giriiş
Kalıp mühendisinin odaklanması gereken faktörlerden biri, enjeksiyon kalıplama verimliliğini ve ürün kalitesini doğrudan etkileyen kalıbın stabilitesidir. Kalıplardaki dengesizlik çarpılma, parlama ve erken aşınma gibi termal kusurlara neden olarak üretim maliyetlerini ve duruş sürelerini artırır. İster termal yorgunluk, ister malzeme tutarsızlıkları veya hizalama sorunları ile mücadele ediyor olun, güçlü kalıp performansı elde etmek tasarım hassasiyeti, malzeme bilimi ve bakım protokolleri arasında bir denge gerektirir. Bu makalede, sofistike soğutma kanalı iyileştirmelerinden alaşım geliştirmelerine ve gerçek zamanlı izlemeye kadar, üreticileri kalıp stabilitesini artırmaya, engelsiz çıktıyı korumaya ve kalıp ömrünü %40 oranında uzatmaya yardımcı olacak 7 kanıtlanmış strateji paylaşılmaktadır.
Üretim uygulamasında, bazı kalıplar üretim hattında kullanılmaya başlandıktan sonra, genellikle çeşitli sorunlara neden olur, ürünün üretim gereksinimlerini veya teknik gereksinimlerini karşılayamaz, üretim hattında anormal kapanmalara vb. neden olur ve birçok dengesiz faktörü beraberinde getirir. Bu nedenle, kalıbın stabilitesinin nasıl iyileştirileceği, kalıp imalat şirketlerinin karşılaştığı pratik bir sorun haline gelmiştir.
Kalıpların tasarımı ve üretiminde, tasarımcıların deneyim ve becerileri kilit bir rol oynar. Tasarımın makul olup olmadığı ancak kalıp testi ile teyit edilebilir ve kalıp, nihayet tamamlanmadan önce birden fazla kalıp testi ve tekrarlanan modifikasyonlar gerektirir. Üretim pratiğinde, bazı kalıplar üretim hattında kullanılmaya başlandığında, genellikle çeşitli sorunlara neden olur, ürünün üretim gereksinimlerini veya teknik gereksinimlerini karşılayamaz, üretim hattında anormal kapanmalara vb. neden olur ve birçok dengesiz faktörü beraberinde getirir. Bu nedenle, kalıbın stabilitesinin nasıl iyileştirileceği, kalıp imalat şirketlerinin karşılaştığı pratik bir sorun haline gelmiştir.
Damgalama şekillendirme ve etkileyen faktörler
Stabilite nedir? İstikrar, süreç istikrarı ve üretim istikrarı olarak ikiye ayrılır. Süreç istikrarı, nitelikli ürünlerin istikrarlı üretimi için gereksinimleri karşılayan süreç planını ifade eder; üretim istikrarı ise üretim sırasında istikrarlı üretim kapasitesini ifade eder.
İlk olarak, kalıpların stabilite kalıplamasını ve damgalama şekillendirmesini etkileyen ana faktörleri açıklayacağız. Kalıp malzemelerinin özelliklerini, kalıpların yapısal bileşenlerinin mukavemetini, damgalama malzemelerinin performansının stabilitesini, malzemelerin kalınlığının dalgalanma özelliklerini, malzemelerin değişen aralığını, çekme nervürü direncinin verilerini, boş tutucu kuvvetinin değişen aralığını içerir; yağlayıcıların seçimi.
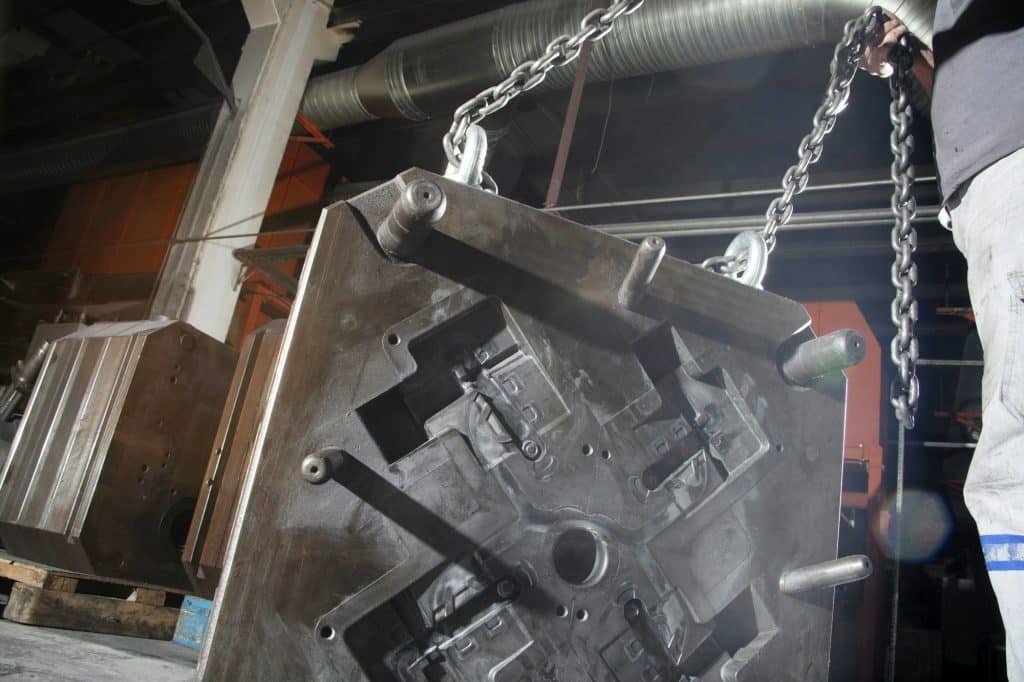
İstikrarı etkileyen çeşitli faktörleri kapsamlı bir şekilde tartın
Malzeme Değişkenliğinin Zorlukları
Damgalama şekillendirme işlemi sırasında, her damgalama tabakasının kimyasal bileşimi, mekanik özellikleri ve damgalama performansı ile yakından ilgili karakteristik değerleri olduğundan, damgalama malzemesinin performansının kararsız olduğunu, damgalama malzemesinin kalınlığının dalgalandığını ve Damgalama malzemelerindeki değişiklikler sadece damgalama şekillendirme işleminin doğruluğunu ve kalitesini doğrudan etkilemekle kalmaz, aynı zamanda kalıbın hasar görmesine de neden olabilir.
Gerdirerek Şekillendirmede Çekme Nervürlerinin Önemi
Çekme nervürleri örnek olarak ele alındığında, damgalama şekillendirmede kritik bir konuma sahiptirler. Germe şekillendirme işlemi sırasında, ürünün şekillendirilmesi, sabit çevre boyunca düzgün bir şekilde dağıtılan belirli bir miktarda çekme kuvveti gerektirir. Bu çekme kuvveti, damgalama ekipmanının kuvvetinden, kenar malzemesinin deformasyon direncinden ve işlenmemiş parça tutucu yüzeyindeki akış direncinden kaynaklanır. Akış direnci sadece işlenmemiş parça tutucu kuvveti tarafından oluşturulursa, kalıp ve malzeme arasındaki sürtünme yetersizdir.
Plastik Deformasyon için Direnci Optimize Etme
Bu nedenle, beslemenin direncini artırmak ve böylece malzemenin plastik deformasyon ve plastik akış gereksinimlerini karşılamak için malzemenin daha büyük plastik deformasyonuna neden olmak için işlenmemiş parça tutucusu üzerinde daha fazla direnç üretebilen çekme nervürleri ayarlamak gerekir. Aynı zamanda, çekme nervürlerinin direncinin boyutunu ve dağılımını değiştirerek ve kalıba akan malzemenin hızını ve besleme miktarını kontrol ederek, çekme kuvveti ve çekme parçasının her bir deformasyon alanındaki dağılımı, gerilmeyi önlemek için etkili bir şekilde ayarlanabilir. Kalite sorunları arasında çatlama, buruşma ve kalıplama sırasında ürün deformasyonu yer alır.
Damgalama Süreci ve Kalıp Tasarımında Dikkat Edilecek Hususlar
Yukarıdan görülebileceği üzere, damgalama işleminin ve kalıp tasarımının formüle edilmesi sürecinde, çekme direncinin boyutu dikkate alınmalı, çekme nervürleri düzenlenmeli ve çekme nervürlerinin şekli, her bir deformasyon alanının gerekli olana göre deforme edilebilmesi için işlenmemiş parça tutucu kuvvetinin değişim aralığına göre düzenlenmelidir.

İşte kalıbın sağlamlığını artıracak 14 ipucu:
1. Malzeme Seçimi:
Kalıp yapımı için kalıplama sürecindeki gerilimlere ve sıcaklıklara dayanabilecek yüksek kaliteli malzemeler seçin.
2. Uygun Tasarım:
Kalıp tasarımının sağlam olduğundan ve malzeme akışı, soğutma ve parça fırlatma gibi faktörleri dikkate aldığından emin olun. İyi tasarlanmış bir kalıbın üretim süreci boyunca stabilitesini koruması daha olasıdır.
3. Kalıp Soğutma:
Kalıbın sıcaklığını düzenlemek için etkili bir soğutma sistemi uygulayın. Doğru soğutma çarpılmayı önlemeye yardımcı olur, döngü sürelerini azaltır ve genel stabiliteyi artırır.
4. Düzgün Duvar Kalınlığı:
Tutarlı soğutma sağlamak ve kalıp üzerinde eşit olmayan gerilme riskini azaltmak için kalıplanan parçada eşit duvar kalınlığı sağlayın.
5. Havalandırma:
Kalıplama işlemi sırasında hava ve gazların salınmasına izin vermek için yeterli havalandırma sağlayın. Yetersiz havalandırma, kalıbın stabilitesini etkileyebilecek hava tuzaklarına yol açabilir.
6. Yüzey İşlemi:
Kalıbın yüzey kalitesine dikkat edin. Pürüzsüz ve cilalı bir yüzey sürtünmeyi ve aşınmayı azaltarak kalıp stabilitesine ve uzun ömürlülüğe katkıda bulunur.
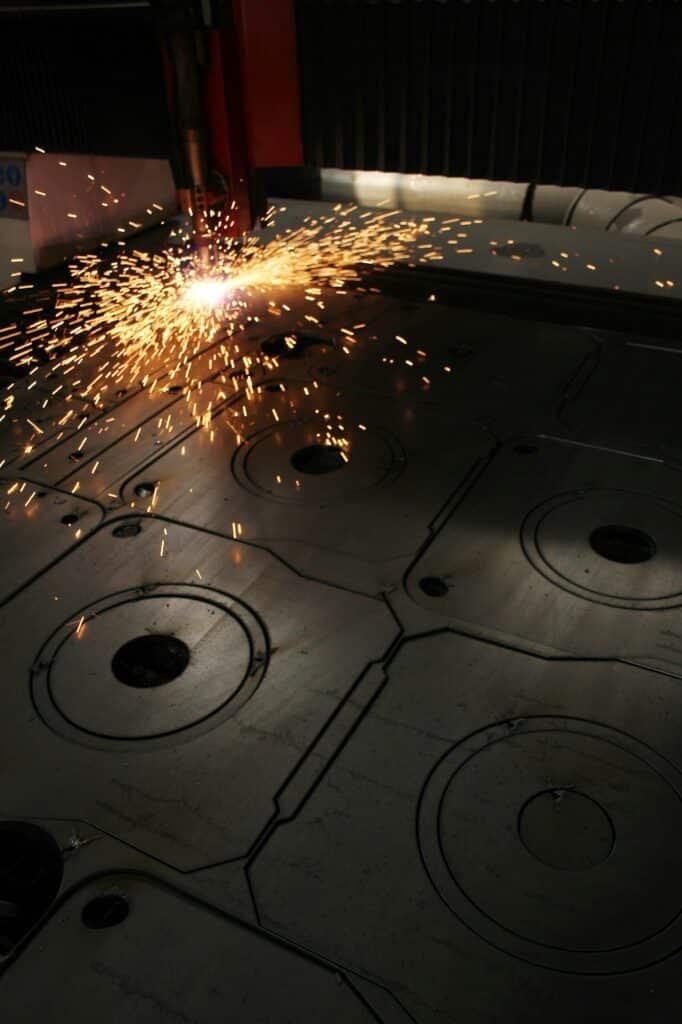
7. Kalıp Bakımı:
Kalıbı aşınma, hasar veya diğer sorunlara karşı düzenli olarak inceleyin ve bakımını yapın. Sorunların artmasını ve stabiliteyi etkilemesini önlemek için sorunları derhal ele alın.
8. Uygun Enjeksiyon Parametreleri:
Malzemenin kalıp boşluğu boyunca düzgün ve eşit bir şekilde akmasını sağlamak için sıcaklık, basınç ve hız gibi enjeksiyon kalıplama parametrelerini optimize edin.
9. Kalıp Uçlarının Kullanımı:
Kalıp içindeki belirli alanların dayanıklılığını ve stabilitesini artırmak için kritik özellikler için kalıp ekleri ekleyin.
10. Kalıp Desteği ve Hizalama:
Kalıbın kalıplama makinesi içinde uygun şekilde desteklendiğinden ve hizalandığından emin olun. Yanlış hizalama veya yetersiz destek dengesizliğe ve erken aşınmaya yol açabilir.
11. Kalıp Malzemesi Sertliği:
Kalıp malzemesinin sertliğini göz önünde bulundurun. Daha sert bir kalıp malzemesi aşınmaya daha iyi direnç gösterebilir ancak kırılganlık gibi faktörlerle dengelenmelidir.
12. İzleme ve Kontrol:
Kalıp sıcaklığı, basınç ve diğer ilgili parametreleri izlemek için izleme sistemleri uygulayın. Bu, stabiliteyi korumak için gerçek zamanlı ayarlamalara olanak tanır.
13. İleri Teknolojiler:
Kalıbın stabilitesini ve genel verimliliği artırmak için sensörler, kestirimci bakım ve otomasyon gibi gelişmiş teknolojileri keşfedin.
14. Uzmanlara Danışın:
Mümkünse, kalıp tasarımınızın ve üretim süreçlerinizin stabilite için optimize edildiğinden emin olmak için kalıp tasarımı ve üretim uzmanlarına danışın.
Bu önlemleri alarak kalıbınızın stabilitesini artırabilir ve daha verimli ve güvenilir bir üretim sürecine katkıda bulunabilirsiniz.
Kalıp tasarımına ihtiyacınız varsa, lütfen BFY Mold ile iletişime geçin. Kalıp çizimlerini sizin için ücretsiz olarak optimize edebilir, maliyetlerinizi düşürebilir, kalıbın stabilitesini sağlayabilir ve üretim verimliliğinizi artırabiliriz.