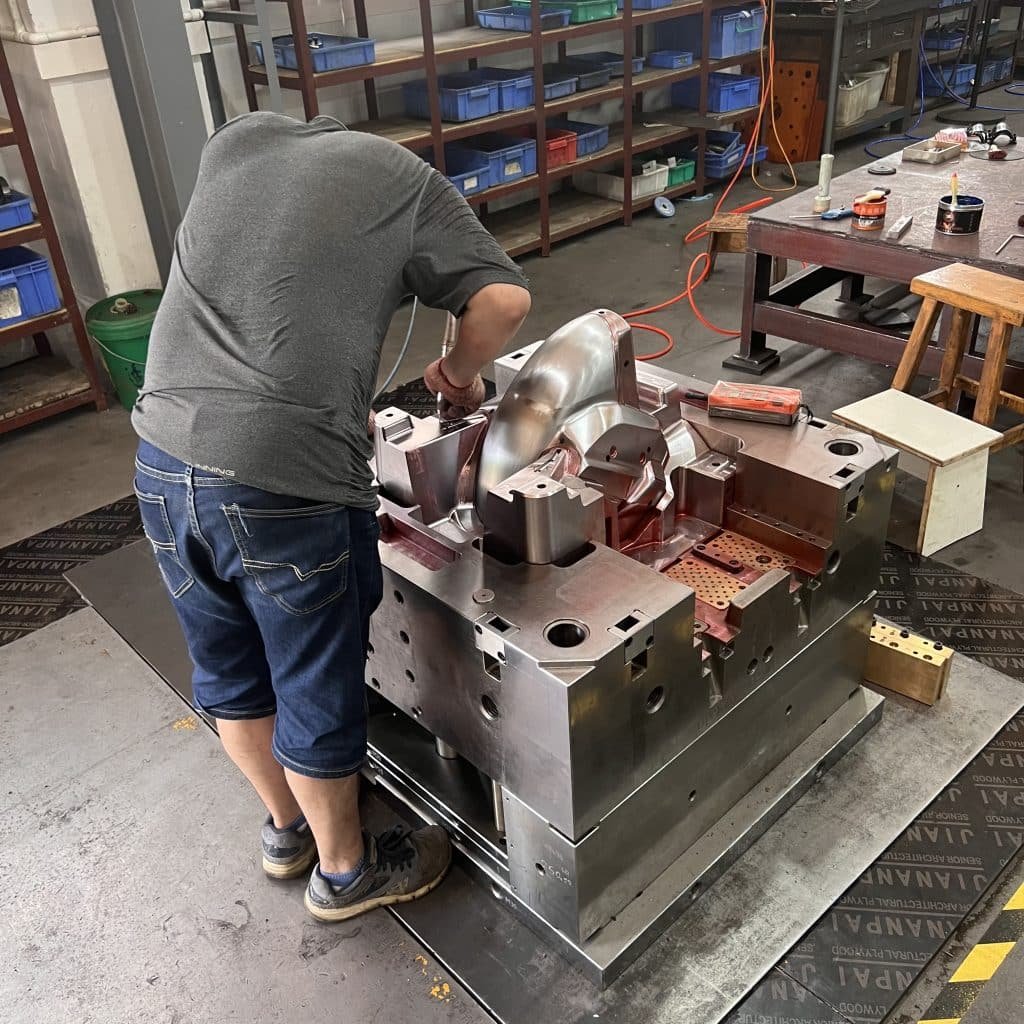
사출 금형 제조
IV. 사출 성형의 장점
높은 정밀도와 복잡성:
사출 성형은 복잡하고 복잡한 부품을 고정밀로 생산하는 데 탁월합니다.
따라서 세부적인 설계와 엄격한 허용 오차가 중요한 산업에 적합한 방법입니다.
머티리얼의 다양성:
사출 성형 공정에는 열가소성 플라스틱, 열경화성 폴리머, 엘라스토머 등 다양한 소재를 사용할 수 있습니다.
재료 특성을 향상시키기 위해 첨가제 및 보강재를 통합할 수 있습니다.

결론:
사출 성형 공정의 복잡한 과정을 자세히 들여다보면 이 방식이 단순한 제조 기술이 아니라 우리 주변의 세계를 형성하는 정밀한 예술이라는 것을 알 수 있습니다. 용융된 플라스틱을 세심하게 주입하는 단계부터 세심한 냉각 및 후처리 단계까지, 각 단계는 우리의 일상 생활을 정의하는 제품을 만드는 데 기여합니다. 산업이 계속 발전함에 따라 사출 성형은 혁신적인 디자인을 가시적인 현실로 전환하는 안정적이고 효율적인 수단을 제공하는 핵심 요소로 남아 있습니다.