Los productos acrílicos moldeados por inyección son populares por su claridad y versatilidad, pero pueden ser propensos a defectos como la deformación y las burbujas. Entender cómo abordar estos problemas es crucial para lograr resultados óptimos en su proceso de fabricación. En este artículo, exploraremos soluciones prácticas y las mejores prácticas para minimizar estos defectos, garantizando la producción de productos de moldeo por inyección de alta calidad.
Supongamos que se producen alabeos y deformaciones del producto durante el proceso de moldeo por inyección. En ese caso, debe resolverse principalmente a partir del diseño del molde, y el efecto de ajuste de las condiciones de moldeo es mínimo.
Soluciones para el alabeo y la deformación en productos de moldeo por inyección
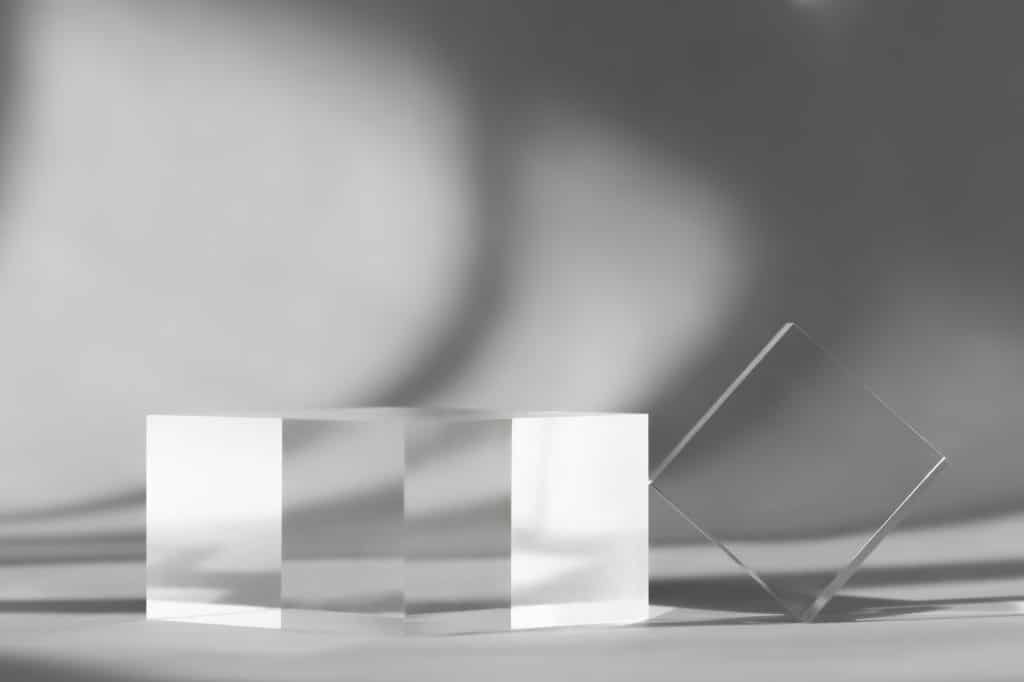
PASO 1: Cuando la tensión residual causada por las condiciones de moldeo provoca deformación, la tensión puede eliminarse reduciendo la presión de inyección, elevando el molde y uniformando la temperatura del molde, elevando la temperatura de la resina o utilizando el método de recocido.
PASO 2: Cuando la deformación por tensión se debe a una mala liberación, puede solucionarse aumentando el número o el área de la varilla de empuje y ajustando la pendiente de liberación.
PASO 3: Cuando el método de enfriamiento no es adecuado y el tiempo de enfriamiento no es uniforme o insuficiente, se puede ajustar el método de enfriamiento y ampliar el tiempo de enfriamiento. Por ejemplo, puede colocarse un bucle de enfriamiento lo más cerca posible de la deformación.
PASO 4: Para la deformación causada por la contracción de conformado, hay que corregir el diseño del molde. Entre ellos, lo más importante es prestar atención a que el grosor de la pared del producto sea consistente. A veces, en caso de necesidad, es necesario corregir el molde midiendo la deformación del producto y recortándolo en sentido contrario.
Las resinas con grandes índices de contracción, generalmente resinas cristalinas (como las resinas de poliformaldehído, nailon, polipropileno, polietileno y PET, etc.) tienen una deformación mayor que las resinas amorfas (como las resinas acrílicas, cloruro de polivinilo, poliestireno, resinas ABS y resinas AS, etc.). Además, como la resina reforzada con fibra de vidrio tiene coordinación de fibras, la deformación también es grande.
Cómo resolver las causas de las burbujas
Cuando el grosor de la pared del producto es mayor, la velocidad de enfriamiento de la superficie exterior es más rápida que la del centro, de modo que, con el enfriamiento, el lado de resina del centro se contrae y se expande hacia la superficie, por lo que el centro se llena insuficientemente. Esta situación es propensa a la formación de burbujas de vacío. Las principales soluciones son:
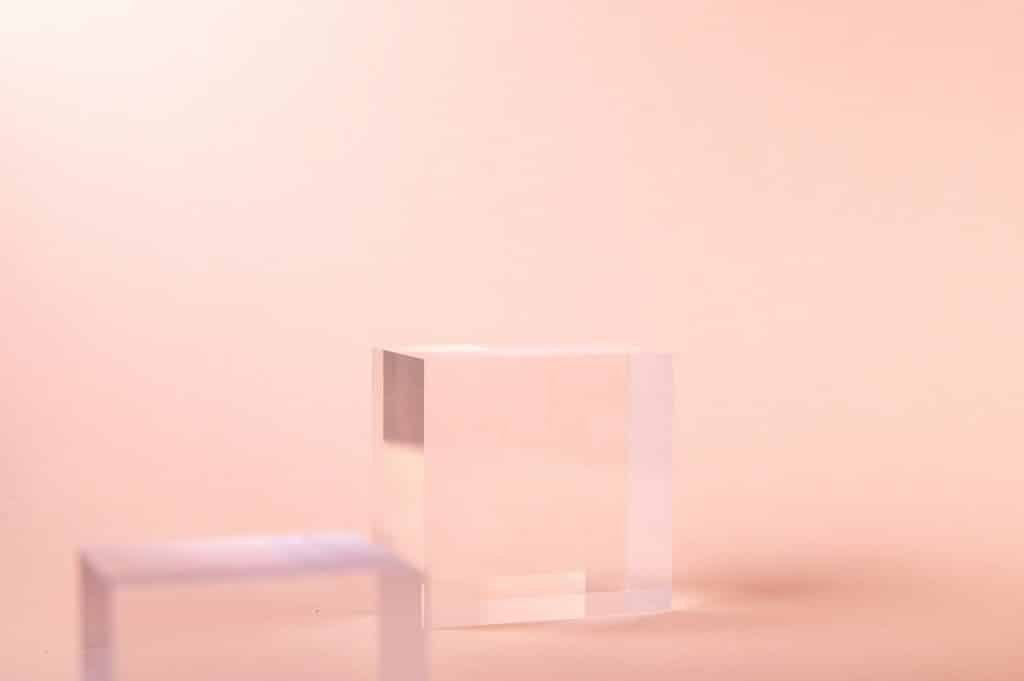
a) Determinar el tamaño razonable de la compuerta y el canal en función del grosor de la pared. Por lo general, la altura de la compuerta debe ser del 50% al 60% del grosor de la pared del producto.
b) Hasta que se cierre la compuerta, queda una cierta cantidad de material de inyección suplementario.
c) El tiempo de inyección debe ser ligeramente superior al tiempo de sellado de la compuerta.
d) Reducir la velocidad de inyección y aumentar la presión de inyección.
e) Se utilizan materiales con alto grado de viscosidad de fusión.
Cómo resolver los problemas de las burbujas de gas volátil en el moldeo por inyección
a) Presecado completo.
b) Reducir la temperatura de la resina para evitar la generación de gas de descomposición.
c) Las burbujas causadas por una fluidez deficiente pueden solucionarse aumentando la temperatura de la resina y del molde e incrementando la velocidad de inyección.