Einführung
Ein Faktor, auf den sich der Werkzeugtechniker konzentrieren muss, ist die Stabilität der Form, die sich direkt auf die Effizienz des Spritzgießens und die Produktqualität auswirkt. Instabilität in den Formen führt zu thermischen Defekten wie Verformung, Gratbildung und frühzeitigem Verschleiß, was die Produktionskosten und Ausfallzeiten erhöht. Ganz gleich, ob Sie mit thermischer Ermüdung, Materialinkonsistenzen oder Ausrichtungsproblemen zu kämpfen haben – um eine hohe Formleistung zu erzielen, ist ein ausgewogenes Verhältnis von Konstruktionspräzision, Materialwissenschaft und Wartungsprotokollen erforderlich. In diesem Artikel werden 7 bewährte Strategien vorgestellt – von ausgeklügelten Kühlkanalverbesserungen über Legierungsverbesserungen bis hin zur Echtzeitüberwachung -, mit denen Hersteller die Stabilität ihrer Formen erhöhen, den Ausstoß ungehindert aufrechterhalten und die Lebensdauer der Werkzeuge um 40 % verlängern können.
In der Produktionspraxis verursachen einige Formen, sobald sie in der Produktionslinie eingesetzt werden, oft verschiedene Probleme, entsprechen nicht den Produktionsanforderungen oder den technischen Anforderungen des Produkts, verursachen anormale Stillstände der Produktionslinie usw. und bringen viele instabile Faktoren mit sich. Daher ist die Frage, wie die Stabilität der Form verbessert werden kann, zu einem praktischen Problem geworden, mit dem sich die Unternehmen des Formenbaus konfrontiert sehen.
Bei der Konstruktion und Herstellung von Formen spielen die Erfahrung und die Fähigkeiten der Konstrukteure eine entscheidende Rolle. Ob der Entwurf vernünftig ist oder nicht, kann nur durch Formtests bestätigt werden, und die Form erfordert mehrere Formtests und wiederholte Änderungen, bevor sie schließlich fertiggestellt wird. In der Produktionspraxis verursachen einige Formen, sobald sie in der Produktionslinie eingesetzt werden, oft verschiedene Probleme, entsprechen nicht den Produktionsanforderungen oder den technischen Anforderungen des Produkts, führen zu anormalen Stillständen der Produktionslinie usw. und bringen viele instabile Faktoren mit sich. Daher ist die Frage, wie die Stabilität der Form verbessert werden kann, zu einem praktischen Problem geworden, mit dem sich die Unternehmen des Formenbaus konfrontiert sehen.
Stanzformgebung und ihre Einflussfaktoren
Was ist Stabilität? Stabilität wird in Prozessstabilität und Produktionsstabilität unterteilt. Prozessstabilität bezieht sich auf den Prozessplan, der die Anforderungen für eine stabile Produktion qualifizierter Produkte erfüllt; Produktionsstabilität bezieht sich auf eine stabile Produktionskapazität während der Produktion.
Zunächst werden die wichtigsten Faktoren erläutert, die sich auf die Stabilität des Formenbaus und der Stanzformgebung auswirken. Dazu gehören die Spezifikationen der Formenmaterialien, die Festigkeit der strukturellen Komponenten der Formen, die Stabilität der Leistung der Stanzmaterialien, die Schwankungseigenschaften der Dicke der Materialien, der Änderungsbereich der Materialien, die Daten des Zugrippenwiderstands, der Änderungsbereich der Rohlingshaltekraft; die Auswahl der Schmiermittel.
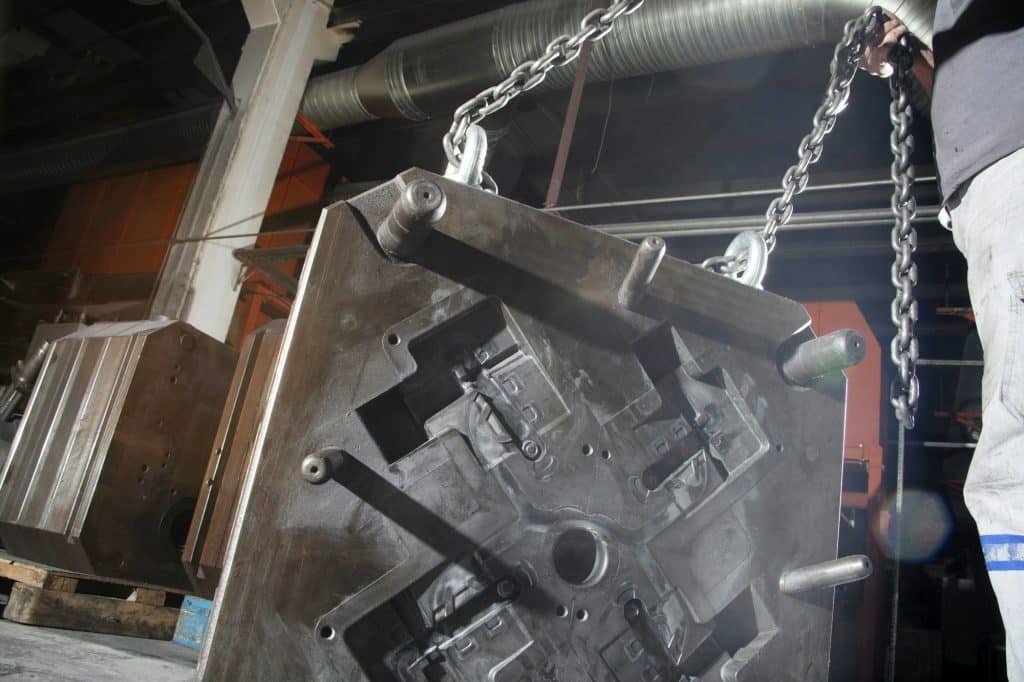
Umfassende Abwägung verschiedener Faktoren, die die Stabilität beeinflussen
Herausforderungen der Materialvariabilität
Es ist erwähnenswert, dass während des Stanzprozesses, da jedes Stanzblech seine chemische Zusammensetzung, mechanischen Eigenschaften und charakteristischen Werte hat, die in engem Zusammenhang mit der Stanzleistung stehen, die Leistung des Stanzmaterials instabil ist, die Dicke des Stanzmaterials schwankt und Veränderungen im Stanzmaterial nicht nur direkte Auswirkungen auf die Genauigkeit und Qualität der Stanzformverarbeitung haben, sondern auch Schäden an der Form verursachen können.
Die Bedeutung von Zugrippen beim Streckziehen
Am Beispiel der Zugrippen lässt sich zeigen, dass sie eine kritische Position bei der Stanzformung einnehmen. Während des Streckziehverfahrens erfordert die Umformung des Produkts eine gewisse Zugkraft, die ordnungsgemäß entlang des festen Umfangs verteilt ist. Diese Zugkraft ergibt sich aus der Kraft der Stanzeinrichtung, dem Verformungswiderstand des Kantenmaterials und dem Fließwiderstand auf der Oberfläche des Niederhalters. Die Reibung zwischen der Form und dem Material ist nicht ausreichend, wenn der Fließwiderstand nur durch die Kraft des Niederhalters erzeugt wird.
Optimierung des Widerstands gegen plastische Verformung
Aus diesem Grund ist es notwendig, Zugrippen einzustellen, die einen größeren Widerstand auf dem Rohlingshalter erzeugen können, um den Widerstand des Vorschubs zu erhöhen und dadurch eine größere plastische Verformung des Materials zu bewirken, um die Anforderungen an die plastische Verformung und den plastischen Fluss des Materials zu erfüllen. Gleichzeitig können durch Änderung der Größe und Verteilung des Widerstands der Zugrippen und durch Steuerung der Geschwindigkeit und der Vorschubmenge des in die Form fließenden Materials die Zugkraft und ihre Verteilung in jedem Verformungsbereich des Zugteils wirksam eingestellt werden, um eine Dehnung zu verhindern. Zu den Qualitätsproblemen gehören Rissbildung, Faltenbildung und Produktverformung während des Formens.
Überlegungen zum Stanzprozess und zur Formgestaltung
Aus den obigen Ausführungen ist ersichtlich, dass bei der Formulierung des Stanzprozesses und der Formgestaltung die Größe des Zugwiderstandes berücksichtigt werden muss, die Zugrippen angeordnet werden sollten und die Form der Zugrippen entsprechend dem Variationsbereich der Niederhalterkraft so angeordnet werden sollte, dass jeder Verformungsbereich entsprechend der erforderlichen Form und dem Verformungsgrad verformt werden kann.

Hier sind 14 Tipps zur Verbesserung der Stabilität der Form:
1. Auswahl des Materials:
Wählen Sie für die Konstruktion der Gussform hochwertige Materialien, die den Belastungen und Temperaturen beim Gussprozess standhalten können.
2. Richtiges Design:
Stellen Sie sicher, dass die Formkonstruktion robust ist und Faktoren wie Materialfluss, Kühlung und Teileauswurf berücksichtigt werden. Eine gut konstruierte Form behält während des Produktionsprozesses mit größerer Wahrscheinlichkeit ihre Stabilität.
3. Kühlung der Form:
Implementieren Sie ein effektives Kühlsystem, um die Temperatur der Form zu regulieren. Eine ordnungsgemäße Kühlung hilft, Verformungen zu vermeiden, verkürzt die Zykluszeiten und erhöht die allgemeine Stabilität.
4. Gleichmäßige Wanddicke:
Behalten Sie eine gleichmäßige Wandstärke im Formteil bei, um eine gleichmäßige Abkühlung zu gewährleisten und das Risiko einer ungleichmäßigen Belastung der Form zu verringern.
5. Entlüftung:
Sorgen Sie für ausreichende Entlüftung, damit Luft und Gase während des Formprozesses entweichen können. Unzureichende Entlüftung kann zu Lufteinschlüssen führen, die die Stabilität der Form beeinträchtigen können.
6. Oberflächengüte:
Achten Sie auf die Oberflächenbeschaffenheit der Form. Eine glatte und polierte Oberfläche verringert Reibung und Verschleiß und trägt zur Stabilität und Langlebigkeit der Form bei.
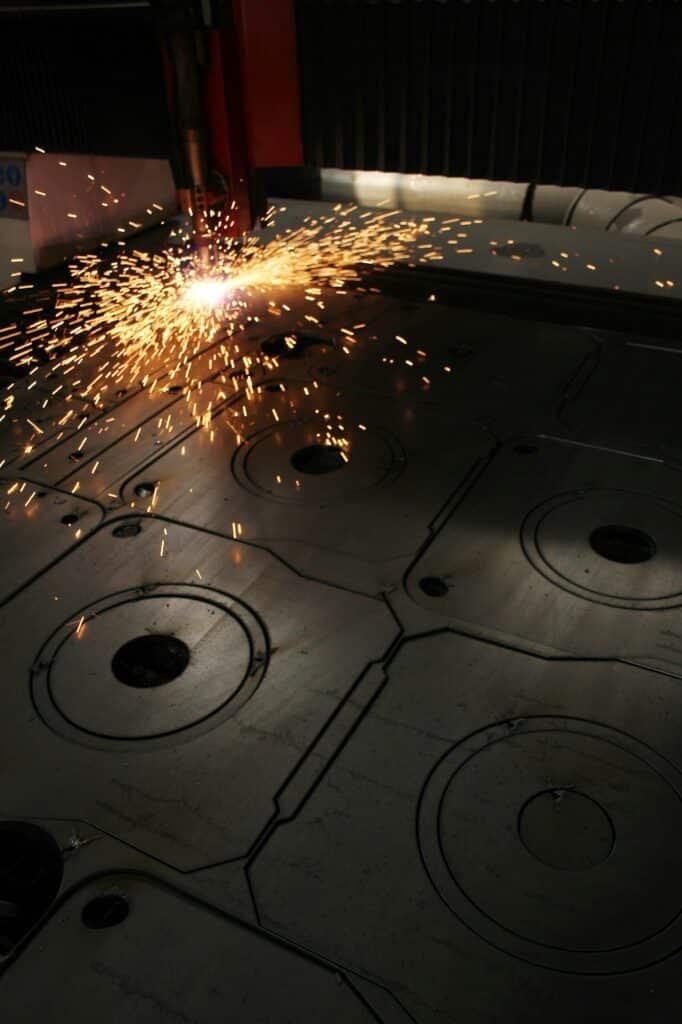
7. Wartung von Schimmelpilzen:
Regelmäßige Inspektion und Wartung der Form auf Anzeichen von Verschleiß, Schäden oder anderen Problemen. Kümmern Sie sich umgehend um alle Probleme, um zu verhindern, dass sie eskalieren und die Stabilität beeinträchtigen.
8. Richtige Injektionsparameter:
Optimieren Sie Spritzgießparameter wie Temperatur, Druck und Geschwindigkeit, um sicherzustellen, dass das Material gleichmäßig durch den Formhohlraum fließt.
9. Verwendung von Formeinsätzen:
Integrieren Sie Formeinsätze für kritische Merkmale, um die Haltbarkeit und Stabilität bestimmter Bereiche in der Form zu verbessern.
10. Unterstützung und Ausrichtung der Form:
Achten Sie auf die richtige Abstützung und Ausrichtung der Form in der Formmaschine. Eine falsche Ausrichtung oder unzureichende Unterstützung kann zu Instabilität und vorzeitigem Verschleiß führen.
11. Formstoffhärte:
Berücksichtigen Sie die Härte des Formmaterials. Ein härteres Formmaterial kann dem Verschleiß besser widerstehen, sollte aber gegen Faktoren wie Sprödigkeit abgewogen werden.
12. Überwachung und Kontrolle:
Implementieren Sie Überwachungssysteme, um die Formtemperatur, den Druck und andere relevante Parameter zu überwachen. Dies ermöglicht Anpassungen in Echtzeit, um die Stabilität zu erhalten.
13. Fortgeschrittene Technologien:
Entdecken Sie fortschrittliche Technologien wie Sensoren, vorausschauende Wartung und Automatisierung, um die Stabilität der Form und die Gesamteffizienz zu verbessern.
14. Beratung mit Experten:
Ziehen Sie, wenn möglich, Experten für Werkzeugkonstruktion und -herstellung zu Rate, um sicherzustellen, dass Ihre Werkzeugkonstruktion und Ihre Produktionsprozesse für Stabilität optimiert sind.
Durch diese Maßnahmen können Sie die Stabilität Ihrer Form verbessern und zu einem effizienteren und zuverlässigeren Herstellungsprozess beitragen.
Wenn Sie eine Formkonstruktion benötigen, wenden Sie sich bitte an BFY Mold. Wir optimieren die Formzeichnungen kostenlos für Sie, senken Ihre Kosten, gewährleisten die Stabilität der Form und verbessern Ihre Produktionseffizienz.