Introducción al moldeo de plásticos
El moldeo de plásticos transforma materiales poliméricos en componentes funcionales mediante diversas técnicas de fabricación. En BFY Mold, estamos especializados en ocho procesos básicos que sirven a industrias que van desde los dispositivos médicos hasta la fabricación de automóviles. Esta completa guía examina los parámetros técnicos, las aplicaciones ideales y las consideraciones económicas de cada método para ayudarle a seleccionar los servicios de moldeo de plástico.

1. Moldeo por inyección: El caballo de batalla de la alta precisión
Detalles del proceso
- Preparación del material: Secado (2-4 horas a 80°C para resinas higroscópicas)
- Fase de fusión: Rotación del tornillo a 150-400°C (depende del material)
- Inyección: 50-200MPa de presión en moldes de acero/aluminio
- Enfriamiento: 15-60 segundos (depende del grosor de la pared)
- Expulsión: Extracción robotizada automatizada
Especificaciones técnicas
Parámetro | Gama | Norma del sector |
Duración del ciclo | 15-120 segundos | ISO 294 |
Tol dimensional. | ±0.005-0.05mm | ASME Y14.5 |
Vida del moho | 500k-1M ciclos | SPI CLASE 101-104 |
Aplicaciones:
- Medicina: carcasas para instrumentos quirúrgicos (conforme a ISO 13485)
- Automoción: Componentes de revestimiento interior (certificado IATF 16949)
- Electrónica: Carcasas de conectores con paredes de 0,2 mm de grosor
Ventajas:
- Alta repetibilidad (CpK >1,67 alcanzable)
- Posibilidad de geometrías complejas
- Opciones multimaterial mediante coinyección
Limitaciones:
- Elevada inversión inicial en utillaje (15.000-250.000 dólares)
- Viabilidad económica limitada por debajo de 1.000 unidades
2. Moldeo por extrusión: Producción continua de perfiles
Desglose del proceso
- Alimentación: Los gránulos entran en el barril a un ritmo controlado
- Plastificación: Fundición monohusillo a 150-275°C
- Formación de la matriz: Forma determinada por la geometría de la herramienta
- Refrigeración: Mesas de calibración con dimensionamiento por vacío
- Corte: Sierras volantes para controlar la longitud
Métricas clave de rendimiento
Tipo de salida | Velocidad | Tolerancia |
Tubos | 2-10 m/min | ±0,1% de diámetro |
Hoja/Película | 5-50 m/min | ±5% de grosor |
Perfil | 1-5 m/min | ±0,2 mm de sección transversal |
Consideraciones materiales:
- PVC: 60% de las aplicaciones de extrusión
- HDPE: Para tuberías a presión (PN10-PN25)
- TPE: Perfiles de tacto suave
Estudio de caso sobre moldes BFY: Producción de 12 km/mes de tubos médicos con un control constante de ±0,05 mm de diámetro interior.
3. Moldeo por soplado: Fabricación de piezas huecas
Variaciones del proceso
Extrusión Soplado
- Extrusión de parisón
- Cierre del molde
- Inflado con aire (0,3-0,7MPa)
- Enfriamiento (30-90 segundos)
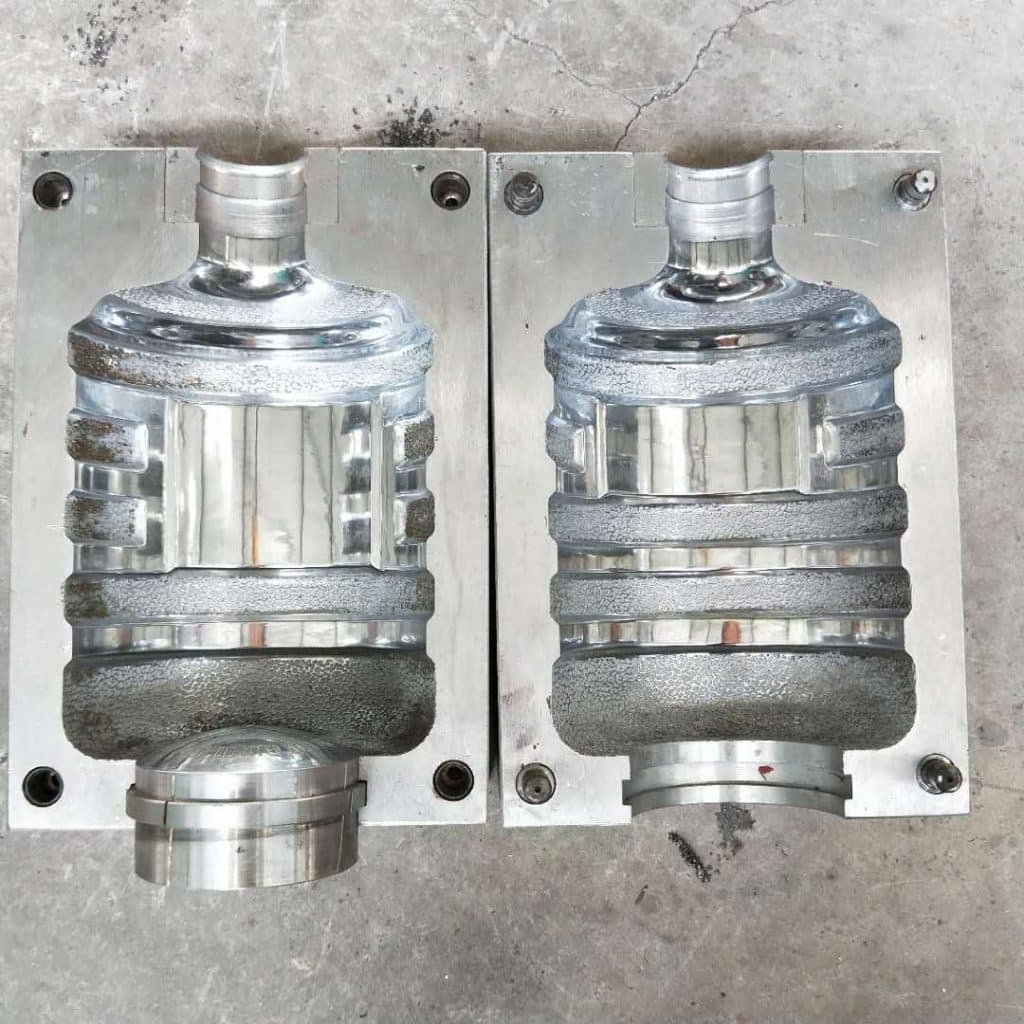
Moldeo por inyección-soplado
- Inyección de preformas
- Traslado a la estación de soplado
- Orientación estiramiento-soplado
Análisis comparativo
Factor | Extrusión BM | Inyección BM |
Control de pared | ±15% | ±8% |
Acabado del cuello | Requiere recorte | Calidad de inyección |
Tasa de salida | 200-500/hr | 100-300/hr |
Guía de selección de materiales:
- PET: Botellas de bebidas gaseosas
- HDPE: Contenedores químicos
- PP: Conductos para automóviles
4. Moldeo rotacional: Componentes grandes y sin costuras
Calendario del proceso
- Carga: Polvo medido en el molde (±1% de precisión)
- Calentamiento: Horno a 300°C con rotación biaxial (6-12 RPM)
- Refrigeración: Agua pulverizada + fases de refrigeración por aire
- Descarga: Extracción manual/automática de piezas
Parámetros de diseño
Tamaño de la pieza | Peso del molde | Duración del ciclo |
<1m³ | 50-200kg | 20-40 minutos |
1-5m³ | 200-800kg | 40-90 minutos |
>5m³ | 800-3000kg | 2-4 horas |
Opciones de material:
- Polietileno (90% de las aplicaciones)
- Nylon (para depósitos de combustible)
- PVC (juegos infantiles)
5. Termoformado: Soluciones de envasado de pared delgada
Flujo de procesos
- Alimentación de hojas: Rollo a rollo u hojas sueltas
- Calefacción: Paneles infrarrojos (150-200°C)
- Conformado: Vacío (0,5-0,9 bar) o presión (3-6 bar)
- Recorte: Troqueles de acero o fresadoras CNC
Métricas de control de calidad
Tipo de defecto | Método de prevención | Herramienta de medición |
Cinta | Preestiramiento óptimo | Escáner láser 3D |
Puntos finos | Control de la presión | Medidor de espesor por ultrasonidos |
Alabeo dimensional | Velocidad de enfriamiento controlada | CMM |
6. Moldeo por compresión: Especialización en Termoestables
Secuencia técnica
- Preparación de preformas: Corte de SMC/BMC
- Carga del molde: Precalentamiento 80-120°C
- Curado: 100-200kg/cm² durante 2-15 minutos
- Postcurado: 1-4 horas a 150°C (opcional)
Propiedades del material
Tipo compuesto | Contenido en fibra | Resistencia (MPa) |
SMC | 25-30% de vidrio | 80-120 |
BMC | 15-25% de vidrio | 40-70 |
GMT | 30-40% de vidrio | 100-150 |
7. Moldeo de espuma estructural: Solución de aligeramiento
Características del proceso
- Reducción de peso: 15-30% frente a las piezas macizas
- Acabado superficial: Clase B SPI (texturizado)
- Estabilidad dimensional: ±0,3% tras 24 horas
Requisitos de equipamiento
Tamaño de la pieza | Fuerza de apriete | Sistema de inyección de gas |
<5kg | 50-100 toneladas | Nitrógeno |
5-20kg | 100-300 toneladas | Agente espumante químico |
>20kg | 300-600 toneladas | Sistema híbrido |
8. Moldeo por inserción: Fabricación de componentes híbridos
Directrices de diseño
- Materiales del inserto: Acero inoxidable, latón, cerámica
- Selección de plásticos: PPS para alta temperatura, PEEK para resistencia química
- Métodos de unión: Se prefieren los enclavamientos mecánicos a los adhesivos
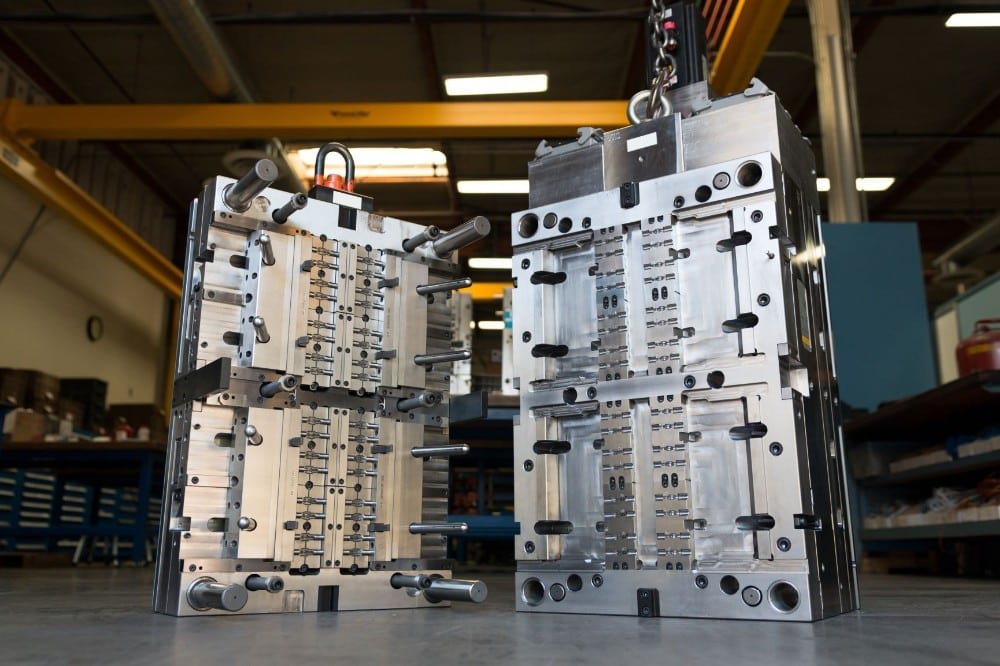
Normas de calidad
- Requisitos de la prueba de tracción: 50N mínimo para productos sanitarios
- Continuidad eléctrica: Resistencia <0,5Ω para los conectores
- Cierre hermético: Prueba de fugas de helio <1×10^-6 mbar-L/s
Matriz comparativa de selección de procesos
Proceso | Volumen económico | Plazo de entrega de las herramientas | Opciones de material | Precisión dimensional |
Inyección | 10k+ | 4-8 semanas | 200+ | ±0.005mm |
Extrusión | Continuo | 2-4 semanas | 30 | ±0.1mm |
Sople | 5k+ | 6-10 semanas | 15 | ±0.2mm |
Rotacional | 500+ | 3-5 semanas | 10 | ±0.5mm |
10 preguntas frecuentes de los expertos sobre los servicios de moldeado de plástico
P1: ¿Cómo elegir entre el moldeo por inyección y el moldeo por compresión?
R: Inyección para termoplásticos (más de 1.000 unidades), compresión para termoestables/composites.
P2: ¿Cuál es el grosor mínimo de pared para la extrusión de PE?
R: 0,1 mm para láminas, 0,5 mm para perfiles.
P3: ¿Puede el moldeo por soplado lograr socavados?
R: Limitado a ángulos de tiro de 5° sin núcleos plegables.
P4: ¿Cómo reducir las marcas de hundimiento en las costillas gruesas?
R: Mantenga una relación costilla-pared ≤60% y utilice gas asistido.
P5: ¿Qué acabado superficial es posible con el moldeo rotacional?
R: Normalmente SPI C-1 a D-3, con una replicación de textura de hasta el 90%.
P6: ¿Cuál es la precisión del termoformado frente al moldeo por inyección?
R: ±0,2 mm frente a ±0,05 mm en dimensiones críticas.
P7: ¿Qué proceso permite los cambios de material más rápidos?
R: Termoformado (15-30 minutos entre materiales).
P8: ¿Cuál es la pieza más grande posible con espuma estructural?
R: Hasta 4m×2,5m×1m con prensas de 600 toneladas.
P9: ¿Cómo se valida la fuerza de adherencia del moldeo por inserción?
R: Prueba de arranque ASTM D4541 a 23°C y 85°C.
P10: ¿Por qué asociarse con BFY Mold para servicios de moldeo de plástico?
- Más de 50 sistemas de moldeo de 5 a 600 toneladas
- Herramientas propias con un plazo medio de entrega de 25 días
- Laboratorio de ciencia de los materiales para pruebas de formulación