Introduction
One factor the tooling engineer must focus on is the stability of the mold, which directly impacts injection molding efficiency and product quality. Instability in the molds causes thermal defects such as warping, flash, and early wear, increasing production costs and downtime. Whether you’re struggling with thermal fatigue, material inconsistencies, or alignment issues, getting strong mold performance demands a balance of design precision, material science, and maintenance protocols. This article shares 7 proven strategies—from sophisticated cooling channel improvements to alloy enhancements and real-time monitoring—that equip manufacturers to help increase mold stability, maintain unobstructed output, and prolong tooling life by 40% increase.
In production practice, once some molds are put into use on the production line, they often cause various problems, fail to meet the production requirements or technical requirements of the product, cause abnormal shutdowns of the production line, etc., and bring many unstable factors. Therefore, how to improve the stability of the mold has become a practical problem faced by mold manufacturing companies.
In the design and manufacturing of molds, the experience and skills of designers play a key role. Whether the design is reasonable or not can only be confirmed through mold testing, and the mold requires multiple mold testing and repeated modifications before it is finally completed. In production practice, once some molds are put into use on the production line, they often cause various problems, fail to meet the production requirements or technical requirements of the product, cause abnormal shutdowns of the production line, etc., and bring many unstable factors. Therefore, how to improve the stability of mold has become a practical problem faced by mold manufacturing companies.
Stamping forming and its influencing factors
What is stability? Stability is divided into process stability and production stability. Process stability refers to the process plan that meets the requirements for stable production of qualified products; production stability refers to stable production capacity during production.
First, we will explain the main factors affecting the stability molding of molds and stamping forming. It includes the specifications of mold materials, the strength of structural components of molds, the stability of the performance of the stamping materials, the fluctuation characteristics of the thickness of the materials, the changing range of the materials, the data of the tensile rib resistance, the changing range of the blank holder force; the selection of lubricants.
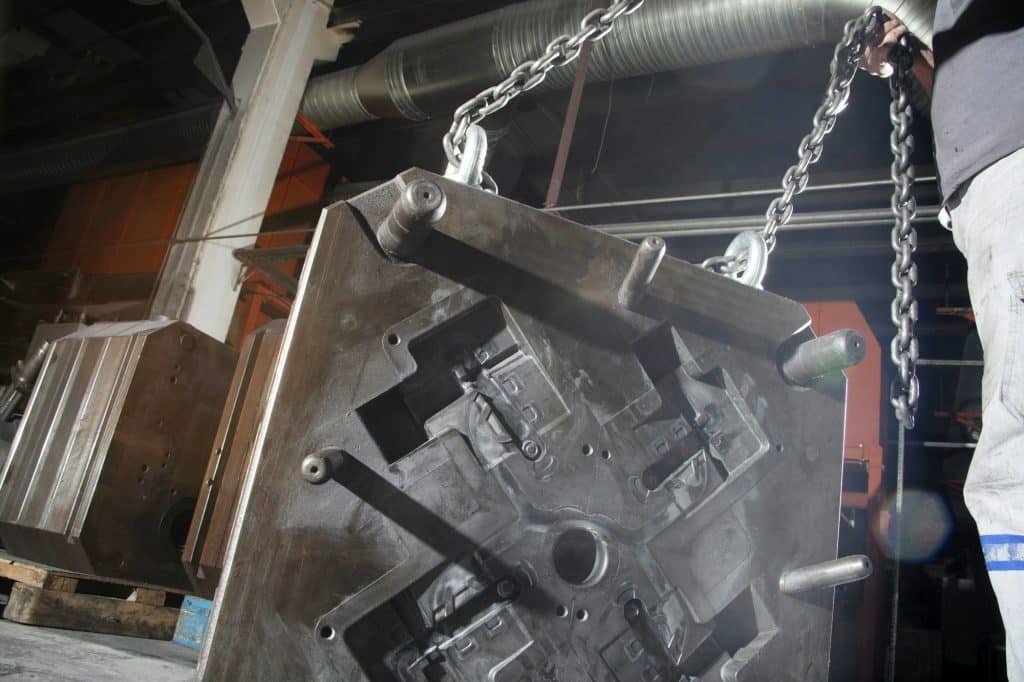
Comprehensively weigh various factors affecting stability
Challenges of Material Variability
It is worth noting that during the stamping forming process, since each stamping sheet has its chemical composition, mechanical properties, and characteristic values closely related to the stamping performance, the performance of the stamping material is unstable, the thickness of the stamping material fluctuates, and Changes in stamping materials not only directly affect the accuracy and quality of stamping forming processing, but may also cause damage to the mold.
Importance of Tensile Ribs in Stretch Forming
Taking tensile ribs as an example, they occupy a critical position in stamping forming. During the stretch forming process, the forming of the product requires a certain amount of pulling force that is properly distributed along the fixed periphery. This pulling force comes from the force of the stamping equipment, the deformation resistance of the edge material, and the flow resistance on the blank holder surface. The friction between the mold and the material is insufficient if the flow resistance is generated only by the blank holder force.
Optimizing Resistance for Plastic Deformation
For this reason, it is necessary to set tensile ribs that can produce greater resistance on the blank holder to increase the resistance of the feed, thereby causing greater plastic deformation of the material to meet the requirements of plastic deformation and plastic flow of the material. At the same time, by changing the size and distribution of the resistance of the tensile ribs and controlling the speed and feed amount of the material flowing into the mold, the tensile force and its distribution in each deformation area of the tensile part can be effectively adjusted to prevent stretching. Quality problems include cracking, wrinkling, and product deformation during molding.
Considerations in Stamping Process and Mold Design
It can be seen from the above that in the process of formulating the stamping process and mold design, the size of the tensile resistance must be considered, the tensile ribs should be arranged, and the form of the tensile ribs should be arranged according to the variation range of the blank holder force so that each deformation area can be deformed according to the required The shape and degree of deformation are completed.

Here are 14 tips to enhance the stability of the mold:
1. Material Selection:
Choose high-quality materials for the mold construction that can withstand the stresses and temperatures involved in the molding process.
2. Proper Design:
Ensure the mold design is robust and takes into account factors such as material flow, cooling, and part ejection. A well-designed mold is more likely to maintain stability during the production process.
3. Mold Cooling:
Implement an effective cooling system to regulate the temperature of the mold. Proper cooling helps prevent warping, reduces cycle times, and enhances overall stability.
4. Uniform Wall Thickness:
Maintain uniform wall thickness in the molded part to ensure consistent cooling and reduce the risk of uneven stresses on the mold.
5. Venting:
Provide adequate venting to allow for the release of air and gases during the molding process. Insufficient venting can lead to air traps, which can impact the stability of the mold.
6. Surface Finish:
Pay attention to the surface finish of the mold. A smooth and polished surface reduces friction and wear, contributing to mold stability and longevity.
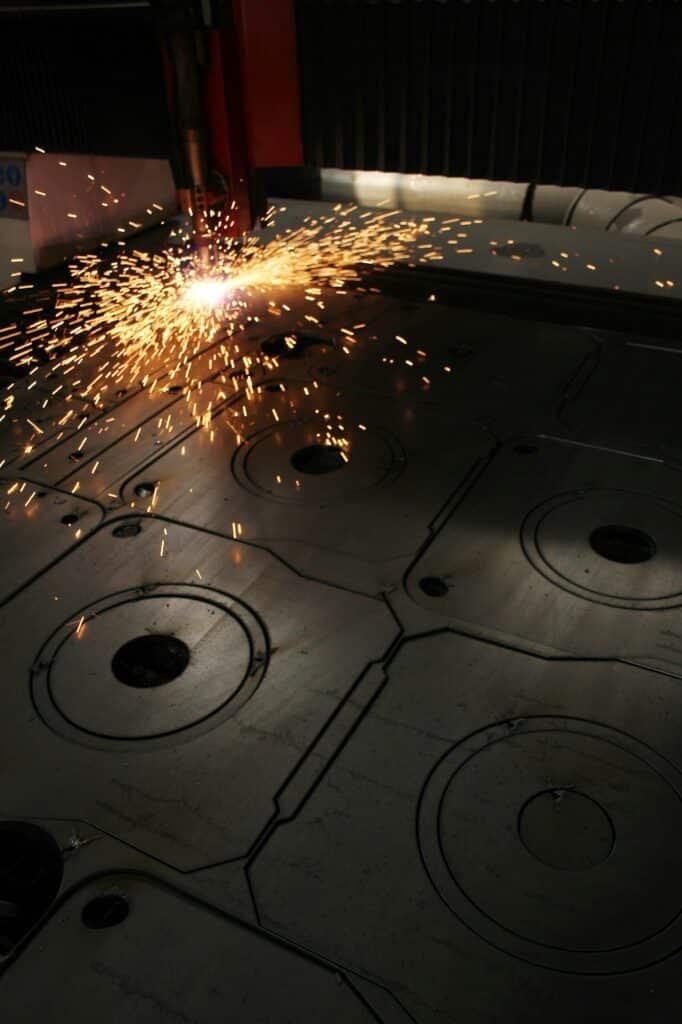
7. Mold Maintenance:
Regularly inspect and maintain the mold for signs of wear, damage, or other issues. Promptly address any problems to prevent them from escalating and affecting stability.
8. Proper Injection Parameters:
Optimize injection molding parameters such as temperature, pressure, and speed to ensure the material flows smoothly and evenly throughout the mold cavity.
9. Use of Mold Inserts:
Incorporate mold inserts for critical features to improve the durability and stability of specific areas within the mold.
10. Mold Support and Alignment:
Ensure proper support and alignment of the mold within the molding machine. Misalignment or inadequate support can lead to instability and premature wear.
11. Mold Material Hardness:
Consider the hardness of the mold material. A harder mold material may resist wear better but should be balanced with factors like brittleness.
12. Monitoring and Control:
Implement monitoring systems to track mold temperature, pressure, and other relevant parameters. This allows for real-time adjustments to maintain stability.
13. Advanced Technologies:
Explore advanced technologies such as sensors, predictive maintenance, and automation to enhance the stability of the mold and overall efficiency.
14. Consult with Experts:
If possible, consult with mold design and manufacturing experts to ensure that your mold design and production processes are optimized for stability.
By incorporating these measures, you can improve the stability of your mold and contribute to a more efficient and reliable manufacturing process.
If you need mold design, please contact BFY Mold. We can optimize the mold drawings for you for free, reduce your costs, ensure the stability of the mold, and improve your production efficiency.