光学レンズ、医療機器ハウジング、消費者向けパッケージなど、透明な製品の射出成形では、材料の純度、工程精度、表面仕上げの完全性に細心の注意を払う必要があります。気泡、フローマーク、ヘイズなどの小さな欠陥でさえ、製品を使用不可能にする可能性があるため、材料の準備から金型設計に至るまで、すべての段階が重要です。
このガイドでは、高度な乾燥プロトコル、金型温度管理、光学グレードの研磨技術など、譲れない7つの要素を分解し、透明度の高い結果を保証します。PMMAまたはポリカーボネートのいずれの部品を製造する場合でも、これらの戦略により再加工を最小限に抑え、透明性と耐久性に関する業界標準に適合させることができます。
透明製品の透明性に関する表面仕上げ基準
透明プラスチックは光透過率が高いため、厳しい表面品質基準が要求されます。マーキング、気孔、変色、光沢不良などの欠陥は許されません。射出成形の工程では、材料、設備、金型、製品設計など、あらゆる面で厳しい要件を満たす必要があります。

透明な製品成形: ヘイズとバブルの除去
透明プラスチックは一般的に融点が高く、流動性が悪い。製品の品質を確保するためには、バレル温度、射出圧力、射出速度などのプロセスパラメーターを微調整する必要がある。これにより、内部応力や変形、ひび割れを起こすことなく、プラスチックが金型に充填されます。
透明ポリマーの完全性のための材料乾燥
素材の純度の確保
プラスチック中の不純物は透明性に影響する。保管中、輸送中、供給中は、原料を密閉して清潔に保つ必要がある。原料に含まれる水分は加熱劣化の原因となるため、徹底した乾燥が不可欠である。乾燥ホッパーを使用し、投入空気はフィルターでろ過され、除湿されていることを確認する。
透明製品の純度を高める装置洗浄
バレル、スクリュー、アクセサリーのクリーニング
使用前と停止後にスクリュー洗浄剤でスクリューと付属品を洗浄し、汚染を防いでください。洗浄剤が使用できない場合は、PEまたはPS樹脂を使用することができる。一時停止中は、ドライヤーとバレルの温度を下げ、原料の劣化を防ぐ。
高光沢透明製品の金型設計
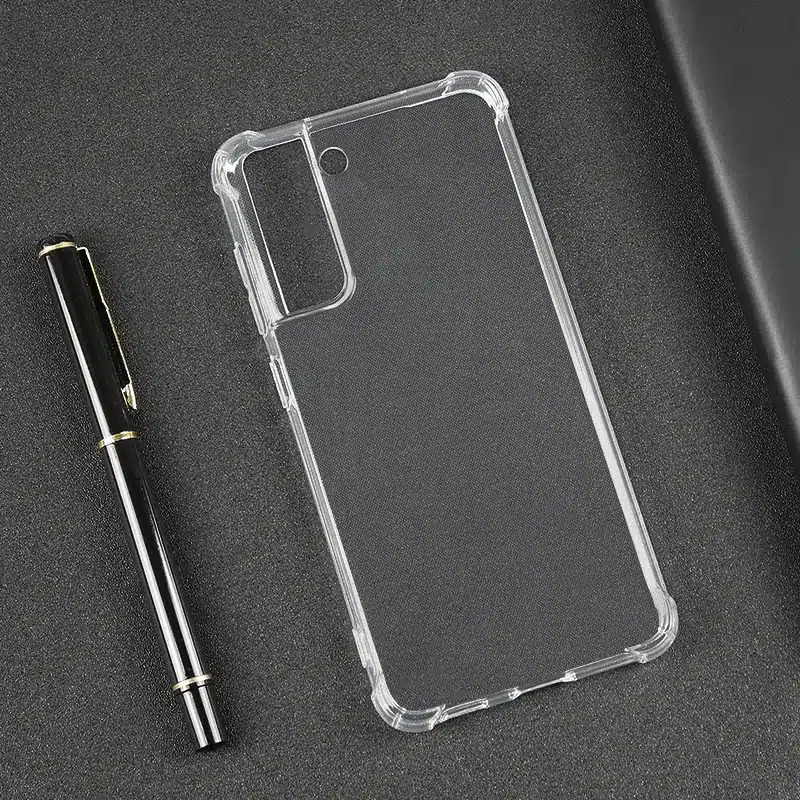
品質のためのデザイン
表面欠陥を避けるため:
1. 均一な肉厚と十分な脱型勾配を確保する。
2. 鋭角にならないよう、コーナーを徐々に移行する。
3. 必要であれば、幅が広く短いランナーや、冷却ウェルのある適切な位置のゲートを使用する。
4. 金型表面の凹凸を少なくし、十分な通気性を確保する。
金型表面と肉厚
鋳型の表面は滑らかで、粗さが小さいこと(好ましくは0.8以下)。溶融物から空気やガスを排出するために、十分な通気孔を確保する。PETを除き、壁の厚さは最低1mmとし、過度に薄いものは避ける。
透明クリスタル製品の射出パラメータ
最適注入パラメータ
内部応力と表面欠陥を最小限に抑える:
1. 特殊なスクリューと温度制御されたノズルを使用する。
2. 樹脂の分解限界内で高い射出温度を使用する。
3. 溶融材料の粘性に打ち勝つために高い射出圧力をかけるが、変形を引き起こすほど高くはない。
4. 低速射出、好ましくは低速-高速-低速の多段射出を選択する。
5. 窪みや気泡を避けるため、保圧時間と成形サイクルを短く保つ。
6. 材料の劣化を防ぐため、低いスクリュー速度と背圧を使用する。
7. 金型温度を正確に制御し、最適な冷却と製品品質を実現。
透明製品のポストモールディングにおける欠陥防止
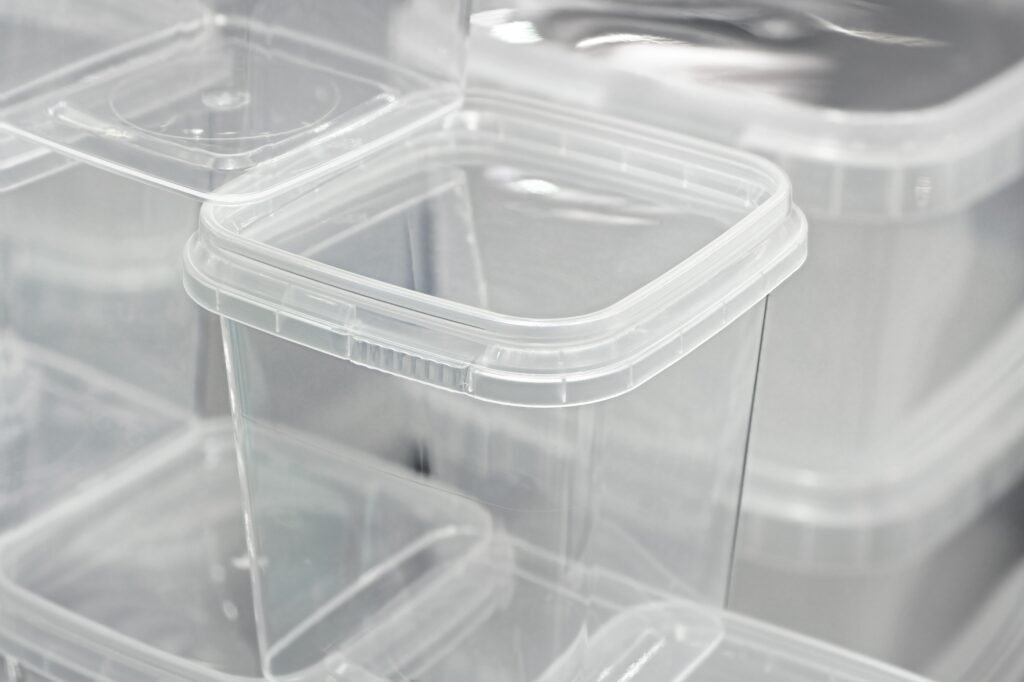
離型剤とリサイクル素材の使用
表面品質の劣化を防ぐため、離型剤の使用は最小限に抑える。再生材料を使用する場合は、20%を超えないようにする。
製品の後処理
PETのように、内部応力を除去するために後処理が必要な素材もある。PMMAは70~80℃で4時間、PCは110~135℃で乾燥させる。PETは良好な機械的特性を得るために双方向延伸が必要である。