Введение в литье пластмасс
Литье пластмасс превращает полимерные материалы в функциональные компоненты с помощью различных технологий производства. В компании BFY Mold мы специализируемся на восьми основных процессах, которые используются в различных отраслях промышленности — от производства медицинского оборудования до автомобилестроения. В этом подробном руководстве рассматриваются технические параметры каждого метода, идеальные области применения и экономические соображения, чтобы помочь вам выбрать услуги по литью пластмасс.

1. Литье под давлением: Высокоточная рабочая лошадка
Подробности процесса
- Подготовка материала: Сушка (2-4 часа при 80°C для гигроскопичных смол)
- Фаза плавления: Вращение шнека при 150-400°C (в зависимости от материала)
- Инжекция: Давление 50-200 МПа в стальные/алюминиевые формы
- Охлаждение: 15-60 секунд (зависит от толщины стенок)
- Выброс: Автоматизированное роботизированное извлечение
Технические характеристики
Параметр | Диапазон | Отраслевой стандарт |
Время цикла | 15-120 секунд | ISO 294 |
Размеры Тол. | ±0.005-0.05mm | ASME Y14.5 |
Жизнь плесени | 500k-1M циклов | SPI КЛАСС 101-104 |
Приложения:
- Медицина: корпуса для хирургических инструментов (в соответствии с ISO 13485)
- Автомобили: Компоненты внутренней отделки (сертифицированы IATF 16949)
- Электроника: Корпуса разъемов с толщиной стенок 0,2 мм
Преимущества:
- Высокая воспроизводимость (достижимо CpK >1,67)
- Возможна сложная геометрия
- Возможность использования нескольких материалов благодаря совместной инъекции
Ограничения:
- Высокие первоначальные инвестиции в оснастку ($15k-$250k)
- Ограниченная экономическая жизнеспособность при количестве менее 1 000 единиц
2. Экструзионное формование: Непрерывное производство профилей
Разбивка процесса
- Подача: Гранулы поступают в бочку с контролируемой скоростью
- Пластификация: Одношнековое плавление при 150-275°C
- Формирование штампа: Форма определяется геометрией инструмента
- Охлаждение: Калибровочные столы с вакуумным уплотнением
- Резка: Летающие пилы для контроля длины
Ключевые показатели эффективности
Тип выхода | Диапазон скоростей | Толерантность |
Трубы/трубопроводы | 2-10 m/min | ±0,1% диаметр |
Лист/пленка | 5-50 м/мин | ±5% толщины |
Профиль | 1-5 м/мин | ±0,2 мм в поперечном сечении |
Материальные соображения:
- ПВХ: 60% экструзионных применений
- ПНД: для напорных труб (номиналы PN10-PN25)
- TPE: профили Soft-touch
Пример из практики BFY Mold: Производство 12 км/месяц медицинских трубок с постоянным контролем ±0,05 мм ID.
3. Выдувное формование: Производство полых деталей
Вариации процесса
Экструзионно-выдувное формование
- Выдавливание из паролона
- Закрытие формы
- Надувание воздухом (0,3-0,7 МПа)
- Охлаждение (30-90 секунд)
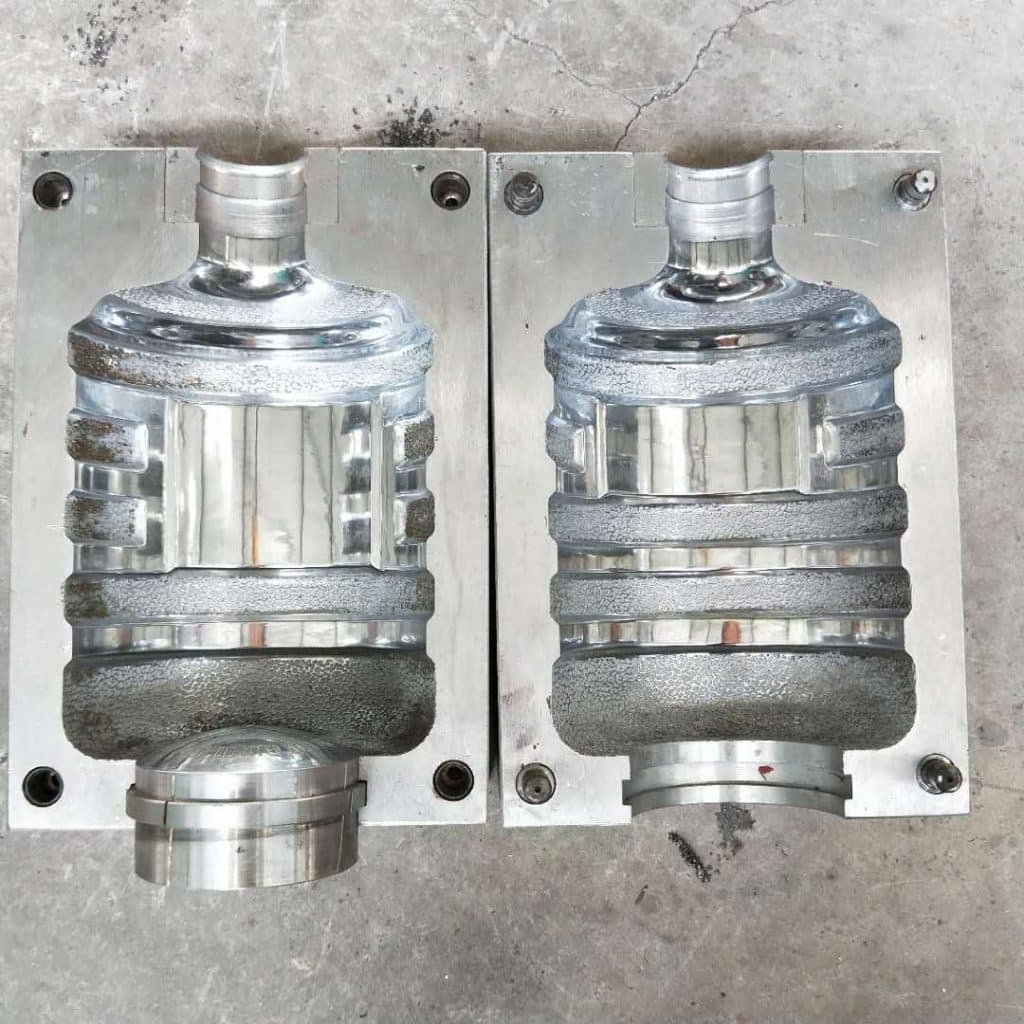
Выдувное формование под давлением
- Впрыск готовой формы
- Трансфер на станцию продувки
- Ориентация на растяжение и раздувание
Сравнительный анализ
Фактор | Экструзия BM | Инъекция BM |
Настенное управление | ±15% | ±8% |
Отделка шеи | Требуется обрезка | Качество инъекций |
Скорость выхода | 200-500/hr | 100-300/hr |
Руководство по выбору материала:
- ПЭТ: Бутылки для газированных напитков
- ПНД: контейнеры для химикатов
- PP: автомобильные воздуховоды
4. Ротационное формование: Большие бесшовные компоненты
График процесса
- Загрузка: Порошок отмеряется в форму (точность ±1%)
- Нагрев: Печь 300°C с двухосным вращением (6-12 об/мин)
- Охлаждение: Водяной спрей + воздушные фазы охлаждения
- Разгрузка: Ручное/автоматическое удаление деталей
Параметры конструкции
Размер детали | Вес пресс-формы | Время цикла |
<1m³ | 50-200kg | 20-40 минут |
1-5m³ | 200-800kg | 40-90 минут |
>5m³ | 800-3000kg | 2-4 часа |
Варианты материалов:
- Полиэтилен (90% применений)
- Нейлон (для топливных баков)
- ПВХ (оборудование для детских площадок)
5. Термоформование: Решения для тонкостенной упаковки
Технологический поток
- Подача листов: Подача рулонов или разрезанных листов
- Нагрев: Инфракрасные панели (150-200°C)
- Формование: Вакуум (0,5-0,9 бар) или давление (3-6 бар)
- Обрезка: Штампы со стальными ручками или фрезерные станки с ЧПУ
Метрики контроля качества
Тип дефекта | Метод профилактики | Инструмент для измерения |
Веревка | Оптимальное предварительное растяжение | 3D лазерный сканер |
Тонкие места | Контроль давления | Ультразвуковой толщиномер |
Деформация размеров | Регулируемая скорость охлаждения | CMM |
6. Компрессионное формование: Специализация по термореактивным материалам
Техническая последовательность
- Подготовка заготовок: Резка SMC/BMC
- Загрузка пресс-формы: Предварительный нагрев до 80-120°C
- Отверждение: 100-200 кг/см² в течение 2-15 минут
- После отверждения: 1-4 часа при 150°C (по желанию)
Свойства материала
Композитный тип | Содержание волокон | Прочность (МПа) |
SMC | 25-30% стекла | 80-120 |
BMC | 15-25% стекла | 40-70 |
GMT | 30-40% стекла | 100-150 |
7. Формование структурной пеной: Решение для облегчения веса
Характеристики процесса
- Снижение веса: 15-30% по сравнению с цельными деталями
- Отделка поверхности: Класс B SPI (текстурированная)
- Стабильность размеров: ±0,3% через 24 часа
Требования к оборудованию
Размер детали | Усилие зажима | Система впрыска газа |
<5kg | 50-100 тонн | Азот |
5-20kg | 100-300 тонн | Химический пенообразователь |
>20kg | 300-600 тонн | Гибридная система |
8. Вставное формование: Изготовление гибридных компонентов
Руководство по проектированию
- Материалы вставки: Нержавеющая сталь, латунь, керамика
- Выбор пластика: PPS для высоких температур, PEEK для химической стойкости
- Методы скрепления: Механические соединения предпочтительнее клеев
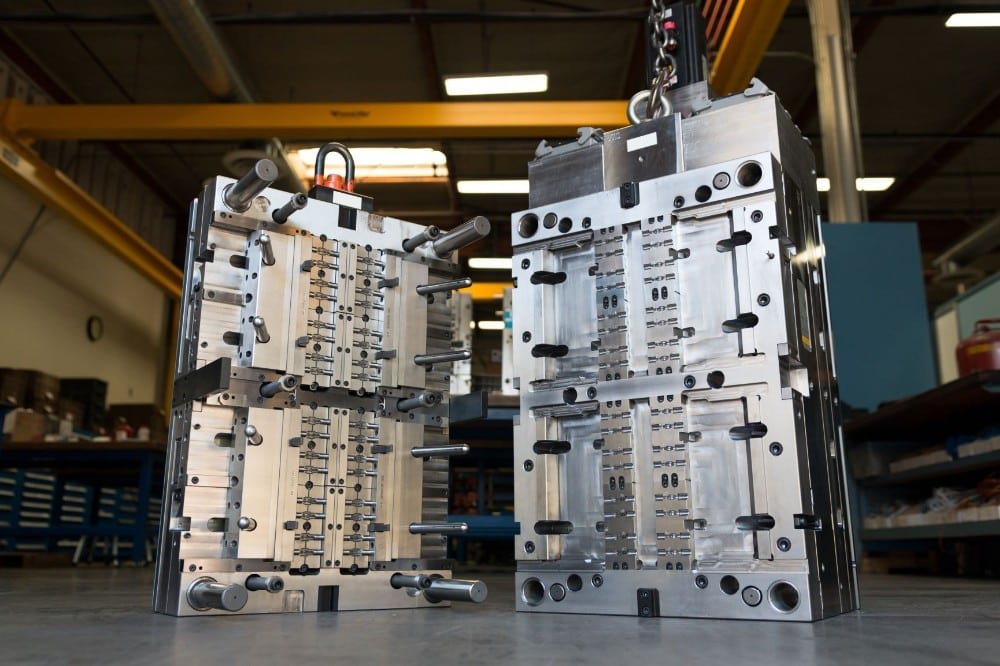
Стандарты качества
- Требования к испытаниям на растяжение: 50 Н минимум для медицинских изделий
- Электрическая непрерывность: Сопротивление <0,5 Ом для разъемов
- Герметичное уплотнение: Испытание на герметичность гелием <1×10^-6 мбар-л/с
Матрица выбора сравнительного процесса
Процесс | Экономический объем | Время изготовления инструмента | Варианты материалов | Точность размеров |
Инъекция | 10k+ | 4-8 недель | 200+ | ±0.005mm |
Экструзия | Непрерывный | 2-4 недели | 30 | ±0.1mm |
Продувка | 5k+ | 6-10 недель | 15 | ±0.2mm |
Вращение | 500+ | 3-5 недель | 10 | ±0.5mm |
10 часто задаваемых экспертами вопросов об услугах по литью пластмасс
Q1: Как выбрать между литьем под давлением и компрессионным литьем?
A: Инжекция для термопластов (более 1 000 единиц), компрессия для термореактивных материалов/композитов.
Q2: Какова минимальная толщина стенки для экструзии полиэтилена?
A: 0,1 мм для пленок, 0,5 мм для профилей.
Q3: Можно ли с помощью выдувного формования получить заниженные вырезы?
A: Ограничен углом тяги 5° без разборных сердечников.
Q4: Как уменьшить следы от раковин на толстых ребрах?
A: Поддерживайте соотношение ребер и стенок ≤60% и используйте газ-ассистент.
Q5: Какая обработка поверхности возможна при ротационном формовании?
A: Как правило, SPI C-1 — D-3, с копированием текстуры до 90%.
Q6: Насколько точна термоформовка по сравнению с литьем под давлением?
A: ±0,2 мм против ±0,05 мм на критических размерах.
Q7: Какой процесс обеспечивает самую быструю смену материала?
A: Термоформование (15-30 минут между материалами).
Q8: Какую самую большую деталь можно изготовить из конструкционной пены?
A: До 4 м×2,5 м×1 м при использовании 600-тонных прессов.
Q9: Как проверить прочность соединения вставки с формовочным материалом?
A: Испытание на отрыв по стандарту ASTM D4541 при 23°C и 85°C.
Q10: Почему стоит сотрудничать с BFY Mold в области литья пластмасс?
- 50+ формовочных систем от 5-600 тонн
- Собственное производство со средним сроком изготовления 25 дней
- Материаловедческая лаборатория для тестирования рецептур